It is hard to keep identical safety rules active across all company sites. All company units from retail to production and service need to consistently follow workplace safety guidelines which the management must effectively coordinate across all locations.
Safety standards receive different levels of attention in business locations that run parallel operations. Some locations implement all emergency procedures while others miss important safety steps.
Real crises in the workplace occur when employees get injured, ultimately losing their jobs and operations coming to a halt because of failing to meet safety requirements. When different workplaces follow safety rules differently, management misses important emergency plans, skips hazard checks, and struggles to check if regulations are being followed.
Keeping the same safety rules everywhere within a company is essential but very hard to implement. Yet this can still be made possible by tracking and sharing updates using an online system built specifically to streamline safety protocols.
According to The Economic Daily, there were 2.6 million workplace injuries and illnesses in private industry in 2023, down 8.4 percent from 2022.
This article shows how a digital tool makes safety work better by creating standard process directions, checking everything matches the required rules, and letting different units share important updates.
Priced on per user or per location basis
Available on iOS, Android and Web
Current Challenges in Safety Protocol Management
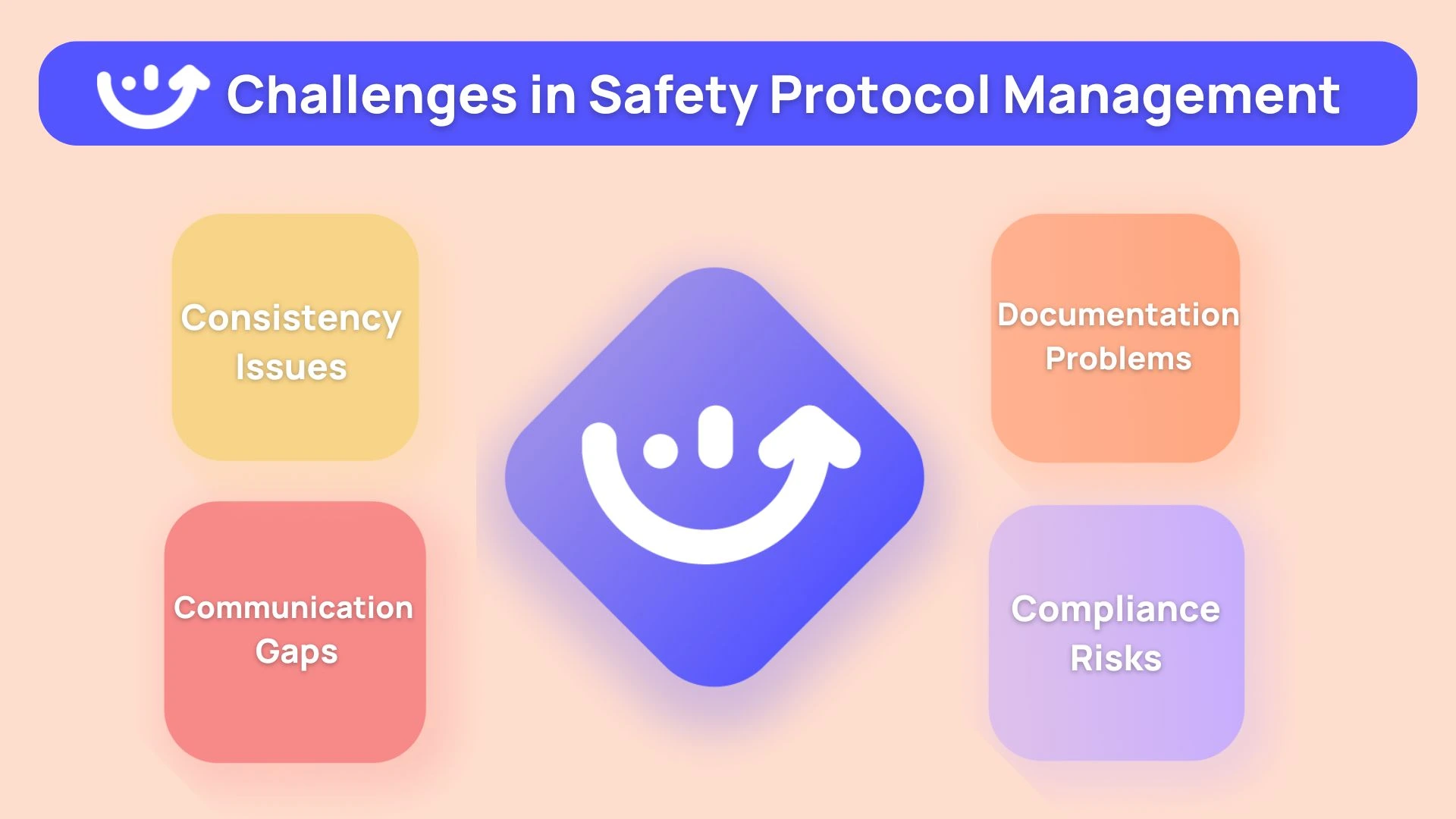
Safety management across multiple workplace units faces problems that hurt the success of safety procedures and health guidelines. Here are the main challenges businesses face:
1. Consistency Issues: Each safety site needs different procedures because companies struggle to make these practices work the same everywhere. Unstable training for employees creates unclear emergency preparedness methods that result in errors.
2. Documentation Problems: Most companies keep their safety checklists on paper and these documents are easily misplaced or not properly completed. Safety logs that haven't been updated present problems during workplace hazard checks and make compliance reviews harder.
3. Communication Gaps: Reporting incidents takes too long which reduces emergency response speed. Employees are left unaware of their new safety requirements because properly shared information does not reach them. When no real-time system is active teams fail to notice evolving workplace dangers which elevates the safety risk.
4. Compliance Risks: Recording workplace safety compliance becomes a difficult process when your system relies on outdated paper records or split infrastructure. When safety records do not exist or contain errors organizations face unsuccessful inspection outcomes. After incidents happen teams usually do not follow standard procedures leading to inconsistent safety tracking and regulation compliance.
To meet safety challenges today, we must use up-to-date tools and technology that helps make safety work faster and better.
Transforming Safety Protocols with Xenia: A Three-Step Approach
Transforming safety protocols across multiple locations can be streamlined using Xenia's comprehensive platform. Here's a three-step approach to enhance safety management:
Step 1: Digitize Safety Documentation
Moving from manual records to digital documents helps organizations apply safety rules consistently while building solid data history. Our digital system stops safety mistakes from happening because every protocol is recorded properly.
Xenia's Key Features
Customizable Checklists: You can build customized safety checklists for all your locations through Xenia's simple drag-and-drop system. Your frontline staff can see and use every safety procedure because it all appears in one place.
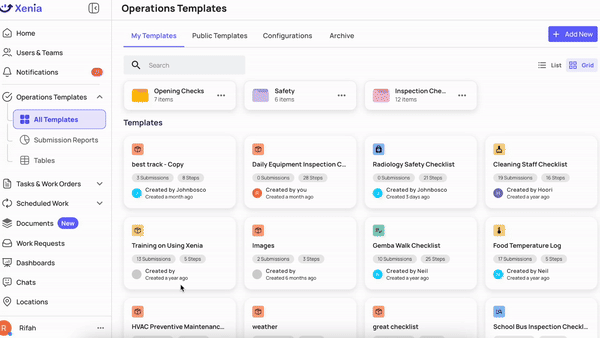
Photo and Video Attachments: Protecting your workplace safety efforts is possible with Xenia's photo and video attachment feature in checklists. The feature shows safety conditions through visual proof which helps everyone report and hold each other responsible correctly.
Digital Signatures: Users can verify safety procedures through online signatures which create legally binding records with authorized team members. These features help teams stay responsible while making audit and compliance work easier.
Offline Access: With Xenia, teams stay productive by updating safety guidelines at any time and in any location even if they don't have internet access. Teams can work on safety documentation offline and stay on track since the software always connects to the main system when the internet is back.
Step 2: Automate Safety Communications
Effective communication helps respond fast to safety hazards. With Xenia's automation tools employees receive instant safety updates quickly.
By automatically sharing safety updates a workplace can respond quickly and deliver consistent safety information which helps control risks and improve workplace protection.
Xenia's Key Features
Real-Time Incident Alerts: Through Xenia notification systems any person reporting safety matters gets immediate alerts on their mobile or computer devices. Teams receive complete data about the occurrence including geographic information, photo, and video footage to respond without delay.
Automated Escalation Workflows: The system's predefined workflows immediately handle dangerous safety problems. Xenia moves unresolved incidents to supervisors and departments when a set time limit expires. Teams use customizable workflows that match different offsite incident responses based on their priorities.
Effortless Protocol Updates: Xenia helps send the latest safety protocols simultaneously to every site. Existing protocols reach every department instantly when distributed through our platform. Our system sends alerts only to employees who own designated safety response tasks.
Role-Based Access Control: Safety information with critical components must remain protected from unauthorized users. Staff members need permissions before they can work with safety data according to their assigned roles under Xenia's control system. Each staff member gets permission to see only the information they need for their role so managers handle compliance records and escalation methods and line staff see essential checklists and directions.
Step 3: Monitor and Improve Safety Performance
To successfully prevent risks, businesses need to continuously monitor and evaluate safety data. Through its tracking and safety improvement features, Xenia helps every business location achieve better safety results. Safety protocols become stronger through data analysis which helps businesses stop issues before they develop.
Xenia's Key Features
Custom Dashboards: View your safety performance numbers in real-time through personalized dashboard displays. View safety numbers and team adherence results to take fast action and base important selections.
Trend Analysis: Use a complete dataset to find safety issues that keep appearing. Look at what happens often and how employees fail to follow safety procedures to take steps that stop future risks.
Cross-Location Comparisons: Look at how different sites perform with safety to find where changes need to happen. Find safety weaknesses at individual units and enforce the same set of safety requirements across all units.
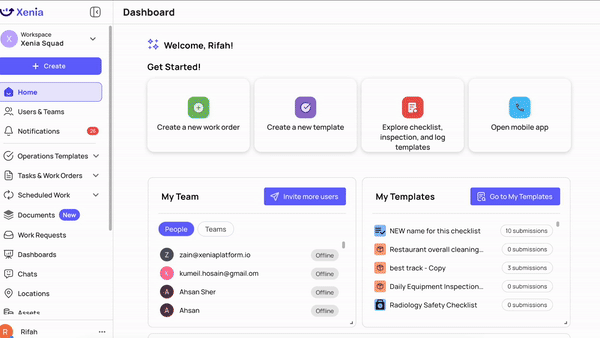
Automated Compliance Reporting: The system creates safety compliance reports without manual effort. Put safety checklists with workplace hazard reports and incident data together so audits work better and faster.
Implementation & Features: Step-by-Step Process
Rolling out our digital safety system Xenia follows a defined method that handles every basic part of safety management.
Here's a step-by-step guide:
Step 1: Configure Safety Templates
Begin your project by designing procedural frameworks for workplace risk evaluations, emergency responses, and everyday safety work. Match these templates to match what your locations need while staying safe at work. Safety templates provide the required structure for standard safety procedures.
Step 2: Set Up Notification Workflows
Design automated systems to notify teams when incidents happen and share changes happen. Once a workplace hazard is recorded our system transmits the alert directly to departments that need to take action. The escalation process helps safety teams handle emergencies faster so they do not create delays.
Step 3: Define User Roles and Permissions
Groups users with job duties and lets them see only the data they need with well-defined User Roles and Permissions. Managers must see compliance records while frontline employees depend on safety checklists to do their jobs. Set up a simple path for people to move through different work areas plus track what each area shows.
Step 4: Leverage Key Capabilities
- Let employees submit safety reports from their smartphones to monitor work hazards instantly.
- Our system will run safety checklists to prevent important daily steps from being forgotten.
- Send official updates directly to every employee for instant safety awareness.
- Safety compliance tracking helps you conduct audits faster and maintains secure digital records of all safety work processes.
Step 5: Follow Best Practices
Update your safety audit templates according to changes in workplace safety rules. Check your safety protocols regularly and teach your workers new information through formal training events. Every organization member must learn and apply set incident response approaches to maintain safety standards.
Benefits & ROI on Implementing Advanced Safety Protocols
The digital transformation of security systems provides measurable gains in productivity, risk reduction and cost savings.
1. Operational Improvements
Digital systems enable faster incident response, reduce downtime and reduce losses. When safety measures are consistently implemented, employees and stakeholders build trust in the system. Advanced safety training ensures that every employee understands their role in maintaining a safe environment. Additionally, fully digital documentation simplifies audits and analysis, making the compliance process seamless.
2. Risk Reduction
The approach to job risk assessment reduces safety incidents, which means less legal liability and lower insurance costs. Improved incident reporting ensures safety no information goes unnoticed, helping to comply with workplace safety standards. Proactive risk management strengthens an organization’s ability to address threats before they escalate.
3. Cost Savings
Companies can save resources by reducing incident-related costs such as legal fees and lost productivity. A strong safety record also reduces insurance premiums. Automation reduces the time spent on administrative tasks, such as incident reporting and monitoring compliance, further reducing administrative costs
Success Metrics to Gauge
Measuring success is essential to assessing the impact of digital security transformation.
Key Performance Indicators (KPIs)
- Incident Rate Reduction: Monitor the reduction in reported incidents to assess the effectiveness of the platform in identifying and mitigating risks.
- Protocol Compliance Rates: Monitor consistent adherence to security procedures at all locations. High compliance rates reflect strict adherence to workplace safety standards.
- Response Time Improvement: Measure incident processing time from initial report to resolution. Faster response rates indicate improved productivity.
- Training Completion Rates: Ensure employees have completed training modules and remain familiar with emergency planning and workplace risk assessments.
ROI Measurements
- Cost Savings Calculation: Compare incident-related costs before and after implementation, including legal fees and downtime.
- Risk Reduction Metrics: Evaluate improvements in compliance scores and audit readiness. Fewer safety incidents directly contribute to lower premiums.
- Efficiency Improvements: Track manual processes such as submitting reports or maintaining checklists to measure time saved.
To Sum Up
Ready to raise your organization’s security standards? Schedule a Xenia demonstration today to see firsthand how our product can revolutionize security protocol management for multi-unit operations.
Xenia empowers businesses to maintain continuous safety management, streamline emergency procedures, and conduct effective workplace risk assessments. Through real-time reporting tools, automatic compliance monitoring, and proactive risk management, Xenia drives a pervasive safety culture across all locations
We prioritize workplace safety standards.
Start on your journey to a safe, compliant, and efficient organization today!
.webp)
%201%20(1).webp)