A pass-fail inspection is an integral part of maintaining the quality of your products or services. As a general manager this is your top priority.
Central to this is the process of inspection, which allows you to evaluate your operations and identify areas of improvement.
One of the most efficient and straightforward methods of inspection is the pass-fail inspection system. The process also applies to pass fail home inspection, or any other on-site inspection for that matter.
Priced on per user or per location basis
Available on iOS, Android and Web
Moving on, this type of inspection, by nature, is a binary evaluation.
It classifies items into two clear categories: those that meet the pre-established criteria (pass) and those that do not (fail).
This sense of overall simplicity is their strength. With clearly defined parameters, an inspection of product, and a pass fail inspection contigency cuts down on ambiguity, expedites the decision-making process, and provides unequivocal feedback to the operations team.
But beyond these immediate benefits, quality inspections have broader implications for general managers.
With every inspection, you're reinforcing the standards your products or services must meet, building a reputation for excellence in the market.
These inspections serve as a direct line of communication with your production or operations team.
This post offers a comprehensive guide to carrying out suchinspections.
Read on…
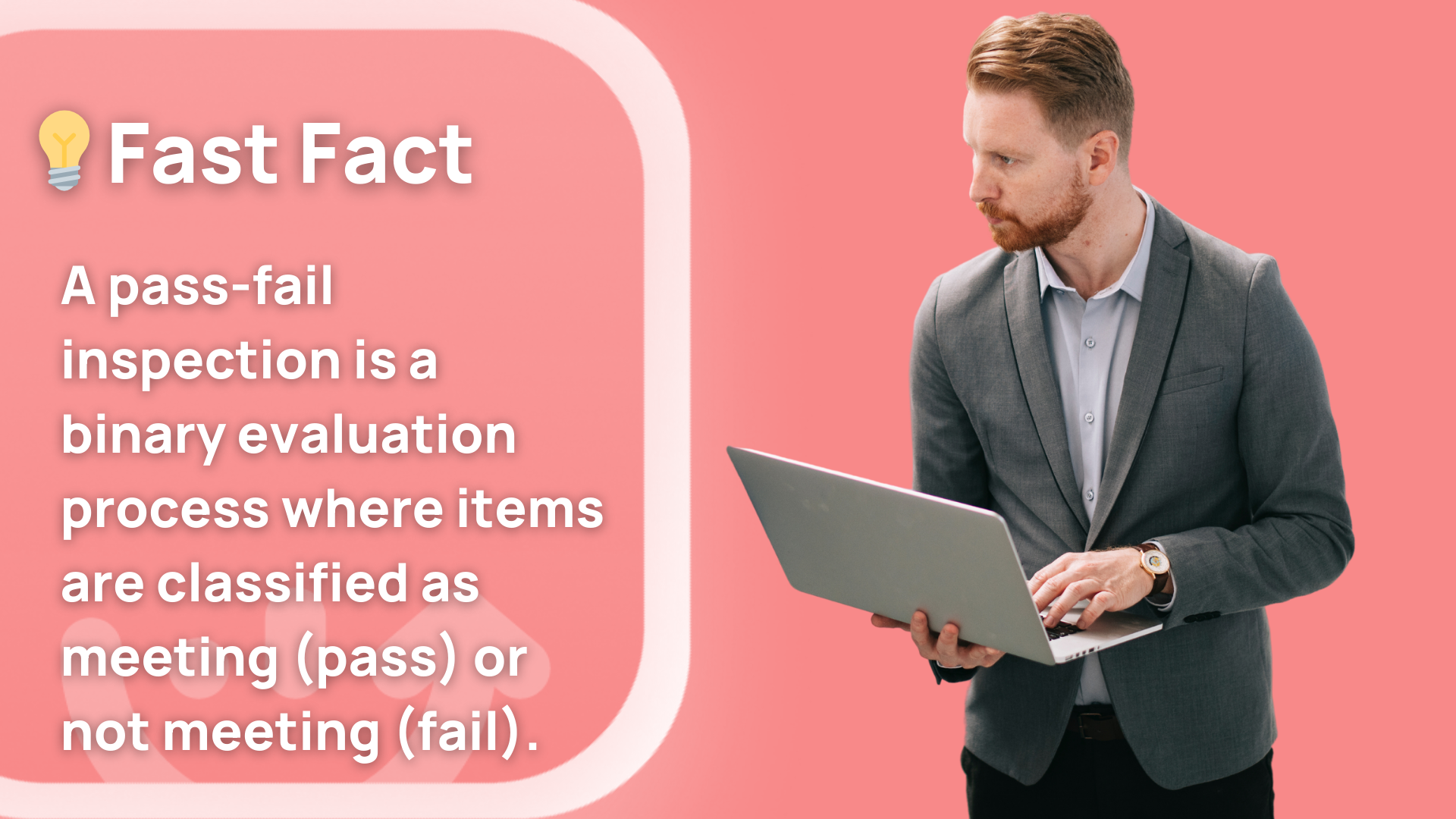
What Is a Pass Fail Inspection: Understanding Pass Fail Inspection Contingency
Pass fail inspections are a streamlined and efficient approach to evaluating the functionality of products, systems, or procedures.
Before further doubling down on this step-by-step process, it's crucial to comprehend the key benefits and objectives behind these inspections.
Simplified Evaluation
These inspections involve a straightforward classification, either approving (pass) or disapproving (fail) a system or product based on predefined criteria.
This level of simplicity reduces decision-making time and eliminates ambiguity.
Time-Efficient Decision Making
By providing a binary evaluation, pass fail inspections expedite the decision-making process. General managers can quickly assess whether an item meets the established criteria or requires further attention, saving valuable time.
Clear Feedback Loop
These inspections offer a direct and unambiguous feedback loop to the production or operations team. The classification provides clear guidance on the quality of the item, enabling immediate corrective actions if necessary.
Consistent Quality Standards
Implementing fail pass inspections helps maintain consistent quality standards throughout your operations. By adhering to predefined criteria, you ensure that every product or system meets the required level of quality, enhancing your reputation and customer satisfaction.
Enhanced Accountability
Fail pass or pass-fail inspections promote accountability within the organization.
By clearly defining the criteria for passing or failing, individuals responsible for the quality of products or systems can be held accountable for meeting those standards.
Increased Customer Satisfaction
Implementing inspection-related processes contributes to increased customer satisfaction.
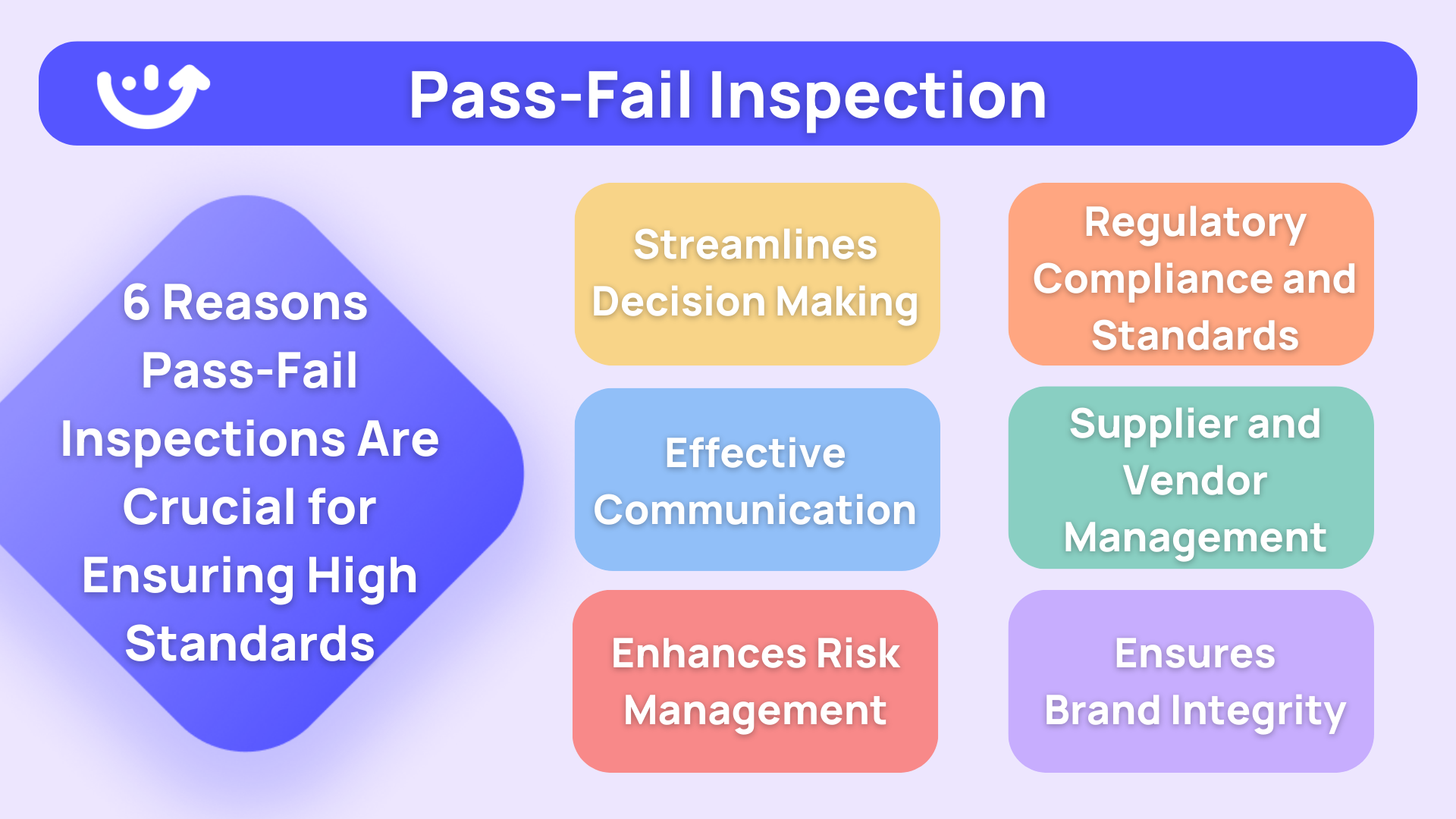
The Importance of a Pass Fail Inspection In a Modern-Day World
Adopting a pass-fail inspection system offers significant value to organizations in the realms of quality control and operations management.
Ensures Brand Integrity
Moving on, these inspections play a pivotal role in maintaining brand integrity by upholding consistent quality standards across all operations.
Streamlines Decision Making
The binary nature of such activities simplifies the decision-making process.
Rather than grappling with subjective evaluations, general managers can swiftly categorize items as either meeting the criteria (pass) or needing attention (fail).
Effective Communication
Pass fail inspections establish a direct and clear communication channel for production or operations teams, facilitating immediate corrective actions and fostering continuous improvement by promptly identifying and resolving quality issues.
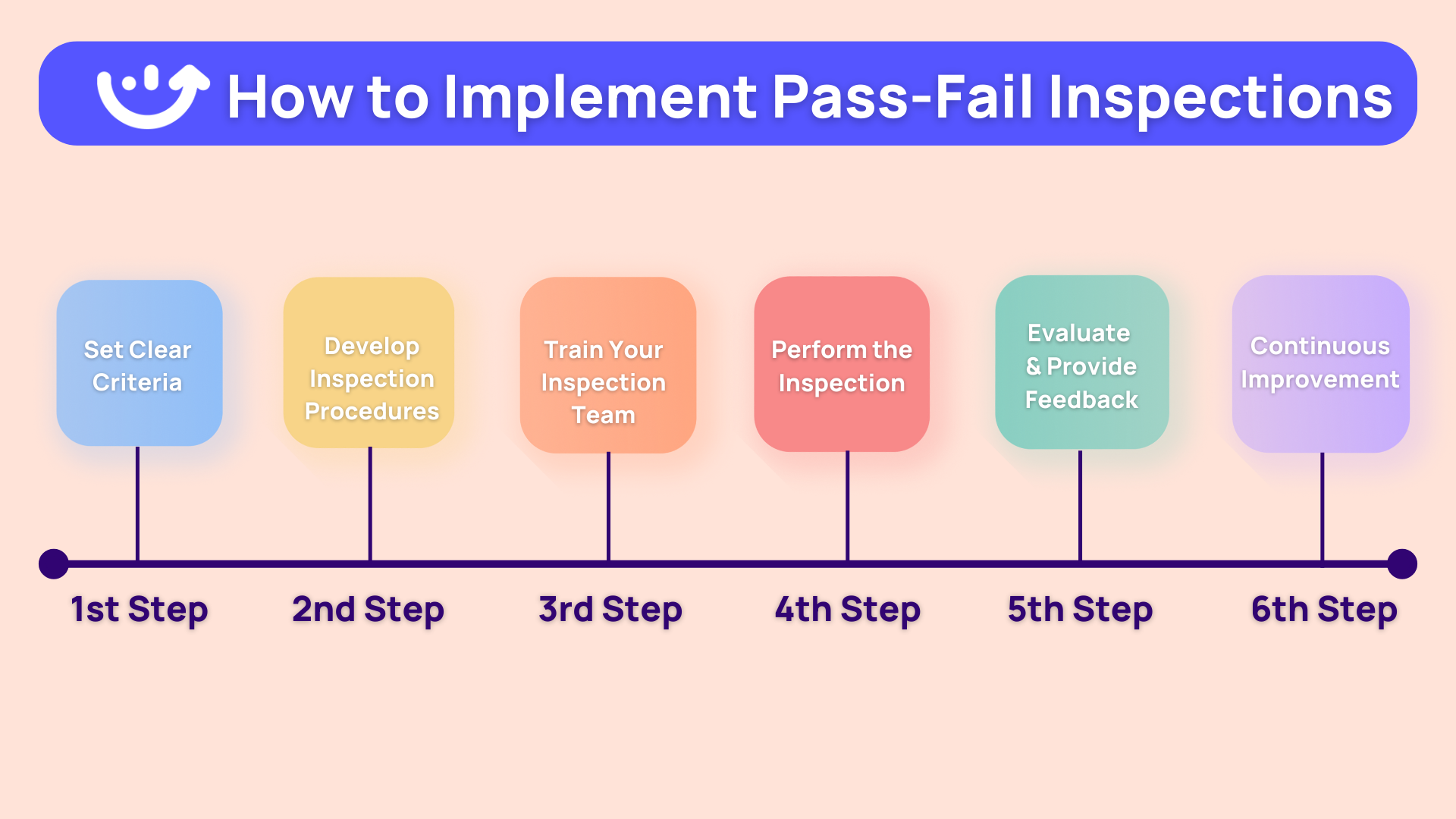
Step By Step Guide For Pass Fail Inspection Implementation
Implementing pass-fail inspections can pose challenges that hinder the organization's ability to enhance quality control measures.
Overcoming these challenges is vital to ensure successful implementation and continuous improvement.
Here is a step-by-step guide to successfully implementing pass-fail inspections.
1. Set Clear Criteria
To begin, define specific parameters that a product or system must meet to pass inspection.
These criteria should be measurable, objective, and relevant to the functionality of the item being inspected.
It is essential to involve key stakeholders, such as quality control experts and relevant teams, in the process to ensure consensus and understanding.
2. Develop Inspection Procedures
Next, outline a detailed inspection procedure that provides clear guidelines on who will conduct the inspections, what tools or equipment they will utilize, and how to record results.
Include any necessary safety measures to protect the individuals performing the inspections. Consider establishing routine inspections to ensure consistent monitoring.
3. Train Your Inspection Team
Ensure that the inspection team is well-trained and familiar with the specific product or system being inspected.
Provide comprehensive training on the pass-fail criteria, inspection techniques, and the proper use of inspection tools and equipment.
Encourage team members to ask questions, seek clarification, and voice any concerns related to the inspection process.
4. Perform the Inspection
Carry out the inspections according to the established procedures and guidelines.
Thoroughly document the results, including any issues or non-compliance identified during the inspection.
5. Evaluate and Provide Feedback
Review the inspection results, considering both pass and fail outcomes.
Provide clear and constructive feedback to the relevant teams based on the inspection findings.
Take necessary actions based on the results, such as proceeding to the next step in the production process for a pass or initiating corrective measures for a fail.
6. Continuous Improvement
Continuously review and update the inspection criteria as necessary to reflect evolving quality standards and business requirements.
Evaluate the effectiveness of the inspection process by seeking feedback from the inspection team and other stakeholders.
Leveraging Technology in Pass Fail Inspection(s)
The integration of technology into pass-fail inspections can drastically improve their efficiency and accuracy, empowering general managers to enhance their quality control measures.
Here are some key areas to consider when leveraging technology in pass fail inspections:
Digital Checklists
One way to optimize these inspections is by leveraging digital platforms to manage inspection checklists.
These platforms provide a centralized and streamlined approach to ensure that all criteria are checked and results are accurately recorded.
Digital checklists help eliminate manual errors, provide clear guidance to the inspection team, and facilitate efficient data collection.
Data Analytics
Data analytics enable a data-driven approach to decision-making, fostering continuous improvement and better resource allocation.
Real-Time Reporting
Real-time reporting tools offer immediate insights into inspections.
Managers can receive instant updates on the progress and outcomes of inspections, enabling swift decision-making and timely intervention if necessary.
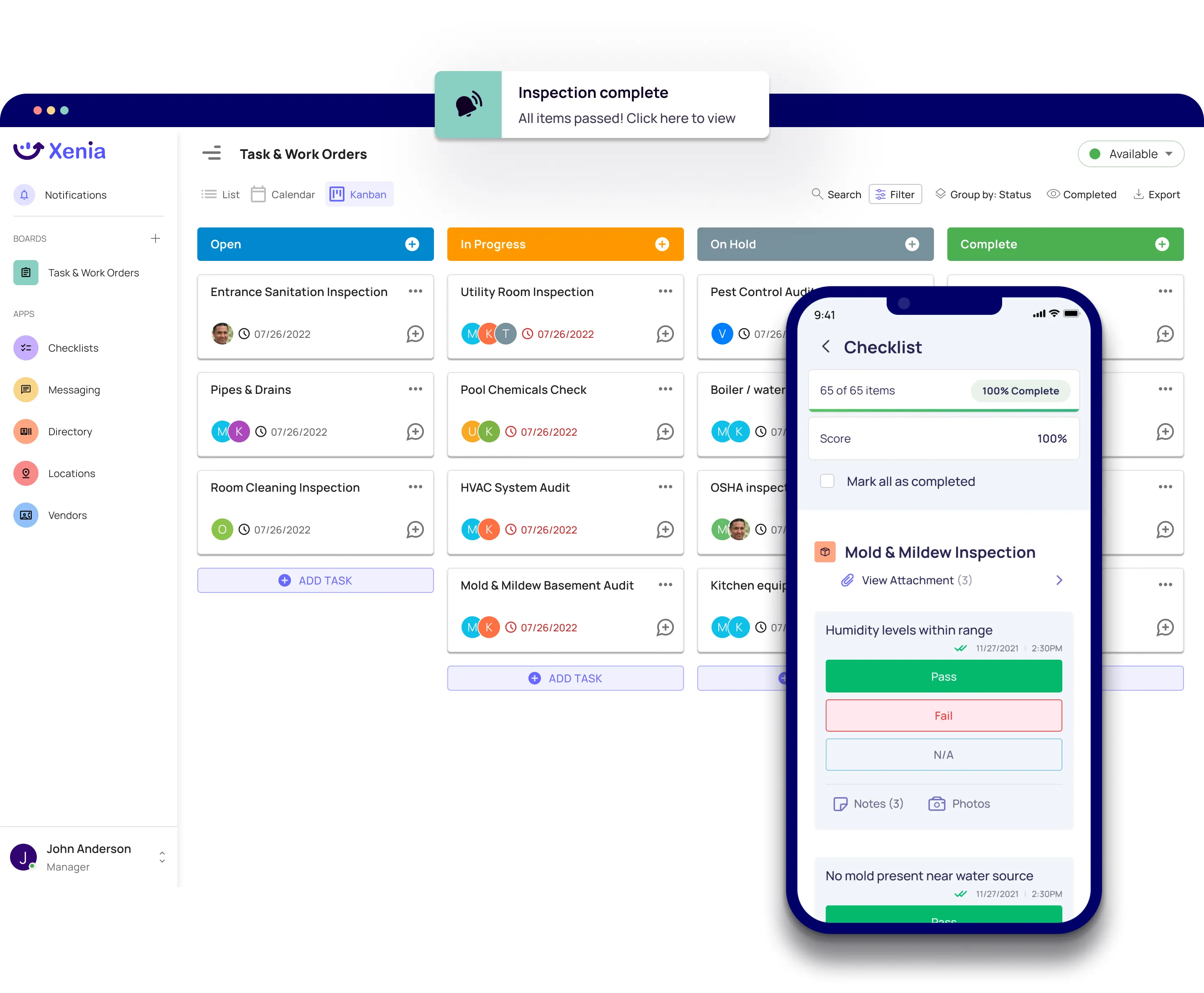
Benefits of Using Xenia for Inspection Management
Implementing a robust software solution like Xenia can revolutionize pass fail inspection management for general managers.
The platform serves as an all-in-one holistic solution that streamlines the entire inspection process and enhances the efficiency and effectiveness of your quality control measures.
As a frontline manager, or someone who’s in charge of selecting inspection software solutions for the company, here are some of the benefits you need to know:
Centralized Inspection Management
Xenia serves as a centralized platform for managing pass fail inspections.
The tool allows you to store and access all inspection data, criteria, and results in one secure location.
Efficient Digital Checklists
Through this platform, you can create and customize digital checklists tailored to your specific pass or fail criteria.
Digital checklists in Xenia eliminate manual errors, standardize inspections, and enhance data accuracy.
Real-Time Monitoring and Alerts
Xenia offers real-time monitoring and alerts, enabling you to stay updated on the progress and outcomes of pass-fail inspections.
You can receive instant notifications when an inspection is completed, a failure is recorded, or when corrective actions are required.
Comprehensive Reporting and Analytics
Our comprehensive tool provides powerful reporting and analytics capabilities that facilitate in-depth analysis of inspection data.
You can generate customized reports to identify trends, measure performance, and gain valuable insights for process improvement.
Collaboration and Communication
Our program fosters seamless collaboration and communication among team members involved in pass fail inspections.
Elevate Your Inspections and Audits with Xenia: Start Your Free Trial Today!
Pass fail inspections play a crucial role in ensuring consistent and reliable product and system functionality.
As a general manager, it is imperative to optimize this inspection process to enhance efficiency, accuracy, and overall quality.
That’s is where Xenia, the powerful facilities and frontline operations management software, steps in to revolutionize your pass-fail inspection management.
With Xenia's robust reporting and analytics capabilities, you can gain valuable insights, identify trends, and make data-driven decisions for continuous improvement. Real-time monitoring and alerts keep you informed of inspection progress, failures, and necessary corrective actions.
Start your free trial of Xenia today!
.webp)
%201%20(1).webp)