Without a preventive maintenance schedule, equipment health is ignored until it is too late.
Priced on per user or per location basis
Available on iOS, Android and Web
Trust Me, You Need a Preventive Maintenance Schedule
Let me paint a picture:
It’s the biggest revenue day of the year and the quarterly bottom line hangs in the balance. Marketing dollars have been spent wisely and you are expecting a huge turnout. Just before opening, you get a call on the phone. The HVAC system for the entire building has shut down unexpectedly and a technician can’t make it out for 2 days. Inside temperature is currently 87 degrees and the forecast says it will surpass 100 outside. You keep thinking of one word: disaster.
A few days later, you learn that lack of preventive maintenance led to overheating and an untimely system failure. The system is repaired, but the quarterly revenue targets are badly missed.
Businesses without a preventive maintenance schedule for each asset are much like people who refuse to go to the doctor until they are deathly ill. Lack of attention and data lead to increased risk of sudden, sometimes catastrophic failure. And unfortunately, the bill for saving a catastrophic failure is often multiples of what preventive check ups would have cost.
But it’s not only the tail end risk of failure to consider. Without proper care, both equipment and human bodies are less efficient and productive. This means every minute of reduced efficiency puts negative pressure on growth.
Recommended Resources:
- Preventive Maintenance Software
- Maintenance Management Software
- 8 Best Maintenance Work Order Software For Businesses in 2024
- 10 Best CMMS Software For Small Business In 2024
- 8 Best & Free Digital Inspection Software in 2024
- 7 Best Preventive Maintenance Software For Hotels To Streamline Operational Efficiency
The solution is simple and obvious: If you have assets, you must create and enforce a preventive maintenance schedule.
This article will show you three different ways of creating a preventive maintenance schedule at varying levels of cost, flexibility and difficulty. We provide the pros and cons, along with downloadable resources and tools to help you get started today. Let’s dive in.
.webp)
PM Schedule Level 1: Pen and Paper
The first and most “old school” solution for making a preventive maintenance schedule is to do it by hand with pen and paper. Although the least efficient and effective method, thousands of businesses rely on preventive maintenance binders and clipboards every day. To get a jump start, download our free work order form pdf.
How to Make a Pen and Paper Preventive Maintenance Schedule
- Create a list of all the assets that need to be maintained
- Create a preventive maintenance procedure checklist for each asset
- Print or write multiple copies and place them in a binder.
- Get a calendar and add dates for each asset to be worked on
- Post the calendar in a visible location and keep the binder nearby
- Train employees to check the schedule, retrieve the correct checklist from the binder, complete the preventive maintenance and return the completed checklist to a filing cabinet or binder storage system
Pros and Cons of using Pen and Paper for PMs
As with anything, pen and paper can solve the problem, but it is likely not the easiest way. Still, you may decide that this is the only way that you can get the job done.
Pros
- Easy for old school staff to understand
- Does not require tech or electronics
Cons
- Takes a lot of time
- Limited accessibility and accountability
- Limited ability to analyze results
- High risk of getting lost or damaged
- Does not prepare for future
If you want to take the pen and paper route, we highly recommend checking out our template library to fast track your creation of standardized maintenance procedures. They are free to download as PDFs and will get you up and running much faster. However, we recommend you read on before doing so.
PM Schedule Level 2: Microsoft Excel / Google Sheets
Spreadsheets are useful whether you love them or hate them. For making a preventive maintenance schedule tool, they are a solid option when built the right way. The “right way” is the key phrase here and can be hard to achieve. That’s why we built you a system that you can copy for free using the links below.
There are two parts: the preventive maintenance calendar and the work order log & inventory list. Pull up them both in a separate window and read on to learn how to use them (Or read ahead and see why a CMMS may be a better solution for you)
How to Use Xenia’s Free Preventive Maintenance Calendar
How to use:
- Save a Copy by navigating to File Menu → Make a Copy
- In Settings: Add your Status Options, Work Orders and Staff Members
- In PM Planner: Schedule work orders with drop down menus
- In Calendar: View all planned PM Activity
How to Use Xenia’s Free Work Order Log & Inventory List
Before Using:
- Download Copy to be able to edit: File→ Make a Copy
- Copy Document must have Apps Script File “Log Work Order” attached
- The first time “Submit to Log” button is clicked, you will need to provide Authorization for it to work.
- Authorization Required → Continue → Sign In
- “Google hasn’t verified this app” → Advanced → Go to Log Work Order (unsafe) → Allow
To Use:
Step 1: In Settings input your Asset Locations, Team Members and PM Procedures.
Step 2: In Inventory List add each asset in your property along with relevant information such as ID #, cost, location, as well as a list of parts that need preventive maintenance attention.
Step 3: In Work Order Entry tab
- Input date of Work Order
- Select the Asset, Location and Team Member from drop down
- Input Asset ID
- Note: Parts Column will auto-populate from Inventory List. Do not manually add parts to the Work Order Entry.
- Select Procedure for each Part from drop down
- If applicable, input Cost, Invoice Number and Comments
- Once complete, press “Submit to Log” Button
- This will send all Work Order Entry data to Work Order Log for safe storage
- Work Order Entry can now be reused for another work order
Pros and Cons of Using Excel or Google Sheets for PMs
Pros
- Free Forever
- Fast to get started
- Digitizes PM maintenance record
- Allows digital PM schedules
- Sharable and printable
Cons
- Requires basic excel knowledge
- Cannot set recurring tasks
- Difficult to use on mobile
- It is possible to accidentally break built in functionality
- Cannot assign PMs as tasks
- Limited data collection granularity
PM Schedule Level 3: Computerized Maintenance Management System
A Computerized Maintenance Management System or CMMS, is a software solution to manage maintenance processes including work orders, preventive maintenance, inspections, audits and more. These solutions work on both desktop and mobile to help teams optimize their processes.
Core Features of a CMMS
Work Order Management
The core of a CMMS is the work order tracking system. This allows facilities to eliminate pen and paper, and instead streamline assignment, progress tracking and record retention in a cloud-based digital system.
Preventive Maintenance Schedules
The CMMS schedules and tracks preventive maintenance on assets in the property and provides easy access to tools such as checklists and logs to standardize procedures and ensure proper standards are upheld.
Safety and Quality Inspections
A CMMS enables inspections with detailed lists with rich data such as images and notes tied to each step. This data is crucial for ticketing new work orders to make necessary corrections, which can all be tracked and measured in the CMMS.
Inventory & Meter Logs
Many CMMS solutions offer Asset Management modules with parts inventory tracking. These tools centralize all asset information to better understand the costs and advantages associated with asset upkeep.
Xenia is a Light-Weight CMMS for Deskless Teams
Xenia is a light-weight CMMS, built specifically for ease of use on the frontline. The platform provides the essential functions such as work orders, PM calendars, inspections, checklists and logs in a format that can be understood and implemented on day 1. Xenia puts aside complex data models and internet of things monitors to bring you the core functionality at a much lower price point than other CMMS solutions.
Xenia is great for hospitality, property managers, and construction teams because the platform combines CMMS tools with operations, communication and quality management workflows. With Xenia, managers can unify their facilities and frontline data streams to improve efficiency and drive company wide technology adoption.
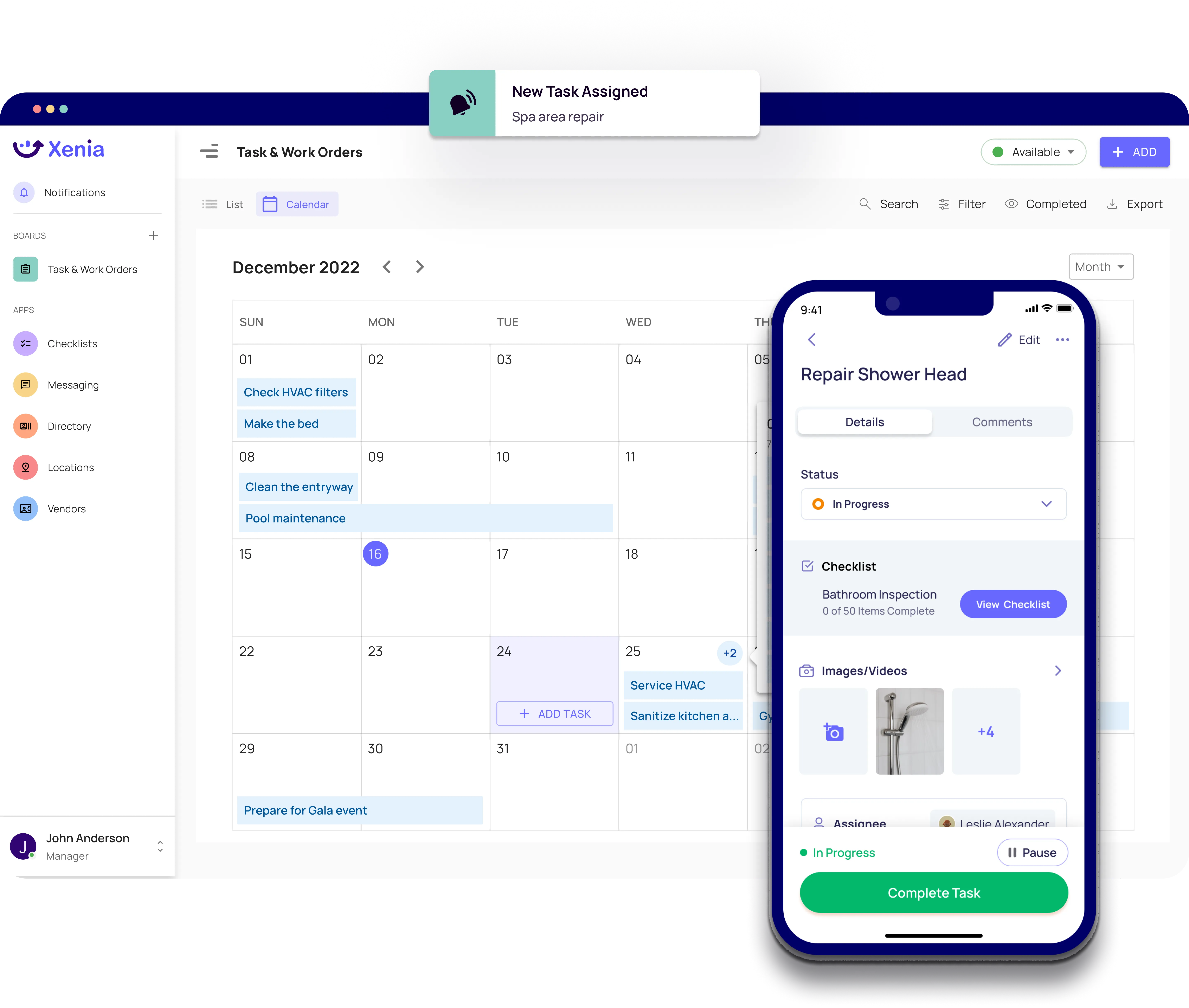
.webp)
%201%20(1).webp)