Prioritizing health and safety in manufacturing operations isn’t just a compliance obligation; it can affect the company’s bottom line.
Within 1 in every 6 Americans are estimated to be sick and die from foodborne illnesses.
With these statistics imagine if the food inspector finds food hazards or equipment issues during an unannounced inspection there can be penalties, fines, and possible closure. These violations can cost restaurants a lot of money from paying attorneys and court fees.
This is merely a starting point.
While there are some pretty substantial fines associated with workplace injuries – not to mention the impact on the employee and his or her family – accidents can affect a company’s reputation and ability to do business, too.
The National Safety Council reports the sector of leisure and hospitality is ranked 7th in nonfatal injuries and 6th in deaths per 100,000 workers for 2020.
However, there is always a silver lining.
Investing in a solid health and safety program, including proper equipment, training, and culture, is the strategic way to protect your workers and enhance business scalability.
As a manufacturer, you want to ensure that you are monitoring and managing the quality of your processes effectively.
However, the real puzzle to solve is; How do manufacturers ensure that quality checks are instituted in every operation?
About SafetyChain
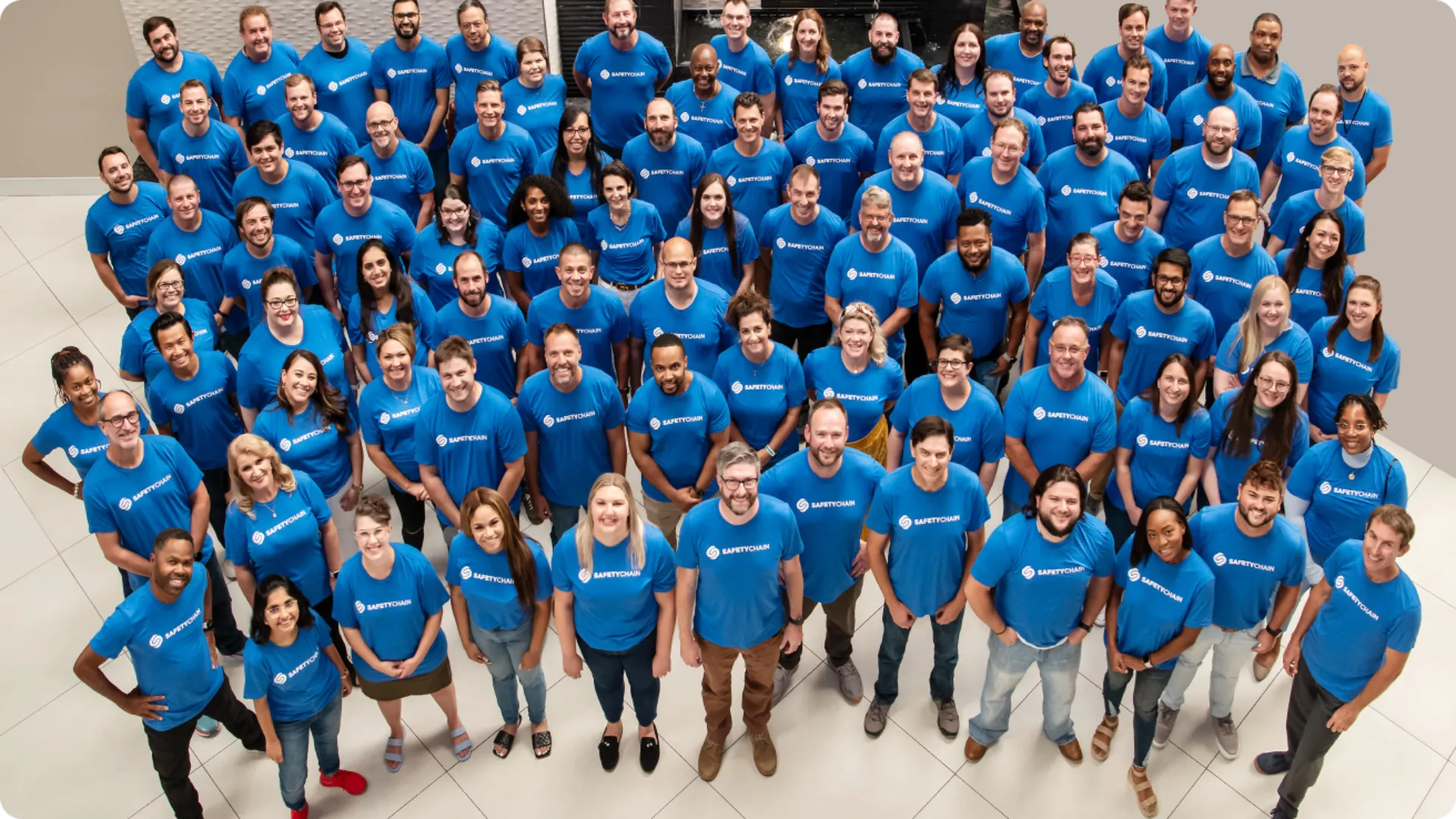
SafetyChain is among the leading digital solutions in manufacturing safety providing end-to-end safety solutions for EHS management. Through real-time visibility and control, it empowers stakeholders with proactive involvement in quality checks, supplier evaluations, performance metrics, and benchmarking leading to continuous improvement possibilities.
Additionally, SafetyChain enhances productivity and risk mitigation, while improving compliance by digitizing incident analysis and enabling proactive maintenance.
SafetyChain, which was founded in 2011 by a seasoned executive team and investors with whom we have collaborated for over 15 years, spearheaded and is still leading SaaS innovation in the process manufacturing sector.
We service over 2,000 sites throughout North America from our locations in the San Francisco Bay Area (HQ) and Chicago (Customer Success), where all of our in-house project and support teams are situated in the United States.
However, don't jump on the bandwagon because it's rolling through town; what's hot in the market may not fit your specific manufacturing needs.
In this article, we have covered some of the noteworthy SafetyChain alternatives, evaluating their features, functionalities, and suitability for diverse manufacturing environments.
By the end, you will gain insights into the array of options available, empowering you to make informed decisions tailored to their operational requirements and strategic objectives.
Best SafetyChain Alternatives
Here's a quick look at some of the best alternatives to SafetyChain that are hot in the market these days.
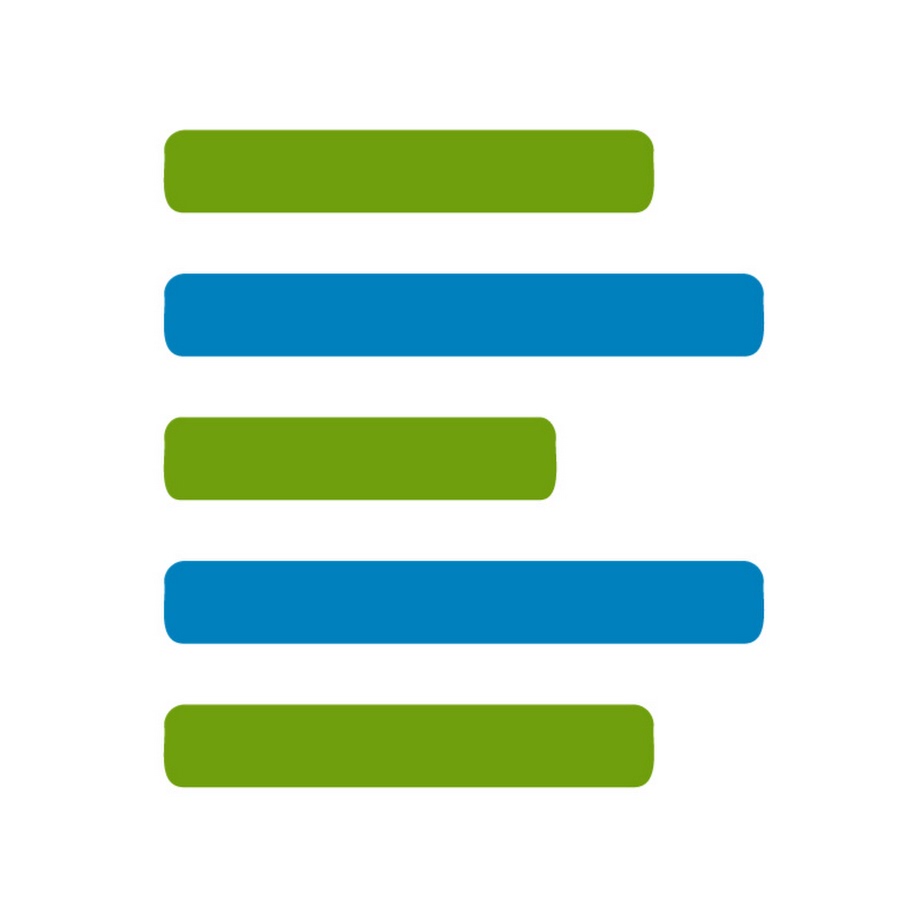
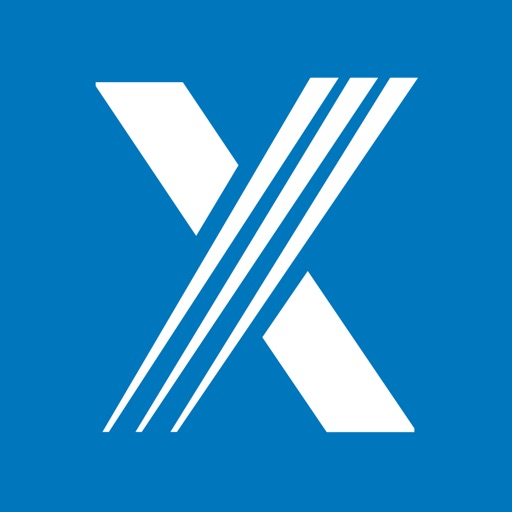
1. Xenia- Overall Best SafetyChain Alternative
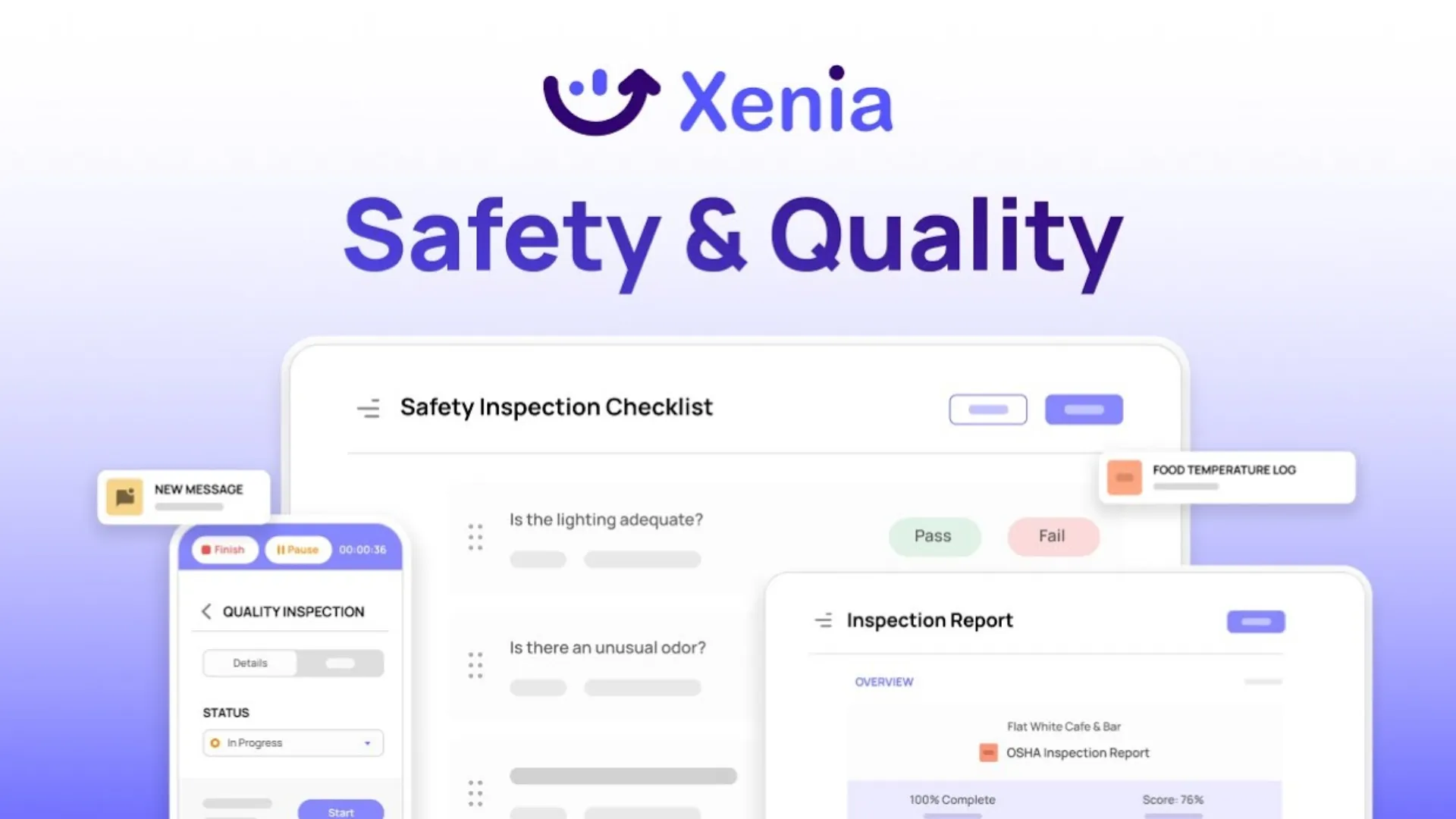
The top SafetyChain alternative, Xenia offers an end-to-end solution integrated with maintenance management, daily operations, and safety compliance modules giving manufacturing managers and stakeholders a user-centric platform tailored to their needs.
Ensuring the work environment is secure entails many critical tasks, including managing injured workers and the required recordkeeping, as well as maintaining compliance with safety audits and inspections. The unified solution provides organizations with the necessary EHS strategies and checklists to guarantee the safety and well-being of their workforce.
Nevertheless, Xenia’s scope is much bigger than regulatory inspection, it’s much bigger than that.
A core competency is its ability to standardize any operational process via customized templates. Automating processes and streamlining inspection, maintenance, or regular tasks, can help organizations to reduce errors and increase productivity.
On top of that, with the help of in-app chats, the entire team can stay informed and quickly communicate incidents or potential risks. These chats allow users to attach multimedia to the messages that they send in both one-on-one and group conversations.
Also, EHS managers can be productive even when not connected to the internet. Thanks to offline functionality. The mobile app works in such a way that, when they regain an internet connection, everything syncs across the web-based software and the app as if there had been no time lag.
And we’re not done yet
A centralized request management and approval process streamlines workflow by providing transparency and maintaining oversight over how resources are being allocated and what they are being expended for.
The dedicated Analytics & Reports section lets manufacturing plants extract deep insights from past inspection data, historic evidence of completed vs. pending work, and tons of other things. As a result, real-time visibility renders itself a particularly useful feature during in-depth inspections or audits.
Key Features
- Customizable Checklists: Customize maintenance, Quality control, safety and compliance inspection forms, checklists, and even SOPs to make them align with your organizational requirements and legal obligations.
- Inspections & Audits: To prevent near misses, generate safety work orders for each procedure carried out on the premises. Record each stage of a process in real-time, alongside its safety inspection.
- Automated Workflows: Simplify the operational or inspection activities by setting up automated reminders for proactive safety management.
- Corrective Action tracking: Assign and track corrective actions that stem from audits to ensure quality concerns are resolved and ensure compliance with regulations.
- Records Management: Establish a central repository for all safety-related records, including permits, and training documentation that is easy to locate and assess.
- Offline Functionality: Continue to work even with spotty or no internet, and once you are connected again all of your data will sync automatically.
- Advanced Reporting & Analytics: Generate detailed reports to identify production trends, how to improve them, and track equipment performance, maintenance needs, and team performance metrics. This enables data-driven to optimize manufacturing processes and drive continuous improvement across all operational activities.
Pricing
- Free Forever: For up to 5 users with access to all the basic features.
- Starter: $99 per month for the first 15 users, with access to core features.
- Premium: $199 per month for 15 people, including access to all the core and advanced features and functionalities.
- Custom: Do you need anything exclusive to your organization?
Priced on per user or per location basis
Available on iOS, Android and Web
2. BenchMark Gensuite EHS
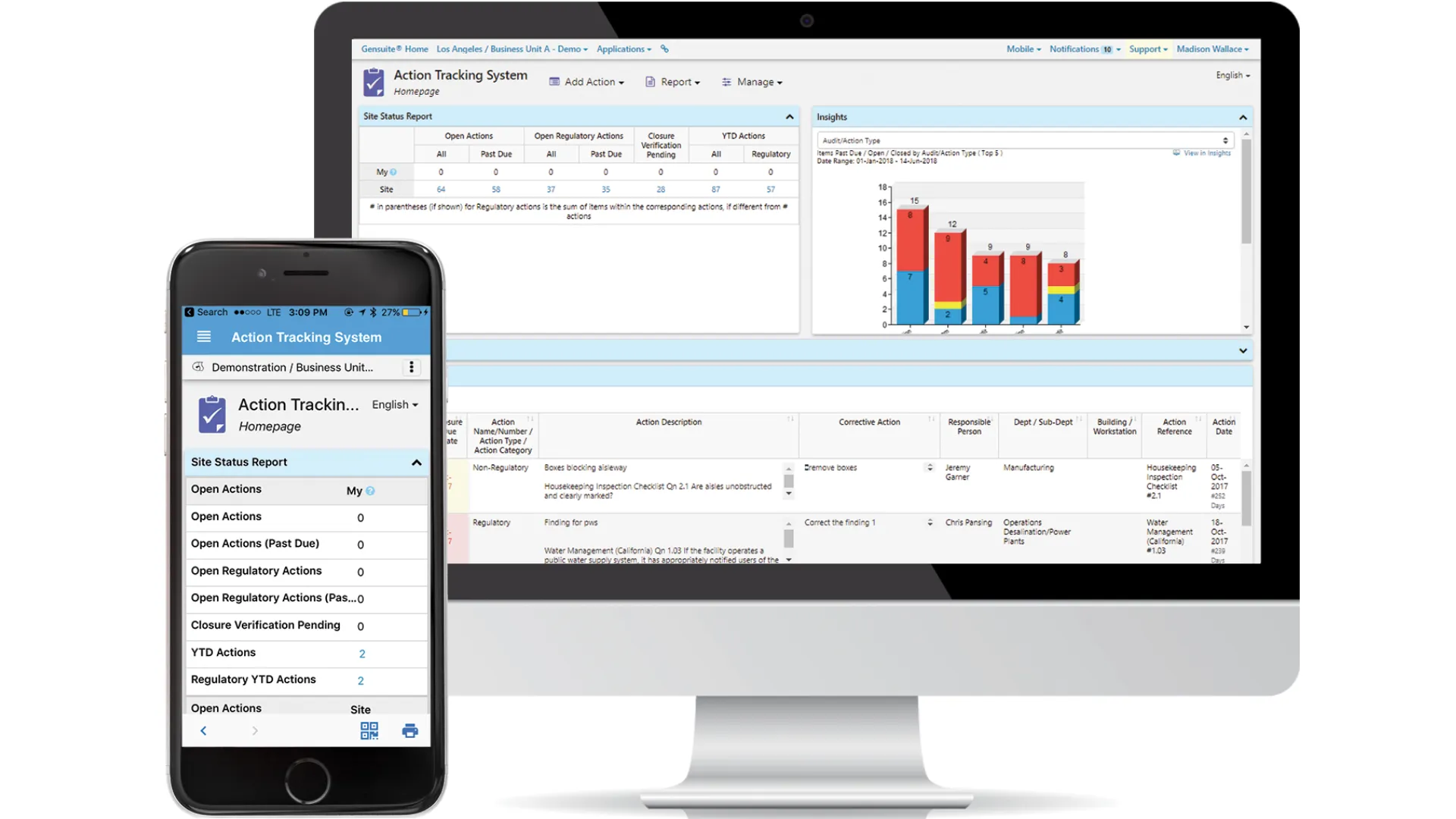
The next leading SafetChain alternative, Benchmark Gensuite offers a cloud-based software solution suite that allows you to manage EHS (Environmental, Health, and Safety), Sustainability, and ESG (Environmental, Social, and Governance) Programs.
The software focuses on reducing risk, building safety programs, and compliance with global regulatory mandates. With their cloud-based solutions, you can bring people of all levels at your organization together in one place to help build a risk management and compliance culture.
This Equipment Management Suite allows for the equipment and all activities or malfunctions to be managed easily. Its features include preventive maintenance inspections, inspection history tracking, and more.
Taking it further, automation and configurable reporting empower teams to focus on program improvements while maintaining compliance standards and meeting customer expectations. The integration of quality management systems permits organizations to limit error, and track results in real-time while remaining proactive and responsible stewards of the environment.
Key Features
- Compliance Management: Leverage robust tools for managing regulatory compliance, and help ensure that your organization stays in alignment with evolving safety regulations across multiple industries.
- ESG Reporting: Allows organizations to track and report on various ESG metrics. This allows for transparency and accountability in sustainability initiatives.
- Inspection Management: Enables efficient managing to consist of actual-time assessments, keeping an eye on conformity to regulatory specifications.
- Document Management: provides centralized document management, allowing companies to preserve, organize, and keep track of crucial documents.
Pricing
- For pricing, contact the Vendor.
3. Intelex
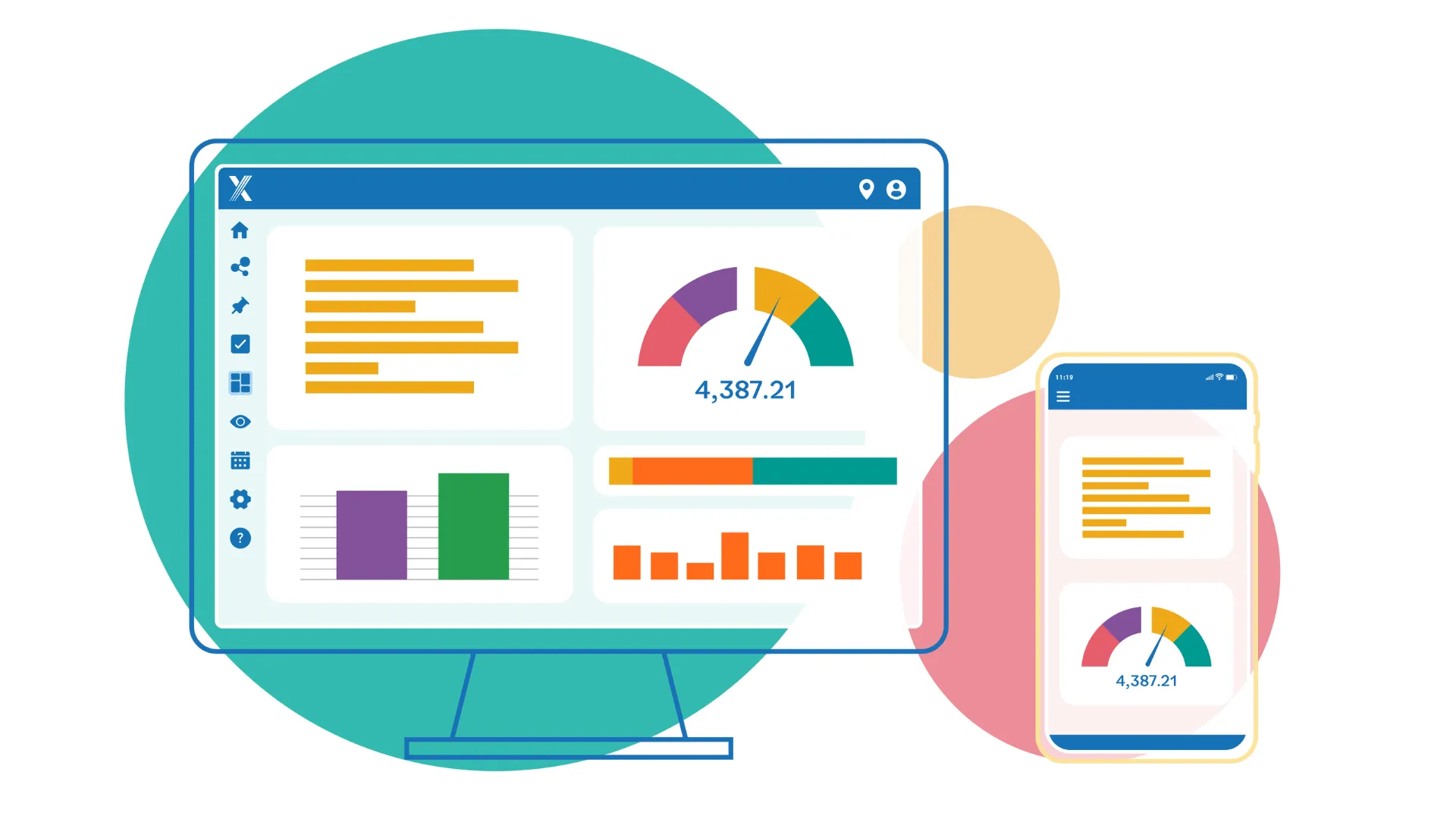
If you're casting around for a SafetyChain alternative, Intelex is another safe choice in the field.
This robust platform allows clients to extract and structure critical business data to stay compliant with regulatory requirements, mitigate risks to the business, and proactively manage critical incidents. Thus improve operational performance by engaging with all personnel across all operations via a suite of critical features relevant to all industries.
In addition to its core audit management solution, Intelex offers a suite of health and safety features to help businesses identify and control occupational health and safety risks and reduce the potential for workplace accidents. With functionality ranging from occupational injury and illness management to audits management and inspection management, Inetlex is perfectly placed to help health and safety managers ensure the safety and well-being of the workforce and maintain compliance with a wide range of health and safety legislation.
Instead of having different systems to manage quality processes, compliance, and risk, Intelex offers a platform to manage all three. By centralizing these functions, Intelex streamlines processes, boosts visibility, and allows for more proactive decision-making improving operational excellence and reducing risk.
Key Features
- Regulatory Compliance: Compliance: Tools that can keep you in compliance with the government; this can help an organization change its controls with time, regulations, and any other routing that needs to be changed.
- Audit Management Software: Enable businesses to conduct efficient, timely audits to identify deficiencies and ensure the organization meets their high level and industry standards.
- Compliance Tracking: Whether you need to track training, licensing, or compliance to regulations or standards, compliance tracking software solutions help meet your goals, providing visibility into overall compliance status and automating the corrective actions required when noncompliance situations arise.
- SupplyChain Management: By allowing organizations to identify risks and improvement opportunities, enhance transparency, and promote collaboration with suppliers.
Pricing
- For pricing, contact the vendor.
4. Workhub
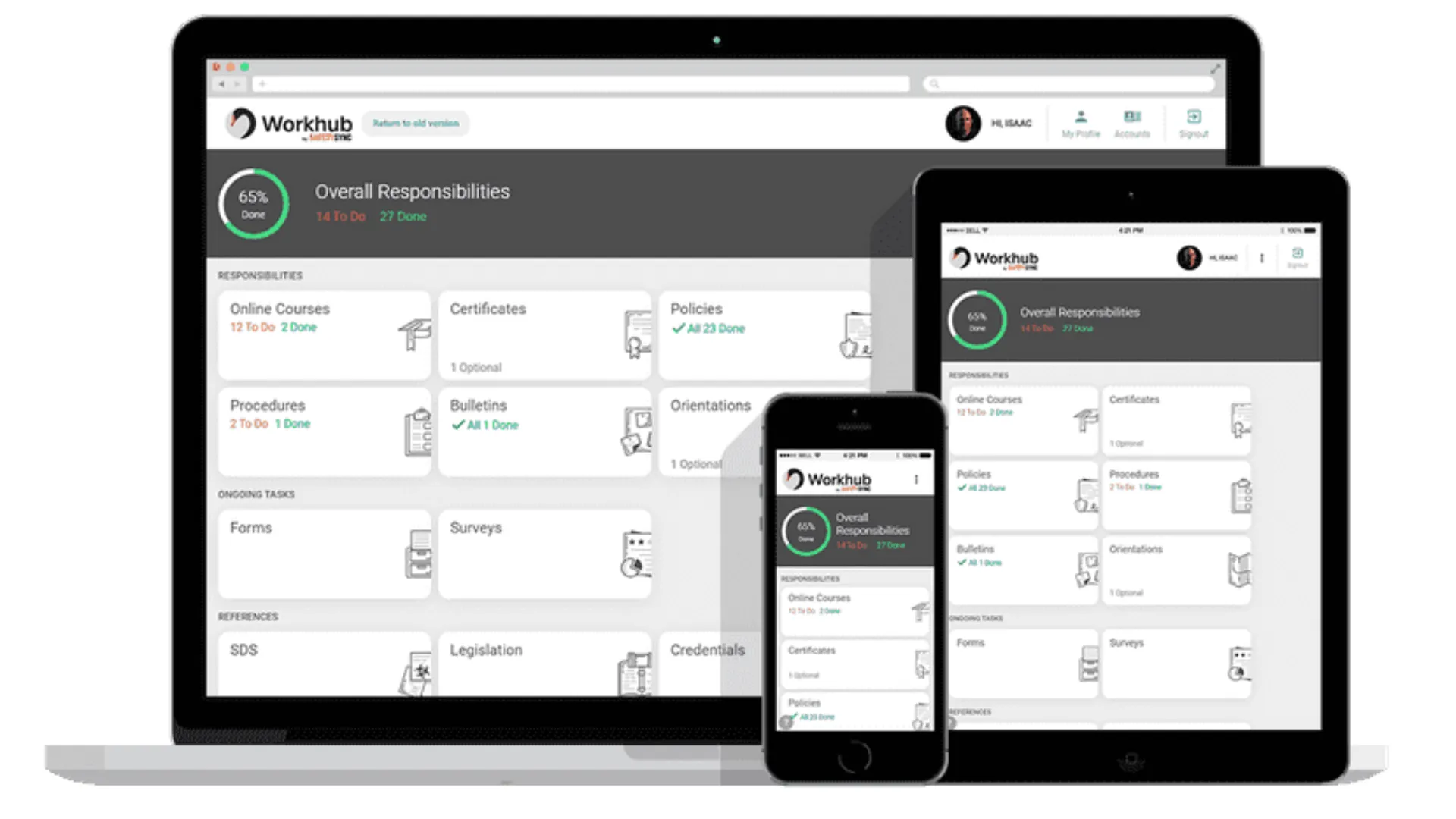
Designed to quickly and easily streamline the management of training, procedures, policies, inspections, and more, Workhub offers a comprehensive health and safety compliance software solution for companies in virtually every industry.
The solution serves as the user-friendly hub that makes managing health and safety compliance easier than ever.
One of Workhub’s greatest selling points is its affordability and comprehensiveness. As the most extensive and affordable system in the safety and compliance software market, Workhub includes more than 25 customizable tools that organize workflow and communicate health and safety programs to your workers. With the ability to provide thousands of tools that fit your company’s unique needs, Workhub delivers unmatched value for organizations looking to strengthen their safety and compliance initiatives.
In addition, Workhub’s software is easy to deploy, bringing improvements to workplaces within hours of adoption. They offer free implementation assistance so the transition is smooth and employees can learn onboard quickly maximizing efficient use of the software in addition to regular day-to-day work.
Key Features
- Operating Procedures: Easily manage operating procedures, define standard operating procedures for various tasks and activities; communicate this as the standard operating procedure to your asset and reaction team.
- Inspections: Conduct easy inspections regularly. Inspections can help organizations identify hazards, compliance issues, and opportunities for improvement.
- Incident Reporting: This communication platform greatly facilitates and encourages the worker to report all accidents, dangerous near misses, and other safety-related events.
Pricing
- Free
- Standard:$3
5. Cority
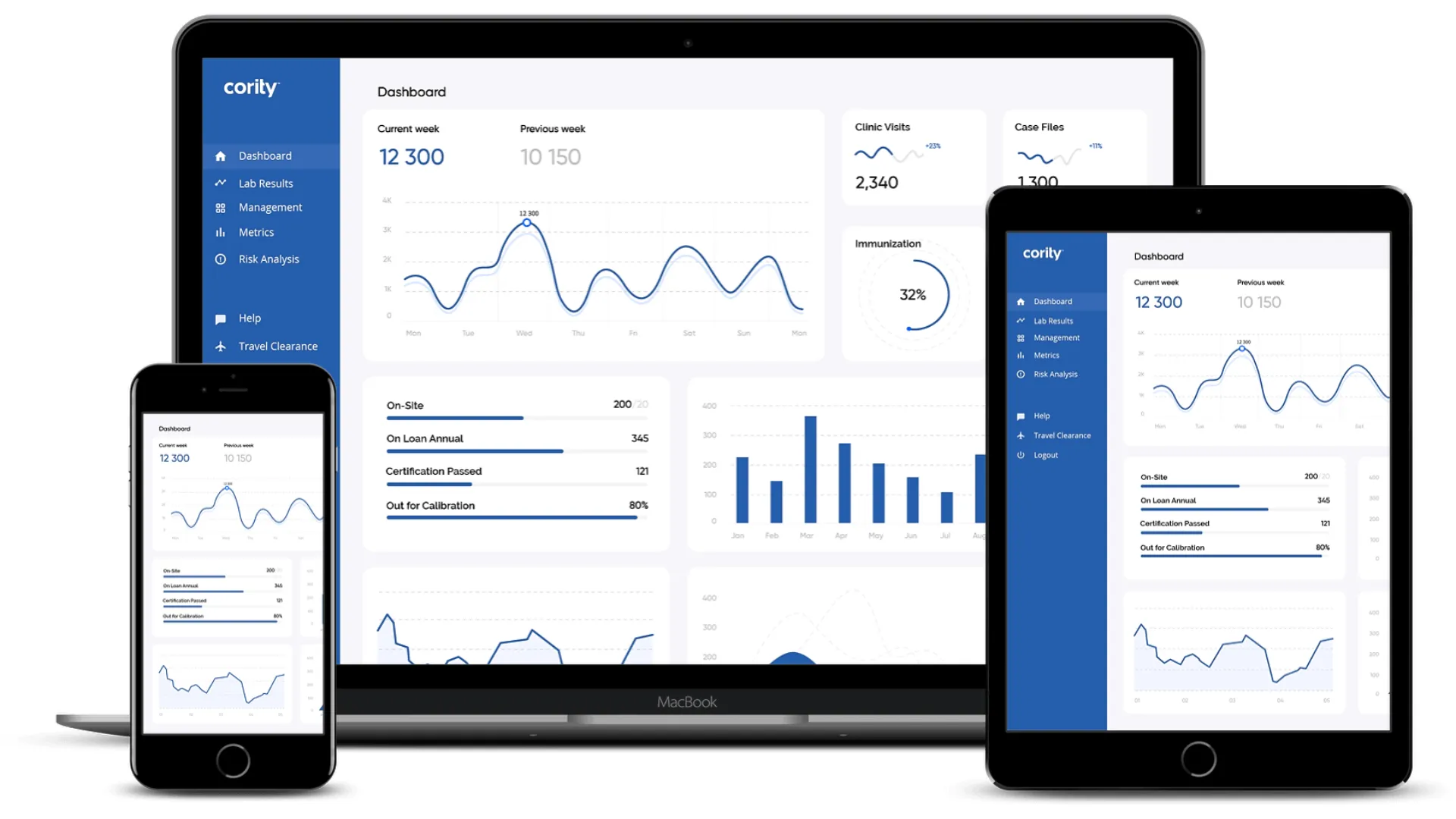
Cority is the leading SafetyChain alternative, offering tailored cloud-based enterprise quality management and compliance software for mid to large-sized global manufacturers.
It provides tailor-made, comprehensive core process functions including full integration for supplier quality, customer complaints, nonconformance, corrective actions, document control, employee training, and competence.
This comprehensive solution lets managers achieve the most effective streamlined, increased operational efficiencies, risk reduction, and compliance with industry standards and regulations.
That’s not all.
The platform also serves as an integrated data hub to feed critical performance and risk metrics into the exceptional platform users' performance, risk, and environment.
In addition, it serves sectors such as automotive, aerospace and defense, oil and gas, and medical device products.
Key Features
- Compliance Management: Streamline your compliance processes and ensure adherence to regulatory requirements.
- Incident Management Solution: Manage incidents effectively from the initial report through to resolution, minimizing their impact on operations and providing corrective action swiftly.
- Audit Management: Using out-of-the-box audit templates, you can easily prepare for audits by standardizing the process of capturing audit information and generating reports.
- Risk Management: Identify, assess, and mitigate risks across your organization, with Cority’s robust risk management tools, ensuring proactive execution of risk mitigation strategies.
- Document Management: provides a secure electronic environment to manage, share, and store your documents.
Pricing
- Contact Vendor
6. MasterControl Quality Management System
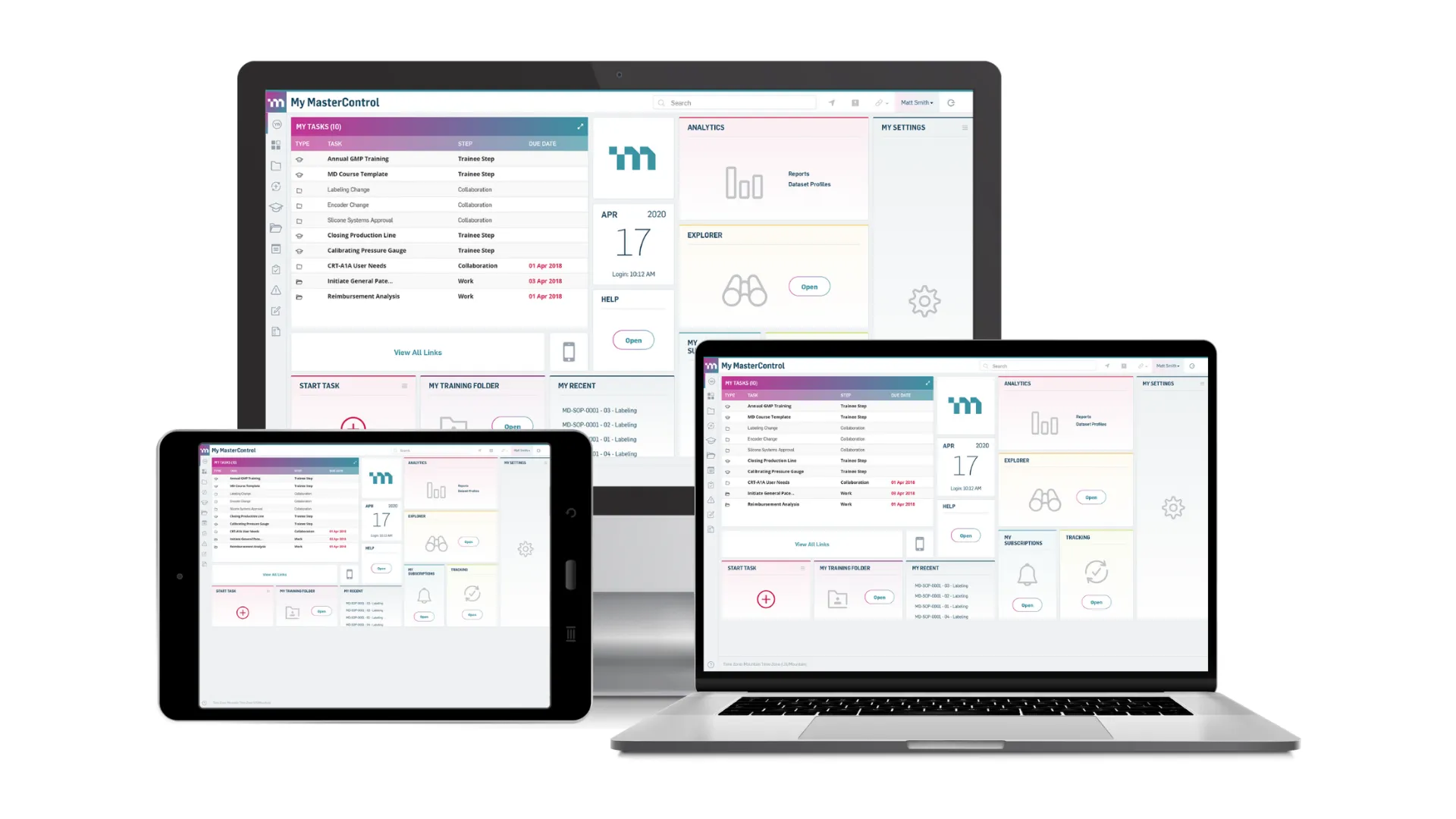
If quality is just considered an afterthought or a checkbox, it will never be a differentiator. Quality at the source is achievable with an end-to-end digital quality management system, such as MasterControl's Quality Excellence, which also eliminates compliance problems.
A regulated company's capacity to develop new goods, enter the market fast, and maintain growth depends on its ability to implement thorough and compliant quality management. However, it needs the appropriate infrastructure and resources, and paper-based procedures are no longer enough in the fiercely competitive market of today.
MasterControl's digital quality management software (QMS), Quality Excellence, streamlines processes, demonstrates compliance and makes quality a true differentiator in the marketplace by automating quality throughout the whole product life cycle.
Key Features
- Quality in the Cloud: By completely digitizing and consolidating formerly paper-based data and documentation, cloud QMS software allows for more regular software upgrades, which facilitates ongoing process improvements for quality and compliance.
- Automated Regulatory Compliance: By automating crucial quality activities including document, training, quality event, supplier, and quality audit management in a single end-to-end system, you can reduce the burden of compliance and enhance the quality of your products.
- Connected QMS Platform: Quality data can drive change and improvement across the whole product life cycle when it is digitized, gathered, and integrated. This makes quality data a commodity that can be used by any size organization.
Pricing
- Contact Vendor
7. TrackWise Digital
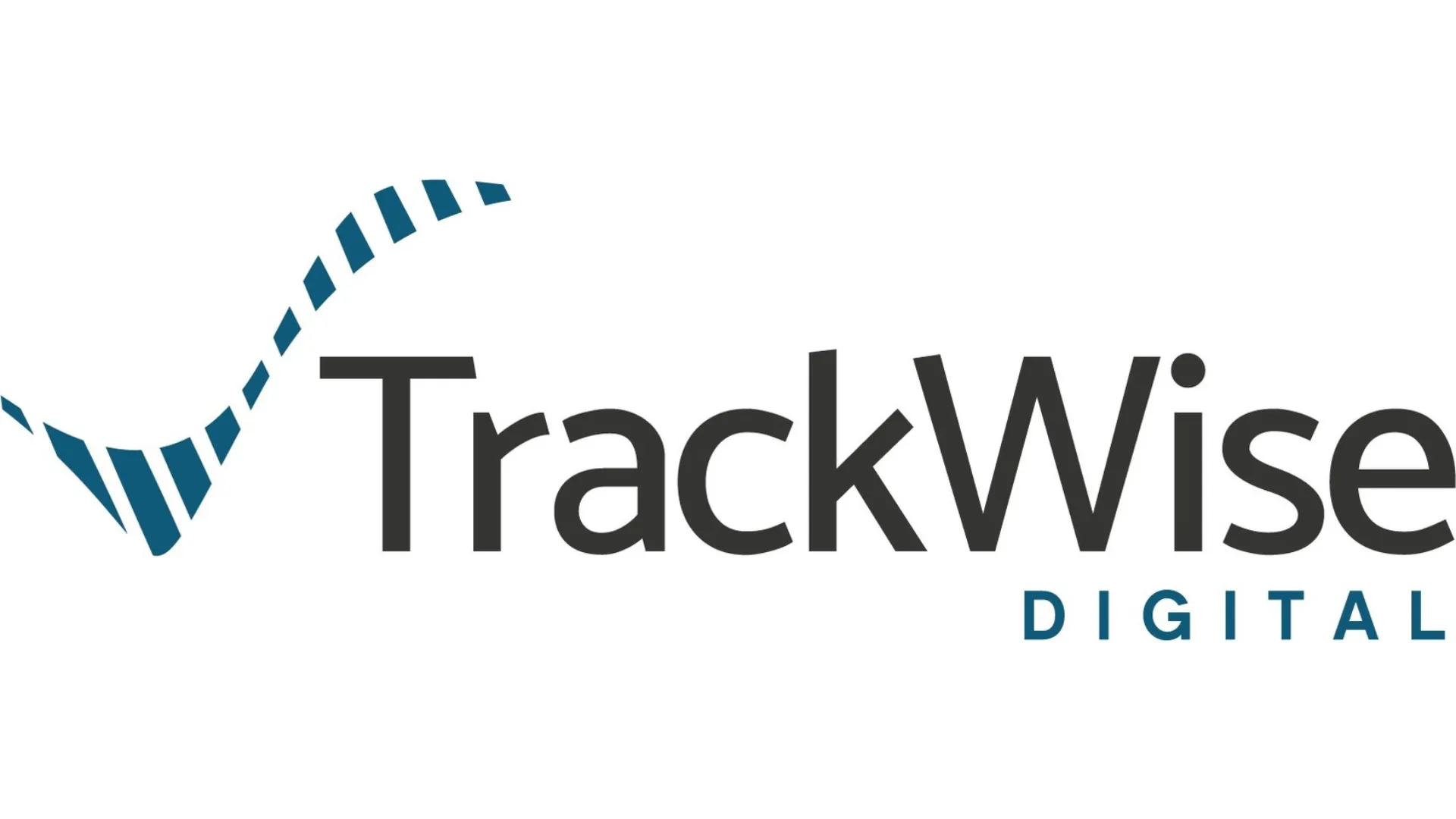
With integrated modules that support quality, compliance, and more effective and efficient decision-making, TrackWise Digital is a leading cloud-based quality management system (QMS). With AI-augmented features like auto-summarization and auto-categorization, TrackWise Digital's enhanced capabilities help organizations meet their quality management productivity and efficiency targets.
TrackWise Digital is the first QMS in the market to use AI to improve decision-making linked to quality, enabling a change from reactive to proactive quality.
Users can utilize quality data to improve company-wide performance and fortify their quality culture by using sophisticated analytics and reporting across all quality processes.
Key Features
- Simplifying Quality Management: With TrackWise Digital, an integrated quality management system that is strong, scalable, and flexible enough to handle both basic and complicated operations, you can reduce quality complexity and dismantle silos.
- Connecting Stakeholders and Suppliers: TrackWise Digital enables suppliers and manufacturers to work together in a smooth, integrated environment while reducing risk, increasing productivity, and protecting customers. Connect teams inside and outside the organization to collaborate effectively and get insight into all quality procedures.
- Intuitive Quality: TrackWise Digital improves end-user productivity with timely alerts and effective reporting. You can control quality anywhere at any time and on the road with mobile capabilities.
Pricing
- Contact Vendor
8. ETQ Reliance
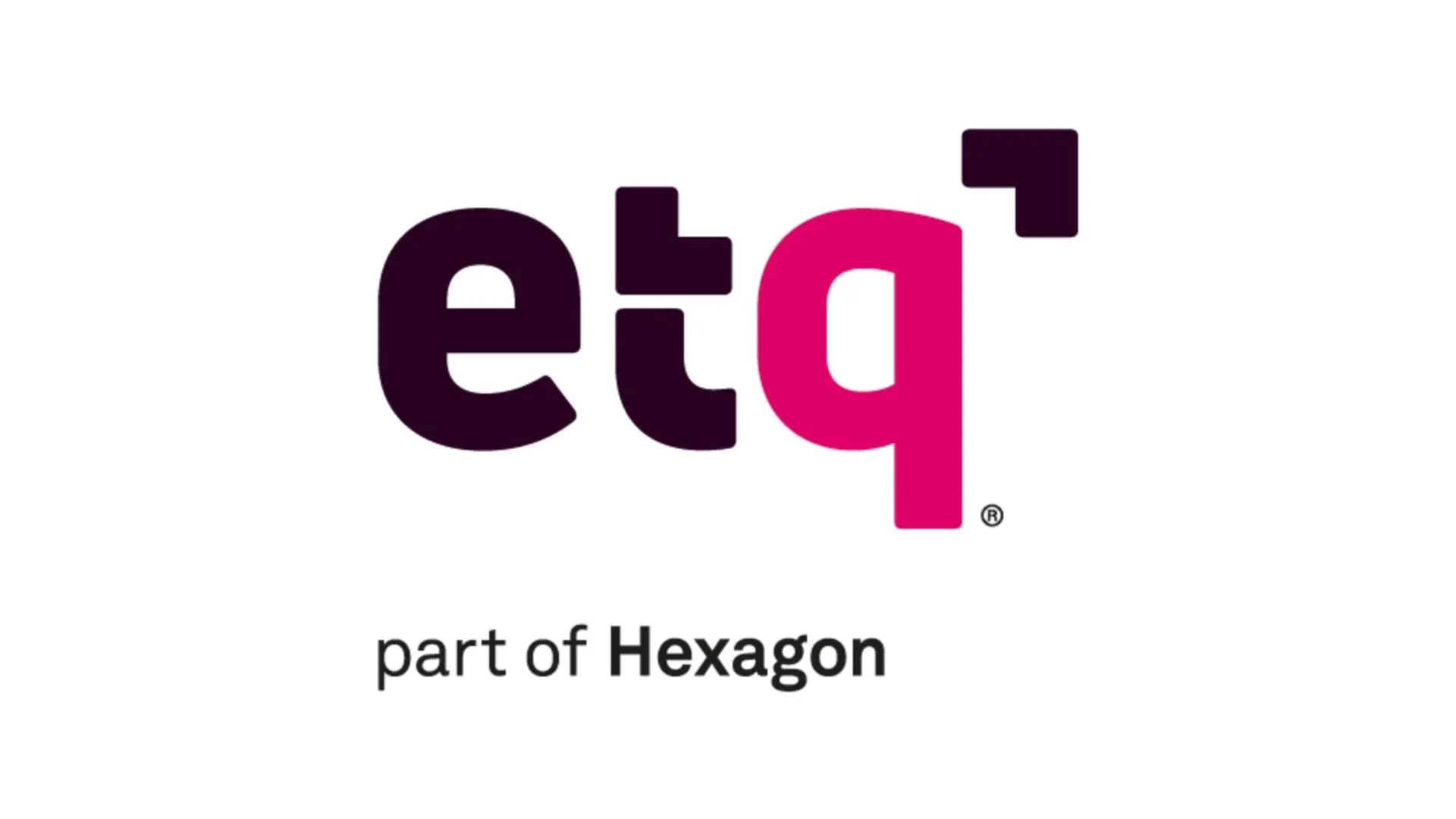
Hexagon's ETQ Reliance platform is a comprehensive management solution that companies can utilize to enhance operations, ensure compliance, and lower risk.
It is a useful tool for audit management because of its various aspects, which enable managers to assess the current situation and potential for improvement.
More than 40 pre-built applications are included with ETQ Reliance, a flexible workflow engine for managing business and quality operations. With this platform, you may design, test, and implement quality processes that are specific to your requirements.
Even non-IT professionals may confidently construct their own apps and alter pre-built Reliance applications using ETQ's drag-and-drop process design tool. ETQScript is a useful tool for automating complex business processes and logic.
Key Features
- Document Control: Establish a structure within the company for organizing and maintaining papers pertaining to safety guidelines, rules, and procedures.
- Corrective and Preventive Action (CAPA): Create a procedure for locating, resolving, and stopping reoccurring safety hazards by taking proactive and remedial action.
- Reporting and Analytics: To improve safety procedures and practices, use analytics and reporting tools to monitor safety performance, spot patterns, and make data-driven choices.
Pricing
- Contact Vendor
9. ComplianceQuest
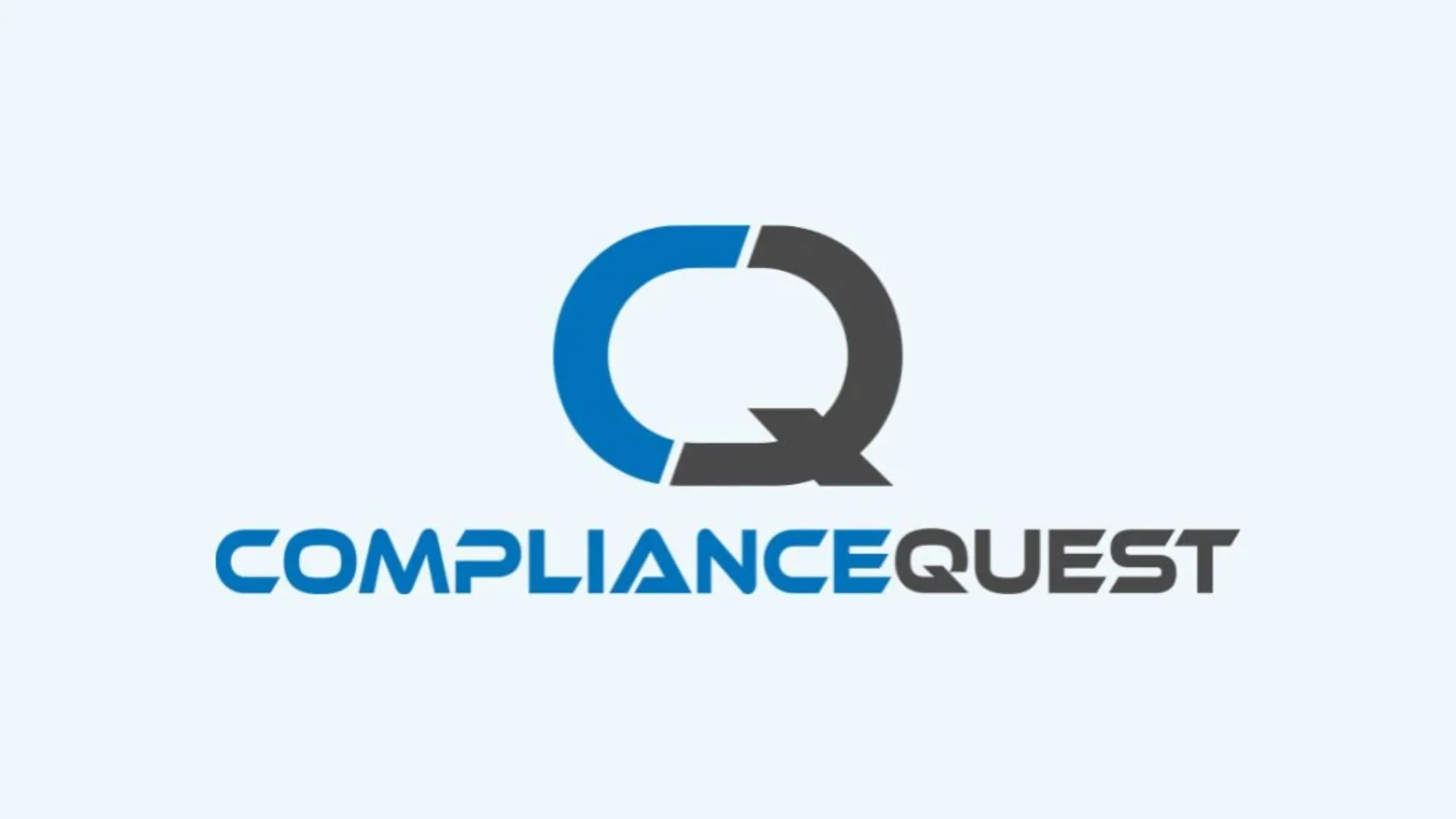
A well-known CAPA management tool, ComplianceQuest keeps an eye on all of your CAPA processes while guiding your business toward ongoing development.
Numerous industries, including supply chain, manufacturing, engineering, and healthcare, may make use of the tool. In addition to carrying out other crucial tasks, it makes use of AI to spot trends early on and arrange your action plans properly.
With its best-in-class integrated procedures, this intelligent data-driven platform protects your workers, suppliers, and brand reputation while boosting innovation, compliance, profit, and customer loyalty. ComplianceQuest facilitates efficient communication and cooperation across the product value chain since it is pre-validated and simple to use, manage, and apply.
Key Features
- Scalable Cloud Platform: ComplianceQuest's cutting-edge cloud technology allows you to securely and efficiently grow intricate supplier networks and supply chains.
- Advanced Dashboards: With ComplianceQuest's effective reporting, dashboarding, and querying engine, you may get insights that can be put to use.
- Accessibility: Enjoy complete access to reports, approvals, record views, reviews, alerts, and more with ComplianceQuest, accessible from any location, at any time, and on any device.
Pricing
- Contact Vendor
Which is the Best SafetyChain Alternative?
Two of the key drivers of modern manufacturing are safety and efficiency.
An advanced Safety Management Software system like SafetyChain’s SafetyChain puts companies in the best position to push their productivity to the highest level possible while remaining in line with OSHA standards.
However, organizations that focus on Operational Excellence and seek tailored safety processes should look for a SafetyChain alternative.
As a seamless combination of manufacturing business operations, safety compliance, and management maintenance, Xenia offers the most comprehensive alternative to SafetyChain.
It offers one of the most comprehensive, one-of-a-kind, and highly innovative approaches to enterprise safety management. Its user-friendly interface, collaboration, and its long list of features make it one of the leading enterprise safety solutions in the market today.
FAQs
Why is digitalization an important factor for safety processes?
By quickly addressing any safety threats and concerns that occur and taking remedial action to protect their employees' safety and security, site leaders may benefit from digitalization in ensuring a safe and secure work environment.
Why is digitalization important in the manufacturing industry?
Manufacturing processes going digitally bring in a new era of accuracy and efficiency. This transition offers businesses several benefits in addition to preventing costly errors and guaranteeing accurate work performance.
Access to clear, real-time operational data and analytics is one major benefit. Manufacturers are able to make data-driven choices quickly by using digital technologies, which provide them with previously unattainable process insight. Proactive problem-solving and optimization are made possible by this real-time information, which boosts output and reduces expenses.
Digitization also makes it easier to track and monitor each step of the production process. Digital systems provide thorough monitoring at every level, from the acquisition of raw materials to the delivery of products. This degree of observation improves quality control and allows for quick detection and fixing of any potential problems.
How is digital technology used in manufacturing?
The rollout of the Internet of Things (IoT) has brought about a revolution in the industrial sector by enabling smooth connection and communication between machines and physical objects. Manufacturers can collect real-time data on a variety of characteristics, including vibration, temperature, pressure, and more, by integrating sensors into their gear and products. This abundance of information allows for preventive maintenance, optimization, and quality control by offering priceless insights into the operation of machinery and processes.
Furthermore, a key component of the digital industrial revolution is artificial intelligence (AI) technology. Large volumes of data are gathered by IoT sensors, and AI algorithms examine this data to find trends, abnormalities, and areas for development. By minimizing downtime and increasing overall efficiency, these insights enable manufacturers to make data-driven choices, improve manufacturing processes, and even anticipate maintenance requirements before they arise.
What is an example of digital manufacturing?
Smart factory: Workers get real-time data regarding the tasks they are carrying out via the use of smart machinery and sensors. Information technology (IT) teams that work with back-end systems like SAP are connected to operations teams who keep an eye on the machines via this input.
.webp)
%201%20(1).webp)