Quality control is an important part of every organization that wants to provide superior products or services to its potential customers.
We can all agree that quality can make or break a brand's reputation. When was the last time you bought something, and poor quality didn't bother you? That’s right—probably never. This underscores the increasing need for proper quality maintenance more than ever.
Quality manufacturing inspection software is essential for ensuring the quality of your goods and services. Unfortunately, many organizations believe that quality checking is only necessary throughout the manufacturing process.
However, quality inspection is an essential component of the whole product life cycle, from design and development to production and distribution. Not only that, but the quality applies to many industries and operations, not simply those in manufacturing.
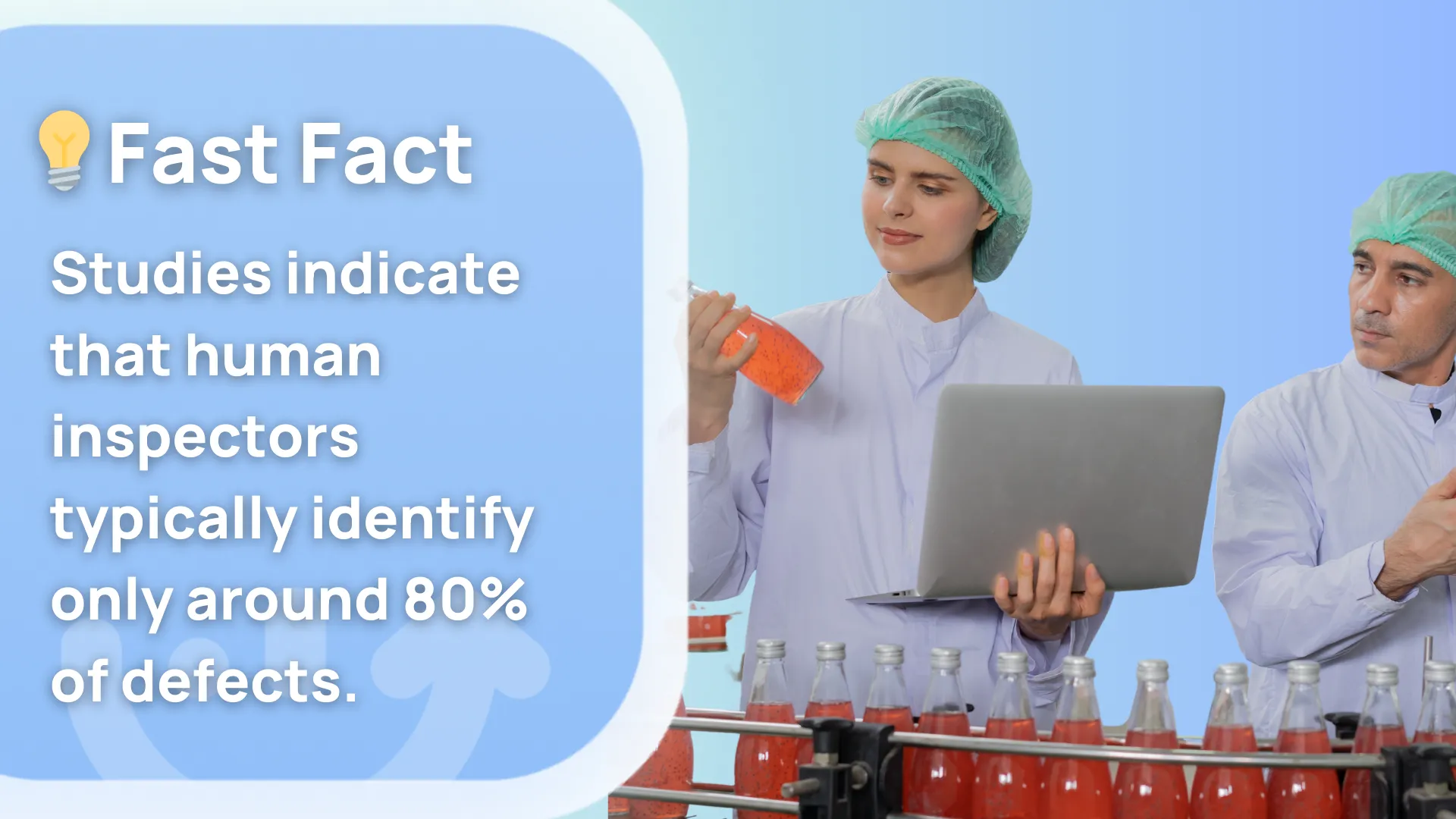
As industries expand and become more competitive, the necessity for effective Inspection Management Software grows.
What is Quality Inspection?
Quality inspection is the process of determining if a product or service satisfies quality requirements. Quality standards can be established by the business, the customer, or an industry association. Quality inspection is often performed at different phases of the product life cycle, from raw materials to final goods.
Quality Inspection vs. Quality Control. What’s The Difference?
Quality inspection is the process of inspecting items after they have been manufactured. It has no direct impact on how things are produced. To ensure that no subpar goods leave the production, a quality inspector inspects the goods.
Since quality inspection lacks a feedback loop, managers and employees are not informed about failures and their reasons. Consequently, this system is unable to advance on its own.
In a quality control system, inspectors and QC Inspection Software work hand in hand to check and fix any issues with the product's quality. In addition to identifying the source of issues, product quality inspection results allow for the differentiation of good products from poor ones.
Incorporating QC Inspection Software that doubles as ISO 9001 software can further streamline and optimize these quality control processes, ensuring adherence to international quality management standards.
Results are communicated to both management and workers to enhance the process. Since quality control is a feedback loop system, employees attempt to improve their jobs without altering the system or the final product when they get information.
Types of Quality Inspections
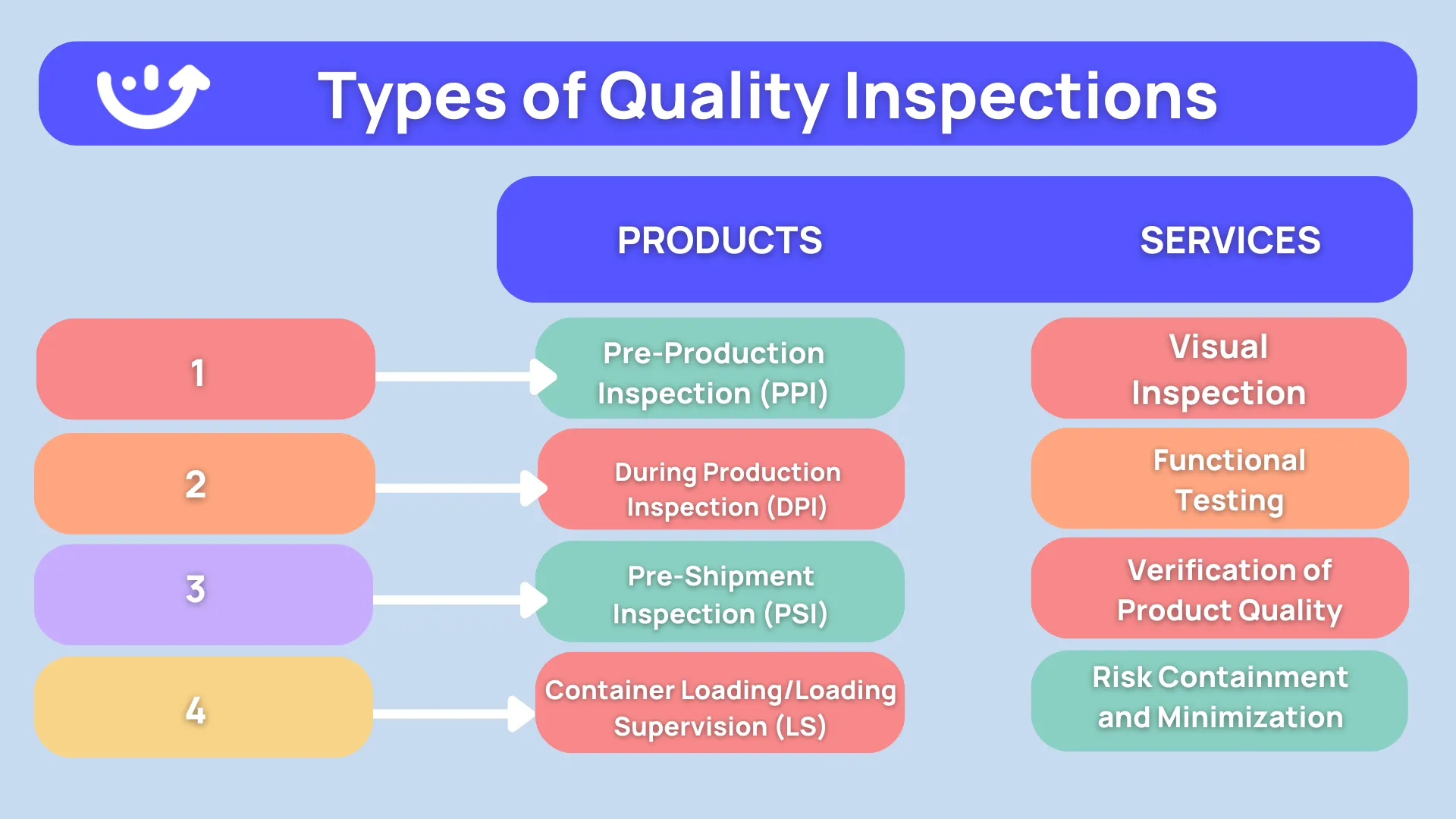
Pre-production, during-production, pre-shipment, and container loading/unloading inspections are the four categories of inspection that makeup quality control in the case of products.
As their names suggest, each quality control technique is used at a distinct level and serves a specific function in supply chain management and quality control.
One or more of these procedures can apply to your company's requirements, depending on the product, your supplier's track record, and other factors.
Pre-Production Inspection (PPI)
Before the start of the manufacturing process, the Pre-manufacturing Inspection (PPI) is carried out to evaluate the amount and quality of the components and raw materials and to determine if they meet the applicable product quality inspection criteria.
When working with a new supplier, particularly for a major contract with important delivery deadlines, a PPI might be helpful. Your and your supplier's communication on production schedules, delivery schedules, and quality standards may be reduced or eliminated as a result of this inspection.
During Production Inspection (DPI)
A quality control inspection that is carried out while production is in progress is called DUPRO or during production inspection (DPI).
This stage is very helpful for products with tight specifications that are manufactured continuously, as well as when quality problems were discovered during a previous PPI and the product was not manufactured.
When just 10% to 15% of the units are finished, DPI inspections are conducted to find any deviations, provide comments, and recheck any flaws to ensure they have been fixed. It allows you to verify that standards are being met and quality is being maintained throughout the manufacturing process.
Furthermore, it offers early identification of any problems that need to be fixed, which cuts down on delays and rework.
Pre-Shipment Inspection (PSI)
Pre-shipment inspections, or PSIs, are a crucial part of the quality control procedure and a way to verify the products' quality before shipping. PSI makes sure that the production meets the buyer's standards.
When at least 80% of the order has been packaged for transportation, completed items are subjected to this inspection procedure. Selected at random, the samples are examined for flaws by the applicable protocols and standards.
Container Loading/Loading Supervision (LS)
Inspections of the loading and unloading of containers guarantee that your items are loaded and unloaded properly. To ensure your items arrive safely at their destination, inspectors will oversee the whole process and make sure they are treated properly.
Typically, this inspection happens at the factory of your choice during the process of loading the cargo into the shipping container and at the destination after the items have been delivered and are being unpacked.
During this procedure, the shipping container's condition will be assessed, and all product details, amounts, and packaging conformity will be confirmed.
In the case of service inspections, there are two types of processes.
Visual Inspection
When inspecting a service for physical flaws, inspectors conduct visual inspections. This task can be facilitated by equipment inspection software or done manually. Concurrently, functional testing evaluates the service's efficiency based on established standards. Common practice involves using automated test equipment for this quality assessment.
Functional Testing
However, functional testing determines whether a service can carry out its intended functions. Electronics and items with moving components are common candidates for this quality check. In functional testing, quality inspectors put procedures through a series of scenarios designed to mimic real-world use.
Why Do You Need Inspection Management Software?
.webp)
While humans continue to bear the responsibility of inspection, it is widely acknowledged that the quality inspection tasks performed by humans are prone to errors. Studies indicate that human inspectors typically identify only around 80% of defects.
Software for quality inspection is a kind of digital technology used in organizations to help automate and streamline different inspection procedures. It enables companies to produce accurate inspection reports collaboratively, detect flaws, gather and evaluate data, and comply with industry requirements.
Businesses can ensure the dependability, accuracy, and consistency of their goods and services by using this software and inspection forms.
A complete solution for overseeing the whole inspection process is offered by quality inspection software. It has capabilities including real-time data collection, configurable inspection checklists, and activities and procedures for inspectors that are automated.
Organizations can improve overall efficiency, minimize human mistakes, and simplify their inspection methods with the help of this software.
Facilitating compliance with diverse quality control standards and laws is a fundamental role of quality inspection software for enterprises. It offers businesses a centralized platform on which to specify and implement their quality control procedures.
Moreover, companies can identify flaws, non-conformities, and faulty items early on thanks to quality inspection software. It offers instruments for recording and preserving inspection findings, such as photos, measurements, and notes. Analyzing this data will reveal trends, patterns, and areas in need of improvement and remediation.
Key Features of Quality Inspection Software
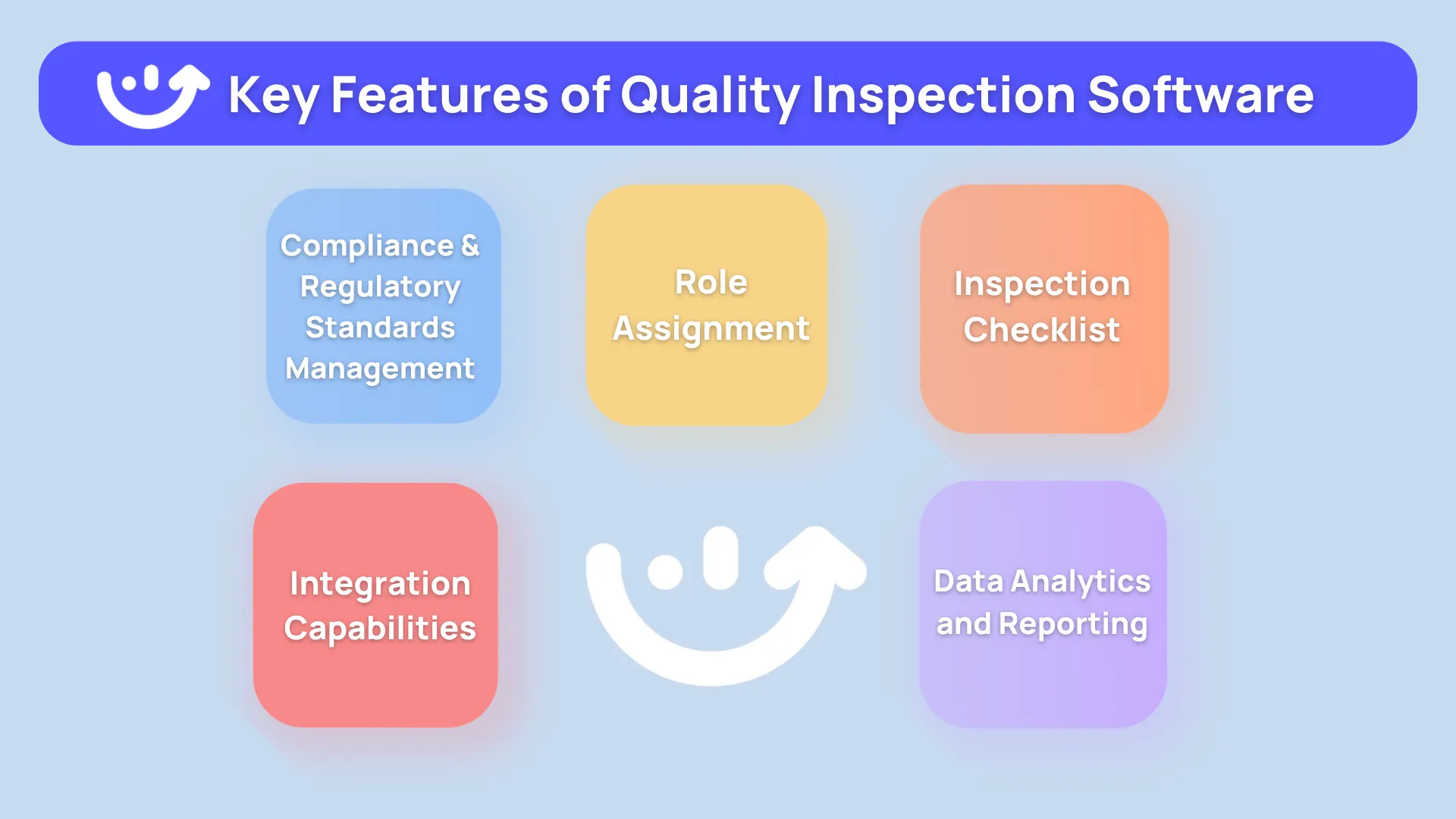
Compliance and Regulatory Standards Management
Businesses must abide by industry norms and rules to stay reputable and retain their credibility. By offering integrated compliance capabilities, quality inspection software enables businesses to comply with these regulations. With the use of these technologies, organizations can demonstrate regulatory compliance during audits and inspections and verify that inspections are carried out in line with certain requirements.
Furthermore, the manufacturing inspection software streamlines the team's productivity and compliance management process by managing paperwork, including audit trails, visual inspections of test records, and certifications.
Role Assignment
Without a clear schedule outlining how long each inspection should take and which employees are responsible for which areas, the process could become chaotic.
You can easily plan things out and let the right individuals know when their time comes with the help of software. To further improve productivity and decrease downtime, approval operations are also automated.
Inspection Checklist
Everything from physical requirement verification to correct packing and labeling to functional testing and carton drop tests is included in the comprehensive inspection checklist.
Regular inspections of equipment and safety procedures can foster a sense of confidence in workers and keep them actively involved in their job. This is why inspection checklists are so useful in the workplace.
To a large extent, using checklists can prevent endless inspections. Methods for examining work areas, tools, and duties are laid forth in detail. The inspector will use your checklist to complete the inspection and then write up a report detailing their findings.
Integration Capabilities
Integrating quality and inspection data and software with other systems in a business could significantly improve efficiency and effectiveness.
The elimination of redundant data input and the facilitation of smooth data sharing between departments are both made possible by this. To better understand production processes and keep tabs on errors, for instance, the program can link with MES.
Data Analytics and Reporting
Numerical analysis has long been manufacturing inspection software's forte. After an inspection is over, automation can almost quickly generate and distribute results, allowing strategic teams to do analytics and make well-informed decisions as soon as possible.
What Are the Use Cases of Inspection Software?
Here is a general overview of some typical example uses.
Inspections
The focus on audits and inspections is due to the nature of the software, which is an organization's attempt to make sure that its policies are being followed and that internal processes are producing consistent outcomes.
Reporting capabilities also provide information about how your company is doing in that area and could recommend adjustments you can make to make improvements.
Procedures
Integrating with the inspection process, quality management software provides step-by-step guidance to assist staff complete complex processes.
Employees gain self-assurance when they have a clear picture of the process for all of their responsibilities, including but not limited to paperwork, report filing, and inspections.
Field Service Management
It is sometimes required to dispatch inspectors to outlying areas to carry out their duties, given that the majority of enterprises operate in more than one geographical location.
Thanks to Field Inspection Software, it is much simpler to get all that inspection data back to the primary quality control department.
How much Does Quality Inspection Software Cost for your Business?
Estimating the cost of Quality Inspection Software for your corporation can be done utilizing a software as a service (SAAS) licensing model. In this setting, the expected price will generally be in the range of fifty to eighty USD per month per inspector.
A cost/benefit analysis demonstrates the economic benefits of such an investment contrasted with the complete costs of an inspector. When management time and other related expenses are added in, the total exceeds the substantial sum of $1,500 per month per inspector.
Assigning specific QC inspection software software to inspectors does not just make their job smoother but saves a lot. The price tag on the purpose-built software, which assists with things such as paperwork and saves about one hour each day, is only a nickel on inspectors’ total overhead.
This smart investment not only ensures that the office is running efficiently but also provides a wise moot of saving; it makes a good return on investment by taking full advantage of resources while decreasing overhead.
How to Successfully Deploy Quality Inspection Software?
- Begin by creating the core elements, such as your company's logo and a few test users.
- Set up the initial setup parameters for the product Quality Inspection.
- Customize data such as product descriptions, checkpoints, and faults, adapting settings to your company's specific needs and goals.
- Run initial tests in the office or on the production floor.
- Adjust and check the program setup depending on actual usage.
- Import necessary base data, such as supplier and product information.
- Explore integration options with your Enterprise Resource Planning (ERP) system to facilitate data transmission.
- Deploy a small team (1-3 inspectors) to conduct inspections using the mobile application over a few weeks.
- Fine-tune the Quality inspection software based on their input and test its efficacy.
- Continuously fine-tune the setup to enhance the user experience.
- Ensure that inspectors can access essential information with a few clicks.
- With the best quality inspection software, Schedule training seminars for all inspectors.
- Switch all inspectors to the mobile app for a thorough and consistent adoption.
Benefits of Conducting Quality Inspection
Nowadays, moving your business online is the way to go, and even a corporate strategist can see this.
The management of rule-based processes and data-driven activities are best accomplished using software tools and automation. Therefore, it should come as no surprise that software and inspection methods work together.
We might simply state that QA teams get a greater return on investment (ROI) from using inspection software since it saves them time and money. 24% of companies saw an instant increase in ROI once they started automated testing.
Team Accountability
Mobile inspection software is often used by quality assurance teams to plan workflow and assign duties. The timetable for deliverables and which team members are responsible for various inspections and audits are displayed.
By detailing who was in charge of what processes, the inspection management software assists in promoting accountability if the inspection process is incomplete.
Cutting Down on Manual Tasks
Some of the work will need human workers, however, there is always the risk of human mistakes when dealing with manual tasks like data input.
In addition to reducing the burden of quality assurance, automation speeds up the process.
Enhancing efficiency and visibility for corrective actions, automated features such as built-in photo taking, collaborative corrective actions, and the ability to give much-needed context reduce the most laborious elements of the inspection process.
If you can find ways to free up your employees from mundane, repetitive duties, you could motivate them to focus on the more engaging and creative aspects of their work. All of this is necessary groundwork for establishing a quality culture in your company.
Instantaneous Updates
If you choose to alter the inspection schedule, you won't have to maintain a mountain of unrelated paperwork or notify everyone via mass email. The inspection management software allows you to quickly update all parties involved, reducing the likelihood of miscommunication and successfully standardizing your business's quality assurance operations.
The result is a more unified experience across all of your locations, which in turn guarantees that your customers will have a consistent experience once they get their orders. The quality of your product will remain constant regardless of the manufacturing site.
Lastly, as the changes are made in real time, the remedial actions can be executed almost immediately after the request is made. With the correct quality inspection software, making well-informed judgments doesn't have to take forever.
Inexpensive Implementation
Digitizing the inspection process could seem like it would cost a pretty penny, but that's not the case. Accessible via a wide range of devices, including smartphones, tablets, and laptops, mobile inspection software is available from contemporary manufacturers at a reasonable price.
With this degree of accessibility, the examination procedure is open to nearly everyone; a piece of high-end, costly equipment is not necessary.
Facilitating Analysis
Collecting inspection data is pointless if you don't leverage the insights contained inside those figures. To make the production line better, inspectors need to be able to see patterns and draw conclusions from the data.
These patterns in the data can be more easily seen and problems can be more quickly resolved using software-driven inspection methods. Having better insight into what's happening on the production floor is one of the main advantages of inspection software for the QI department.
Even supplier relationship management can be analyzed via QI. If a company notices that specific suppliers are having an abnormally high failure rate for either their raw materials or their services, they can evaluate their vendor agreements appropriately.
Data Storage and Security
It is important to safeguard the data collected during inspections since it contains significant company information. While it may be difficult to keep track of a mountain of paper, digitizing all of your paperwork and photos makes them easily accessible and secure.
In case of data loss, you can usually recover an older backup thanks to the cloud storage offered by most inspection management software suppliers.
Tips for a Successful Quality Control Inspection
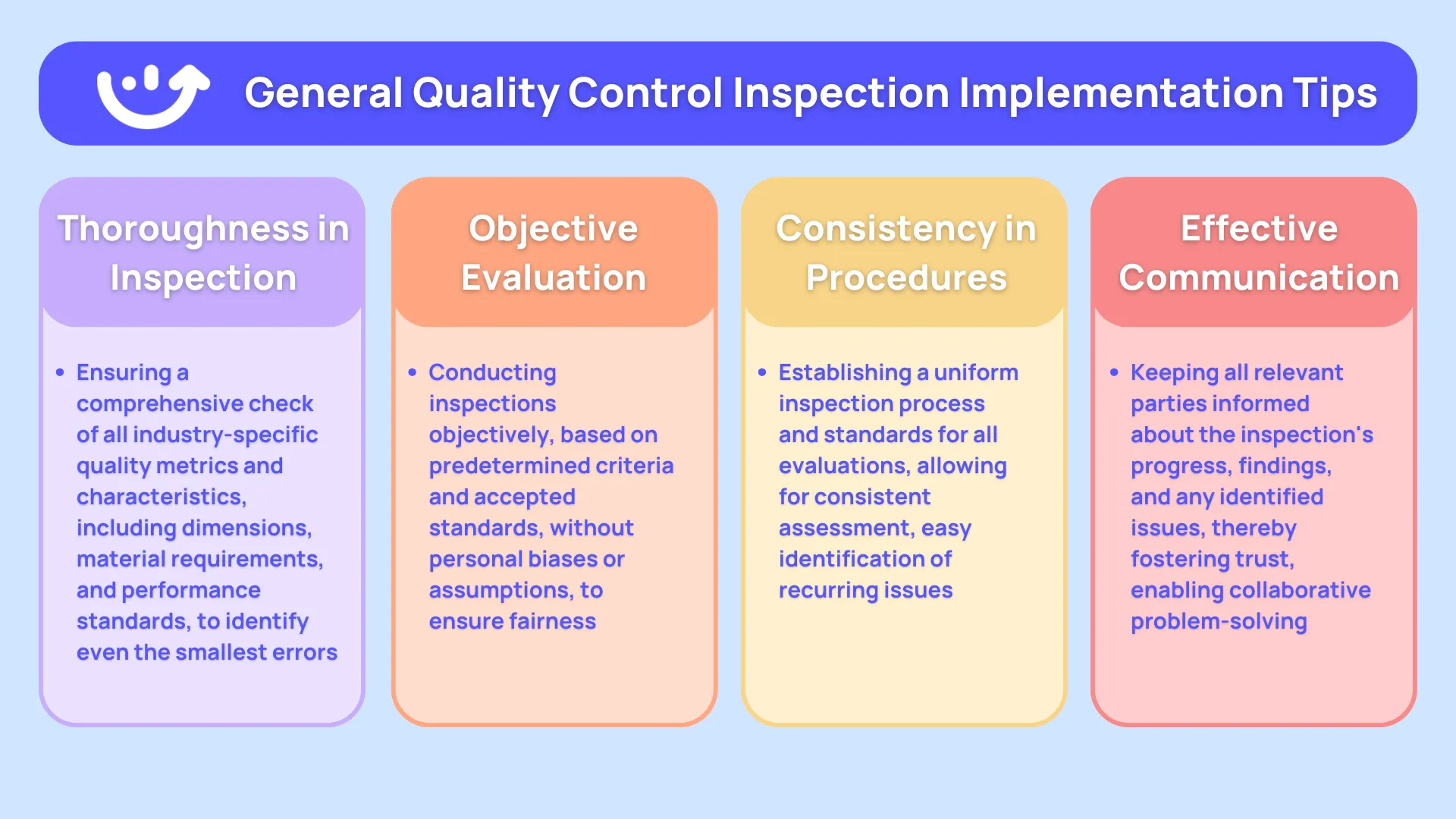
The following are some tried-and-true methods for conducting a quality control examination of your production process:
1. Thoroughness
Being careful and comprehensive is key when doing a quality inspection check. Verify that all industry-specific quality metrics and characteristics are included in the inspection.
Everything crucial to the quality of your goods or services, such as dimensions, material requirements, performance standards, and so on, falls under this category. If you check everything thoroughly, you can find the smallest mistakes and guarantee top-notch quality.
2. Objectivity
To keep the quality inspection process honest and reliable, objective inspections are essential. It is essential to conduct inspections objectively, free from any biases or assumptions that might skew the findings.
Only predetermined criteria, accepted standards in the field, and written requirements should be considered by the inspectors using Field Inspection Software. This guarantees uniformity and equity, which in turn permits precise evaluations and the objective detection of any non-conformities.
3. Consistency
Quality control checks must be conducted consistently. Create a uniform inspection procedure and set of standards that are used for all inspections. This eliminates evaluation variances by making sure all products or services are appraised using the same criteria.
Staying consistent allows you to easily monitor patterns, see problems that keep popping up, and fix them as needed. Establishing a dependable foundation for quality control is as simple as keeping your inspection techniques consistent.
4. Effective Communication
Effective quality control inspections rely heavily on communication. Important parties must be kept apprised of the inspection's development, results, and any problems or flaws found at all times.
Making ensuring everyone is informed of the inspection results in a timely and open manner develops confidence.
Furthermore, if any non-conformities are identified, it enables collaborative problem-solving and quick decision-making. Make sure the inspection findings are easily integrated into your entire quality management system by communicating them effectively.
5. Utilize Technology
60% of businesses predict keeping up with rapidly advancing technology will be their top challenge.
Your quality control inspection process can be made much more efficient and accurate by embracing technology.
Make use of inspection management software, hardware, and specialized equipment developed specifically for your sector. Automated data gathering, real-time monitoring of vital parameters, and exact measurements are all made possible by this technology.
You can enhance the overall dependability of your quality control efforts, expedite the inspection process, and decrease human error with the use of modern inspection technologies.
8 Best Quality Inspection Software That You Need To Try Right Now!
For better understanding of how quality inspection software bode against your business requirements, here's a quick look at some of the hottest picks of the day.
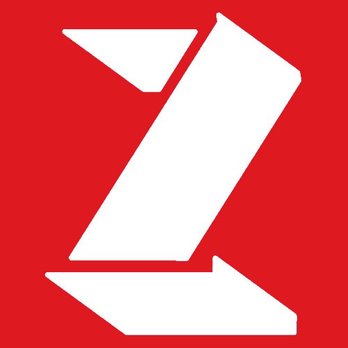
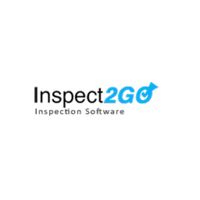
1. Xenia - Overall Best In Line Quality Inspection Software
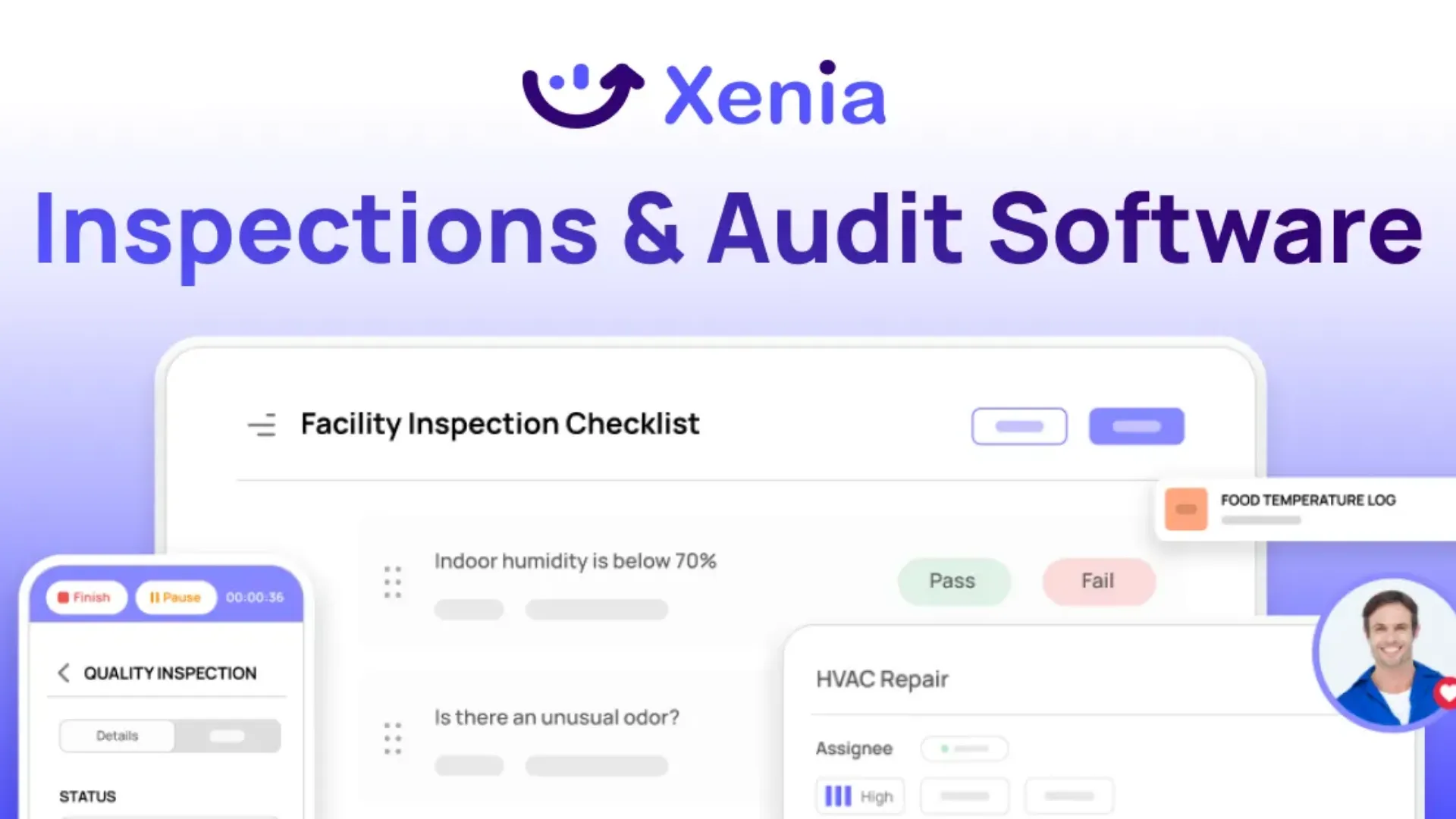
Xenia is the best quality inspection platform that provides the right tools to help take your organization's quality up a notch. It does so by allowing you to effortlessly perform quality inspections and monitor quality data.
This procedure will be streamlined using our mobile inspection app, eliminating the need for paperwork and expensive administration. With is a robust workflow automation plan that allows you to design extensive workflows, checklists, and other important tools for quality inspection procedures. The inspection management software also allows you to gather real-time quality data and monitor quality trends over time.
Its simple drag-and-drop interface makes it simpler to create and deploy quality inspection procedures than ever before. So, why not test out our quality management platform today?
Schedule a free demo now to see how Xenia can help you increase the quality of your business.
Key Features
- Operations Template Builder: With adaptable pre-built templates and an advanced builder, you may speed up manufacturing work processes and inspections.
- Smart inspections: Detect issues with production, streamline product quality inspections, automate remedial actions, follow-up queries, and upload photographs to the cloud.
- Work-Order Management: Using graphics, notes, and templates for task management can improve standardization and accountability compared to taking notes.
- Scheduled Inspection Tasks: Xenia, the best QC inspection software, improves efficiency by defining clear task plans and providing mobile team updates.
- Requests and approvals: Centralize request management, accelerate approvals, and maintain track of associated expenditures and resources.
- Incident Reports: Improve problem management with mobile reporting, corrective actions, and live progress tracking.
- Analytics and Reporting: Boost decision-making with extensive work analytics, robust filters, and customizable data exports
Pricing
- Free Forever
- Starter -$99
- Premium -$199
- Need a Customized Pricing?
Schedule a free demo now to see how Xenia can help you increase the quality of your business.
Priced on per user or per location basis
Available on iOS, Android and Web
2. Zontec
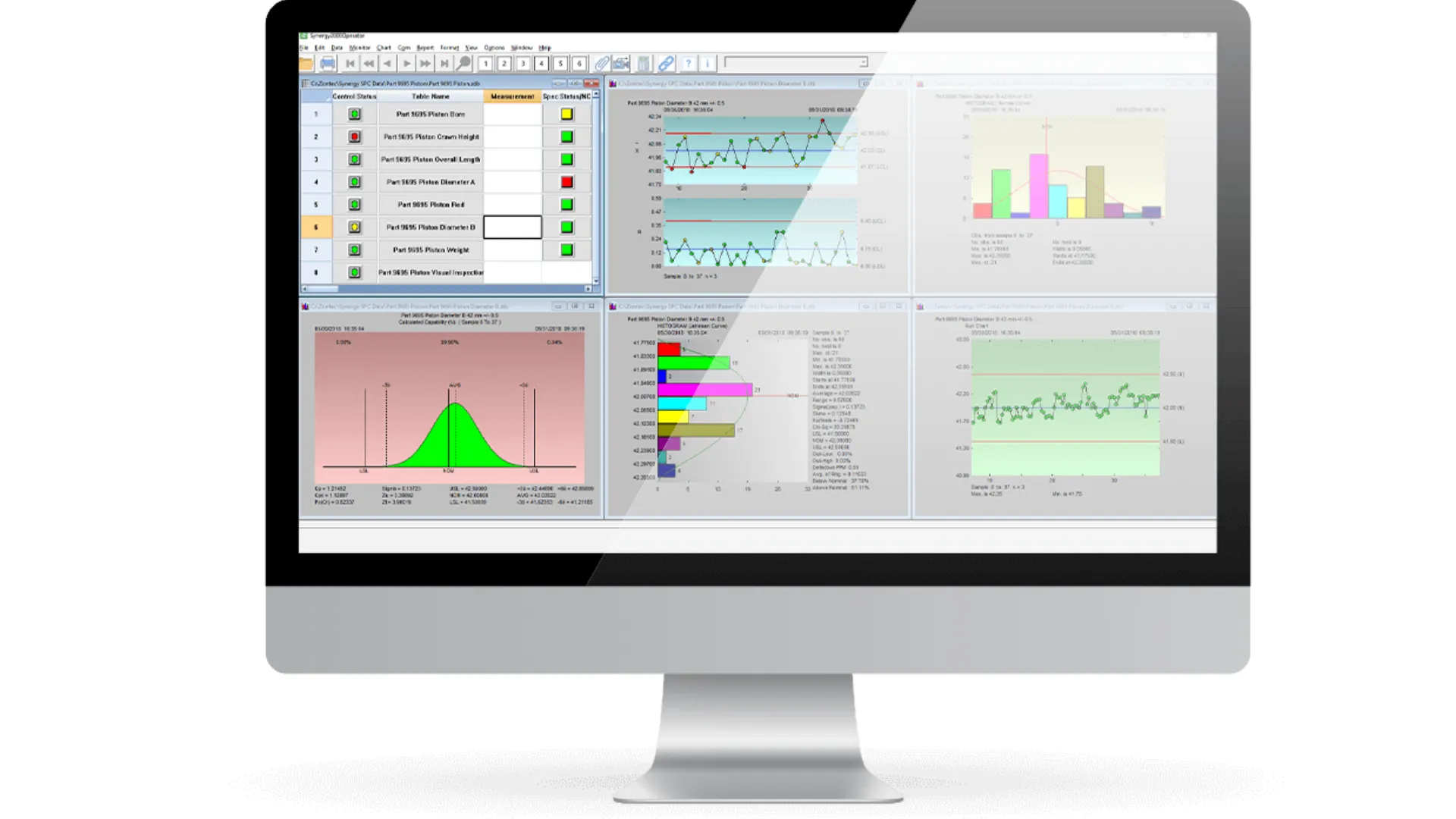
Zontec is a cloud-based software created to redefine quality control inspections through a high level of sophisticated statistical process control(SPC).
Offering real-time monitoring and analysis functions, Zontec empowers manufacturers to maintain and improve the quality of their production.
Zontec's customizability is one of their key assets as it can be easily modified to fit your unique quality control requirements. With this kind of flexibility, manufacturers can customize the software to fit their unique product quality inspection requirements.
Key Features
- Streamlines the data collecting and analysis process by automating key steps to increase productivity.
- Real-time tracking tools enable businesses to keep informed as the production process progresses.
- Promotes root cause analysis, allowing producers to discover and resolve underlying quality concerns.
Pricing
- Contact Vendor
3. Inspect2Go
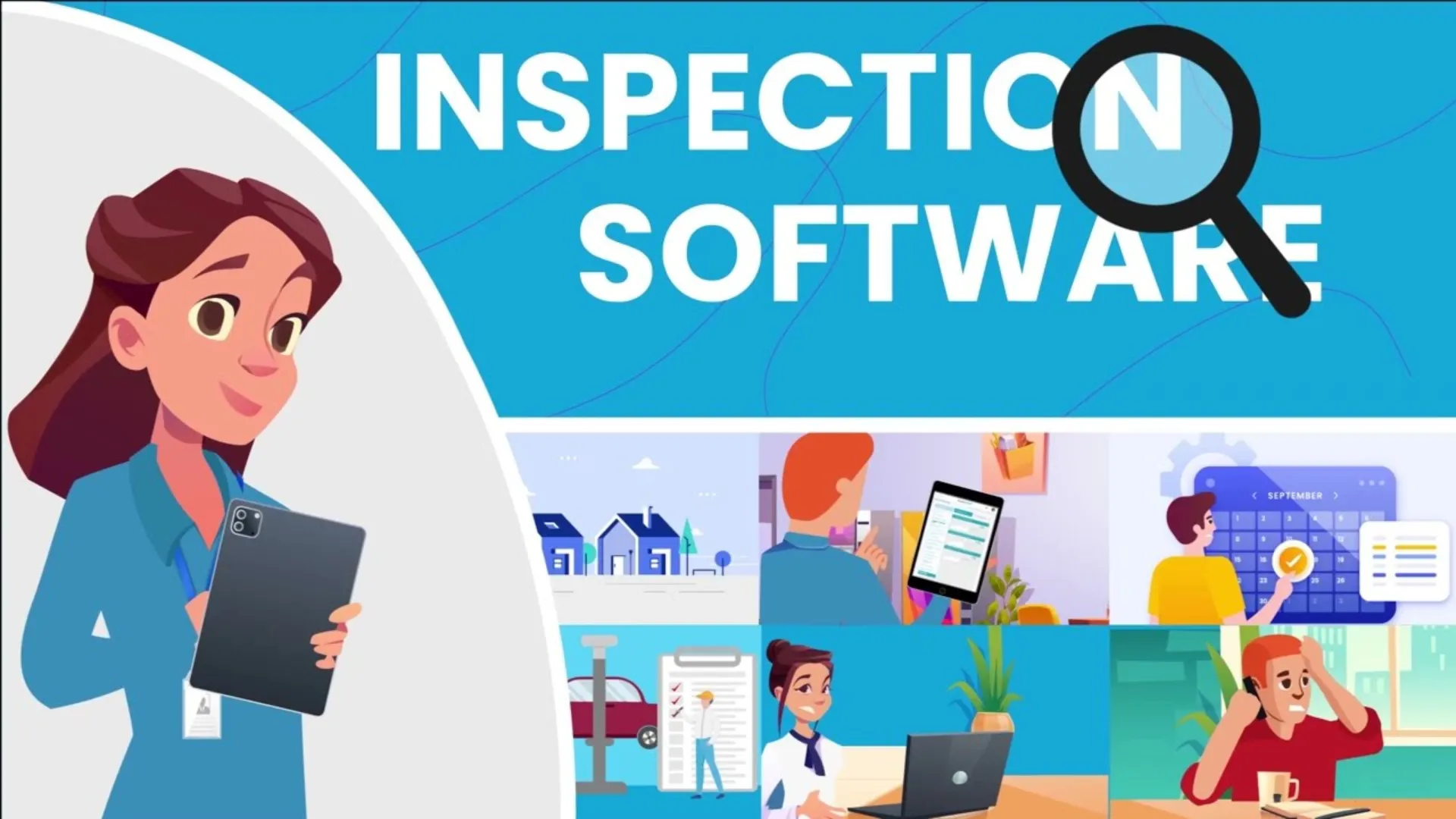
This innovative edge and cloud-based Quality Control (QC) software is exclusively designed for small-scale manufacturing enterprises. Inspect2Go is another best quality inspection software that contributes to cutting the cost of manufacturers and goes a step further by elevating management of product quality to the next level.
Merging the mobile, database, and cloud technologies brings Inspect2Go a complete quality-control solution.
One of the things that makes Inspect2Go a go-to option is cost-effectiveness. The software is designed to greatly improve product quality management, making sure that manufacturers can meet the desired quality levels and more often than not, exceed them entirely.
Key Features
- A user-friendly interface can help to streamline field data-gathering approaches.
- Create on-the-fly reports to meet unique requirements and insights.
- The powerful data management tools allow you to efficiently manage and organize data.
- Using techniques for data analytics can provide significant insights into quality control operations.
- Conduct seamless product quality inspection and document the findings for full record-keeping.
- Stay organized with notification and scheduling options to ensure timely inspections.
- Use geolocation features to monitor data precisely and collect evidence for full analysis.
Pricing
- Contact Vendor
4. MasterControl
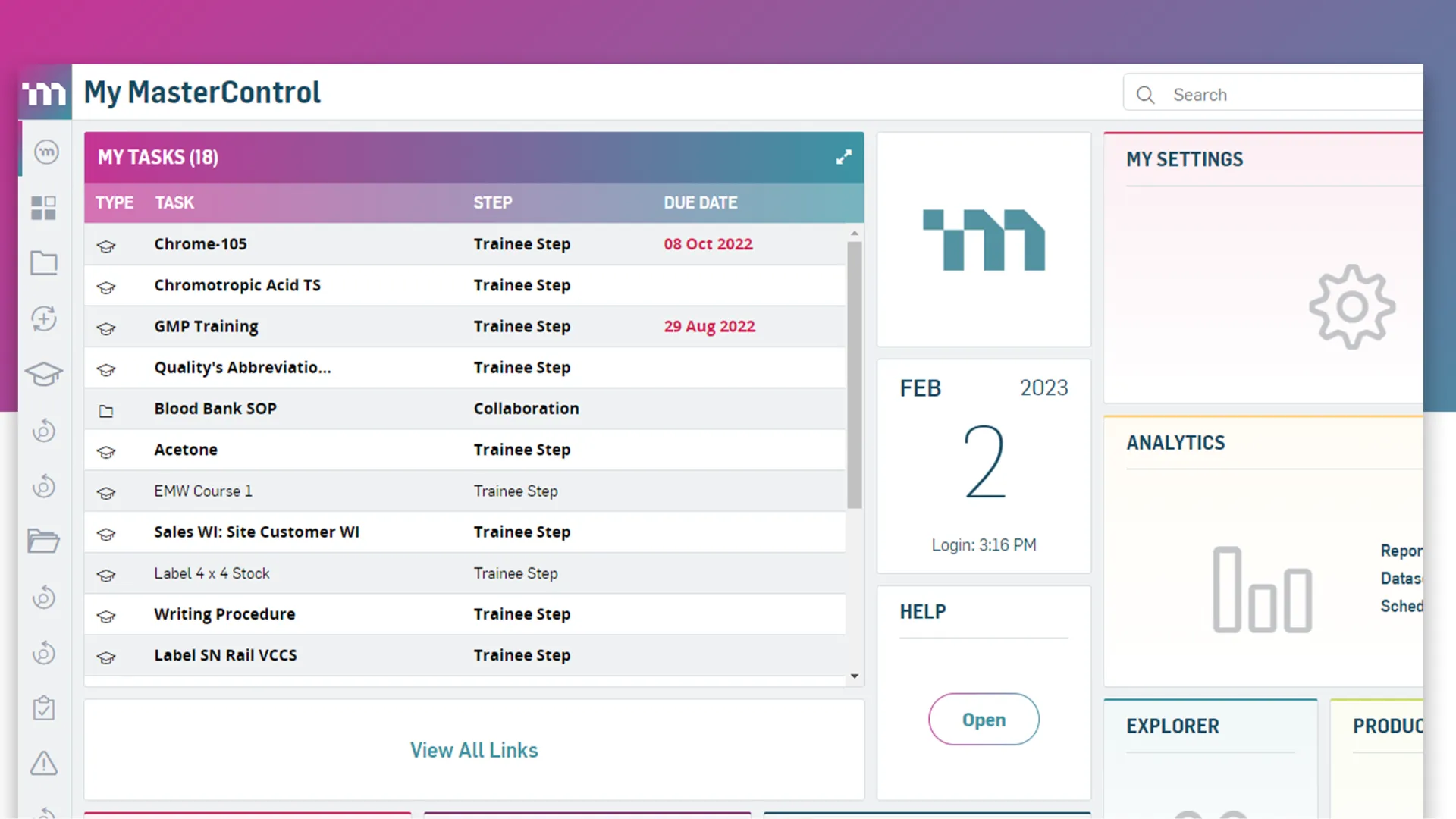
MasterControl is a QC inspection software that includes a multitude of fully integrated compliance and quality management tools in a single platform.
Designed to meet the stringent requirements of FDA regulations and ISO standards, MasterControl's enterprise quality management software is helping companies eliminate paper-based quality processes, as well as facilitate adherence to tougher quality standards.
Key Features
- complies with ISO quality standards and FDA regulations, giving customers a solid foundation to meet industry-specific compliance needs.
- seamlessly implement corrective and preventative activities to solve issues and avoid reoccurrence.
- Automate the handling of nonconformances to guarantee a timely resolution.
- To improve customer satisfaction, manage and respond to complaints efficiently.
- Automate processes with forms-based automation to ensure efficiency and accuracy.
Pricing
- All Access is $199/month
- Advanced is $169/month
- Basic is $109/month
5. QCBD
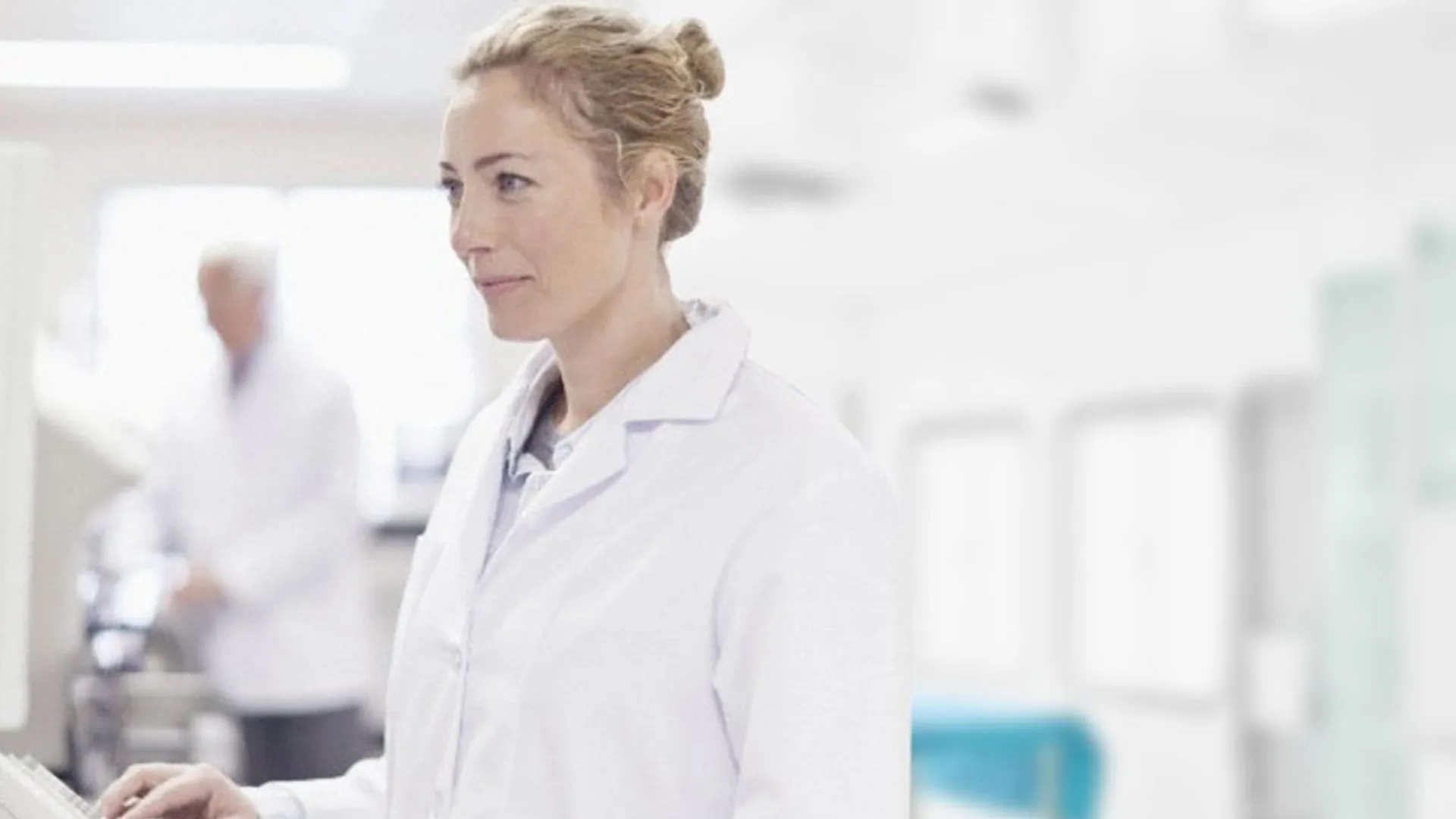
The QCBD is designed to serve the needs of both small and large organizations. Using this quality inspection software, inspectors can reduce human error and data/File corruption.
Moreover, It is the key data hub responsible for:
• Managing items
• Scanning inspection data
• Reporting the quality data information
• Analyzing data (graphically and numerically)
• Displaying data in query, forecast, and chart formats
• Viewing data from UDAs or backend databases (SQL Server, Oracle, ODBC, dBase, Access).
The corrective action module is a key component in the recording and tracking of all corrective and preventive actions aimed at all quality failures. The generated corrective action reports give an excellent platform to carry out an in-depth analysis and to ensure continuous improvement efforts.
Key Features
- Enables the recording and monitoring of actions performed to address and prevent quality issues.
- Manages and resolves process deviations while adhering to a regulated and documented strategy
- Creates a centralized system for efficient document control and management
- Manages products throughout their life cycle, helping to ensure overall quality.
- Streamlines training procedures to improve staff competency.
- Manages and evaluates vendors to provide a consistent and quality-focused supply chain.
Pricing
- Standard Edition
- Enterprise Edition
Contact vendor for tailored price quotation
6. Anvl
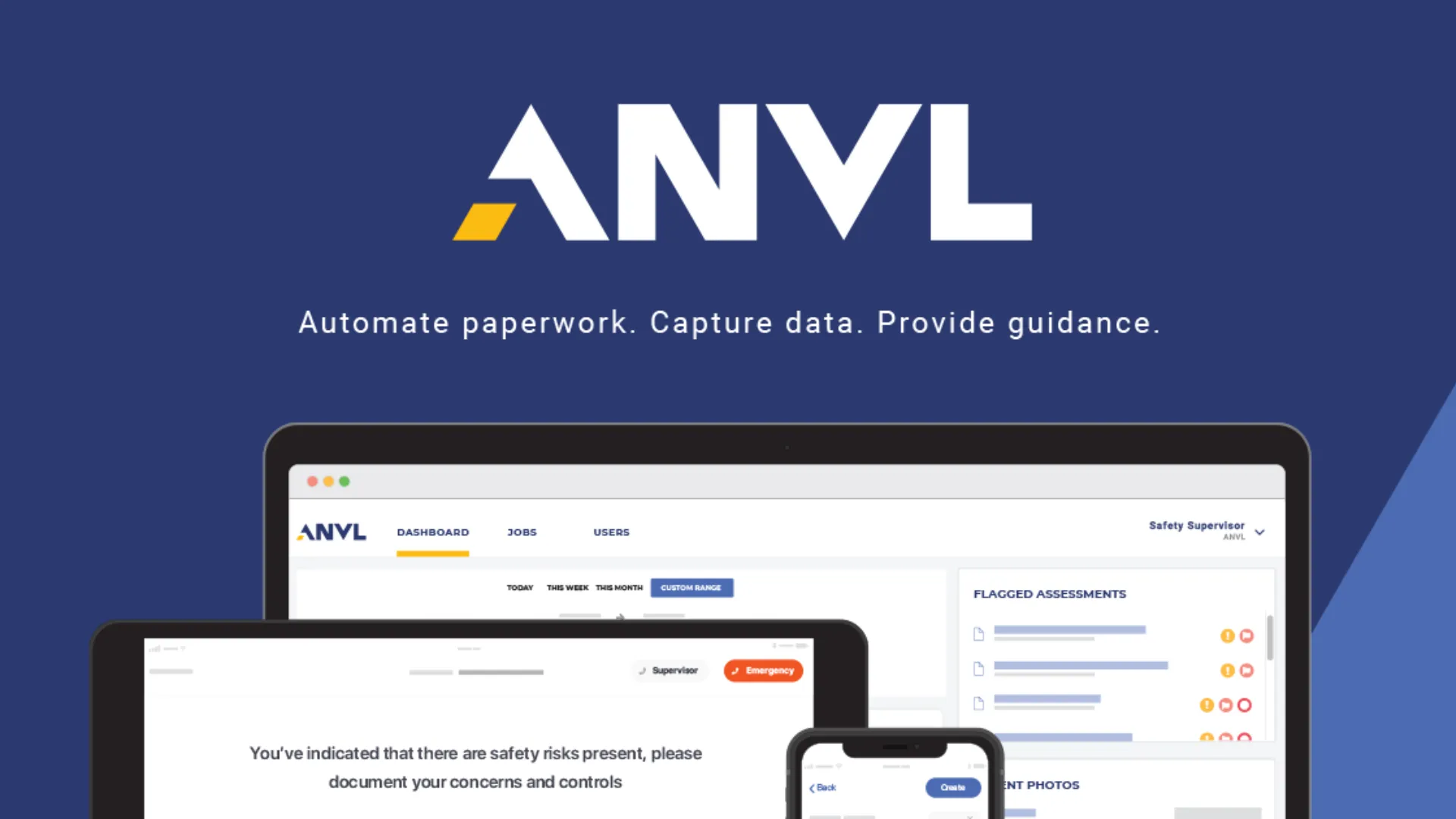
Anvl is an innovative, mobile-native SaaS QC inspection software that assists industrial enterprises in meeting compliance, quality, safety, and sustainability objectives by delivering dynamic-logic workflows via a frontline worker and supervisor mobile app, as well as true real-time reporting and analytics to management and corporate leaders.
Key Features
- provides a comprehensive quality overview, offering businesses a consolidated picture of their quality management processes.
- The Layered Process Audit feature for quality product inspection allows for a more systematic approach to process audits.
- Real-time monitoring and analysis allow businesses to maintain and improve product quality standards.
- The Quality Resources feature provides you with the tools and expertise you need to effectively manage resources, ensuring optimal usage and allocation for quality activities.
Pricing
- Contact Vendor
7. Qarma
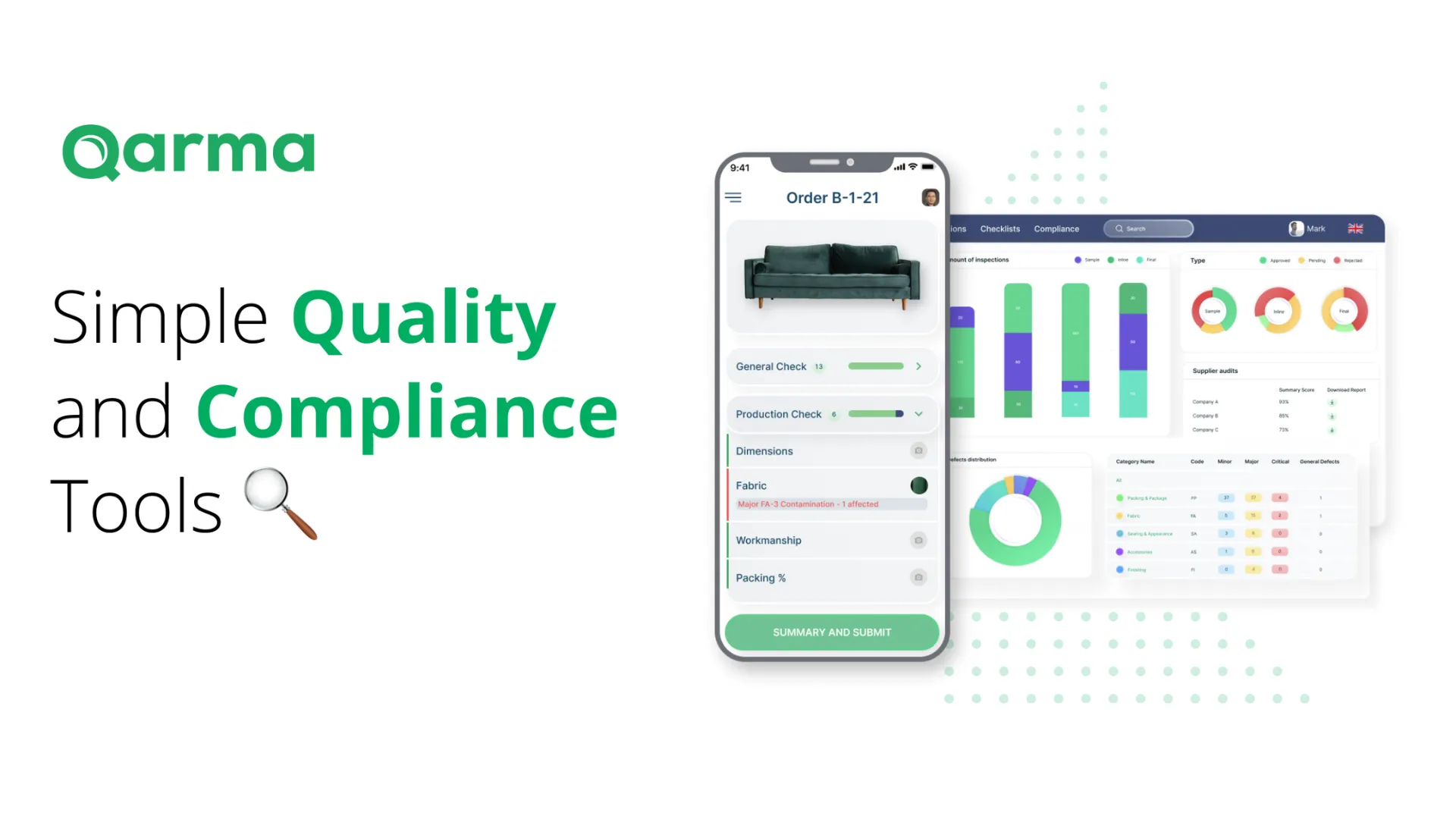
Using one of the best quality inspection software, which organizes processes, increases productivity, and ensures correct data at every encounter, is critical for business growth.
On that note, Qarma is a scalable system that enables teams, suppliers, and agencies - the people you engage with every day - to conduct consistent, responsive, and accurate inspections more quickly than ever before.
Implement established methods to ensure consistent results throughout inspections. This significantly simplifies your inspection procedures, increasing productivity.
Inspectors can view reports from anywhere in the world to make rapid decisions.
Key Features
- Provide teams, vendors, and agencies with a full-quality toolbox that is available via their mobile devices.
- Customize your digital checklists to fit the precise inspection criteria.
- The user-friendly interface makes planning simple, allowing for seamless inspection management.
- Easily control access for inspectors, third-party companies, and external vendors.
- Keep your reports safe, accessible, and well-organized.
Pricing
- Contact Vendor
8. Arena QMS
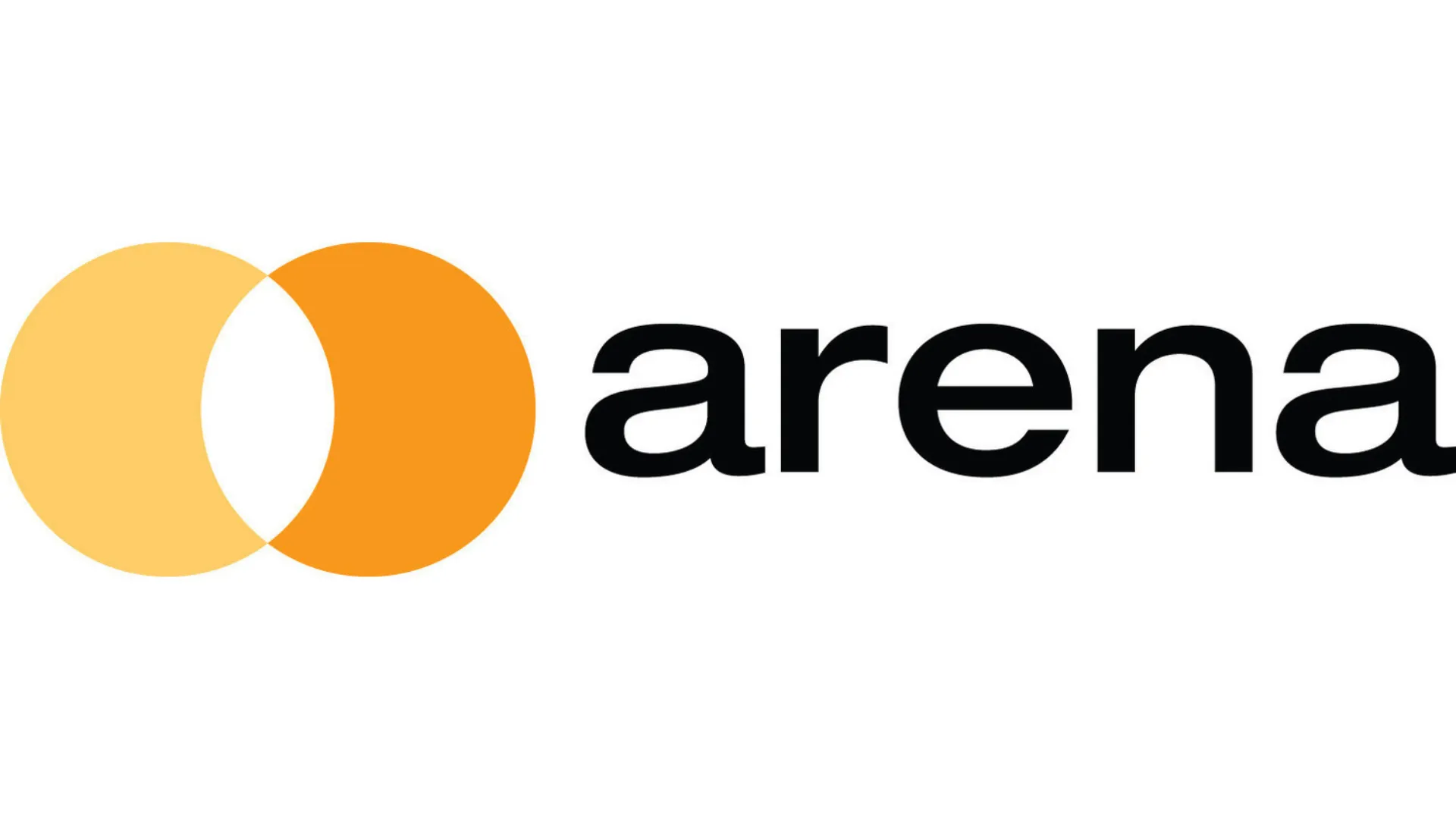
Arena QMS is a top-notch QC inspection software solution for enterprise users.
It is secure cloud-based quality management software that provides visibility for the product lifecycle, tracks quality resolutions indefinitely, and allows for full traceability of issues by integrating supplier interaction into an enterprise's core process.
Arena QMS solutions, which are designed specifically to model an enterprise's needs around FDA standards, benefit a wide range of manufacturing and high-tech companies, from brand management to complete traceability in a multinational corporation and everything in between.
Key Features
- Long-term tracking of quality resolutions allows firms to assess and improve their procedures over time.
- fosters collaboration with suppliers, resulting in a more seamless and integrated approach to quality management throughout the supply chain.
- Fulfill FDA rules and ISO standards, ensuring that businesses can establish and manage quality procedures that correspond to regulatory requirements.
- Reduce costs across the whole value chain by emphasizing efficiency and optimization in quality management operations.
- Streamline approval procedures by establishing default owners and allowing proxy approvals on behalf of unavailable team members.
- Customize your quality procedures by incorporating one or more sign-off steps. This flexibility ensures that the approval process meets your organization's specific needs.
Pricing
- Starts from $89
Over To You!
Through standardized checks, any robust modern-day inspection management software guarantees that inspectors are less likely to make mistakes.
Alongisde that, if the said QC inspection software has a dedicated mobile app, maintaining paperless quality control is possible.
As a matter of fact, going digital with the help of a safety inspection software mobile is the reportedly quicker, simpler, and more intuitive than ever before. You can show compliance with quality requirements while keeping inspection data secure in the cloud.
On top of that, it provides an abundance of advantages for companies looking to improve their quality management procedures.
Organizations can achieve operational excellence, regulatory compliance, enhanced efficiency, and better product quality inspection by learning the fundamentals, investigating important features, selecting the correct QC Inspection Software, and applying it efficiently.
.webp)
%201%20(1).webp)