Quality control is a critical component in any business that produces goods or services. Poor quality control can result in dissatisfied customers, increased costs, and a damaged reputation.
In today's competitive market, companies cannot afford to have these setbacks. By implementing checklists, companies can ensure that their products or services meet the required standards and specifications.
Priced on per user or per location basis
Available on iOS, Android and Web
What is quality control for businesses?
Quality control refers to monitoring products and services to ensure their health and quality. For service businesses, good quality control means offering top-notch services to their customers.
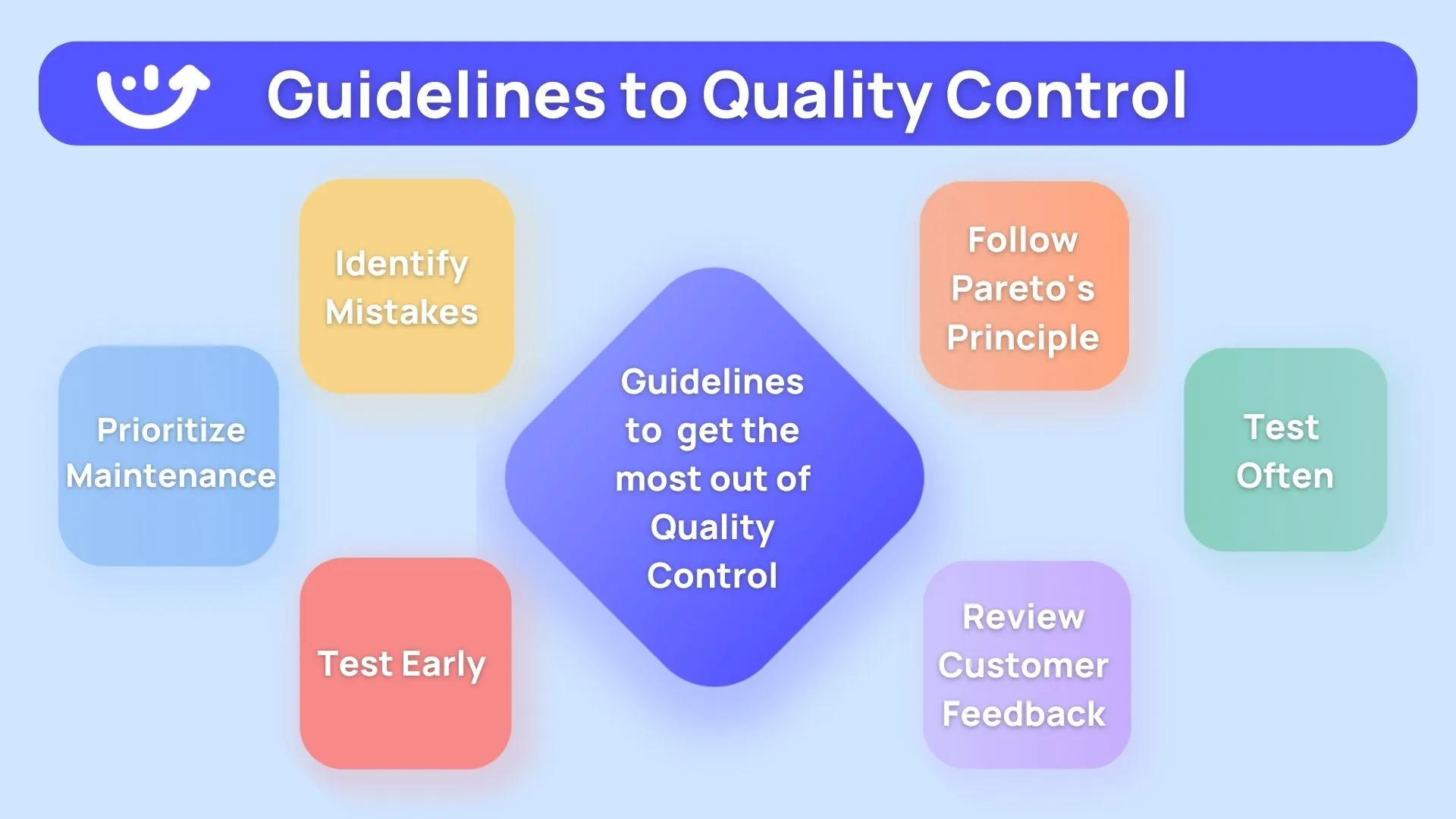
A lot goes into offering a good customer experience.
- Are all the products you offer of good quality?
- Are all the services you offer of good quality?
- How quickly are you delivering these services?
- Are your employees well-trained?
- Are your employees following all SOPs correctly?
- Are your employees engaged and excited about work?
- Do you have enough data to gauge customer satisfaction?
The best way to achieve these is by standardizing processes and implementing a system to easily deploy and track them. Quality control checklists make this possible.
Why are quality control checklists important?
You can’t expect every employee to remember a nine-step process every time they’re about to start one of many tasks.
This is where quality control checklists come in. Quality control checklists help set critical SOPs in place to make it easier for staff members to follow them. This helps standardize every process, making it safer and more efficient.
.webp)
This standardization has tons of benefits.
- Build customer loyalty: Quality control checklists help improve services so you’re able to maintain a healthy business reputation. Bad reviews create buyer hesitancy and threaten your bottom line.
- Avoid compliance fines: Poor quality control can extend to unsanitary conditions or lack of safety. These can result in hefty compliance fines.
- Meet legal standards: You’re also able to reduce your risk of liability claims and lawsuits when employees and customers are both well-protected.
- Avoid pencil whipping: With strong SOPs and checks in place, employees cannot sign off on things that haven’t been completed. This creates better work integrity.
- Establish accountability: Quality control checklists help you track work quality by employee. Teammates are also able to inspect each other's work.
- Access data insights: You’re able to understand how closely your employees are following SOPs, how long certain tasks are taking, and how your
data analytics/process optimization, cost projection, team management, etc.
3 ways to solve the problem
Quality control checklists can be implemented in three different ways. Some are more traditional while others are more future-facing. Let’s have a look at each of these.
1. Pen and paper
Pen and paper checklists are how companies have been implementing quality control for ages. This classic method now requires printed quality control checklists that are filled out by employees on a clipboard.
You create a printed quality control checklist by shortlisting all employee processes and listing out the steps needed to complete each of them. Add checkboxes next to each step. Then, save each of these processes and print copies whenever a task is scheduled. Let’s assume one of these processes is a floor inspection checklist.
Want to save time designing these checklists? Get printable quality control checklists from Xenia’s checklist library.
Each copy is attached to a binder or handed in a folder to the concerned employee. As they perform their task, they follow each step on the list and check it off. Once finished, the checklist is reviewed by a supervisor and safely stored in the company records.
But is this approach right for you? Let’s dig a little deeper.
🤩 Pros
- Easy for old-school staff to understand
- Does not require tech or electronics
🤬 Cons
- Takes a lot of time to develop, fill, collect, and store
- Limited accessibility and accountability
- May not be editable
- Tough to analyze results depending on how different people fill them
- High risk of getting lost or damaged
- Does not prepare for future
The cons mostly outweigh the pros in the case of the pen-and-paper method. This is why modern companies are moving towards digital tools such as excel spreadsheets and quality control apps.
2. Excel spreadsheets
A step ahead of the traditional pen-and-paper method, excel spreadsheets offer digital quality control checklists. This is a more editable and consistent way of filling out checklists. It’s also easier to keep excel sheets secure.
To make a checklist in excel:
- Open a new spreadsheet and label it as the process it’s meant for.
- Add rows for each inspection step.
- Add columns for dates.
- Once an inspection has been completed, hide the column.
- Pivot the entire table to see insights.
Want to save time with a pre-built template? Get a head start with Xenia’s free excel logs. These have a ‘Submit Log’ button so each completed entry is easily added to the log history.
Here’s how to use Xenia’s quality control spreadsheets:
- Access the spreadsheet of your choice and make a copy.
- The spreadsheet includes a sheet for team members. Add the names of your team members here. These will become accessible in the employee dropdown in the main ‘Entry form’ sheet.
- Share the spreadsheet with your team.
- As an employee gets ready to perform an inspection, they head to the ‘Entry form’ sheet to fill it.
- Once an entry is filled out, the team member clicks on ‘Submit Log’ for it to be automatically added to the log sheet.
🤩 Pros
- Digitizes inspections
- Offers an editable solution
- Free Forever
- Fast to get started
🤬 Cons
- Requires basic excel knowledge
- Cannot attach images
- Difficult to use on mobile
- Difficult to scale with multiple types of assets
- Less functional for team operations
- Does not link to task assignments
3. Quality control software
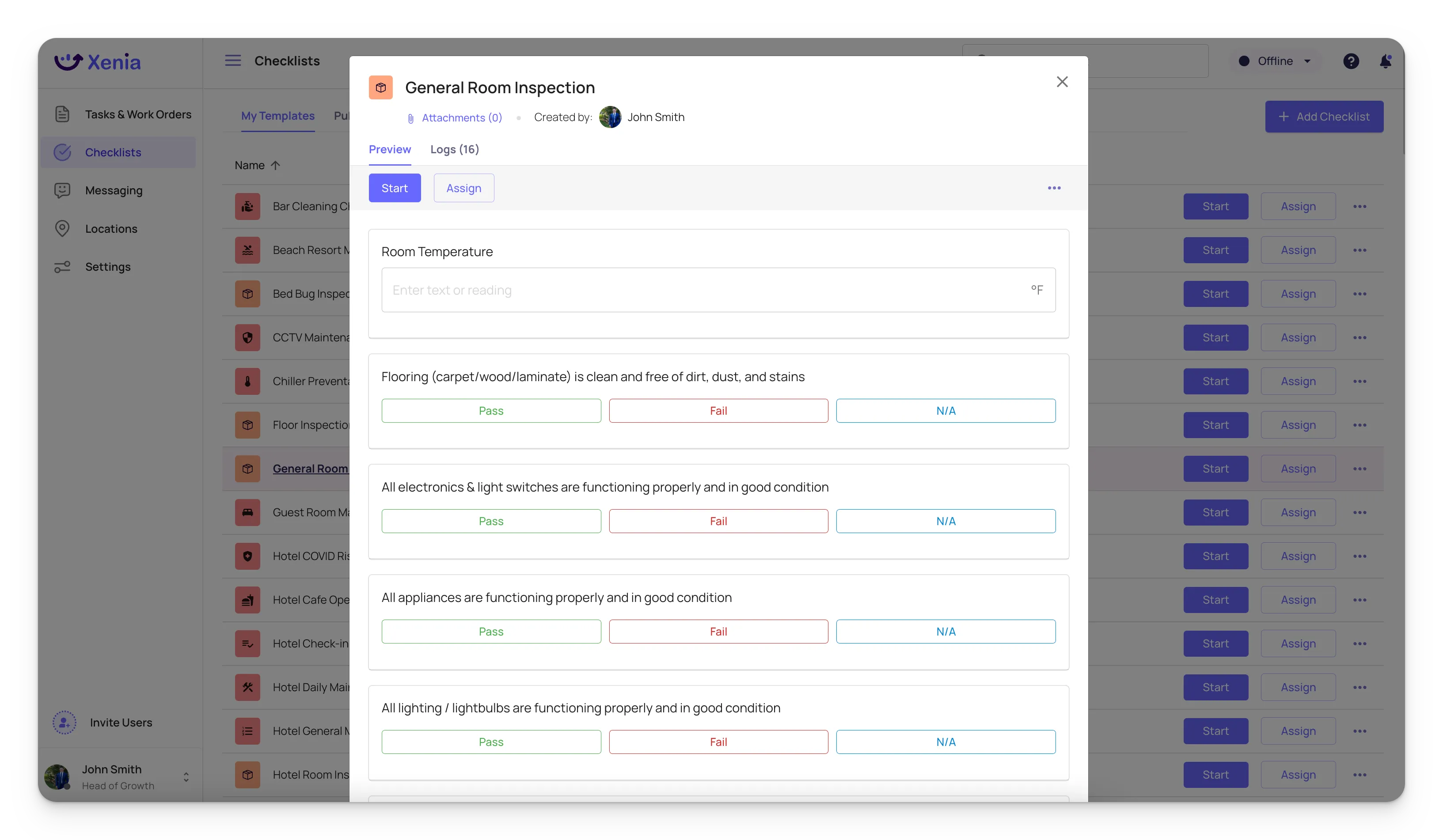
The third option for creating quality control checklists is via checklist software. These are dedicated apps that offer both built-in and custom forms.
This digital solution offers better functionality than excel spreadsheets as these can be accessed at any time from any device and filled out quickly on the go as well. On top of that, many of these have other features that also allow task assignments, internal messaging, progress tracking, and data reports.
🤩 Pros
- Easy checklist creation
- Mobile-friendly forms for deskless workers
- Progress tracking for managers both of task completion and QC testing
- Data analysis to show process improvement
- Maximum flexibility and data security
- Very easy to scale for multiple processes
🤬 Cons
- Often paid solutions
- Require teams to learn new tools
Quality control apps are further divided into different categories. We’ll explore each of these to help you pick the right solution for your organization and use case.
Operations Management Apps Assign, Record and Measure Quality Control
Operations management apps offer a suite of features that help companies manage their tasks, inspections, employees, and locations.
An example of an operations management app is Xenia. It offers custom and pre-built checklists both with an easy-to-use checklist builder. There’s also a task & work orders module that lets users create tasks, assign them, and attach checklists as well. Other modules include instant messaging, and location history.
The best part about the tool is that it’s mobile-first to cater to the needs of on-the-go teams and deskless workers.
Here’s how to use Xenia for implementing quality control processes:
- Pick a checklist, SOP, or inspection form from the template library, or create your own.
- You can also require pictures and notes on your checklist responses.
- Once your checklist is ready, start it yourself or assign it to a member of your team. A task is created when you assign it to another user.
- Set it as recurring so users can perform the process periodically.
- Track task progress, add comments, or attach pictures.
- Message the concerned user to collaborate on the task or see if help is needed.
.webp)
%201%20(1).webp)