Preventing workplace mishaps is a top priority for every company, as nobody wants to be caught off guard or blindsided by an accident or injury.
Right?
But, how does a company even begin to improve safety? Trying to change or fix is such a big, nebulous thing. Proactiveness is the key to safety, or so we hear constantly. Look for hazards; fix what you can before anything goes wrong, and make safety a part of everything you do.
But, then again, the question is: how do you separate the things that can wait until tomorrow from the things that must be fixed right now before somebody gets hurt?
The solution lies in knowing robust safety protocols.
Regarding safety management, we need to be clear on one thing – safety audits and inspections are not the same thing!
While both are vital to a strong safety program, they have different purposes and approaches.
They are, however, very important for the success of a robust safety program. Nonetheless, many organizations fail to understand this duality, and as a result, they don't get the insights that they need to make things safer for everyone in the company.
What are the differences between safety audits and inspections? Well, a safety audit is how satisfied your organization is with meeting the requirements of the regulations. Meanwhile, a safety inspection looks for anything and everything in the workplace that is a potential risk and finds anything in your workplace that is a hazard.
And believe us, you want to find them before they find you. Just think about 5,190 workplace safety incidents in 2021 ended in death.
With such alarming numbers, the question is: can you afford to roll the dice on safety?
The stakes are too high, and the consequences too dire
Throughout our years of experience in safety management, we've found that a clear grasp of safety audits and inspections can drive real results: decreased incidents, improved compliance, and even heightened safety culture.
Not understanding this difference, however, can have significant repercussions. This is specifically important for synergistic management of multiple operations.
For example, in the context of retail chains with numerous stores, misunderstanding the difference between safety audits and inspections can generate issues such as not complying with OSHA regulations. The result is heavy dollar penalties, loss of revenue, and brand damage.
To help you ensure the smooth operation of multiple sites, in this post, we have shared expertise and offer actionable tips to help you streamline your safety processes.
Knowing the safety audit and inspection definition is a fundamental prerequisite that allows you to find out where you can do better.
So, let’s start with that
Priced on per user or per location basis
Available on iOS, Android and Web
Defining Safety Audits and Inspections
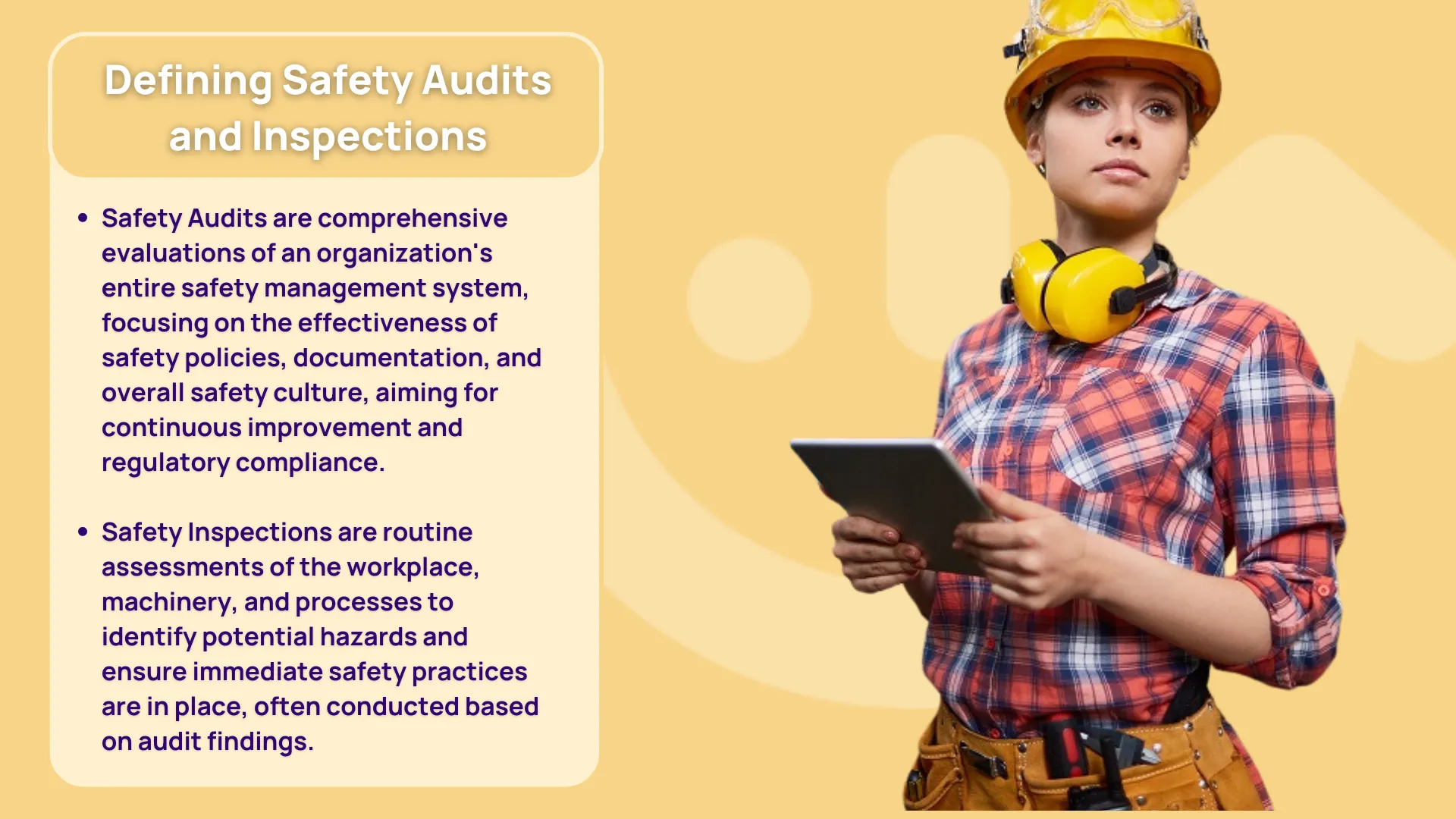
The Health, Safety, and Environment (HSE) manager plays a crucial role in the health and safety of workers, as they are the ones ensuring that the work environment is safe and healthy. It is their job to put plans in place to prevent accidents and illnesses.
The International Labor Organization (ILO) reports that every 15 seconds, there is a worker death due to a work-related accident or illness and that every 15 seconds, 153 workers have a work-related accident.
Certainly, these numbers are alarming, and they serve as an effective impetus for HSE management to take action.
Achieving all this is a tall order for HSE managers, but strategies and methods can help a lot. Two essential tools in the HSE manager's hand are safety inspections and audits.
Let’s conduct a thorough analysis of the two.
Audit and Inspection Definition
Audits
TL: DR - Audits are more around the “check / checking” element, flagging issues as the audit itself is being conducted. These checks or flags, later on, serve as a starting point for inspectors, when they are conducting inspections - either based on the audit, or from scratch.
An organization's whole safety management system is comprehensively evaluated in a safety audit. It goes beyond the day-to-day inspection and involves a thorough examination of safety policies, documentation, training programs, and overall safety culture in an organization.
To put it in another way, it measures the effectiveness of safety programs, focusing on active compliance and continuous improvement. It checks if safety policies are being followed and if there's a culture of ongoing progress.
Note that A safety audit isn't an incident investigation.
Its focus is on getting it right going forward; that is, it's more like a check-up of your safety protocols—with some prescription thrown in for good measure.
The audit serves to:
- Measure the efficacy of your safety policies and procedures
- Identify opportunities for improving safety overall
- Make sure you're complying with safety regulations and standards that apply to your kind of place
- Recommend ways to strengthen the clarity, coverage, consistency, and coordination of your overall safety system.
Who Conducts Safety Audits?
Safety Audits can be conducted by various individuals, including internal auditors (company safety auditor or risk manager), external auditors (independent auditors or their-party auditing firms)who bring a fresh set of eyes, and industry experts who have been around the block a few times.
Additionally, regulatory agencies and certification bodies (OSHA, EPA, ISSO, or ASSE) may also come in to crack the whip and ensure compliance with relevant laws and standards. These auditors leave no stone unturned, reviewing safety policies, incident records, and operational aspects to identify areas for improvement and provide recommendations for enhancing safety management systems.
Inspections
TL: DR - Inspects are more about the “Do/ Doing” element of the process. Usually, inspections are conducted after a thorough audit. They are important in terms of maintaining brand compliance, a consistent back-of-the-house/front-of-the-house experience, or their equivalent in other industries.
Understanding the audit and inspection definition, a safety inspection serves as a routine assessment of the workplace, machinery, and processes to determine potential hazards and to ensure that the necessary practices for immediate safety are in place. The inspector or inspection team assesses various aspects of the workplace i.e. equipment machinery, work processes, and physical environment.
It is the on-the-go type of inspection that is performed by responsible persons authorized to do the work.
A safety inspection centers on four main areas:
- People: Employee behavior, training, and awareness
- Places: Workstations, walkways, and overall work environment
- Equipment: Machinery, tools, and gear
- Immediate safety practices: Compliance with safety procedures and regulations
When regularly performed, these inspections provide a continual "feedback loop" of information regarding potential hazards and problems that can reasonably be expected to affect people associated with the workplace.
Who Conducts Safety Inspections?
Safety Inspections can be conducted by various people such as safety professionals, supervisors, site management team, or employees themselves in case of self-assessment or govt inspector.
Safety Inspections and Audits: How to Tell the Difference?
To put it simply, inspections are what you "do", and audits are what you "check". Sites often have to perform an inspection to comply with an obligation. An audit is a way to ensure that a site has met its legal duty, and that includes checking on whether required inspections have been done.
Proactive vs Reactive
Safety audits are reactive.
For example, a safety audit is performed by a company to gauge how well its current safety precautions work. If the audit uncovers that several workers have been hurt by poorly guarded machines in the past year, this is vital information for the firm to use in revising its safety policies. It would seem intuitive that if you don't want people getting hurt in the future, you simply make sure they don't have easy access to the kinds of machines that have hurt them in the past.
As explained in the audit and inspection definition, Inspections are proactive.
Example: To expose potential dangers and noncompliance, a facility manager sets up regular workplace inspections. During one such occasion, the team discovers the absence of a machine guard that could leave employees open to possible harm and injury. The necessary measures are taken to immediately correct what could have been a hazardous situation.
Methodologies
Audits usually consist of interviews, observations, and various measurements. These measurements might assess how well an intender has performed, what practices were in place, and what safety levels were achieved.
On the contrary, in inspection, the inspector looks for things like signs of structural damage to the buildings, unsafe pathways and tripping hazards, proper lighting, and other conditions that may lead to danger.
Outcome
The results of an audit are reported in detail, including an analysis of the organization's strengths, weaknesses, opportunities, and threats (known as SWOT analysis). The outcome also provides some recommendations to improve the situation and any required actions to take to make the improvements.
When inspections are done, the results will be set down in a report. This will identify what was seen as a hazard, a non-compliance, or (and this is important) a recommendation for improvement. In turn, each of those identified problems may require some kind of corrective action before it's legally considered solved.
How are Safety Inspections and Audits Linked?
As noted earlier, audits and inspections are the dynamic duo of safety management, working in tandem to create a protective shield that safeguards employees and the workplace.
In fact, during our research work, we found the U.S. Bureau of Labor Statistics (BLS) reports a study that claims the use of proper workplace safety systems has resulted in a substantial drop in workplace fatalities. Between 1970 and 2019, the number of work-related deaths decreased by 60.53%.
That's a significant number, to say the least.
Safety inspections inform safety audits in several ways:
- Identifying hazards: Inspections help identify hazards, which are then assessed during audits to determine their impact on the overall safety management system.
- Assessing compliance: Inspections ensure compliance with regulations and standards, which are then evaluated during audits to determine the effectiveness of the safety management system.
- Providing data: Inspections generate data on safety performance, which is used during audits to assess the overall effectiveness of the safety management system.
Operational Application of Inspections and Audits in Various Industries

- Healthcare
Businesses have no legal obligations to conduct a health and safety audit of their work.
However, the HSE guidance document, HSG65 Successful Health and Safety Management, provides very strong reasons for carrying out such an audit. It recommends "auditing for success," seeing the audit as not just a legal necessity but also as an opportunity to improve the business by systematically finding and fixing operational failures.
Keeping patients safe is still the top concern for Medicare.
It's responding by cutting its payments to problem-ridden hospitals. In fiscal years 2018 and 2019, some 800 hospitals took a pay cut because of patient safety worries—and the penalties began from the moment the hospital filed a claim.
That’s a wake-up call for many hospitals, particularly the 800 that received a cut: Shutting the door on safety problems is no longer an option. It’s also why hospitals, as well as doctors, are conducting more regular health and safety checks.
What’s the significance of this?
The reason for doing a health and safety inspection is to uncover any potential hazards that could pose a risk or any modifications (to the premises or equipment) that have been made that could negatively affect a worker's safety. On the other hand, a health and safety audit would more closely resemble an" into the company's health and safety procedures, done either by one of the company's internal audit teams or by an outside expert.
Let’s understand this with a real-case scenario.
In a recent audit, the quality assurance team found or identified an instance of wet floor, potentially leading to a slip and fall accident.
Once the team identified the aforementioned hazard, they promptly formed a corrective action plan to fix it.
As a result, the number of people (*patients and/or visitors) who fell was drastically reduced. On average, the hospital experienced a decrease in patient falls.
That’s a huge win.
But that's not all.
Let’s go through another area where healthcare inspection checklists can help.
If the environmental services team identified a serious safety risk with the disposal of hazardous waste, they'd conduct an inspection.
If their inspection didn't show compliance, the next step would be to raise awareness and give training to the staff about not just this instance but all the ways hazardous waste is produced in a hospital.
To ensure that it worked and stayed that way, an inspection checklist would have to follow the directions to the letter, and it would have to do that not just once, but continuously.
The final step would be to change the procedure so that instead of creating a hazard, the production of hazardous waste would be eliminated.
And voilà!
The hospital achieved compliance with regulations and industry standards.
- Manufacturing Industry
Failing to follow the right safety procedures can lead to manufacturing accidents and injuries, halting work and causing unnecessary delays.
The manufacturing industry had 846,700 injuries in 2019—6.6 per 100 full-time workers or 15 percent of all nonfatal injuries and illnesses recorded in the private industry sector.
Regularly scheduling safety audits and inspections can assist plant managers with identifying and rectifying risk areas before they become expensive and problematic issues.
Building on audit and inspection definition assessments of these risk areas—particularly problematic for workers—are a key part of the worksite's safety and health management system.
During these audits(OSHA or GMP), operational hazards are identified and rectified. To enforce these changes, regulatory standards are adhered to, which are made even more concrete when the inspections are carried out by the government agency responsible for enforcing these standards.
However, manufacturing inspection checklists are entirely different. They involve examining and assessing the work setting while it is in operation or during use. The goal is to find and fix hazards before they can harm workers.
Workplaces are not required to follow any specific safety inspection methods. All they have to do is have a competent person do the job.
Let us comprehend the audit of a drug company following good manufacturing practices (GMP).
The manufacturing audit included all aspects of pharmaceutical production, such as quality management systems, facilities and equipment, materials management, production, and process controls.
In the unfortunate but not entirely surprising "not meeting expectations" category were various levels of poor performance. The general recipe to address such issues is to unflinchingly track down and fix every problem that pops up.
Thus, the company introduced a new quality management system, and calibrated all equipment, and while doing so, they implemented a quality management system, and also accounted for compliance. Moreover, they introduced improvements to their procedures for managing materials.
All of these moves significantly contributed to making their medicines exceed the required quality.
- Construction Industry
With a new regulation enacted seemingly every other business day, and with enforcement on the rise, compliance can go from difficult to impossible.
In 2017 and 2018 alone, more than 25 construction safety regulations were passed—a thunderclap of activity that reshaped the NYC building code, rewrote its construction rules and added thousands of potential violations to the city Buildings Department’s inspectional codebooks.
Performing an audit on your construction site can ensure that you follow OSHA and NYC DOB regulations regularly. It will provide you with practical safety enforcement ensuring that all the documents required by the Licensed Superintendent.
Having regular audits and inspections will help you avoid violations of non-compliance and ensure you have all your documents up to date.
it checks for;
- Are all workers following the right procedures to be safe?
- Is the site safety plan being followed that covers the job?
- Are all workers wearing the right PPE to complete the job?
- Do all workers have the right certifications and training to complete the job?
As a diligent site manager, you are aware that OSHA requires you to maintain a safe working environment following 29 CFR 1926 regulations. This includes routine safety audits to assess safety issues and provide solutions to mitigate risks. Conducting routine audits and addressing identified issues enables you to pass OSHA’s fall protection standards (29 CFR 1926.502) and electrical safety regulations (29 CFR 1926.404).
Doing this will greatly reduce accidents, minimize downtime, and create a more safe working environment.
- Hospitality Industry
Ensuring that hotels and restaurants follow health codes and regulations is essential to the success of any hospitality establishment. The fast food restaurant has more problems than the usual sit-down restaurant. According to the National Institute for Occupational Safety and Health, about 44,000 injuries were suffered by teenage workers in restaurants in two years.
These numbers are shocking but don't panic.
By adhering to these standards, hotels, and restaurants show that they care about the safety and well-being of their guests and that their facility can be trusted to maintain good practices.
Routine safety audits and inspections play a critical role in making sure businesses comply with the health code and naming any areas where they need to step it up.
Inspectors make sure that an organization complies with safety and hygiene regulations, stops food poisoning, as well as maintains cleanliness and hygiene requirements. The critiques are necessary to keep guests safe and healthy and to keep the organization’s reputation intact.
It is essential to inspect hospitality venues regularly to detect and remove safety hazards. These include:
- Kitchens: You should guarantee appropriate food storage, handling, and disposal, as well as assess the condition of equipment, ventilation, and electricity.
- Rooms: Checking lighting, electrical plugs, and stability of the fixtures and fittings should be done regularly. There should also be a guarantee of tidiness and cleanliness.
- Public Areas: The same sort of check should be made over public areas where it is mats, handrails, seating, or wall-mounted items that could potentially give way and so serve as a source of harm.
When top management dedicates itself to safety and undertakes practical steps to foster it, compliance pays off. You could scarcely find a better investment in preventing expensive and possibly reputation-damaging litigation that can arise from even a single work-related accident.
Ensuring the safety of your customers and the integrity of your brand is about more than just serving great food. Any number of things can - and do - go wrong on a day-to-day basis in a restaurant.
And when they do, it's best to have spotted the problem beforehand, rather than dealing with the aftermath.
But spotting problems and taking the necessary action isn't always easy. For instance, old frying equipment can easily be identified as a fire hazard. The extra grease needed to top off these spit trays provides a great source of flammable material for a fire if it were to catch or spread.
As a manager, you don't want your restaurant to be remembered for a slip-up that led to an accident or for something seemingly minor like a handling mistake during food prep.
The Role of Technology in Safety Management
What everything comes down to is this: Organizations must have strong safety governance in place to thrive and attain operational excellence.
However, let's face it: manual auditing and inspection methods are cumbersome. They are not capable of giving accurate results in a short amount of time. They can also be quite prone to errors, and if you make an error in a manual audit, there are often dire consequences.
At the very least, paper-based checklists and reports can lead to data discrepancies, making it almost impossible to track and analyze safety performance.
Moreover, manual processes can lead to:
- Ineffective data collection and analysis.
- Inaccurate reporting and record-keeping.
- Poor visibility into safety performance.
- Cumbersome identification and mitigation of risks.
- Substandard compliance with safety regulations and standards.
These factors combine to produce a very unsatisfactory safety dynamic.
What is the best course of action, then?
The use of digital audit and inspection checklists is top on the list. But how, precisely, do they help ensure compliance?
Robust Safety and Audits: Regulatory agencies need transparency, and digital audit tools offer an unalterable audit trail as well as real-time reporting. They can improve everything from the actual inspections and audits to the workflow and administrative tasks that follow. Not only can they eliminate or minimize fines; but they can also reduce many other costs associated with noncompliance. Audits and inspections do not have to be performed manually; they can instead be scheduled and triggered automatically.
Real-time Risk Monitoring: Being able to collect data in real-time is highly beneficial for organizations. Why? Because it allows them to keep a constant eye on emerging risks and threats, not to mention the number of immediate push notifications they'll be able to send about immediate threats is possible.
The result? Better identification of the unforeseen threats headed their way and shorter response times to potential risks.
Enhanced Compliance & Adherence: Staying compliant with regulations that constantly change can be difficult and time-consuming. But there is a range of tech-based tools that can help. From relatively simple—and oftentimes free—compliance checklists to more robust compliance management software, you can find a solution that works for you. These digital compliance tools can help streamline the process and, for many small institutions or programs, can have a very good ROI.
Protecting Data and Cyber Security: The increasing threat of cyber attacks has prompted organizations to take stronger measures to protect their data. Among the most important of these are encryption, intrusion detection systems, and employee training. Yet, another powerful tool for safeguarding data is the use of digital audit and inspection tools.
Incident Reporting: Using paper for reporting incidents is slow, error-prone, and gives limited visibility.
In contrast, when you use digital platforms, reporting becomes easier, clearer, and perhaps most importantly, faster. Submitting an incident can have more unrestricted, unambiguous interfaces that don't imperil key details. With these simpler interfaces come more instant forms of "who needs to know" alerting, if that's what you want (or don't, if it's a serious agency business that shouldn't allow easy snooping). The digital platform can also help the reporter identify what's next.
Access Control: Outdated access control methods like keys and swipe cards offer little to no security. They can be easily duplicated or stolen. And even if they could be trusted, these methods still come with problems of scale for any organization trying to manage a few hundred to thousands of employees.
But with the relatively cheap and increasingly simple-to-install systems now coming on the market, organizations can achieve the same quality of security at a substantially reduced cost and with many fewer headaches over access control.
Training and Knowledge Sharing: If you’re thinking what kinds of training and learning possibilities can digital tools offer in the realm of occupational health and safety?
Don’t worry.
When it comes to providing training, employers have several options at their disposal. They can offer in-person training to workers, providing them with a hands-on experience of the safety practices and processes that are expected of them. They can also use digital platforms to present this same kind of in-person training to their workers.
Whether in-person or through a virtual medium, this kind of training is important to the workers' learning process and can also induce a kind of bonding experience between the workers and their employer.
Between 2008 and 2016, an in-depth analysis of over 60 cases from all over the country, in a variety of industries, illustrated the benefits of using the safety-climate framework.
We studied these cases closely. What we observed was that, across the board, all industries that had gone through the safety audits and inspection process shared a common outcome—visible and marked improvements in overall business performance, as well as in daily operations.
How to Effectively Conduct Safety Audits and Inspections across Multiple Locations?
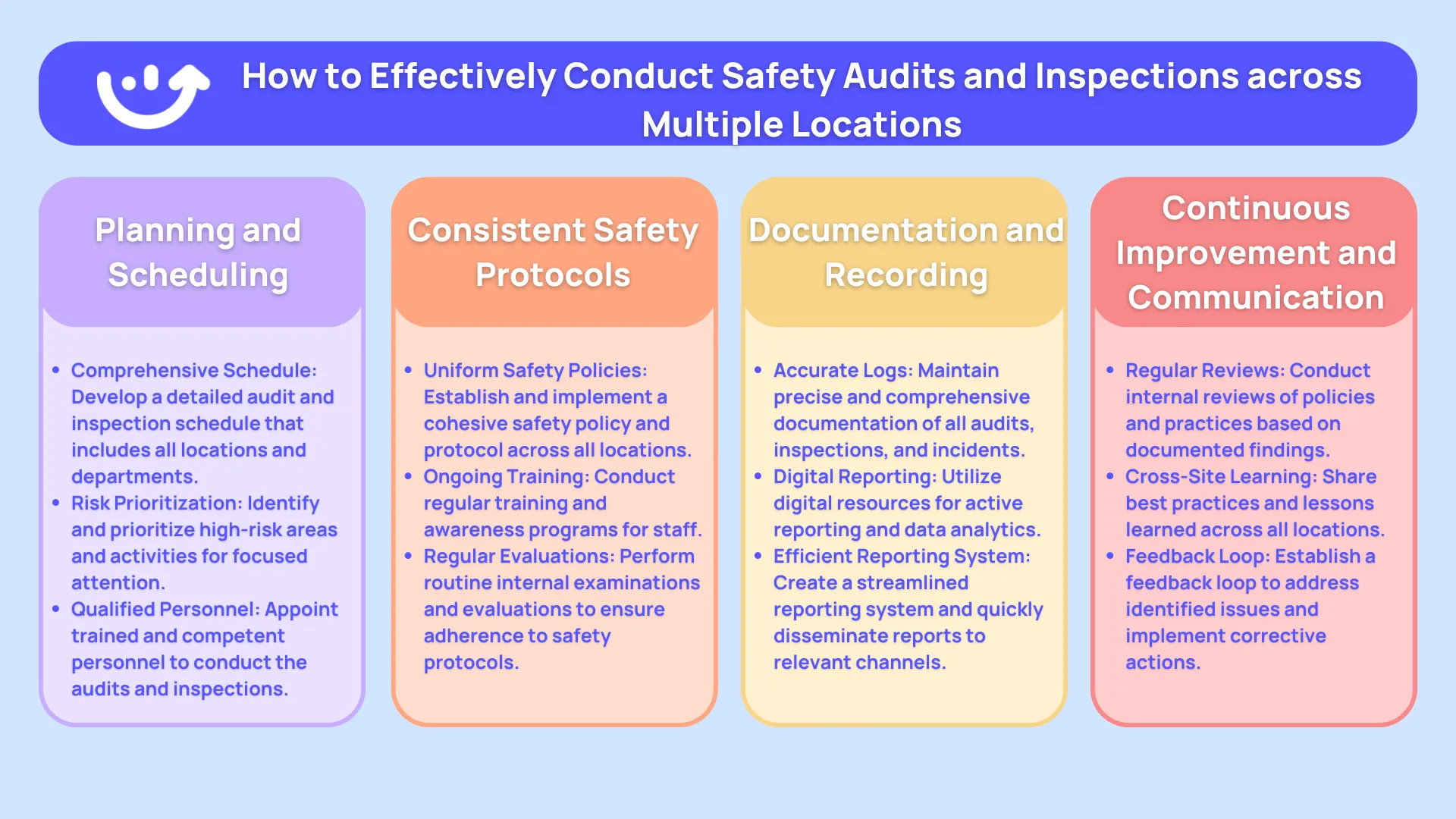
- Planning and Scheduling
Planning and scheduling are key components to ensuring effective safety audits and inspections. To adopt a holistic approach, organizations should:
- Create a comprehensive audit and inspection schedule that covers all locations and departments
- Identify and rank high-risk areas and activities
- Appoint trained and competent personnel to complete audits and inspections
- Allocate sufficient resources and budget
- Utilize digital solutions for scheduling and monitoring of audits and inspections
- Ensure Consistent Safety Protocols
All locations and departments of organizations should have the same safety protocols to avoid accidents, minimize risks, and maintain a safe working environment for all employees.
- Create a cohesive safety policy and protocol
- Initiate frequent instruction and consciousness programs for staff
- Carry out regular internal examinations and evaluations
- Release chief methods and learn from experience across all sites
- Employ virtual tools for live information submissions and analysis
- Documentation and Recording
With comprehensive logs, an organization can maintain an incisive audit trail that ensures regulatory compliance, supports decision-making in internal reviews of policies and practices, and facilitates informed continuous improvement efforts.
How to achieve that?
- Keep precise and thorough documentation of audits, inspections, and incidents.
- Exploit digital resources for active reporting and data analytics.
- Create a report system with no extraneous or verbose elements.
- Send off reports to the proper channels rapidly.
- Analyze the bug reports to determine point-to-point variability.
- Explain your findings so others in the company can think of a fix.
Overcoming Challenges in Multi-Location Settings

Has the thought of having to handle many places and have to keep reconciliation of safety protocols at all of them made your stomach turn? Well, we're here to help you. The first thing you need is a centrally-based, safety management system in place.
This will help make processes easier and keep things consistent across all of the locations.
The best part? The system allows you to fully install a safety coordinator at every single one of your specific locations—dig into the hazard analysis, create a safety plan specific to your location, and put plenty of muscle behind all the regular functions you'd want a safety plan to lean on. You do it once, and then in a properly organized franchise business, with a culture of compliance throughout the system, you just have to maintain and keep operating what you've built.
To start, you must communicate and train effectively. Ensure that your workers have a clear understanding of safety protocols and procedures and that they know how to carry them out. A good way to achieve this in your organization is through a concerted effort focused on safety through healthy communication. When was the last time someone in your unit talked to employees about what it means to be safe doing what they do?
Simple awareness can be the most effective means of stopping potential accidents. Yet, when workers are aware that accidents still happen, it is often because they do not know the whole story.
However, there is always room for improvement, which is precisely the point. That is where audit and inspection findings come into play. We can make good use of their information to make things even better. Here is how: When audits or noncompliance incidents occur, operations use those occurrences to identify the potential causes, then investigate and refine problem-solving methods at the appropriate levels in the command structure to deliver changes that will give the best results.
Don't overlook another essential element: acknowledging employees' safety efforts. When workers know their contributions to safety are seen and valued, they're more likely to take individual and collective ownership of safety protocols and procedures.
Leading by example and demonstrating a commitment to safety at the top of the organization sends a powerful signal that individual and team safety are priorities.
More than that, it standardizes the practice of safety throughout an organization, making it the norm as employees copy the behavior of their top leaders.
And it's not just the part of management; all employees must reinforce the practice by serving as good role models.
Wrapping it Up
Any organization must identify the dangers present in the workspace and set up a safe and healthy work environment.
Understanding the difference between audits and inspections can assist an organization in deciding the appropriate course of action to take and when to implement it.
OSHA recommends organizations perform safety audits and inspections at least once a year and preferably every six months. When done right, safety audits and inspections can effectively reveal hazards, unsafe practices, and work environments that violate safety standards. With routine audits and inspections, the organization can far better ensure the safety of its workers by finding and fixing problems before accidents happen.
Organizations integrate safety management systems to address a clear and present threat to their operations: the loss of human life, the environment, and sometimes their very existence. And when one talks about that threat, one talks at an elemental level. It fundamentally comes down to the security of a company's workforce.
If you can put a healthy and happy employee in a safe, secure, and disciplined work environment, you have won half the battle.
And what about the other half?
The fundamental principle of safety, well embraced, gives you an organizational structure that operates pretty much incident-free, at high levels of productivity, at a low cost, and that earns market share.
.webp)
%201%20(1).webp)