It is of the utmost importance for an organization to maintain the quality of its products when they are supplied to customers since the product is the most essential driver of the business's success. However, nothing is perfect in this corporation, since people make mistakes and machines and equipment malfunction.
This disrupts the manufacturing process, causing the organization to generate items that do not fulfill the requirements defined by the norms and specifications. For that reason, QA inspection and testing are critical to ensuring that the items provided to the client meet the specifications that the customer has requested.
The statistic that 69% of customers are more loyal to companies that provide a customized experience emphasizes the necessity of quality assurance inspections in product development and manufacturing. Periodic quality inspections play an important part in ensuring that items fit/satisfy that customer's needs.
Priced on per user or per location basis
Available on iOS, Android and Web
Understanding Quality Inspection
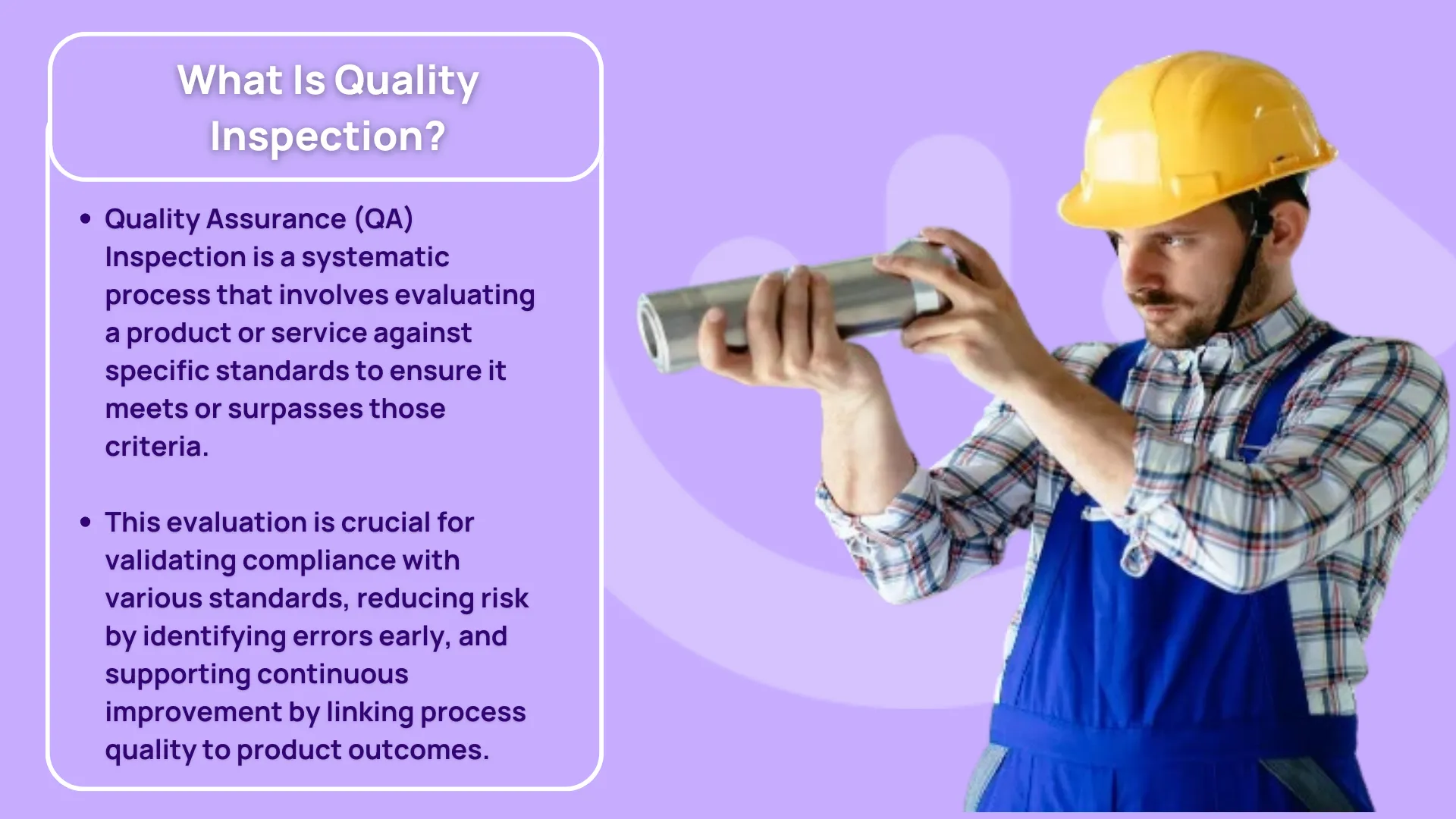
The definition of Quality Assurance (QA) Inspection differs based on the context or firm that employs it. In its most basic form, Quality Assurance Inspection is the meticulous examination, quantification, or evaluation of a product or service against a set of given standards or specifications to determine whether or not it meets or exceeds those standards.
The reasons for QA assessment are manifold.
- Primarily, it is intended to be a complete validation, verifying that the output meets specified requirements such as governmental, industrial, or internal standards.
- QA evaluation decreases risk by discovering and correcting any errors before final modifications.
- Furthermore, QA inspections enhance the feature of continuous recovery by expanding the relationship between process and product quality.
In a quality setting, inspection is more than visually examining the products. It is a systematic, technician-level evaluation of a condition, material, process, or product against set standards to ensure compliance with the given criteria. This quality inspection report could involve visual examination, measurement and testing equipment, reference standards, or input data, as well as expressed or measurable approval or rejection criteria, verbal hoods, evaluating questionnaires, and incident reporting.
Quality Assurance vs Quality Control
Quality assurance (QA) and quality control (QC) are essential for providing high-quality products and services. Although the two are similar in several ways, they differ in their goals, techniques, and methods of measurement.
QA takes a proactive approach, preventing issues before they grow. It entails the whole process, proactive planning, process optimization, and taking all specifications and designing initiatives to generate an end product that fulfills all of the standards.
On the other hand, Quality Control (QC) operates reactively and is effective when dealing with errors that have already occurred. It operates by inspecting, testing, and taking remedial action if a product or service fails to achieve the defined quality.
What is a Quality Inspector?
The key to the success of the inspection process is the role played by the quality inspector. A quality inspector is a seasoned professional with years of experience in the area and the knowledge to inspect with meticulous accuracy. A quality inspector understands the complexities of product specifications, required regulatory requirements, and industry standards, and uses his technical knowledge and analytical skills to scrutinize each significant operational parameter of the product or service, ensuring that the product or service meets all of the desired parameters.
What is a Quality Inspection?
Moving on, Quality inspection is the systematic and organized inspection approach used by the quality inspector of a product or service to confirm compliance with the quality standards or specifications. These criteria are often established for the fulfillment of consumer needs. It can occur at several phases of the manufacturing or service cycle, such as receiving, in-process, final, or shipping.
Sometimes it is extended to the "customer returns" stage. Checking and confirming the compliance of the products or services does not end here; it should be seen as a chance to enhance or keep such high-quality products by responsibility.
How to Conduct QA Inspection?
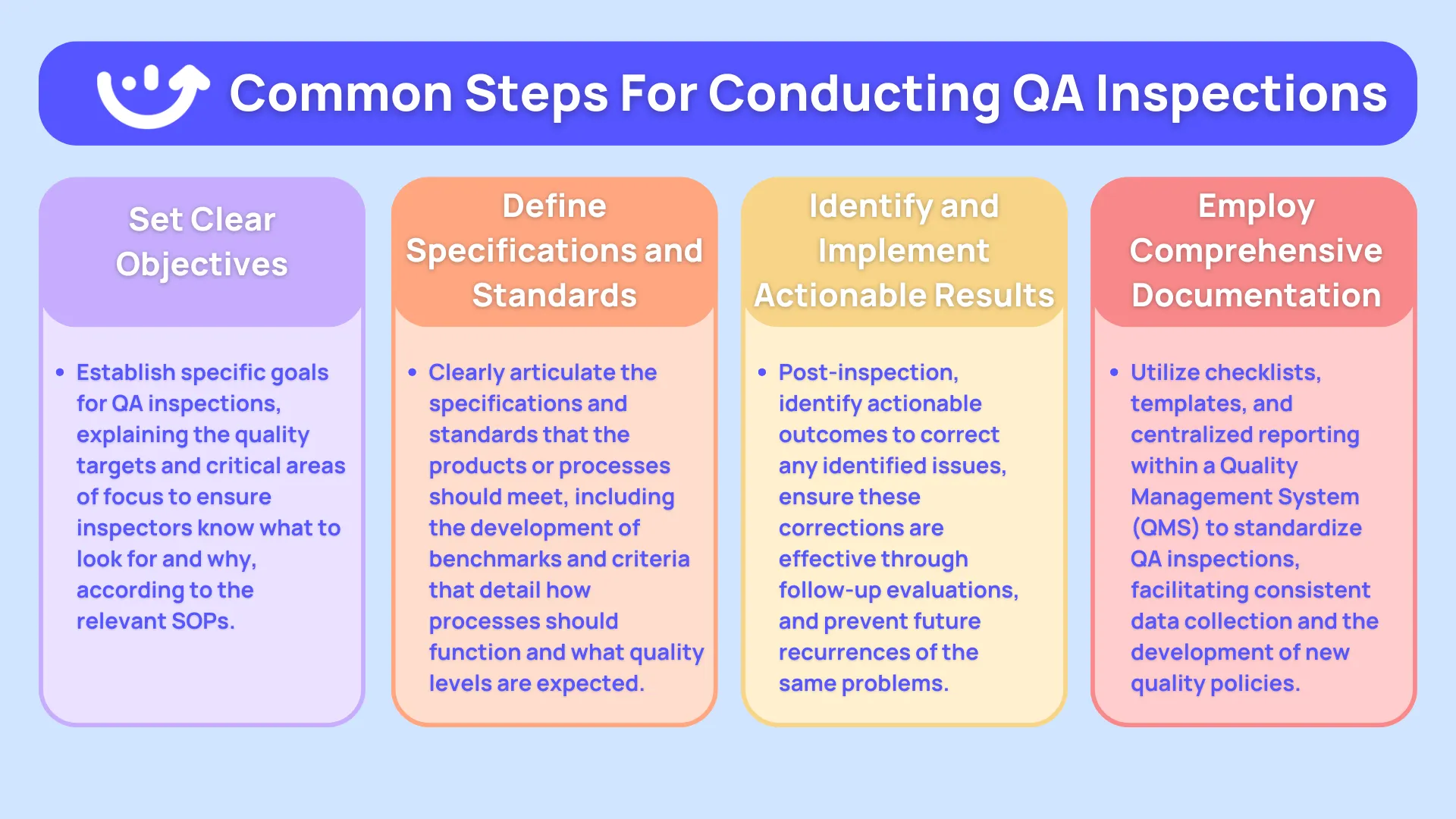
- State Clear Objectives
Setting specific objectives is the first step in QA inspections. Companies must explain what inspectors are looking for and why each inspection is being conducted in addition to which standard operating procedures (SOPs) apply to the processes under review. By following the route, Companies can subsequently focus on examining project-related challenges that will yield better results.
Clarity in objectives allows inspectors to verify that they are checking for the organization's quality goals and focusing on critical areas that contribute to the final product.
- State Specifications
Once the objectives have been set up, the next evident step in the process is to define the specifications. This stage of the procedure asks the following questions
- How will you quantify the things necessary to process better, quicker, or more?
- Which metrics will you use?
- What measurable benchmarks must be implemented for the best outcomes?
This phase frequently includes developing ideal benchmarks and criteria for quality and procedures, as well as picturing how the process should operate and the quality should be. The inspectors will then assess these ideal criteria against what they observed.
This approach ensures that the inspections are thorough, and quantifiable and can serve as a suitable foundation for subsequent product investigation.
- Determine Actionable Results
Moving forward with the inspection process, companies must be able to identify actionable outcomes. Meaning, that remedial efforts will be taken to ensure that this issue does not happen again in the future project. The capacity to evaluate the effectiveness of these remedial efforts. After a quality audit, a periodic follow-up is required to ensure that the desired objectives are achieved.
This strategy aims to learn from the causes of potential QA issues and ensure that they do not occur again in the future.
- Employ Documentation
Quality Management Systems (QMS) require checklists and templates for performing Quality Assurance Inspections. This helps inspectors to categorize their findings and provides a uniform approach. Centralizing all QA inspection reports and results improves the process even more. Businesses could acquire redundant data, increasing the time, effort, and expense. Documentation becomes the backbone of various new policies, ensuring that each inspection contributes to their implementation on a broader scale.
What are QA Inspection Tools?
Quality Assurance Inspection Software is a technology-driven solution that automates and streamlines an organization's quality assurance processes. It essentially provides a digital platform for automating, centralizing, and driving different product management activities, such as
- Inspection
- Planning
- Execution
- Reporting
- Analysis.
The QA inspection tools are intended to assist enterprises in eliminating wasteful inspection procedures that rely on paper, spreadsheets, and other forms of inflexible software.
The program is periodic, which implies that all data should be captured and processed regularly. The program is intended to be simple to use.
All checklists, questions, templates, and processes are customizable based on the user's profile type. All necessary data, including the actual answer to a checklist question, is only a few clicks away. The numerous reports provided, with inspection-level inquiries, can be performed at any time, by any authorized staff member, with no additional software.
By boosting your client retention rates by only 5%, you can boost your profitability by 25-95%.
Quality Assurance Inspection tools are critical since they ensure that the end products meet or surpass our client's expectations continuously. QA Inspection tools assist in boosting customer value by ensuring that defects are not passed on; keeping high-quality standards allows us to charge a little more for our products; and taking a proactive approach helps reduce customer unhappiness.
Furthermore, quality assurance inspection software frequently integrates ERP or QMS, to facilitate data flow and departmental cooperation. The substantial analytics and reporting tools also provide enterprises with the ability to extract meaning from raw inspection data, allowing for better decision-making and continual improvement.
Quality Assurance in Different Industries
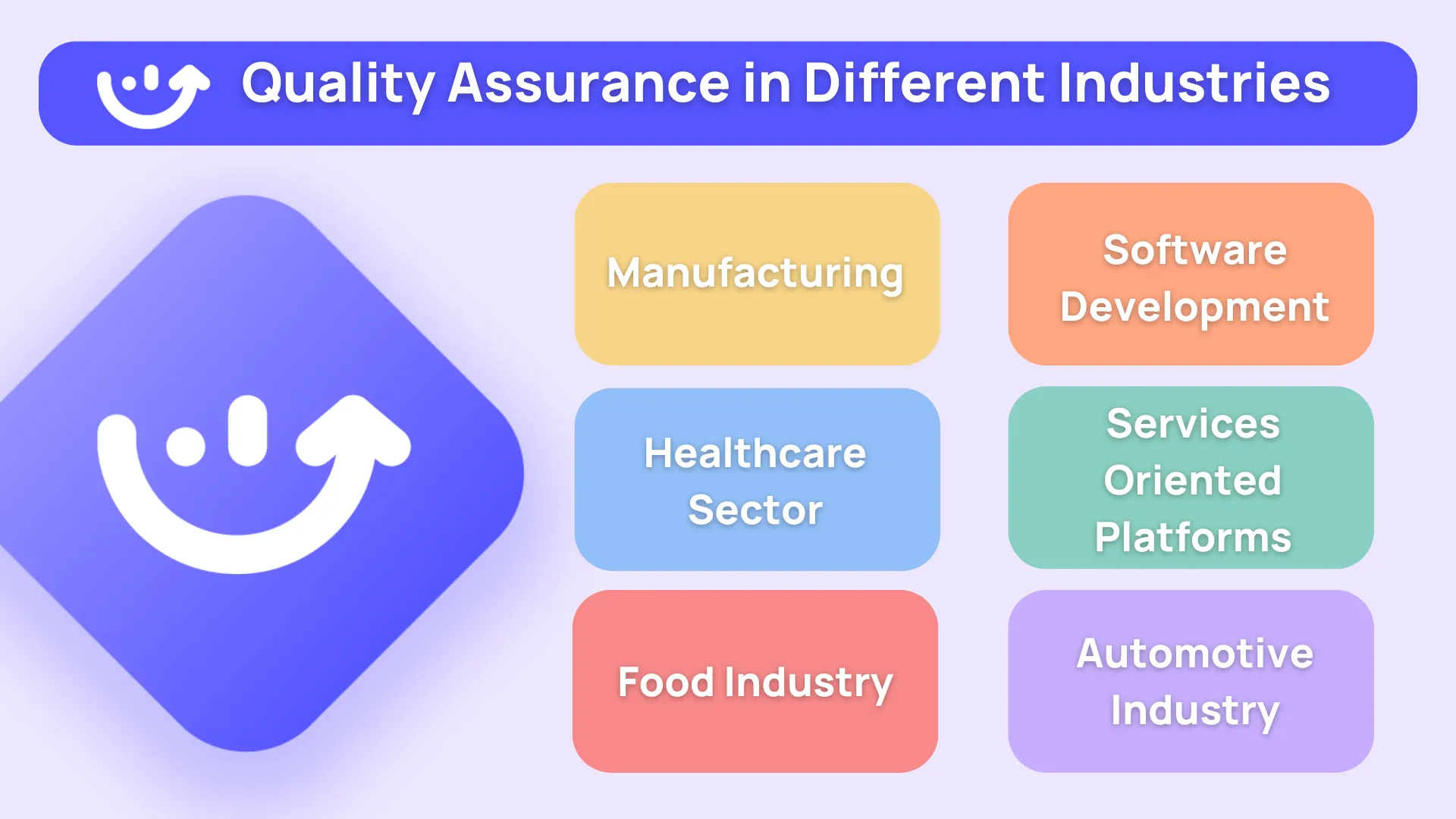
Inspections, as previously indicated, are intended to prevent errors from occurring in the first place. This notion helps companies to provide exceptional quality in the end products, assuring the clients' satisfaction, and allows the firm to comply with all regulatory criteria.
- Quality Assurance in Food Industry
Quality Assurance (QA) inspections tools play an important role in the food business; its goals and objectives include monitoring and maintaining safety and quality in food production processes. QA inspection in food manufacturing takes time, with inspections taking place at every level, from raw material procurement to production procedures to the finished product.
Quality Inspectors, for example, use spectrophotometers to ensure that the color of food products is consistent, and sensors to monitor both temperature and pressure during the process. These inspections were designed to identify and eliminate potential contaminants, ensure ingredient proportioning, and comply with food safety standards.
- Quality Assurance in Auto-Mobile Industry
Quality assurance (QA) is of the highest importance for the automotive industry for obvious reasons: lives are at stake when you slip up. Think of QA as a subset of the larger management strength of a company and then apply it directly to the product.
In automotive manufacturing today, having a strong management team that employs properly trained staff, tech, and tools is a must. So right off the bat, you can see how a specific product you might make needs thorough QA.
Since the quality of the car equals the safety of the occupants, the product's quality cannot be compromised. You don’t want to say "Well, I didn't think it would fall apart like that."
- Quality Assurance in Electronics
Quality assurance (QA) inspection tools in electronics manufacturing focus on functionality and integrity. In an industry where accuracy, precision, and dependability are crucial, functional tests are carried out in which equipment evaluates the performance of electronic devices following predetermined standards. These functional tests are typically carried out by automated test equipment (ATE).
Additionally, thermal cameras may be applied to evaluate whether a product may overheat. In addition to this, hardness testers are frequently used to examine the hardness of different materials found in electrical components. In industries like this, it is vital that every product adopts a QA-wise approach and that strict standards are adhered to.
Challenges in QA Inspection and Quality Inspection Report
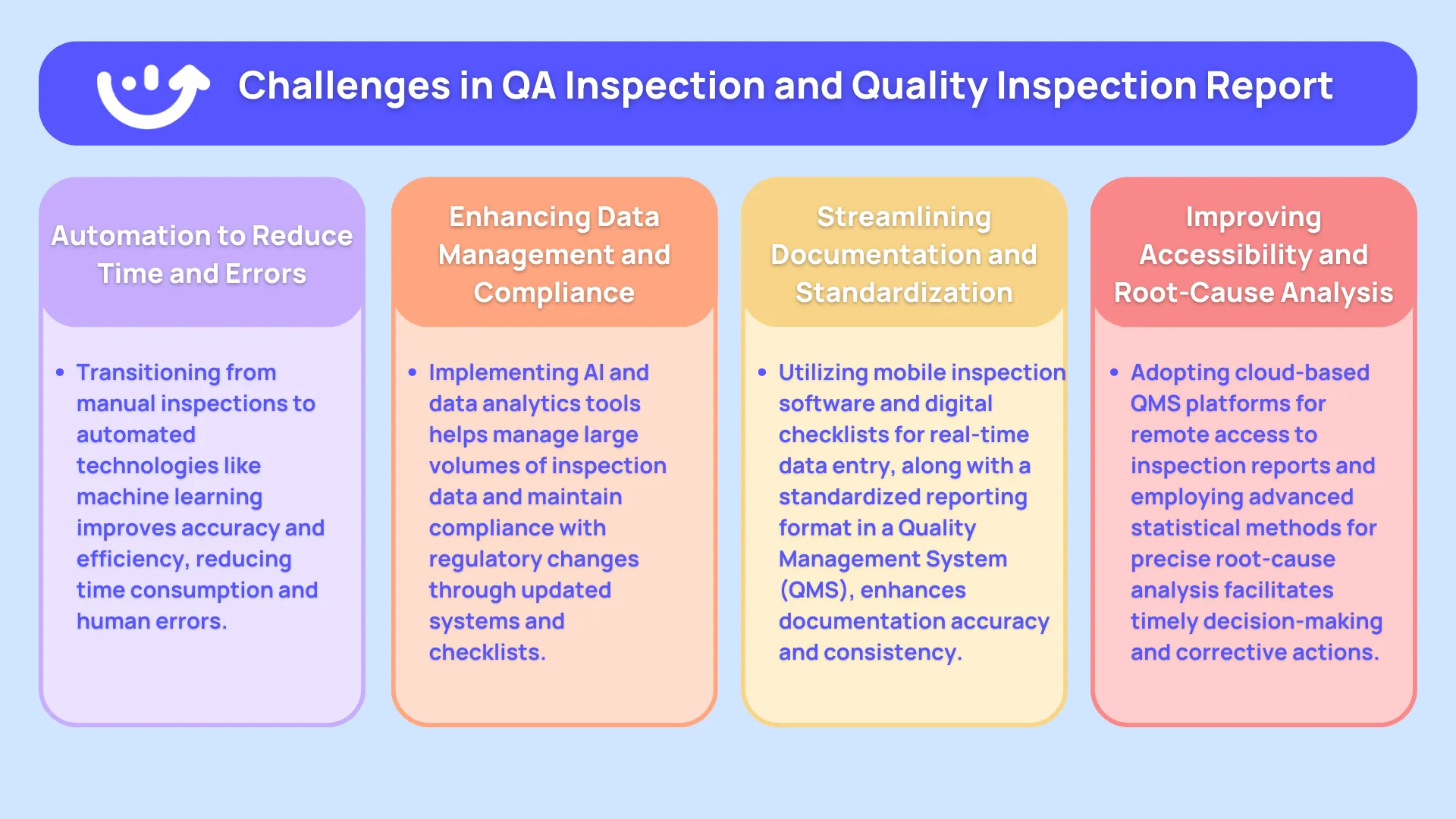
- Time-Consuming Process
Traditionally, inspection operations are carried out manually. These manual methods are frequently time-consuming, error-prone, and could lack consistency.
Adopting automated inspection technologies like machine learning may significantly minimize manual involvement, enhancing inspection accuracy while also simplifying the whole inspection process.
- Data Overloading
A substantial quantity of inspection data can be difficult to analyze and manage, resulting in significant delays and information overload.
The use of data analytics tools combined with artificial intelligence algorithms enables effective data processing, trend analysis, and pattern detection, resulting in faster and more informed decision-making.
- Adherence to Compliance
Being able to remain compliant during inspections is one of the challenges in keeping up with changing regulatory requirements. Implementing regulatory intelligence tools would be a promising alternative for improving inspection quality and ability.
Using a mainframe system, all of your inspection methods and checklists would be maintained up to date when rules change, ensuring that they're accurate.
- Supply Chain Variability
The supply chain has varied inputs, which could hinder inspection consistency: changing suppliers or raw materials might change the inputs, resulting in different outputs.
One approach would be to implement highly good supplier relationship management (SRM) and other communication tools offered by quality inspection software that enable early warnings and reactions to supply chain changes.
- Inefficient Documentation of QA Inspection Reports
Inaccurate documentation of inspection data might impede traceability and make it harder to identify the fundamental causes of faults.
The adoption of mobile inspection software and digital checklists, which allow quality inspectors to enter data in real time and reduce the chance of documentation mistakes, is one solution worth considering.
- Lack of Standardization
Another hurdle that demands great innovation relates to the lack of standardization in quality inspection report data. For instance, inaccurate inspection data visualization causes inconsistency and a lack of perspective in comparison.
The solution to this challenge is a simple, yet advanced method.
- First, provide a QMS with standard templates and a standardized report format.
- Then, require each inspection to use your QMS.
The advantages are two-fold because there is a uniformity of report; inspections perform a more comprehensive analysis and can trend data because they have awareness.
- Limited Accessibility
The inability to access inspection results in real time might inhibit timely decision-making and corrective measures.
Remote access to inspection reports via cloud-based QMS platforms enables vital information to be accessed regardless of time or place, resulting in informed choices and actions taken at the appropriate time.
- Inaccurate Root-Cause Analysis
Inefficient approaches for root-cause analysis allow issues to recur.
The use of statistical methodologies inside the QMS will improve the efficiency of completing root cause analysis, allowing you to pinpoint the exact underlying problem that is causing harm.
QA Inspection Reports and Their Significance
Quality Assurance (QA) inspection reports are more than simply written documentation; they are precious keepsakes that help organizations maintain standards and improve the quality of their products.
- The main purpose of performing QA inspections is to build a list of each finding that was noticed during the evaluations. Each discrepancy is to be addressed as more findings mean that the contractor is building a system that does not meet the predetermined quality criteria.
- These quality inspection reports give a detailed record of an organization's commitment to quality standards and any regulatory issues that have been found, which is mandatory for any audits or certifications the company is trying to achieve.
- Quality Assurance (QA) inspection reports are an essential component of an informed decision-making process, allowing decision-makers to assess the present condition of the quality system and allocate facility resources to correctly rectify the problems.
How to Effectively Utilize QA Inspection Reports?
- Perform a thorough review of the quality inspection reports immediately after the inspections. This review is crucial for finding any serious shortcomings that must be addressed immediately.
- Root cause analysis should be performed on each inspection. Take the irregularities discovered during each inspection and look deep for the underlying cause and contributing reasons to faults, allowing suitable repair steps to be implemented.
- A weekly analysis of quality inspection reports during this phase of the project helps identify trends. Seeing what defects and deviations are written up helps quality inspectors to develop systemic changes, rather than one fix at a time based on deficiencies.
- Use inspection reports to communicate findings and discuss remedial measures. Ensure that all stakeholders are heading in the same direction in terms of quality goals.
- By integrating with QMS, the QA inspection data can be accessible anywhere at any time. This might feed the ongoing improvements mandate while also allowing for more detailed trending data and thorough analysis.
Wrapping it Up
Quality assurance inspections serve as a preventative precaution throughout the manufacturing process, checking products at various stages to ensure that there are no imperfections deviations, or other issues that might negatively impact the product's quality.
The impacts of quality assurance inspections go far beyond finding defects.
They help to establish a proactive quality culture, ensuring that issues are addressed before they become huge problems and contributing to the ongoing improvement of the quality system. Quality assurance activities also serve to maintain compliance with standards, and regulatory and customer requirements.
When every inspection is documented with a great deal of detail and covers every aspect of quality, the automated QA inspection reports will turn into a driving force for decision-making, which will help an organization by being able to help expose areas of improvements, become more efficient in the products that are being built, to be able to continue the delivery of products that will reach or exceed the customer's
The premise stays the same: the usage and efficacy of QA inspections will always be a cornerstone in maintaining a level of product quality that will assist the market and drive the business, regardless of the path pursued.
.webp)
%201%20(1).webp)