Established business leaders know that documentation is the first step in workforce optimization.
There is not enough time for managers to oversee every process, and even if there was, it would be impossible to properly aggregate and analyze the information to make critical decisions.
Priced on per user or per location basis
Available on iOS, Android and Web
A Quality Management System (QMS) provides a solution to this problem. By standardizing procedures and tracking quality of work remotely, managers can compile data on their workforce and determine what's working, and what needs to be updated.
Unfortunately, as with any process involving people, it is not that easy. Managers who are new to QMS systems may learn the hard way that small details regarding implementation, ease of use, and aligning goals with staff can be the determining factor between success and failure.
To save you stress and provide direction, this article will start from the foundation and build up, demystifying Quality Management Systems and the human guidance needed to ensure success.
What is a Quality Management System (QMS)?
According to the international ISO 9001:2015 Standard,
"A QMS is a coordinated collection of principles and procedures that an organization has implemented to improve and show that it meets the requirements needed to fulfill the needs and desires of its clients."
In general, a quality management system (QMS) refers to the overall process of managing a company's quality.
It can include processes such as product design and development, manufacturing, delivery and installation, service, and more.
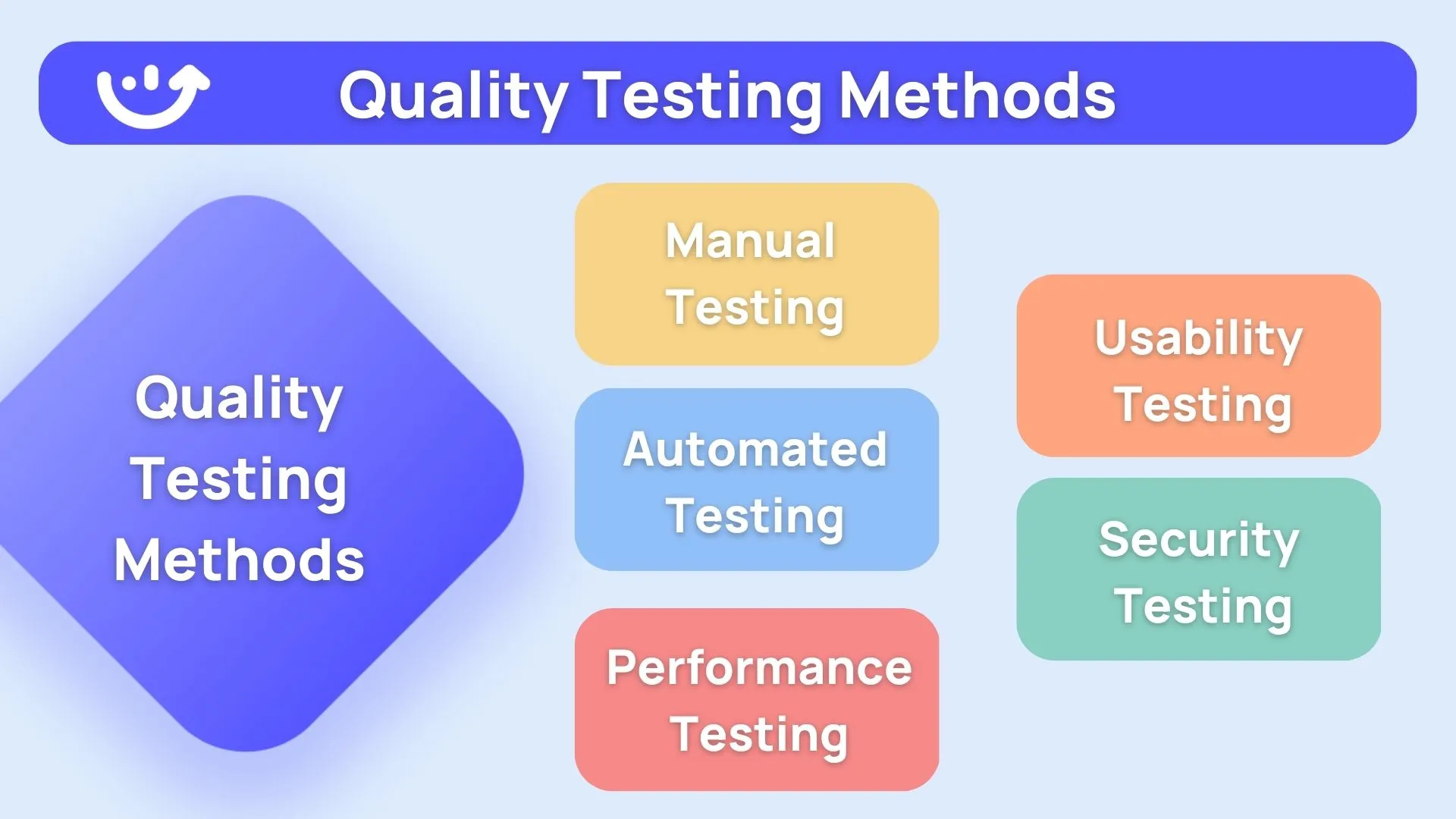
Quality management systems can be broken down into three main categories:
1) Reactive Management Systems
These are focused on responding to failures and fixing them after they happen. This is usually done by having a team of people who work together to eliminate or minimize defects in products or services by using data collection and analysis techniques.
In manufacturing, this would mean a quality control check following production and preceding distribution, with the goal of identifying defects and facilitating removal. In hospitality, a reactive QMS could be an inspection of a housekeepers work to see if it passes standard, or a protocol for fixing a computer system that crashes.
With a reactive quality management system teams don't necessarily identify or resolve the root cause of the problem, but rather add a layer of review and a process for correction before the issue affects the end consumer.
Also Read:
- 7 Best ISO 9001 QMS Software in 2024
- Quality Control Testing Guide For Service Industry Managers
- The Comprehensive Guide to Quality Inspection Software
- 5 Best Quality Control Checklist Apps For Businesses In 2024
2) Proactive Management Systems
This type of system seeks out problems before they become defects by implementing best practices across the entire organization from top down with the goal of improving performance over time through continuous improvement efforts. As a secondary goal, a proactive QMS can assist in minimizing waste at every stage of production or service process which helps reduce costs.
In hospitality, this would mean implementing standard operating procedures for room cleanings, preventive maintenance and guest interactions to ensure that brand standards are not disrupted by individuals. In manufacturing, this could mean protocols for testing equipment or temperature and humidity standards for production.
With proactive quality management systems, the key is to identify the root cause of a problem, and put in place a solution that prevents a disruption in the product or service.
3) Total Quality Management (TQM) Systems
A total quality management system (TQMS) is a set of practices and policies that are implemented by an organization to ensure the highest possible level of customer satisfaction. The aim of a TQMS is to reduce defects, increase efficiency, and establish a culture where employees are constantly striving for perfection.
This system combines effective proactive and reactive techniques to provide ultimate brand quality protections. In reality, not every problem's root cause can be identified and protected against. Sometimes, the systems are too complex and variable to provide complete proactive protection. Integrating a reactive protocol with a proactive QMS provides a dependable system that protects your brand image.
What is ISO 9001?
ISO 9001 is a quality management system standard. It's the most widely-recognized standard for business management and quality assurance, used by over 3.5 million organizations in over 180 countries worldwide.
ISO 9001 is a standard that helps organizations to establish a systematic approach to managing their quality processes, from design to delivery. It encourages companies to develop a culture of continuous improvement which will ultimately lead to increased customer satisfaction, higher employee morale and improved cash flow.
The purpose of ISO 9001 is to provide a common language for both internal and external customers, so that they can understand what they're getting from an organization—and what they can expect from it going forward. It also helps organizations identify areas where they could improve their processes or products such as service delivery times or product quality levels, so that they can deliver on their promises more effectively than ever before!
From a practical standpoint, ISO 9001 Standard sets general principals to follow that can be applied to any process. It is a great practice to either start with the ISO 9001 checklist and modify to suit a specific process, or to use an ISO 9001 checklist to identify gaps in existing processes. Take a look at the ISO 9001 checklist below to get a better feel:
11 Major Benefits of a Quality Management System?
One of the essential missions while a company is creating and implementing a quality management system, is that it should result in accomplishing many long-term financial goals of the company. Let's look at some other benefits of an effective system:
1. QMS reduces costly errors and keeps an eye out for other risks that can derail the company's operations
2. Standardization allows businesses to market their products more effectively by adding weight behind the claims of advertisement.
3. QMS provides concrete standards for onboarding and continuous training to cultivate productive teams.
4. QMS contribute to market share growth through clear communication and execution of value.
5. Standardization establishes a vision and culture to uphold that vision.
6. Quality systems create product consistency that spans time as well as differing employees and managers.
7. QMS improves levels of compliance with regulating bodies to minimize legal risk.
8. QMS are the bedrock of process optimization to ensure companies achieve organizational goals in the most efficient and effective manner.
9. Increased product consistency increases customer satisfaction levels, creating brand advocates that drive growth.
10. Concrete standards provide managers with a consistent rubric to evaluate employee performance and provide feedback to improve.
11. Total QMS helps to identify and correct root causes of problems to provide improvement recommendations and measurable interventions.
What Is The Importance of an Effective Quality Management System?
We saw the benefits a good QMS can provide companies, but what about its worldwide benefits to businesses all over?

Let's look at some advantages of deploying a solution in your company's eco-system.
- QMS establishes and upholds trust between the end customer and brand which leads to brand advocates and growth.
- Worldwide adoption of standards provides ubiquitous reliability of purchase that underlies consumer confidence in markets in general.
- Unification of standards and goals, allows companies to work together to solve larger problems like climate change and social injustice.
- Better work standards increase worker safety, contributing to a happier population.
- Innovation in quality bleeds across companies to improve society as a whole (Toyota and Ford are an excellent example of this).
- These systems also give businesses the ability to develop services that better suit the new market trends and requirements.
Which Types of Industries Use Quality Management Systems?
When it comes to ISO standards, there are certain industries where compliance is mandatory. Industries where a depletion of quality can lead to death, illness and depletion of consumer confidence have unique ISO guidelines to uphold. Here are some of those industries and their identification codes:
- Medical device manufacturing (ISO:13485)
- Circuit board manufacturing (ISO:9001)
- Aerospace and defense manufacturing (AS9100 revC, AS9100 revD)
- Automotive Manufacturing (TS-16949)
- Nuclear power (Nuclear Regulatory Commission standards)
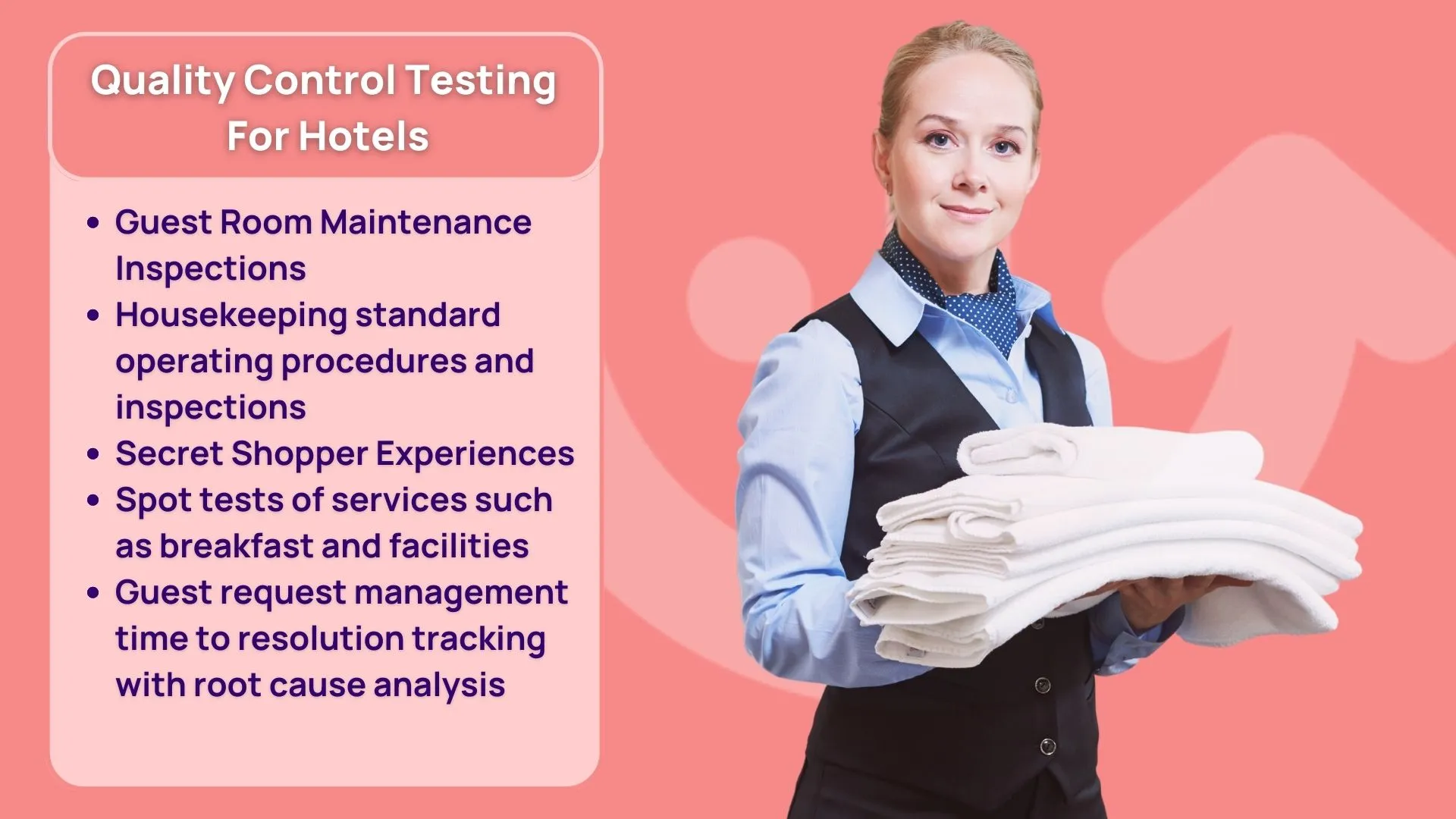
Quality Management Systems extend far beyond manufacturing and ISO standards. Here are a few industries that leverage Q.M.S:
- Hospitality
- Construction
- Restaurants
- Retail
- Hospitals
- Senior living
Different industries may require varying levels of data collection and oversight, however providing a consistent and high quality product or service is the goal of any corporation.
Setting Up a QMS For The First Time? Here's What You Need To Know...
Let's look at all the steps you can use to create an effective quality management system for your company.
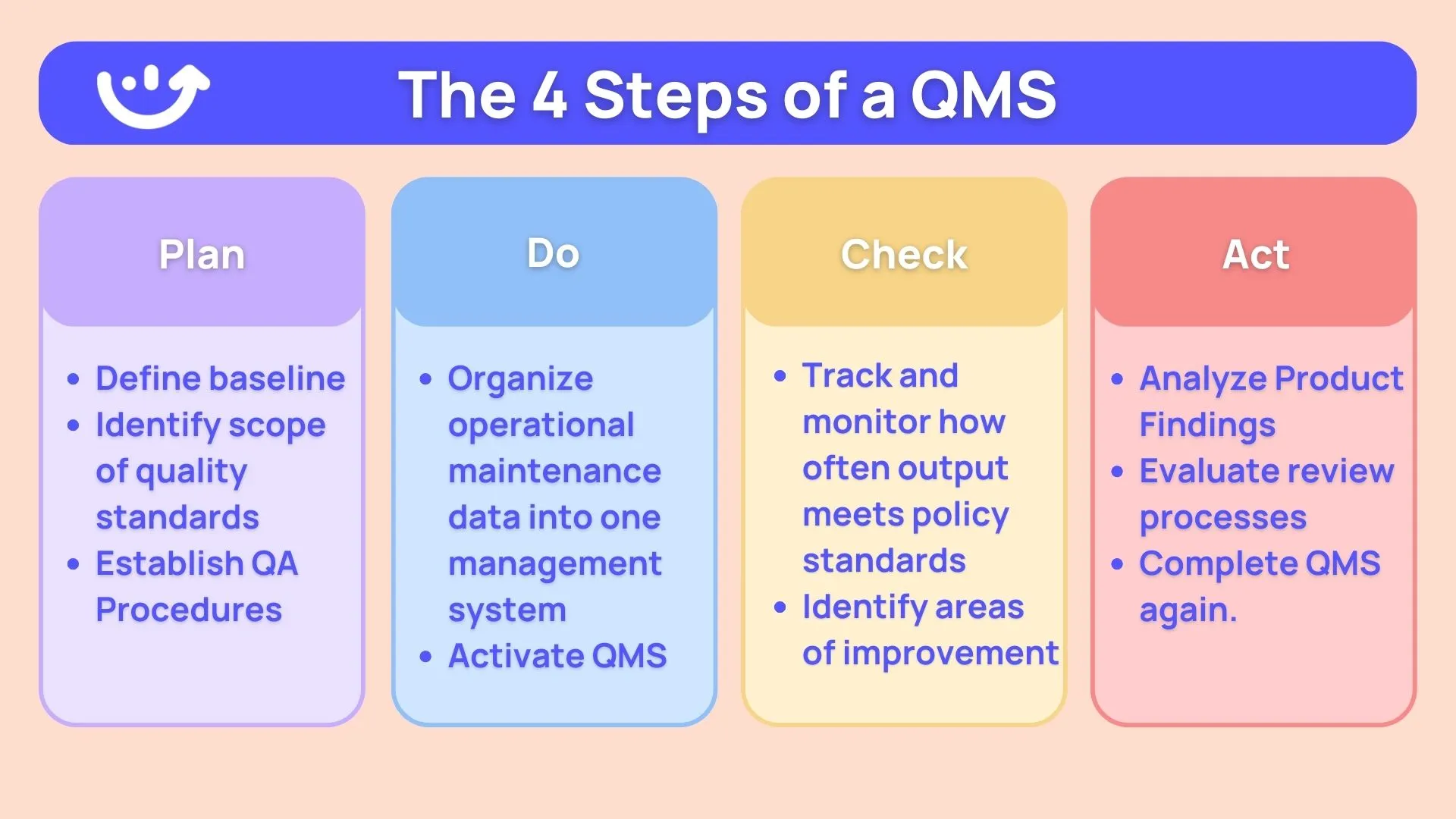
1. Solidify a Core Value Proposition and Goals to Uphold it
The first step in quality management is to understand your "why". A core value proposition defines why your company exists to both internal and external stakeholders. To uphold a core value proposition, a business needs to set goals lead to the realization of value. These goals should be "SMART" meaning Specific, Measurable, Attainable, Relevant and Time Based. This is the foundation of quality management, as all operating procedures must align with goals in order to deliver the core value to customers.
2. Define and Communicate the Contribution Structure
Once goals are understood, management must define and map out the processes to be followed to achieve the set goals. Using a free diagram and flow charting tool such as LucidChart can help a company to visualize its functions effectively and communicate clearly to all stake holders. This helps to break down a complex system into manageable pieces that can be improved upon, ensuring that everyone agrees on their role, and sees how their contribution leads to the larger picture of success.
When charting, think through the order of events, key indicators of success of each step and individuals or teams responsible for execution and oversight. The RACI structure is great for this step in the process as it clearly defines each parties accountability in the process. RACI stands for Responsible, Accountable, Consulted, and Informed. This is helpful for communication of responsibility and identification of bottlenecks in a process.
3. Establish Baseline Objectives and Processes
Once your process is mapped, more specific key performance indicators (KPIs) are defined to establish the standards that will lead to success. Whereas step one was the "why", step two was the "what", step three is the "how". How is quality achieved on a consistent basis? What interventions are necessary to drive success?
For many teams, this means establishing standard operating procedures and tracking mechanisms to ensure proper processes are followed every time. This may also mean adding teams to do an extra quality review where necessary or buying sensors to achieve a similar goal. The goal of this step is to zoom into each step in the process and think critically about what tools are needed to ensure success, and how can success be measured accurately.
4. Generate and Incentivize Frontline Buy-In
In the end, the front line worker is the bedrock of quality assurance. Without their buy-in, the system will fail or run at a suboptimal level. This is why an important step in setting up your QMS is to incentivize compliance amongst your staff. This is essential and can be the most difficult part in cultivating a successful quality program. To help increase likelihood of success, we recommend to:
- identify a quality "champion" who can enforce standards when management is out of view.
- create incentives for identifying and correcting bottlenecks in a process.
- communicate with employees by connecting their work to the bigger picture.
It should not be underestimated how important this is to get done early in the relationship, as establishing a disciplined culture is easier than reforming an disorganized one.
4. Collect Data and Refine Key Metrics
As you kick off your QMS, it is important to be open to change. No one gets this right the first time, so the mindset should always be focused on continuous growth and improvement. To remove the negative effects of ego and misaligned incentives, a QMS system must collect accurate, unbiased data to be used to compare teams and processes. Use the first few months to establish a baseline, then identify over and under-performers to determine the root cause of success or failure. Use this information to test new success metrics with your teams and empower peer learning.
5. Record All Defects in Product and Process
Defects in any process or procedure are non-conformances that can easily happen as a product or service flaw or a completely different process deficiency. It would help if you ensured that it is tracked, measured, and corrected whenever a defect or an error occurs. This helps management to identify trends and underlying root causes that lead to defects. This data is crucial as it is the basis for strategic incremental intervention to drive optimization.
When recording defects, it is helpful to also categorize them based on severity and scope. In addition, you should record any other processes that could be indirectly contributing to or affected by this defect. This is important for cases where the prescribed intervention does not solve the underlying issue, as you will need to prepare next steps to try and resolve the defect.
6. Iterate, Test and Measure Improvement
Now comes the time to leverage your QMS to enact change in your organization. Using the data covered in previous steps, management can identify areas for intervention and create systems to empower change. When changing processes, it is important to communicate with all stakeholders:
- the underlying inefficiency or defect that led to the change.
- the new process in full detail, along with how it differs from the original.
- the importance and urgency needed in the revision.
- the consequences of non-compliance with the new policy.
Use Xenia to Define Standards, Communicate and Uphold Quality Management
Xenia provides the tools to improve quality management with a software platform designed to integrate facility management and frontline operations. With Xenia, you can:
- create standard procedures for every team and process
- assign tasks equipped with accountability tools such as checklists and logs
- attach images and notes to clarify communication of issues
- segment tasks by priority level, team responsible and due date
- track task progress, time to completion, and inspection scores
- organize reports your way, exporting to PDF or CSV
- streamline communication with in-task chat for teamwork and accountability
Xenia's app is designed specifically for frontline worker productivity with an intuitive interface that teams can learn in less than one day. Check out how easy it is to create checklists and assign work on desktop and mobile:
At The End of The Day...
This was our guide to understanding and creating a quality management system for your company's needs and requirements. We hope you learned a lot. If you are interested in Xenia, click here to start your free trial. If you're not ready to commit, check out our free resource library linked below for free checklists and excel tools designed to improve operations, maintenance and quality.
.webp)
%201%20(1).webp)