Looking to streamline your maintenance work order system? We've got you covered.
From computerized maintenance management systems to mobile work order apps, we'll take a deep dive into each method and provide you with tips on how to get the most out of your maintenance work order system.
Priced on per user or per location basis
Available on iOS, Android and Web
It May Be Time to Rethink Maintenance Work Order Management
Collecting the right data on your assets is crucial, but enabling informed action is what protects your bottom line from the threat of unexpected equipment failure, increased downtime, and hidden maintenance costs.
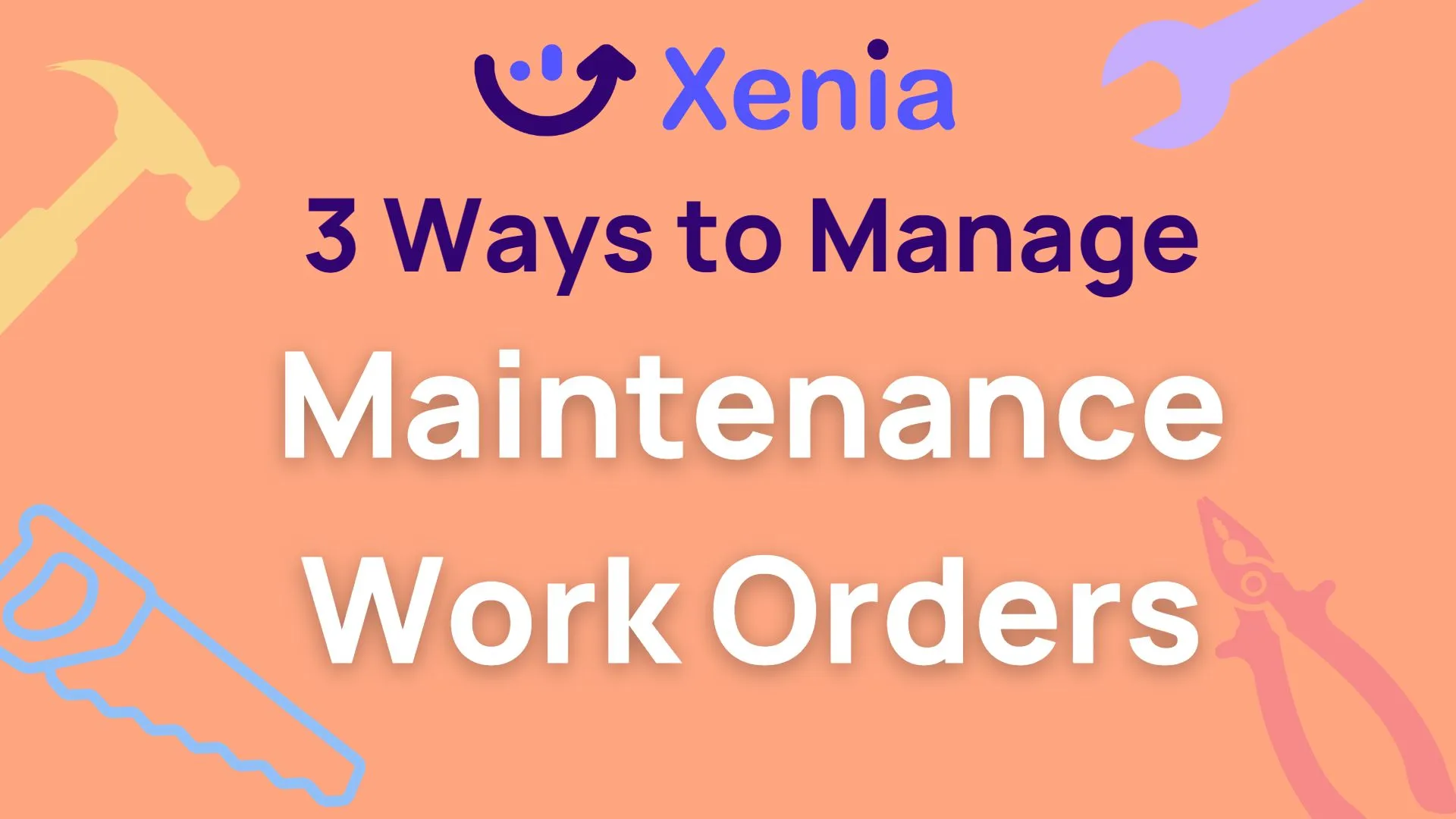
Can you answer these questions today?
- Do you know how many work orders have been completed in the last week, month or year?
- Has there been a measurable increase or decrease in work orders completed over time?
- Has the time spent per work order improved in the past year?
- Can you pull a health report of all the work done to every asset on your property?
- Who is your best employee for handling work orders? How do you know?
- If you had an additional $1,000 in your budget for maintenance, where should you spend it?
How long would it take to gather the answers?
The truth is that these questions are all answerable if you collect work order data.
But depending on how you collect, store and analyze that data, finding those answers could take anywhere from seconds to hours.
Do you have hours to spare to answer these questions? If the data is not available and actionable, are you not more likely to just go with your gut? Then why collect it in the first place?
What will you learn by reading this article?
This post will cover three different ways to structure maintenance work order management in your organization; pen and paper, Microsoft Excel / Google Sheets, and a work order management software. We will cover the pros and cons of each, providing free resources to power each solution.
In the end, the solution must fit the problem and we want you to make the best choice for your company. Regardless of what you choose, we hope that by reading this you will gain a new perspective on maintenance work order management. Ready? Let’s go.
The “Classic” Pen and Paper Maintenance Work Order
One of the oldest and most basic methods for managing maintenance work orders is to do so by hand with pen and paper. Although this is the least efficient and effective approach, thousands of businesses continue to rely on maintenance work order binders and clipboards every day.
For “old school” maintenance managers, this may be the only way to get any data on your maintenance. We want to help out, so download our free maintenance work order form below and follow along to learn how to use it.
How to Manage Maintenance Work Orders on Pen and Paper
- Create a work order template to use for every work order.
- Print or write multiple copies and place them in a binder.
- When an issue occurs, record known details on paper form
- Radio the technician to pick up the work order.
- Have technician record information on work order form.
- Ensure work order is collected and placed back in the appropriate binder or folder.
Pros and Cons of using Pen and Paper for Maintenance Work Orders
When it comes to work orders, pen and paper can provide simple, straightforward reporting to cover the basics of maintenance documentation. They are easy for everyone to understand and use no matter their technological literacy, but there are limitations to be aware of.
Pros
- Easy for old school staff to understand
- Does not require tech or electronics
Cons
- Very time inefficient way to collect data
- Uses large amounts of paper
- Limited ability to analyze results
- High risk of getting lost or damaged
- Limited accessibility and accountability
- Handwriting interpretation can cause confusion
- Does not prepare for the future
If you want to take the pen and paper route, we highly recommend checking out our template library to come away with more PDF downloads that can help standardize your operations. Pairing work order management with Preventive Maintenance Schedule will help prevent sudden, reactive work orders which will protect your bottom line. However, we recommend you read on before kicking off this process.
Microsoft Excel / Google Sheets for Work Order Management
Spreadsheets are useful whether you love them or hate them. For making a Maintenance Work Order tool, they are a solid option when built the right way. The “right way” is the key phrase here and can be hard to achieve. That’s why we built you a system that you can copy for free using the link below.
The sheet has two main parts: the maintenance work order log as well as the asset inventory list. Pull up them both in a separate window and read on to learn how to use them (Or read ahead and see why a CMMS may be a better solution for you)
How to Use Xenia’s Free Work Order Log & Inventory List
Before Using:
- Download Copy to be able to edit: File→ Make a Copy
- Copy Document must have Apps Script File “Log Work Order” attached
- The first time “Submit to Log” button is clicked, you will need to provide Authorization for it to work.
- Authorization Required → Continue → Sign In
- “Google hasn’t verified this app” → Advanced → Go to Log Work Order (unsafe) → Allow
How To Use:
Step 1: In Settings input your Asset Locations, Team Members and PM Procedures.
Step 2: In Inventory List add each asset in your property along with relevant information such as ID #, cost, location, as well as a list of parts that need preventive maintenance attention.
Step 3: In Work Order Entry tab
- Input date of Work Order
- Select the Asset, Location and Team Member from drop down
- Input Asset ID
- Note: Parts Column will auto-populate from Inventory List. Do not manually add parts to the Work Order Entry.
- Select Procedure for each Part from drop down
- If applicable, input Cost, Invoice Number and Comments
- Once complete, press “Submit to Log” Button
- This will send all Work Order Entry data to Work Order Log for safe storage
- Work Order Entry can now be reused for another work order
Pros and Cons of Using Excel or Google Sheets for Work Orders
Pros
- Free Forever
- Digitizes work order log
- Can customize procedures and costs
- Can create inventory list with parts
- Sharable and printable
Cons
- Requires excel knowledge
- Cannot assign work order to team members
- Limited data collection granularity
- Limited ability to customize reports
- Difficult to use on mobile
- Cannot attach standardized procedures or checklists to work orders
- It is possible to accidentally break built in functionality
Maintenance Work Order Management Software
Maintenance work order management software typically falls within the category of Computerized Maintenance Management Systems (CMMS). Work order management solutions provide next level accessibility and actionability compared to paper and excel. Watch to learn more.
6 Features that Differentiate Maintenance Work Order Solutions
Work Order Assignment
Assigning work orders using software takes seconds and can be intelligently distributed based on criteria such as category, location, priority level, start and due times. Work orders can be assigned as recurring tasks to enable quick preventive maintenance scheduling and regular safety inspections.
Attach Checklists, SOPs and Photos
With maintenance work order software, you can attach checklists and standard operating procedures to the assignment so that there is no confusion or miscommunication. Within the checklists, your frontline team member can attach detailed notes, meter readings and photos to ensure maximum data clarity.
Work Order Progress Tracking
Maintenance work order software enables managers to keep tight oversight of operations no matter where they are located. When work orders are assigned, the correct employee is notified via their mobile device. Once they start work, the manager can see the task as in progress.
The manager can monitor the checklist progress and view images from the frontline in real time. If there are questions, the employee can chat with team members or management within the work order itself, providing an unprecedented level of collaboration, detail and transparency.
Customizable Data Dashboards
Managers must have the ability to quickly and easily organize and customize their work order dashboards to be able to understand performance and uncover opportunities for improvement. A maintenance work order software should be able to sort and filter data based on priority, category, employee, location, status and date range. It should also be easy to hide columns of data to direct attention to the insightful data.
Easy Export to PDF and CSV
When you make a beautiful custom report, it is important to be able to share it with your team. A maintenance work order system should make exporting your data quick and easy. The two most effective formats for managers are PDF and CSV. A PDF makes it easy to email and print reports for meetings, while a CSV makes it easy to conduct detailed analysis such as totals, averages and outliers for specific cuts of the data.
Cloud Based Data Storage
Finally, it is essential for your maintenance work order software to store your data in the cloud, where it is safe and secure for future use and analysis. This is how you can power fast retrieval of information on both desktop and mobile to make real time decisions that move your business forward.
Xenia can do all that and more... Let’s see it in action!
Xenia is a light-weight CMMS, built specifically for ease of use on the frontline. The platform provides the essential functions such as work order management, preventive maintenance calendars, inspections, checklists and logs in a format that can be understood and implemented on day one.
.webp)
Xenia is great for hospitality, property managers, and construction teams because the platform combines CMMS tools with operations, communication and quality management workflows. With Xenia, managers can unify their facilities and frontline data streams to improve efficiency and drive company wide technology adoption.
.webp)
%201%20(1).webp)