Facility management is a complex and critical aspect of running a large building. From ensuring the safety of occupants to maintaining the overall facility condition, it requires a great deal of attention to detail and constant vigilance.
However, with the fast-paced nature of the industry and the endless list of responsibilities, it can be all too easy for inspections to fall by the wayside and become deferred. But what exactly is a deferred inspection and why should facility managers be concerned about it?
Priced on per user or per location basis
Available on iOS, Android and Web
Deferred inspection is a term used to describe the act of delaying or postponing regular inspections of a facility. Whether due to resource constraints, inadequate planning, or poor communication, deferring inspections can have serious consequences.
But there's good news! With the advent of digital tools, facility managers now have the ability to prevent deferred inspection and minimize its risks and consequences. From inspection management software and digital checklists to operational analytics, these tools can help improve accuracy, increase efficiency, reduce costs, and ensure compliance. By implementing these tools and integrating them with existing inspection processes, facility managers can identify and address issues in a timely manner and keep their facilities running smoothly.
.webp)
Are you tired of constantly dealing with deferred inspections and the risks and consequences they bring? Do you want to take control of your facility's maintenance and prevent potential safety hazards, legal liabilities, and loss of revenue? Then keep reading and learn about Xenia, the inspection management software that can revolutionize the way you manage your inspection process.
What is a Deferred Inspection?
Have you ever put something off until later, only to realize later on that it would have been much easier to handle sooner? Well, that's exactly what deferring an inspection means. It's like pushing your responsibilities to the back burner and hoping that everything will be okay.
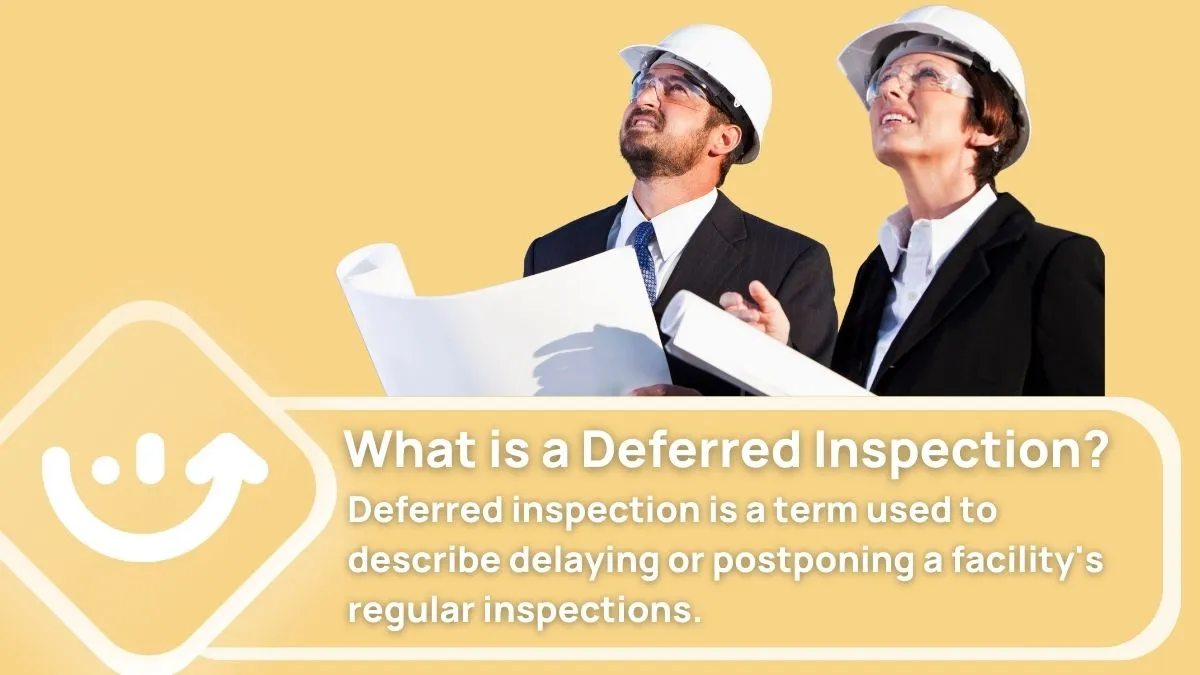
However, in facility management, this practice is a direct indicator of the condition of certain facilities. When inspections are postponed or delayed, facility managers may not be able to maintain the safety, functionality, and compliance of their facility.
Deferred maintenance then creates a backlog of repair and maintenance tasks that need to be completed at some point in the future. As maintenance tasks are postponed or rescheduled due to limited resources, the backlog grows longer and longer. This backlog can be thought of as a "to-do" list for facility management, with work staying on there until it is completed. The longer the backlog, the more work that needs to be done, and the greater the potential risks and consequences.
The backlog of deferred inspection maintenance can have a significant impact on the facility's overall health and safety, as well as its financial and operational performance. For example, if the backlog includes critical repairs to building systems such as electrical, plumbing, or HVAC, the facility may be at risk of system failures, leading to potential safety hazards, disruption to operations, and even costly damage.
To avoid these risks and consequences, facility managers must prioritize and address the backlog of deferred maintenance in a timely and effective manner. This means developing a comprehensive plan for tackling the backlog, allocating the necessary resources and budget to complete the work, and monitoring progress to ensure that tasks are completed on schedule.
Facility managers should be aware of the risks and consequences of a deferred inspection backlog and take steps to prevent it. So, let’s dive into the dangers of deferring inspections.
The Dangers of a Deferred Inspection
Failure to conduct regular inspections can result in various risks and consequences that can significantly impact the facility's overall health and operations. Here are some of the significant dangers that deferred inspections can pose for facilities:
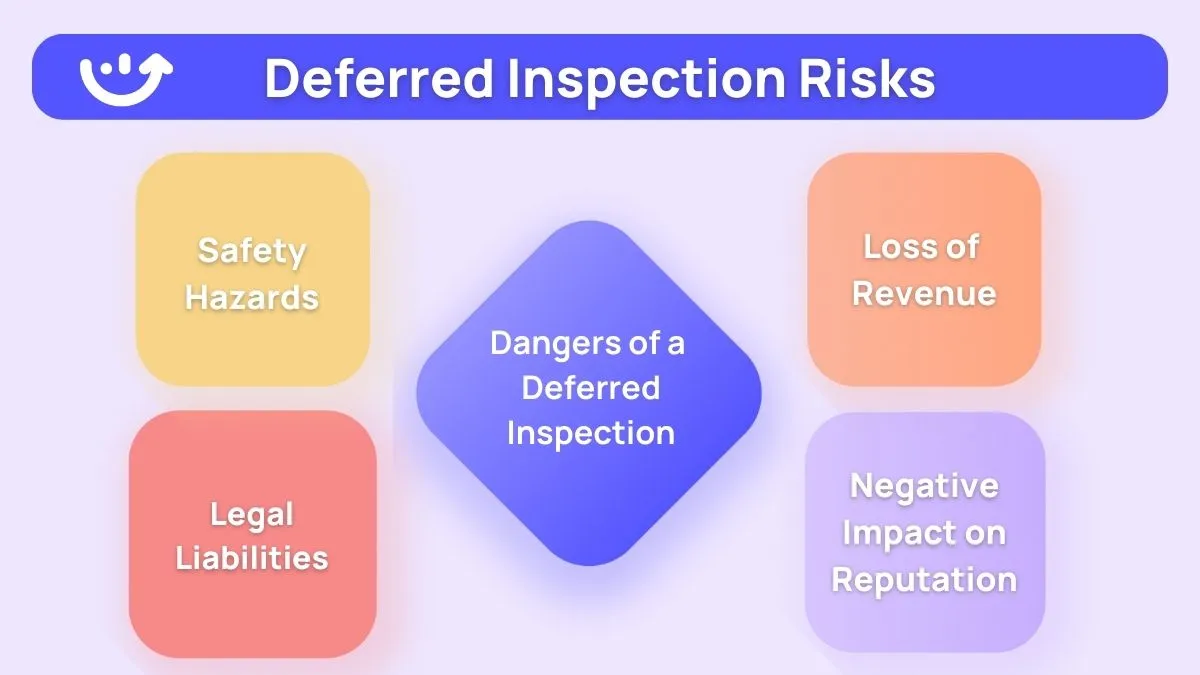
- Safety hazards: Deferred inspections can lead to potential safety hazards for occupants, guests, and employees. For example, if a fire alarm system is not inspected regularly, it may not work correctly in case of a fire emergency, putting lives at risk. Similarly, deferred inspections of elevators, electrical systems, and plumbing can also result in potential safety hazards.
- Legal liabilities: Facilities can be held responsible for any harm or damage that occurs as a result of deferred inspection. For instance, if a guest is injured in a slip and fall accident due to deferred inspection of the flooring or staircases, the facility can be held liable for damages.
- Loss of revenue: Deferred inspection can lead to a loss of revenue for facilities. Necessary repairs or maintenance that could have been prevented with regular inspections may result in the facility needing to shut down temporarily. This can lead to a decrease in occupancy rates and customer satisfaction, resulting in a loss of revenue.
- Negative impact on reputation: A large backlog of deferred inspection maintenance can lead to decreased customer satisfaction, as occupants may be inconvenienced by broken or malfunctioning equipment or facilities. This can add to the loss of revenue as customers seek out alternative facilities that are well-maintained and safe.
Common Causes of Deferred Inspection
Deferred inspections are a common issue in facility management, and it can happen to any facility regardless of its size or type. According to a report by the National Institute of Building Sciences, deferred maintenance in the United States alone costs an estimated $4.5 billion annually. The report also indicates that many facilities are operating with a significant backlog of deferred maintenance tasks.
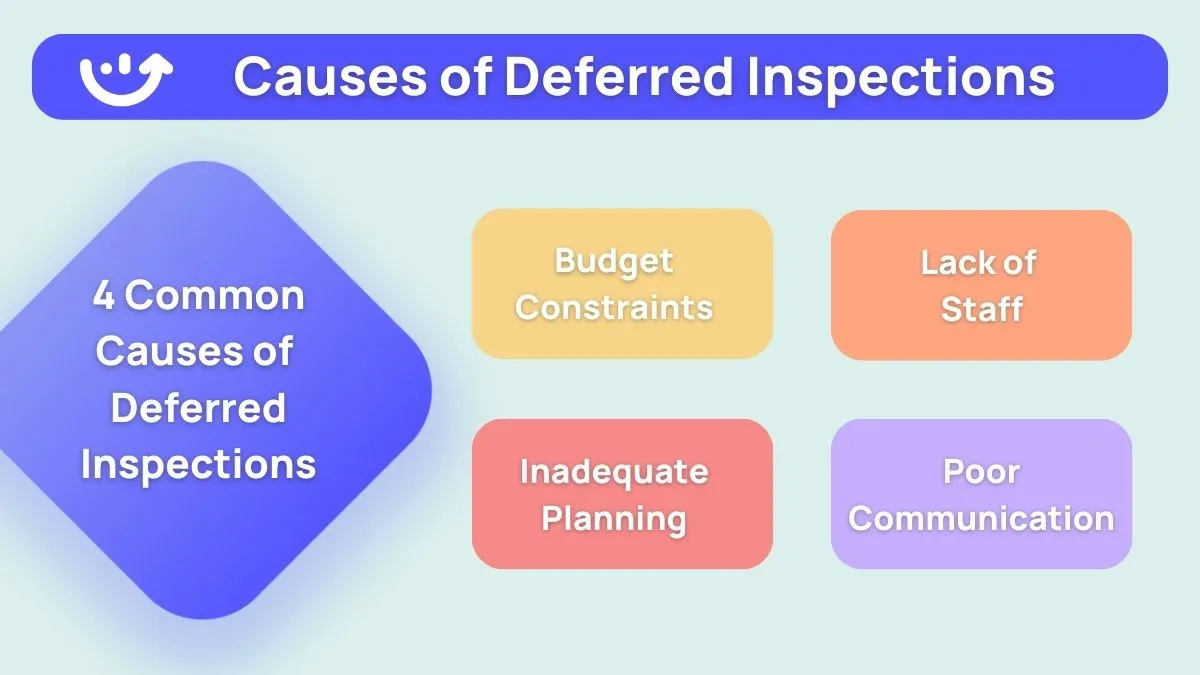
Facility managers may sometimes prioritize other aspects of the facility over inspections, such as day-to-day operations or revenue generation. As a result, inspection tasks may be deferred, leading to a backlog of maintenance tasks. Some facility managers may also mistakenly believe that their facility is in good shape and does not require frequent inspections. However, this can be a dangerous assumption, as even minor issues can quickly escalate and result in serious safety hazards or costly repairs. Moreover, unexpected events such as emergencies or staff turnover can disrupt inspection schedules, further contributing to the deferred inspection backlog.
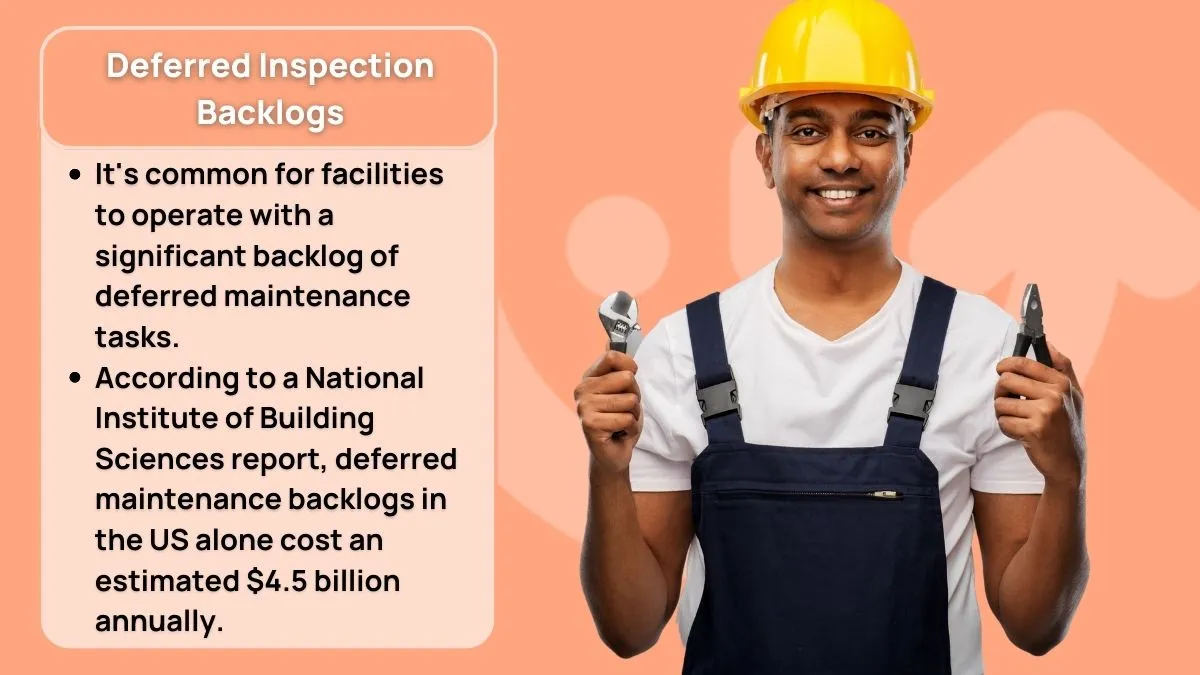
So, what are the common causes of deferred inspection? Here's a quick rundown of the top culprits:
- Budget constraints: When resources are tight, it's easy to put off inspections in order to save money. But this can be a dangerous gambit in the long run, as deferred inspection can lead to much more costly repairs down the line.
- Lack of staff: If you don't have enough people to perform regular inspections, it can be tempting to put them off until you have the manpower to get the job done.
- Inadequate planning: If you don't have a solid plan in place for your inspection schedule, it can be easy to let them fall by the wayside.
- Poor communication: Communication is key in facility management, and a breakdown in communication can easily lead to deferred inspection. Make sure everyone is on the same page and working together to ensure all inspections are performed on time.
Facility managers, take note! You're the ones on the front lines, responsible for ensuring that your facility is safe, compliant, and operating at peak efficiency. By understanding the common causes of deferred inspection and taking steps to prevent them, you'll be well on your way to a successful and stress-free inspection process.
Solutions to Deferred Inspection
By prioritizing inspections and maintenance tasks, facility managers can prevent issues from escalating and reduce the likelihood of deferred inspections. Implementing digital tools can also streamline the inspection process, increase accuracy, and reduce costs. With these solutions, facility managers can ensure that their facility is safe, functional, and compliant with regulations.
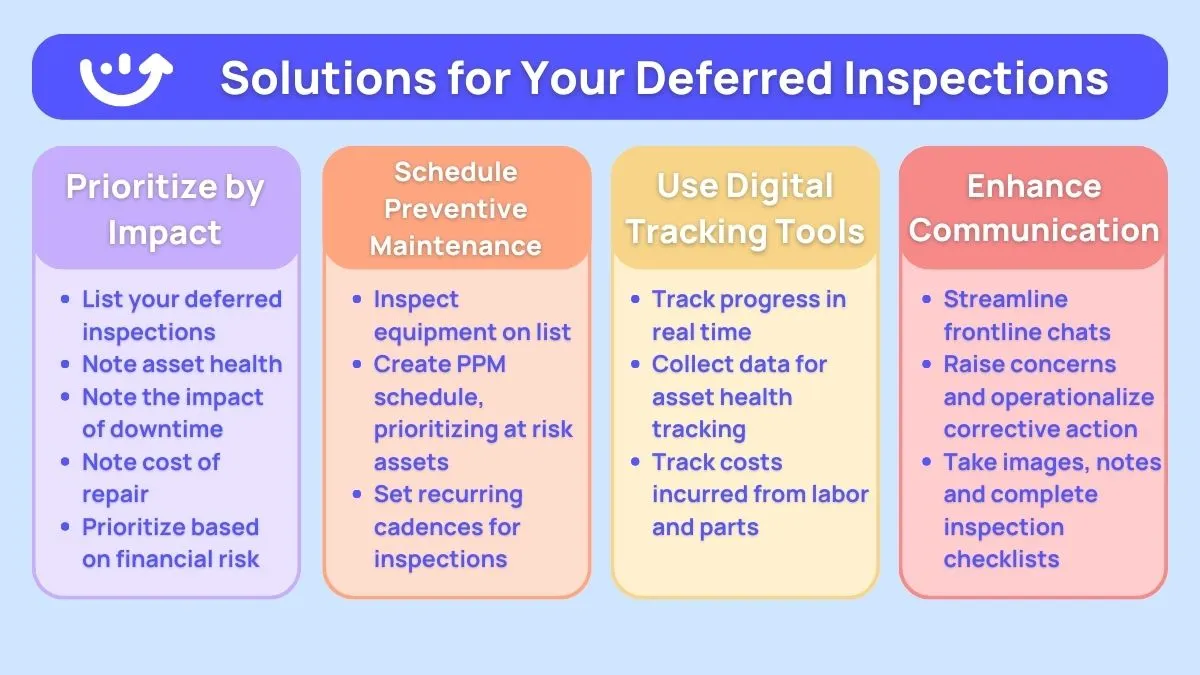
Digital tools for deferred inspection include inspection management software, mobile inspection apps, and digital checklists. Implementing these tools can also streamline the inspection process, increase accuracy, and reduce costs.
Effective communication is also essential in preventing deferred inspection, as staff must be aware of their role in the inspection process and the importance of inspections. By communicating effectively with staff and ensuring that everyone is on the same page, facility managers can prevent deferred inspection and minimize its risks and consequences.
Deferred inspection can be a major headache for facility managers, but it doesn't have to be. With the right tools and strategies in place, you can avoid deferred inspections and keep your facilities running smoothly.
Here are the top four ways to reduce your facility’s deferred inspection backlog.
- Regular Inspections: The key to preventing deferred inspection is to conduct regular inspections. By scheduling regular inspections, you can identify and address issues before they become major problems.
- Preventive Maintenance: Another solution to avoid a lengthy deferred inspection backlog is preventive maintenance. By performing regular maintenance on your assets, you can keep them in good working order and minimize the need for repairs.
- Use of Digital Tools: Digital tools can also be a powerful solution to deferred inspection. With inspection management software, mobile inspection apps, and digital checklists, you can streamline your inspection processes and ensure that nothing falls through the cracks.
- Effective Communication: Good communication is also essential in avoiding deferred inspection. By keeping all stakeholders informed and involved in the inspection process, you can ensure that everyone is on the same page and that issues are addressed quickly and efficiently.
By implementing these solutions, you can keep your facilities in top condition. Start taking control of your deferred inspections today and see the benefits for yourself!
Implementation of Digital Tools for Deferred Inspection
Implementing digital tools in facility management can be a game-changer when it comes to preventing deferred inspections. By utilizing software and technology, facility managers can streamline their inspection processes and stay on top of maintenance tasks in a proactive manner. This means that inspections can be conducted regularly and efficiently, minimizing the risk of deferring inspections and accumulating a backlog of tasks.
Here are a few tips to help you get started:
- Choose the right tools: There are many digital tools available for deferred inspection, including inspection management software, mobile inspection apps, and digital checklists. Choose the right tools that meet your specific needs and goals.
- Train your staff: Ensure that your staff is properly trained on how to use the digital tools effectively. This will help them complete inspections accurately and efficiently.
- Integrate with existing processes: Integrate the digital tools with your existing inspection processes to ensure seamless operation. This will make it easy for your staff to use the tools and for you to manage the inspection process.
- Make it a part of your routine: Make it a routine to use the digital tools for all inspections. This will help you maintain the accuracy and efficiency of your inspection process.
By following these tips, you can successfully implement digital tools for deferred inspection and minimize the risk of deferred inspection in your facility. Not only will you ensure the safety and compliance of your facility, but you'll also improve the overall efficiency of your inspection process.
.webp)
%201%20(1).webp)