In the business world, there is one thing that matters above all else: customer satisfaction.
It seems simple enough; When you consistently deliver reliable products and services, you will make your customers happy and they will return.
However, keeping customers loyal to your brand is not easy. Competitors enter, employees churn and the macro environment changes, challenging the standards and processes that uphold consistent value.
Priced on per user or per location basis
Available on iOS, Android and Web
This is why quality assurance standards and quality control testing are critical to both the manufacturing process and service industry.
It ensures that products and services meet standards that ensure customers are happy in every interaction. This builds reputation, and your company’s reputation is arguably your most valuable asset. According to World Economic Forum, reputation is responsible for more than 25% of a company’s market value.
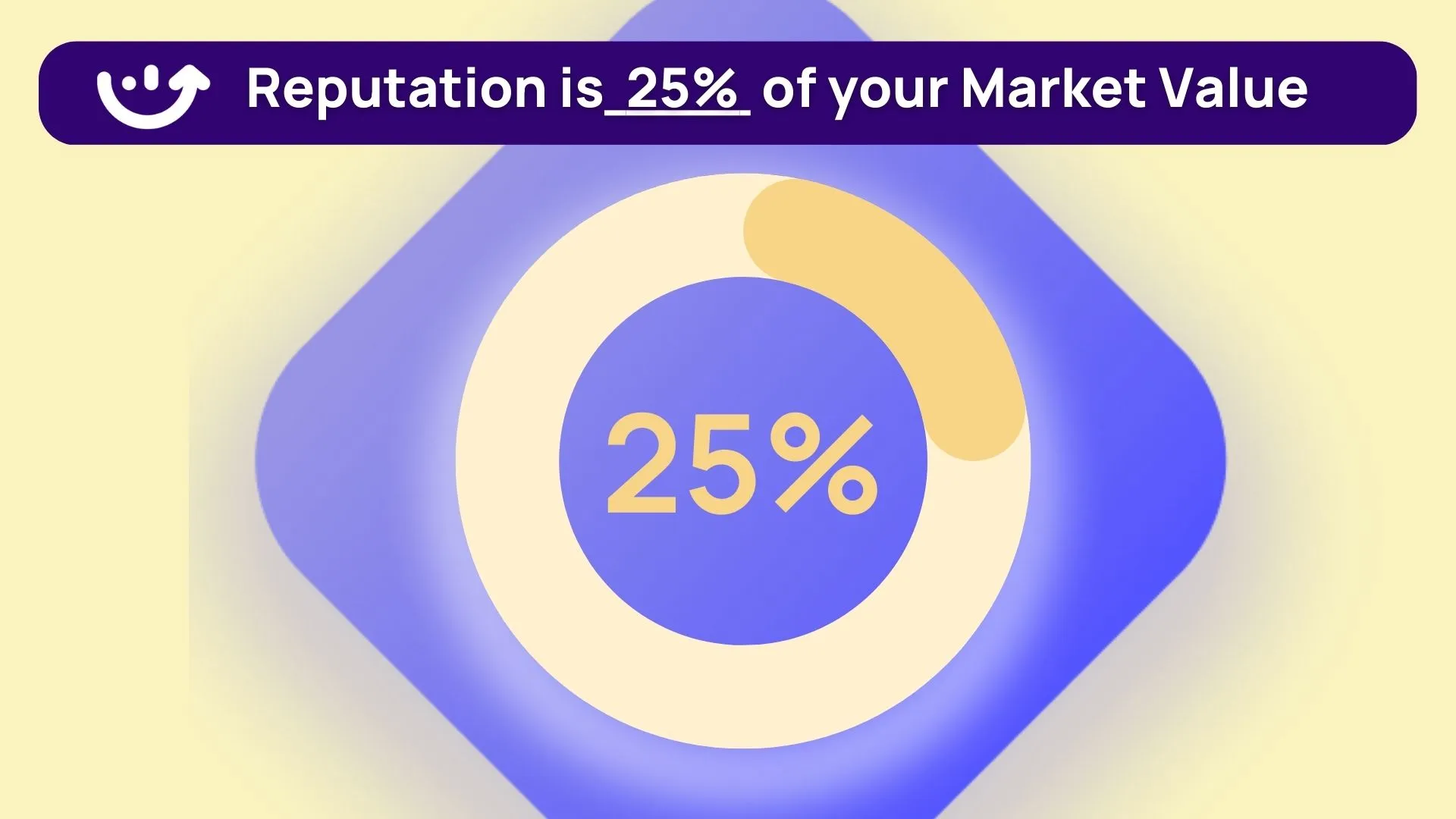
Besides hurting your reputation, It's essential to be aware of the risks associated with poor quality control. Without quality control testing, your production may lead to all kinds of hazards, from safety failures to environmental issues. Poor quality control can even put people at risk for accidents or injuries on the job.
It is critical to implement quality control practices that help you identify and correct problems before they become significant issues. This is where software comes in. Quality Management Software standardizes procedures, streamlines inspections and records data into a digital record for accountability and continuous improvement. Lets take a deeper look.
Recommended Resources:
- Quality and Safety Inspection Software
- Quality Assurance Software
- 5 Best Quality Control Checklist Apps For Businesses In 2024
- 11 Best Safety Management System Software For Workers’ Wellbeing In 2024
- The 5 Best SOP Software for Businesses In 2024
What is Quality Assurance?
Quality assurance (QA) in service industries refers to the process of verifying that a service meets certain standards of quality before it is delivered to customers. This can involve a variety of activities, such as testing, inspections, and audits, to ensure that the service meets the requirements and expectations of the customer.
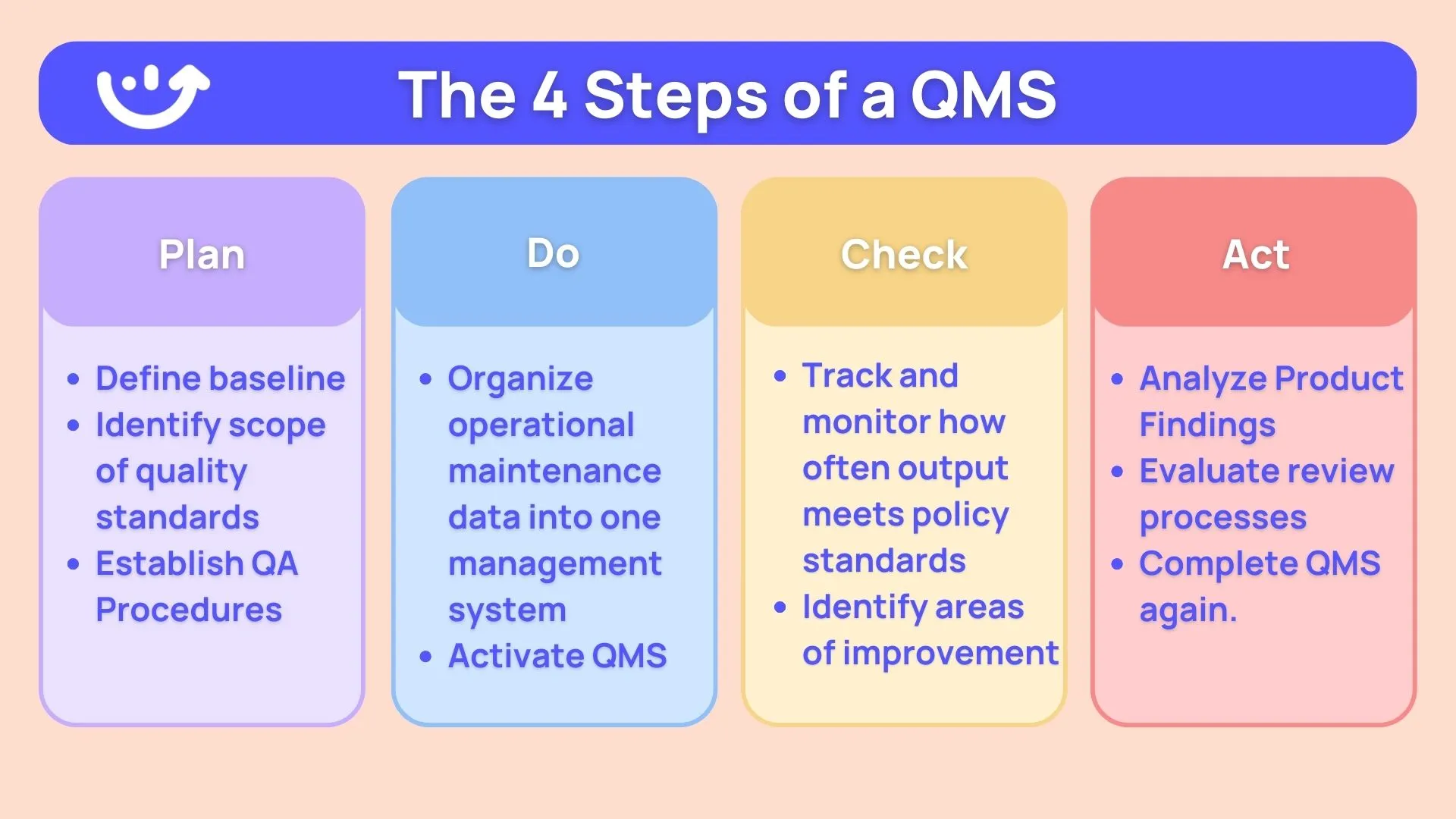
In service industries, QA is often an important part of the customer experience, as it helps to ensure that customers receive a high-quality service that meets their needs. This can be especially important in industries where the service is intangible, such as consulting or professional services, as it can be difficult for customers to assess the quality of the service they are receiving.
There are several key components to a QA process in service industries:
✍🏻 Define Quality Standards and Processes
Defining quality standards is an important part of the quality assurance (QA) process in service industries, as it establishes the criteria that a service must meet in order to be considered of high quality. Quality standards may be defined by the company, the industry, or regulatory bodies, and they can vary depending on the type of service being provided.
When defining quality standards, it is important to consider the needs and expectations of the customers who will be using the service. This may involve gathering input from customers, as well as reviewing industry best practices and regulatory requirements. Quality standards should be specific, measurable, attainable, relevant, and timely (SMART) in order to be effective.
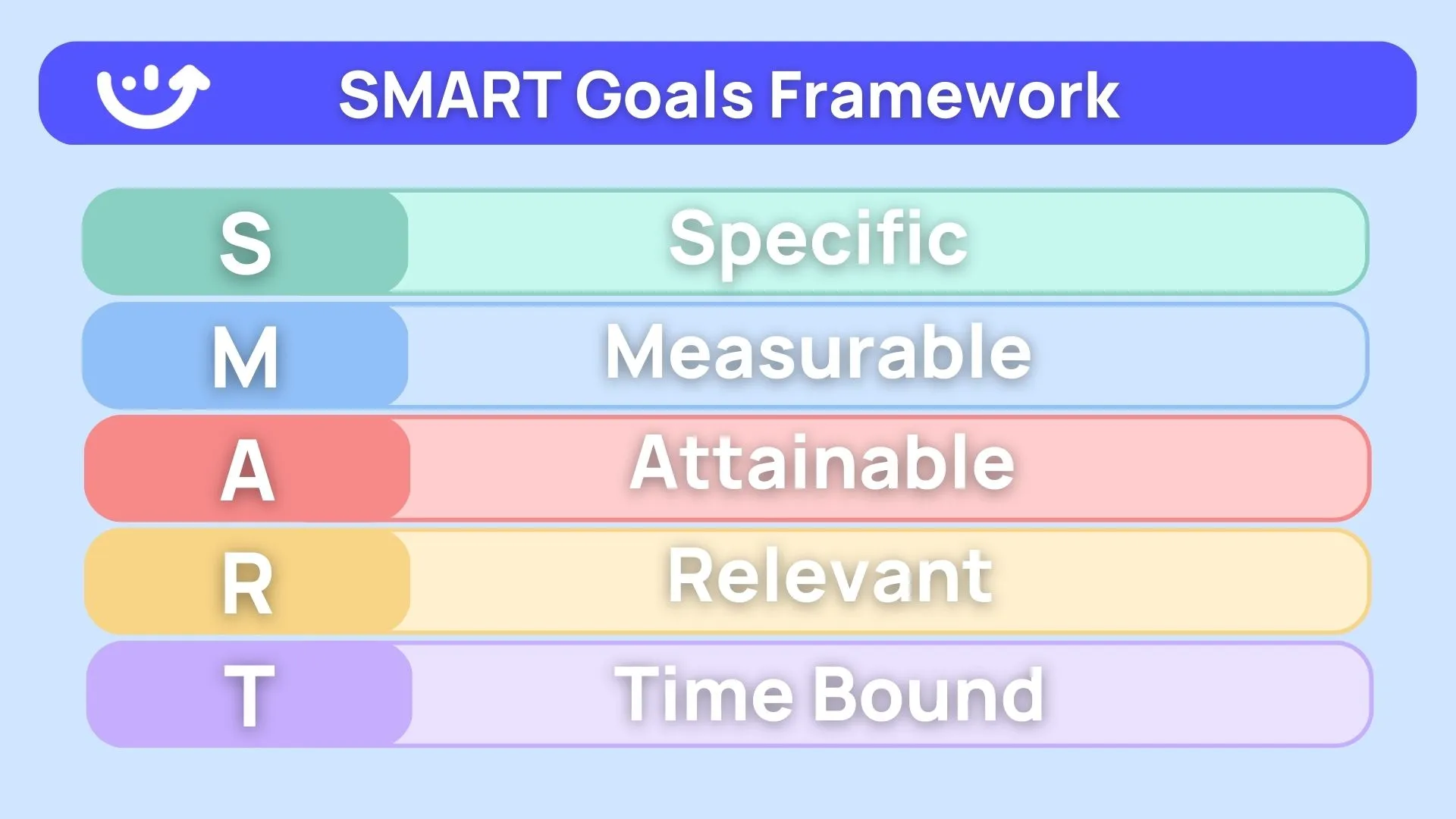
Once quality standards have been defined, they should be communicated to all relevant parties, including employees who will be delivering the service, as well as customers. Quality standards should also be regularly reviewed and updated as needed, in order to ensure that they continue to meet the needs and expectations of customers.
Some examples of quality standards that may be relevant to service industries include:
- Timeliness: Ensuring that the service is delivered within a specified timeframe.
- Accuracy: Ensuring that the service is free of errors or mistakes.
- Customer satisfaction: Ensuring that the service meets the needs and expectations of customers.
- Responsiveness: Ensuring that the service is delivered in a timely and efficient manner.
- Professionalism: Ensuring that the service is delivered in a professional and ethical manner.
- Safety: Ensuring that the service is delivered in a safe and secure manner.
🔎 Inspect and Test Products and Services
Testing and inspection are key components of the quality assurance (QA) process in service industries. Testing involves evaluating the service under different conditions to ensure that it meets the defined quality standards. This can include testing the service in a controlled environment, such as a laboratory or simulation, or testing the service in the field with live customers.
Inspection, on the other hand, involves observing the service being delivered to ensure that it meets the quality standards. This can involve observing the service being delivered in person, or reviewing documentation or other evidence of the service being delivered.
Testing and inspection are important tools for ensuring that the service meets the needs and expectations of customers, and they can be used to identify any weaknesses or issues with the service. Testing and inspection can also be used to validate that the service meets regulatory requirements and industry best practices.
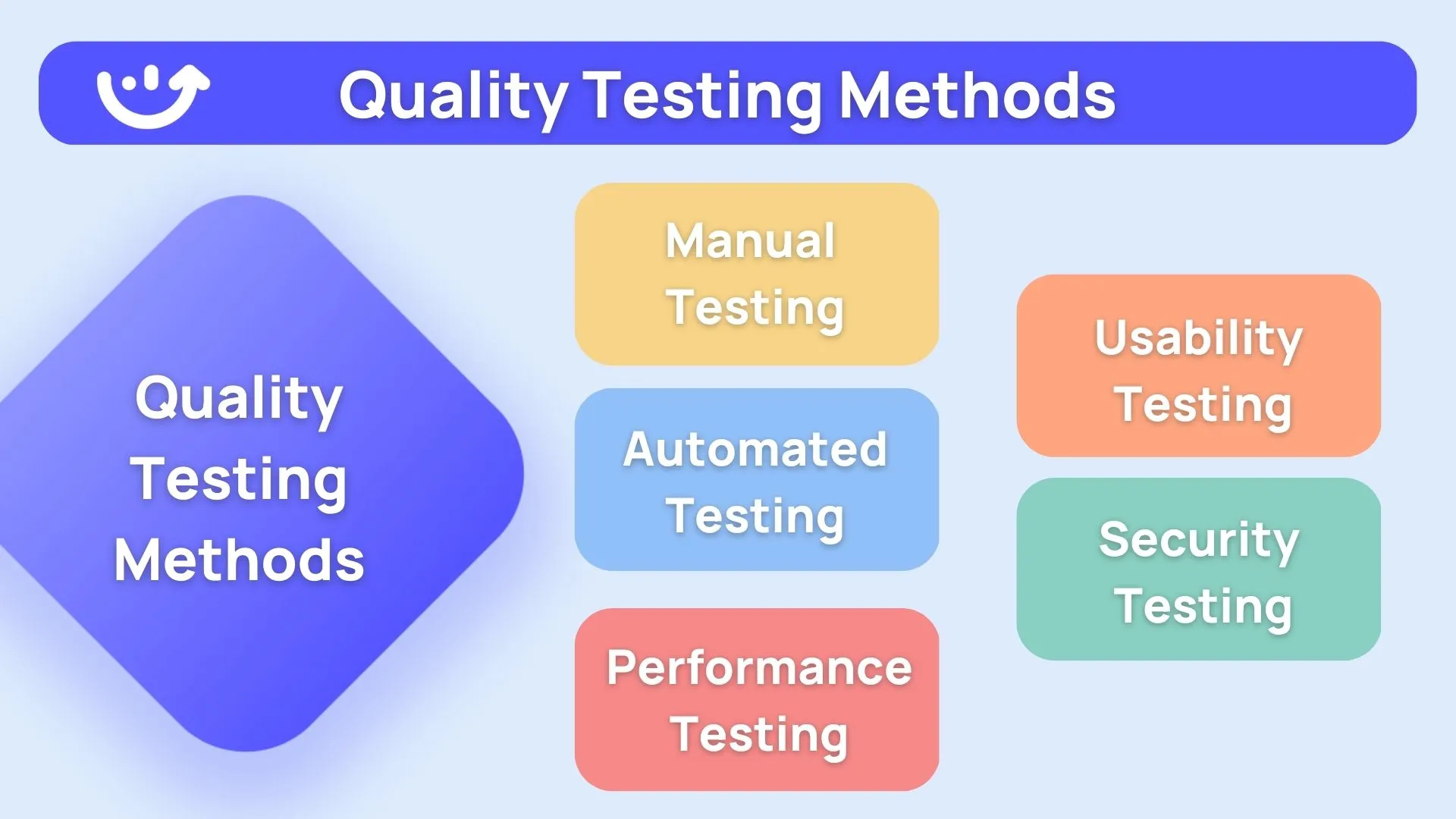
There are a variety of methods that can be used for testing and inspection in service industries, including:
- Manual testing: This involves evaluating the service manually, such as by reviewing documentation or observing the service being delivered.
- Automated testing: This involves using software or other tools to evaluate the service automatically.
- Performance testing: This involves evaluating the service under different load or stress conditions to ensure that it performs as expected.
- Usability testing: This involves evaluating the service from the perspective of the user to ensure that it is easy to use and understand.
- Security testing: This involves evaluating the service to ensure that it is secure and protected against potential threats.
👀 Audit Processes to Identify Bottlenecks
An audit is a process of reviewing and verifying that a service meets certain quality standards. Auditing is an important part of the quality assurance (QA) process in service industries, as it helps to ensure that the service meets the defined quality standards and meets the needs and expectations of customers.
There are a variety of methods that can be used for auditing in service industries, including:
- Document review: This involves reviewing documentation, such as policies and procedures, to ensure that they are up to date and in compliance with quality standards.
- Observations: This involves observing the service being delivered to ensure that it meets the quality standards.
- Interviews: This involves speaking with employees or customers to gather feedback on the service and identify any issues or areas for improvement.
Audits can be conducted by internal staff, external consultants, or regulatory bodies, depending on the specific needs and goals of the organization.
Overall, the goal of auditing is to ensure that the service meets the defined quality standards and meets the needs and expectations of customers. Auditing can help to identify any issues or weaknesses in the service, and can be used to implement improvements and ensure that the service is consistently delivered to a high standard.
💪🏽 Facilitate Continuous Improvement
Quality assurance in service industries is often an ongoing process, as it is important to continually improve the service to meet the changing needs and expectations of customers. This can involve regularly reviewing and updating the quality standards, as well as implementing process improvements to ensure that the service is consistently delivered to a high standard.
There are a variety of tools and techniques that can be used for continuous improvement in service industries, including:
- Root cause analysis: This involves identifying the underlying causes of problems or issues with the service, in order to identify opportunities for improvement.
- Process mapping: This involves creating a visual representation of the steps involved in delivering the service, in order to identify areas where improvements can be made.
- Six Sigma: This is a data-driven approach to continuous improvement that involves identifying and eliminating defects in a process.
- Lean: This is a continuous improvement methodology that focuses on eliminating waste and increasing efficiency in a process.
- Kaizen: This is a continuous improvement approach that involves making small, incremental changes to a process on an ongoing basis.
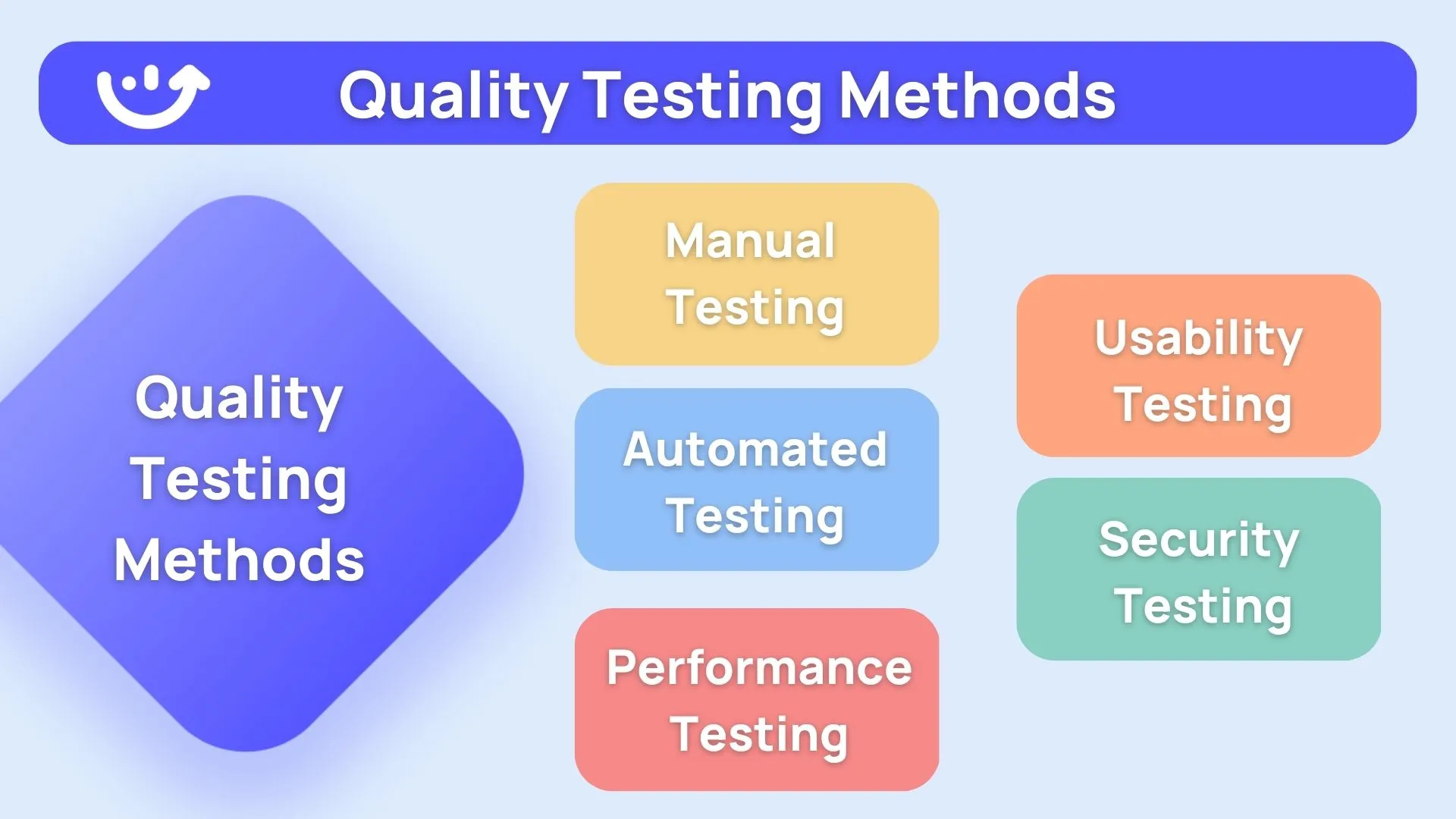
Continuous improvement can involve a variety of activities, such as reviewing and updating quality standards, implementing process improvements, and gathering and analyzing customer feedback. It is important to involve all relevant parties, such as employees and customers, in the continuous improvement process in order to ensure that the service meets the needs and expectations of all stakeholders.
Overall, the goal of QA in service industries is to ensure that customers receive a high-quality service that meets their needs and expectations, which can help to build customer loyalty and improve the reputation of the company.
Why Quality Assurance Is Important?
Quality Assurance is a systematic approach to evaluating the quality of a product or service and determining how to improve it. QA differs from QC because it focuses on evaluation rather than simply checking whether something meets standards. A QA must follow these evaluation standards to meet customer expectations and increase profits.
Quality Assurance Ensures Consistent Value to All Stakeholders
Quality assurance (QA) is important for a variety of reasons, including:
- Customer satisfaction: QA helps to ensure that customers receive a high-quality service that meets their needs and expectations, which can help to improve customer satisfaction.
- Reputation: A service that consistently meets quality standards can help to improve the reputation of the company, which can lead to increased customer loyalty and more business. A recent survey shows 93% of consumers read reviews online before buying a product. If you want customers to purchase from you instead of your competitors, you must ensure that your products are of the highest possible quality.
- Compliance: QA can help to ensure that a service meets regulatory requirements and industry best practices, which is important for maintaining compliance.
- Efficiency: QA can help to identify and eliminate defects in a service, which can improve efficiency and reduce the cost of delivering the service.
- Continuous improvement: QA is an ongoing process that involves regularly reviewing and improving the service, which can help to ensure that the service remains relevant and meets the changing needs and expectations of customers.
What is Quality Control Testing?
Quality control testing is a specific type of testing done on products to ensure they meet quality control specifications. These tests can involve taking samples of a product during various stages of production and comparing them to a set of criteria. It can be regular inspections of the production and customer facing processes. It can be spot checks of customer feedback or task completion data.
In some cases, these standards are established by industry professionals, while others are determined by the organization producing the product. This criterion may include color, texture, or size, which can be tested by measuring physical characteristics. Quality control testing is a cost-effective way to reduce labor costs and increase production output, leading to higher revenue.
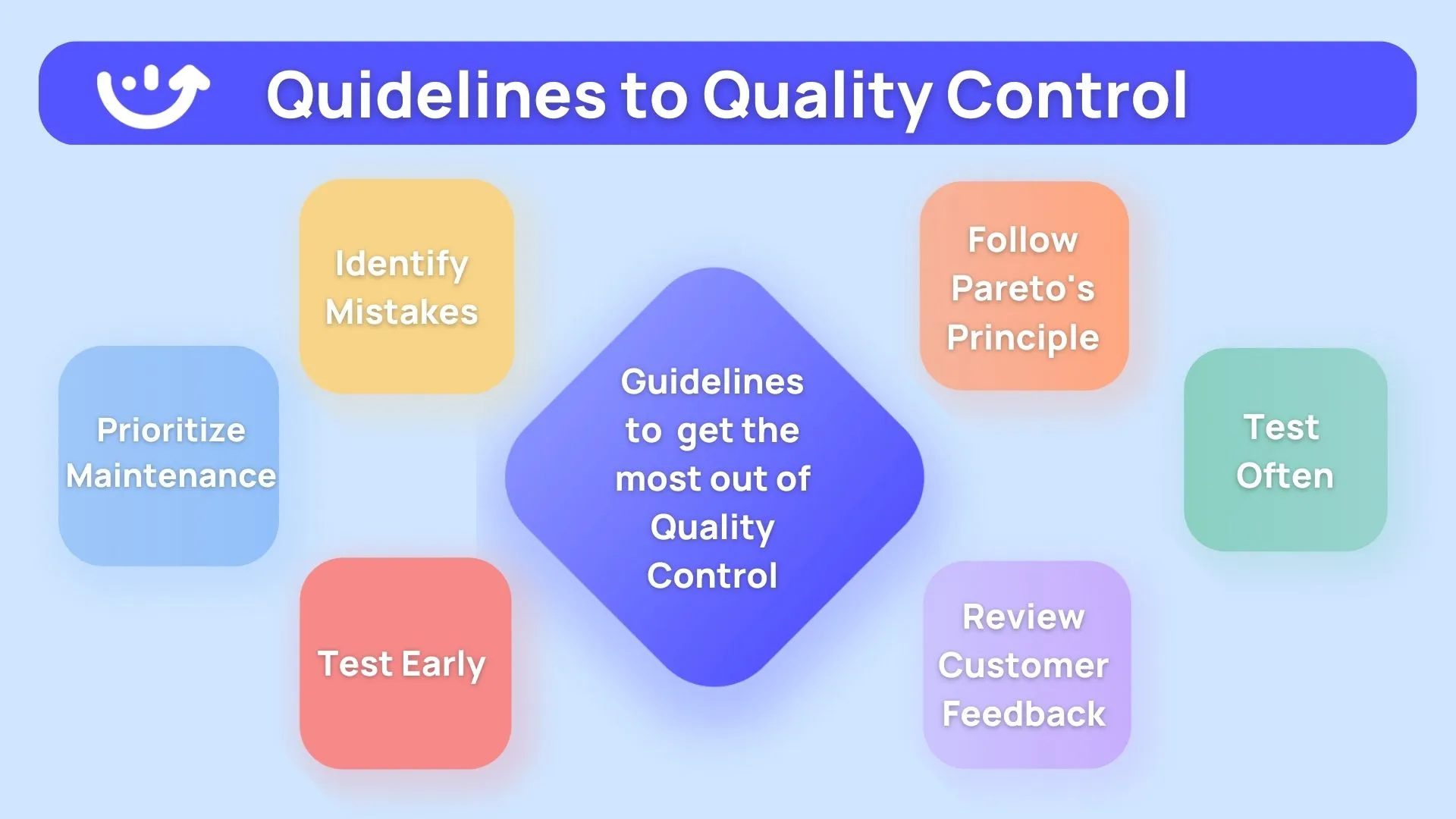
Quality Control Testing Tips
When conducting quality control tests, it is important to prioritize time and attention to key areas for improvement. Here are a few tips to align priorities:
- The Pareto principle says that 80% of defects are clustered in 20% of the elements of a product or service. Identify that 20% quickly and you can save a lot of time and money.
- Test early and often. Don't wait for customer complaints to pile up before taking action and understanding your offering in detail.
- Focus where impact of failure hurts the most. With limited resources, prioritization is necessary.
- Gather Customer Feedback. The complete absence of errors does not necessarily mean your product is user-friendly. It's crucial to gather qualitative feedback from real customers to identify what their experience was like.
Quality Control Testing Example: Hospitality
Quality control testing can be incorporated in several ways in the Hospitality Industry. From the housekeeping team to the General Manager, every staff member has a hand in quality testing.
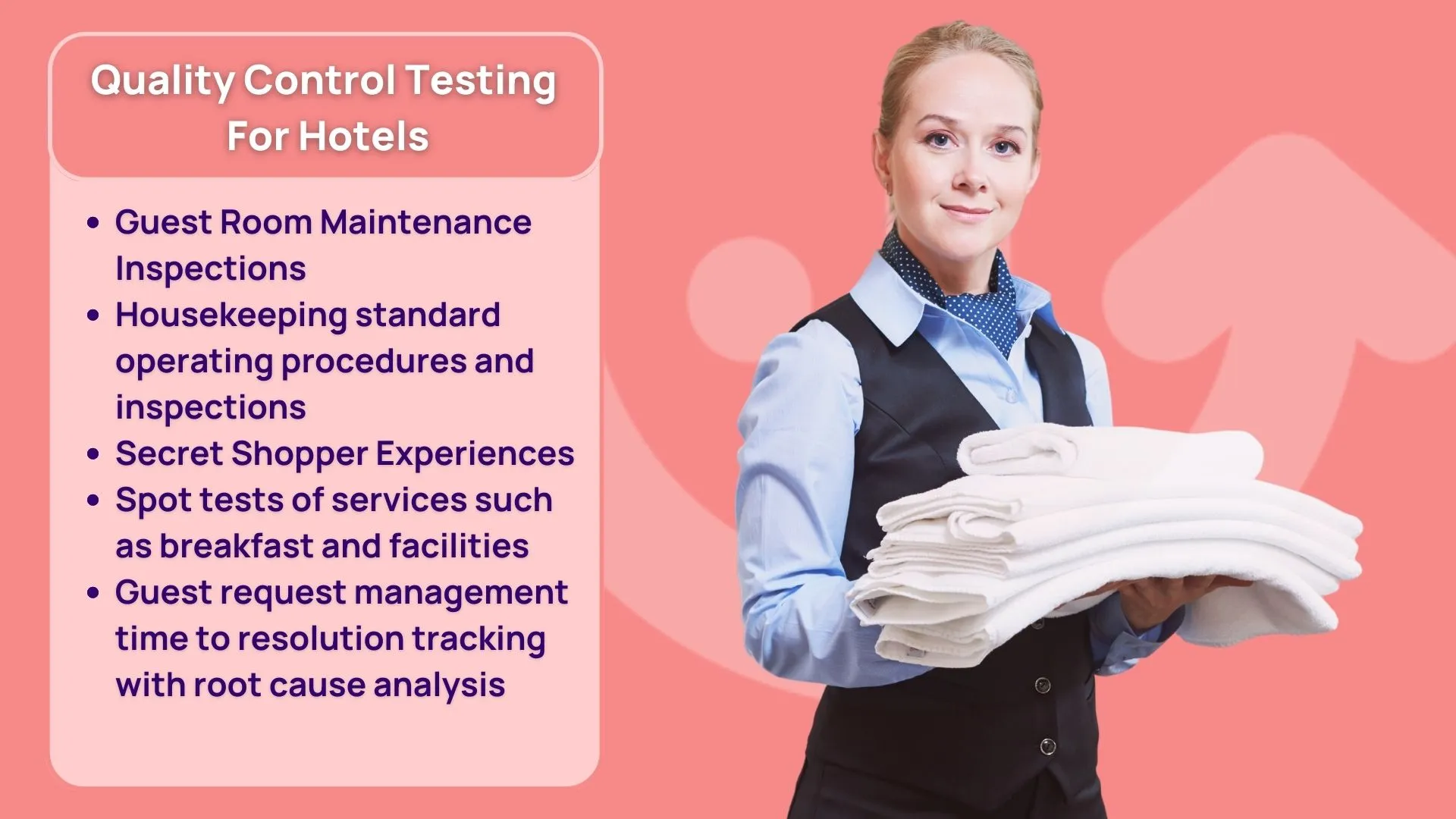
✅ Checklists and Inspections Ensure Housekeeping is Consistent
In hospitality, first impressions are key! From TV malfunction and empty remote batteries to HVAC and door lock issues, there are many ways in which a hotel room can fail to meet customer expectations.
To protect against this, the housekeeping staff can use a checklist to ensure that all areas of the guest room are cleaned and checked for maintenance issues prior to the guest arrival. The maintenance team can also conduct regular inspections of the guest rooms and common areas to identify any issues that need to be addressed. By being proactive with testing and inspections, hotels protect their brand and ensure satisfies guests.
🗣️ Tracking Guest Requests Provides Many Optimization Opportunities
In addition, the hotel can implement a system for tracking and responding to guest requests complaints or issues. For example, if a guest reports a problem with the air conditioning in their room, the maintenance team can promptly address the issue and document the resolution. This helps the hotel to identify and resolve any issues in a timely manner and prevent similar problems from occurring in the future.
Using a work order software is the best way to ensure proper communication, documentation and data reporting to continually improve guest request fulfillment. Using this method, managers and spot check outliers in resolution time to identify potential trends (employees, equipment, floors, rooms) and root causes (old, faulty, poorly trained, poorly maintained) that could be acted upon to prevent future complaints.
🤩 Surveys and Spot Testing are Great Ways of Identifying Areas for Improvement
Finally, the hotel can gather guest feedback through surveys and use this information to spot test and identify areas for improvement. For example, a hotel may receive guest feedback that the breakfast was stale or cold. In response, the hotel may choose to have a manager randomly test breakfast items, logging issues as they arise. Then, using tools such as a root cause analysis, a manager can understand what is causing the quality error. Is it an employee, a supplier or faulty equipment? By regularly gathering and analyzing this feedback, the hotel can identify areas for improvement and make changes to enhance the overall quality of the guest experience.
Quality Control Testing Example: Construction
From standard operating procedures to inspections, punch lists and customer feedback, quality assurance is core to the construction process. A construction team can incorporate quality control testing into their process in several ways to ensure their service is creating brand advocates every time.
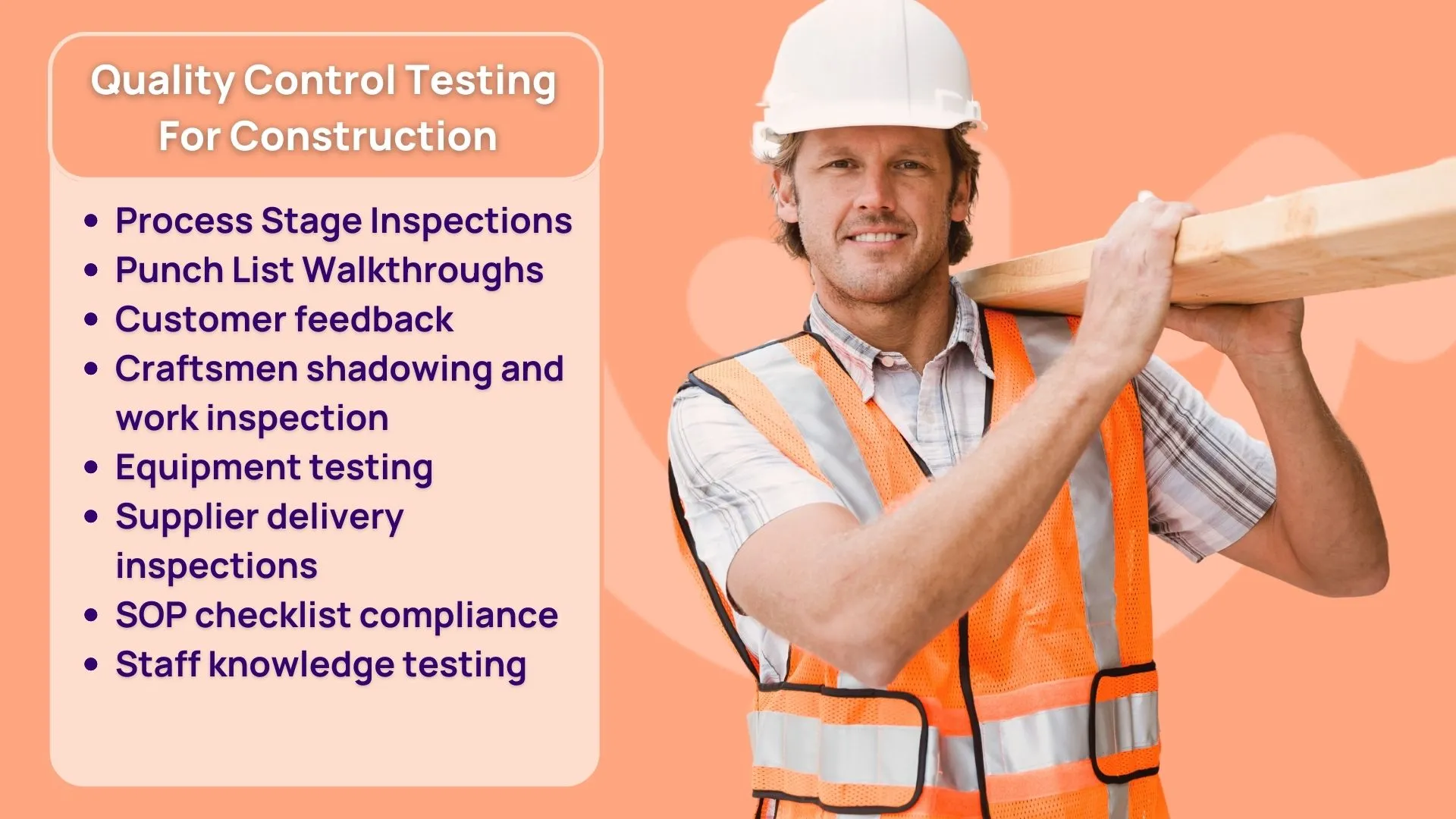
🛠️ Inspections Provide Quality Control at Each Stage of Construction
One way is through regular inspections of the work as it is being completed. For example, the team may have a designated quality control inspector who checks the work at various stages to ensure that it meets the necessary standards and specifications. This may include checks for things like proper materials and installation, as well as ensuring that the work is being completed safely.
📋 Punch Lists are a Common Quality Control Testing Method
Another way that a construction team can do quality control testing is by conducting functional testing and inspections of the finished product. A construction team at a building site is using punch lists for quality control testing as they near the end of a project. The punch list is a document that outlines any remaining tasks or issues that need to be addressed before the project can be considered complete. This includes checking that all finishes, such as paint and flooring, meet the necessary standards and that all systems, such as electrical and plumbing, are functioning properly.
😃 Customer Feedback on Communication Aids in Quality Assurance
Finally, the construction team can gather feedback from the project owner or other stakeholders and use this information to identify areas for improvement. For example, if the project owner reports issues with the team's communication or project management, the team can take steps to address these issues and improve their processes moving forward. By regularly gathering and analyzing this feedback, the construction team can identify areas for improvement and make changes to enhance the overall quality of their work.
Quality Control Testing Example: Restaurants
Restaurants can use quality control testing to improve their service in a number of ways. This includes testing of staff capabilities and compliance as well as ingredient quality and meal taste prior to customer delivery.
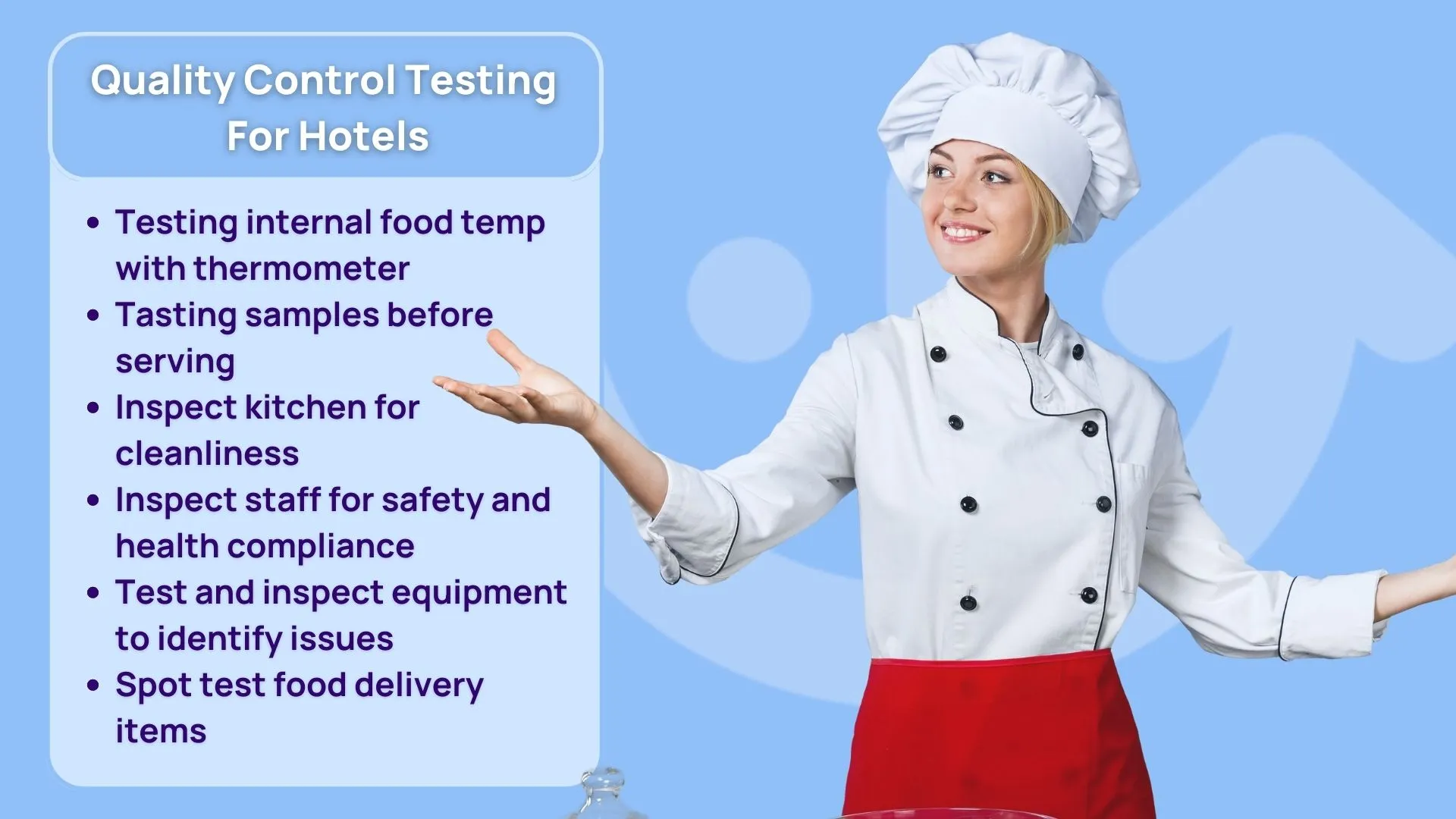
🍔 Testing Food Before It Leaves the Kitchen Saves Money and Ensures Quality
One way restaurants can use quality control testing is by having the chef taste a sauce or dish before it is served to customers. This helps to ensure that the food is flavorful and meets the chef's standards before it is served to the customer.
Another way that restaurants can use quality control testing is by using a meat thermometer to ensure that orders are cooked according to customer preference. This helps to ensure that the food is cooked to the desired level of doneness and helps to prevent under or overcooking.
🍴 Inspecting the Kitchen, Staff and Ingredients Leads to Consistent Dishes
Restaurants can also conduct regular kitchen inspections to ensure that surfaces are clean, employees are following hygiene and safety protocols, and food is being handled according to regulations. This helps to maintain a clean and safe environment for both employees and customers.
In addition, restaurants can spot test samples of food and ingredients that are delivered to the restaurant to ensure that they are fresh and of high quality. By regularly testing the food and ingredients that they serve, restaurants can ensure that their customers are receiving the best quality food and service possible.
.webp)
%201%20(1).webp)