Effective leadership is crucial for the success of any maintenance crew. A well-functioning maintenance crew will save your business time and money by increasing uptime and output. A study suggests that equipment downtime in the service industry can lead to lost revenue and customer dissatisfaction. Some estimates suggest that a single hour of downtime can cost a company up to $300,000.As a maintenance crew leader, you are responsible for overseeing your team's work and ensuring that tasks are completed efficiently, safely, and to the highest standards. A strong leader will help focus the team's efforts and improve morale.
Priced on per user or per location basis
Available on iOS, Android and Web
Leading a maintenance crew can be challenging, but you can effectively guide your team toward success with the right approach and strategies.
In this post, we will explore key strategies for effectively leading your maintenance crew, including setting clear goals and expectations, identifying and addressing inefficiencies, providing support and resources, and fostering a culture of teamwork and collaboration.
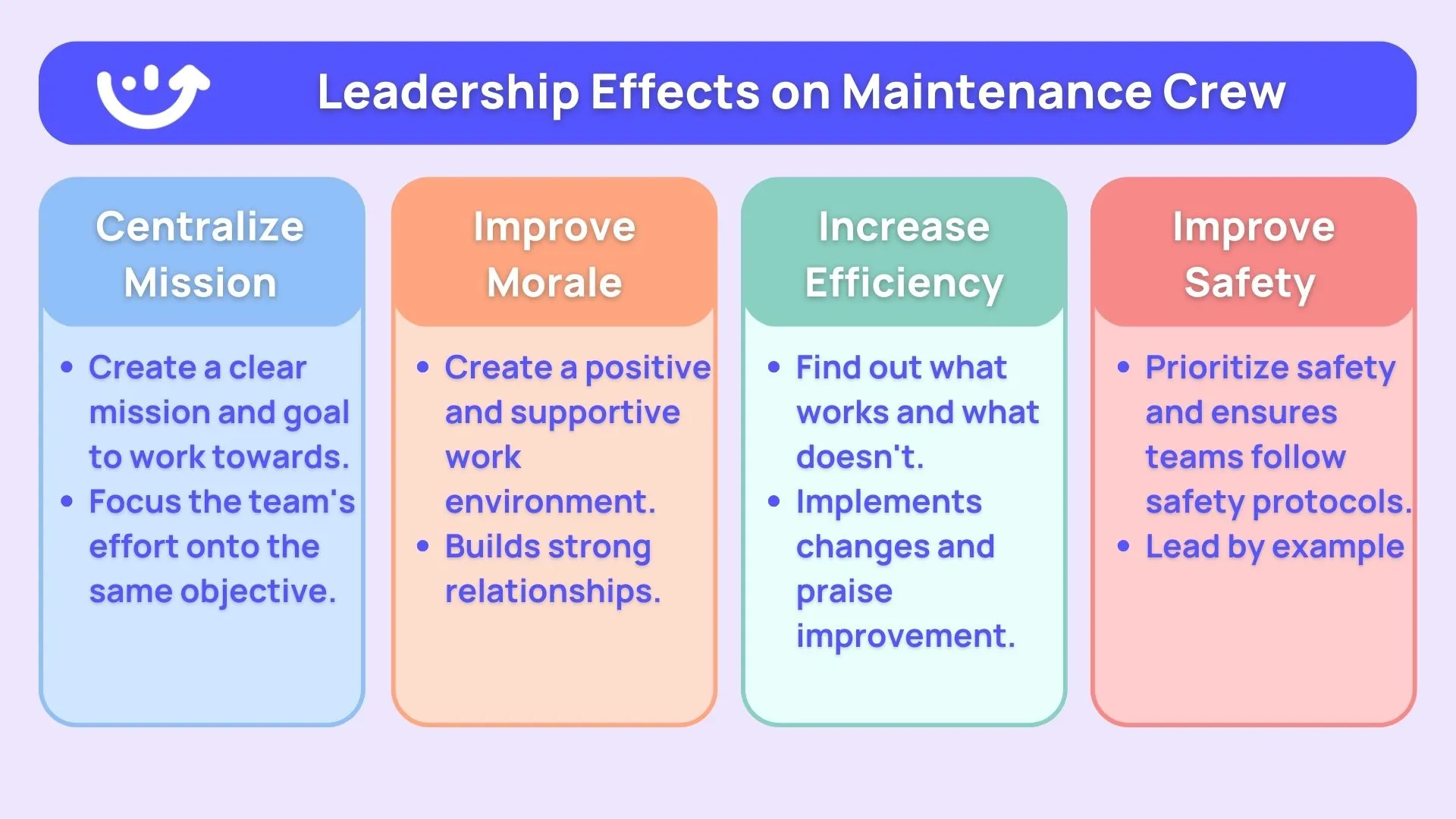
How to Lead a Maintenance Crew Effectively
A meta-analysis published in the Journal of Occupational and Organizational Psychology found that good leadership was associated with increased employee job satisfaction, engagement, and performance.
So, what makes good maintenance lead?
👷 Lead your maintenance crew by example
So, what does a good leader actually do? It’s simple, lead by example.
This can involve demonstrating good behavior, being a role model, and setting a positive and professional tone for the team. It may also include showing expertise in one's field, being reliable, and working hard to succeed.
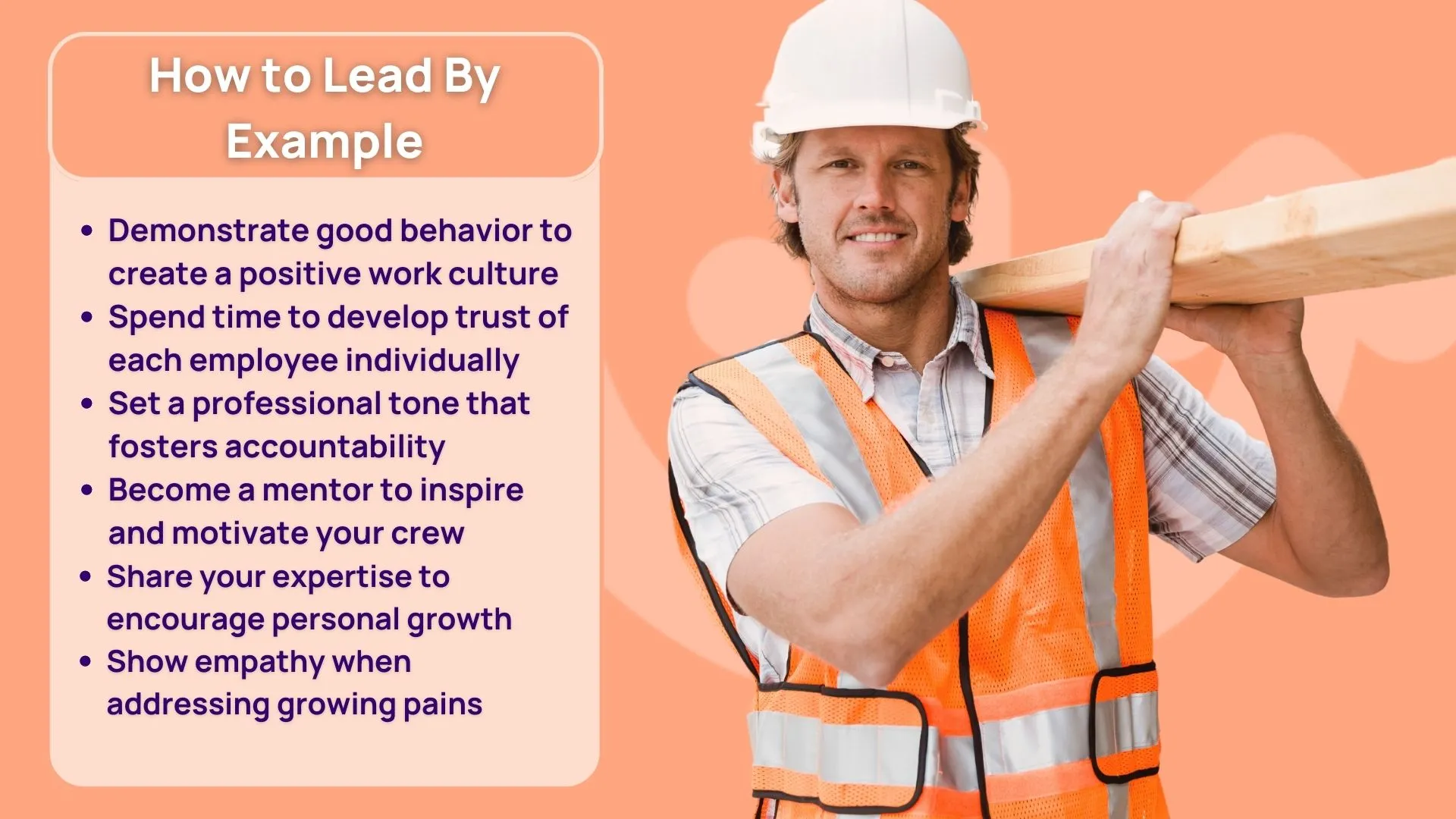
It is essential for management to “walk the talk” for several reasons, but here are the top four.
Demonstrate good behavior
Doing as you say helps establish trust and credibility within your team. When team members see that their leaders are willing to roll up their sleeves and work alongside them, it creates a sense of mutual respect and trust. It also helps to set a positive tone for the team, as team members are more likely to follow the lead of their leaders and adopt a similar work ethic.
Set a professional tone
Leading by example helps to foster a culture of accountability and responsibility within the team. When leaders take responsibility for their actions and hold themselves to high standards, it sets a precedent for team members to do the same.
Be a positive role model
Helps inspire and motivate team members. When team members see their leaders working hard and striving for success, it can encourage them to do the same. This can increase productivity and performance within the team and contribute to the organization's overall success.
Show expertise
Being knowledgeable about your field and being willing to share that knowledge with others. This can improve morale and encourage team members to look to the manager for guidance and support.
It’s your job as a leader to ensure that all team members have the necessary training and resources to perform their tasks effectively. This involves openly communicating team members' needs and offering collaboration.
🦺 Establish Clear Maintenance Procedures
Why are communication skills so critical for a maintenance manager?
A recent survey just found that 86% of respondents believe that workplace failures directly result from ineffective communication and a lack of collaboration.
Influential leaders communicate transparent processes, procedures, and expectations. These guidelines ensure that every job is performed consistently and efficiently.
Maintenance managers can simplify this process by establishing standard operating procedures (SOPs) and checklists. Then conduct inspections to ensure that tasks are being completed correctly and safely.
To simplify this process, it’s critical to implement strategies for tracking and documenting maintenance activities. This can involve using a computerized maintenance management system (CMMS) to schedule and assign tasks, track maintenance work progress, and generate performance reports and other metrics.
By tracking and documenting maintenance activities, leaders can monitor progress, identify any issues or bottlenecks, and make necessary adjustments.
📎Improve Decision Making Capabilities
Effective decision-making is crucial for leaders to guide and lead their team or organization toward success.
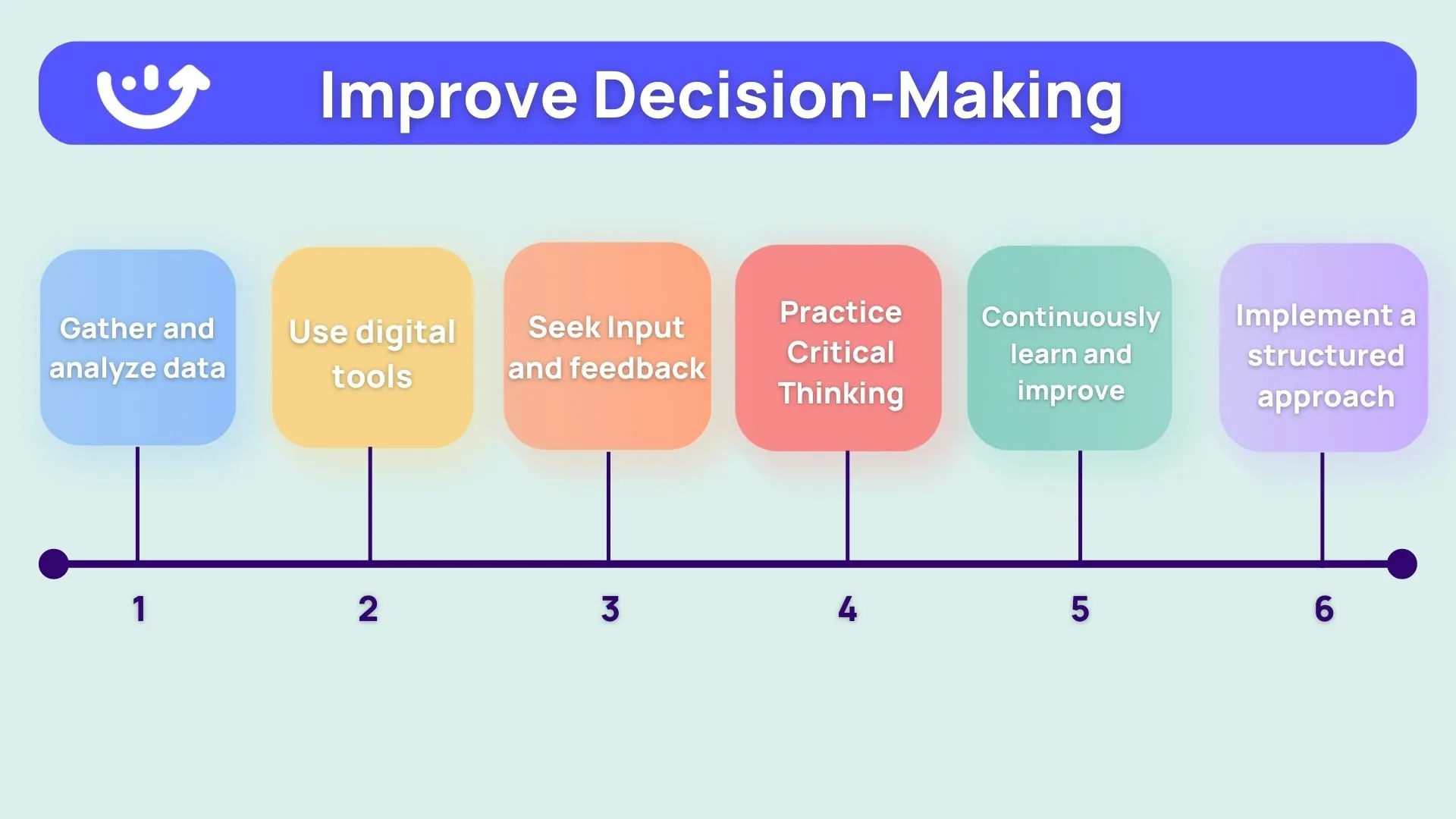
So, how can maintenance managers improve their decision-making?
Gather and analyze data
Use data and analytics to inform decision-making. This can involve collecting and analyzing data on equipment performance, maintenance costs, safety considerations, and production demands.
Use digital tools
Utilize tools and methods such as the DEMATEL method, Six Sigma, or lean practices to structure the decision-making process and identify the most critical factors to consider.
Seek input and feedback
Consider seeking input and feedback from others, such as team members or subject matter experts, to gain a broader perspective on the issue.
Practice critical thinking
Use critical thinking skills to evaluate options carefully and make informed decisions. This can involve asking questions, considering multiple viewpoints, and analyzing different options' potential risks and benefits.
Continuously learn and improve
Stay current on best practices and new developments in the field, and be open to learning from past mistakes and continually improving decision-making skills.
Utilize a structured approach
Follow a structured approach to decision-making, such as the problem-solving process or decision tree analysis, to ensure that all relevant factors are considered, and a logical decision is made.
🖼️ Provide Frameworks for Improvement
There are several ways that good management can provide frameworks for improvement.
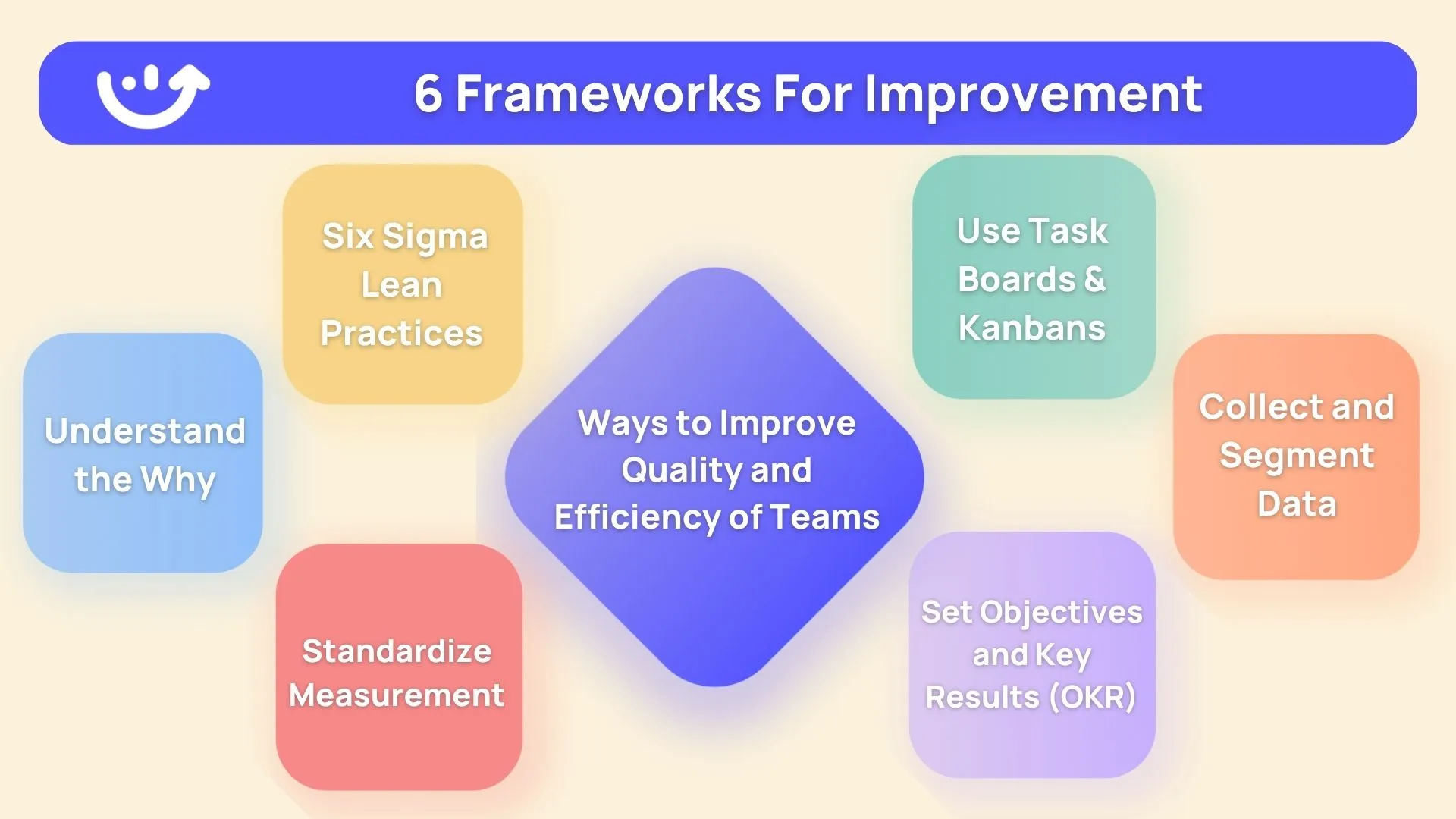
Adopt Six Sigma or Lean Practices
The structured methodologies for identifying and eliminating waste and improving efficiency. These practices often involve standardizing processes and implementing tools like Gemba Walks or the 5 S Framework.
Use task boards, kanbans, and calendars
Help organize and track work activities. These tools can standardize work processes and improve work prioritization, reducing errors and improving efficiency.
Objectives and Key Results (OKR)
Set clear, measurable goals and track progress toward achieving those goals. By setting clear objectives and regularly measuring progress, managers can help drive continuous improvement and ensure that their teams are aligned with the organization's overall goals.
Standardize measurement
Ensure that you track the right metrics and have a clear and consistent way of measuring progress toward their goals.
Segment
Segmenting maintenance tasks by team, individual, and asset type can improve efficiency and effectiveness by ensuring that the right resources are applied to the right jobs.
🚀 Providing Ongoing Support and Development
Providing ongoing support and development is essential for the success of any organization. It helps to improve employee satisfaction and retention, drives performance and efficiency, and fosters a culture of continuous learning and improvement.
When team members have the knowledge and skills to do their jobs effectively, they are more likely to be productive and contribute to the organization's success. This can help to drive business growth and increase profits.
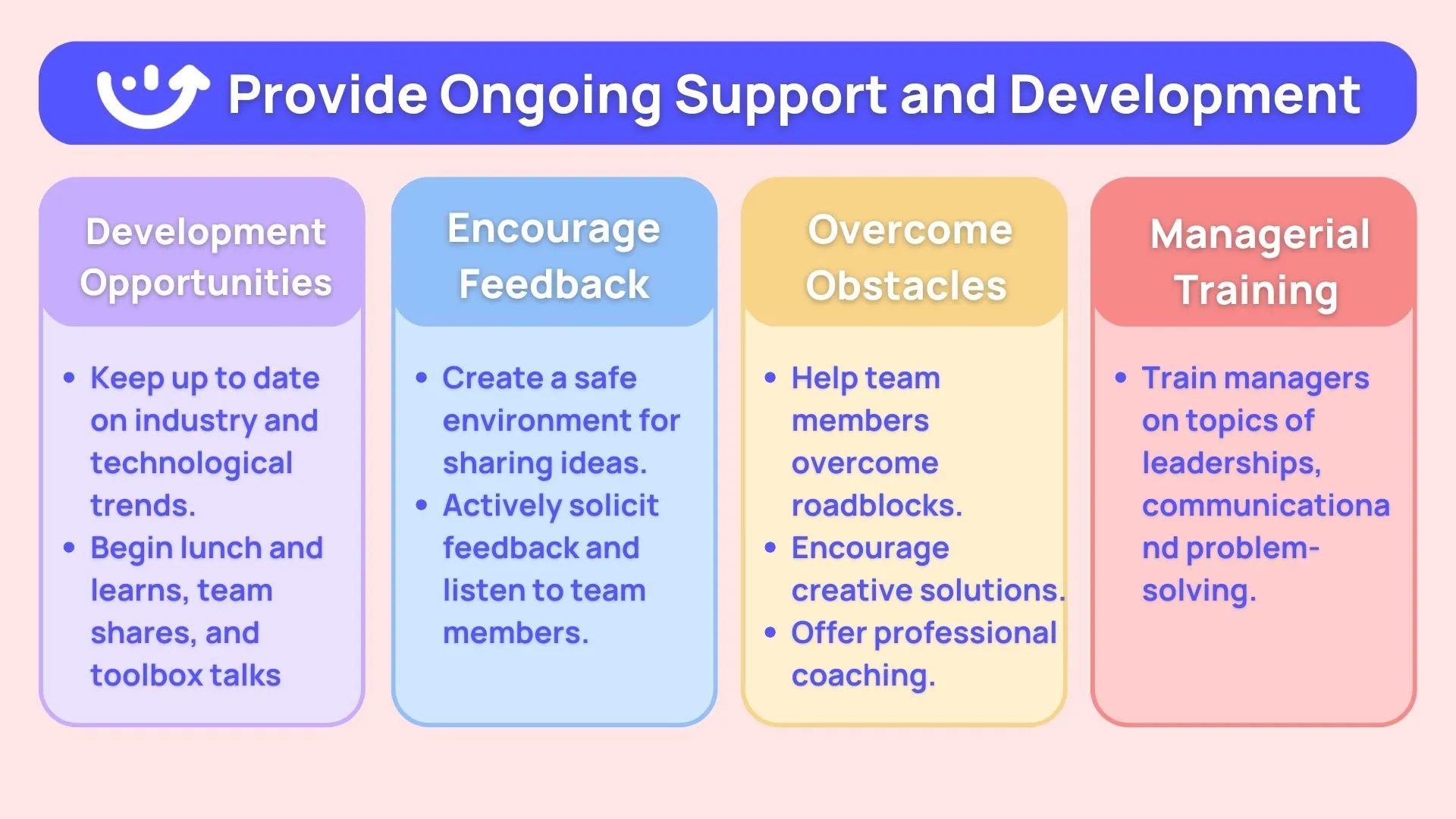
Here are four tips to encourage your maintenance crew to learn and grow:
Offer development opportunities
This can include things like lunch and learns or team shares, where team members can learn new skills and stay updated on industry trends.
Encourage open communication and feedback
Create a safe and supportive environment where team members feel comfortable sharing their ideas and concerns. Actively solicit feedback and listen to team members.
Support team members and help them overcome challenges
Provide resources and support to help team members tackle complex tasks or overcome roadblocks. Offer guidance and coaching to help team members develop their skills and grow as professionals.
Invest in managerial training
Training managers on leadership, communication, and problem-solving topics can help them be more effective leaders and support their teams more effectively.
Benefits and Characteristics of High Performing Maintenance Teams
👍 Benefits of Effective Leadership
Leadership plays a crucial role in the success of any team or organization. Effective leadership not only helps to centralize the mission and goals, but also improves morale, increases efficiency, and enhances safety. A great leader can inspire and motivate their team, foster teamwork and collaboration, and build strong relationships with team members and other stakeholders. By focusing on personal growth and adopting the right leadership style, maintenance crew leaders can drive performance and improve the effectiveness of their team.
🎯 Centralize mission
It helps to clearly define the mission and goals of the maintenance team, which can help to focus the team's efforts and ensure that everyone is working towards the same objectives.
😃 Improve morale
An effective leader can create a positive and supportive work environment, boosting morale and improving team cohesion. This can lead to increased productivity and better work experience for team members.
📊 Increase efficiency
Good leaders are able to identify inefficiencies in processes and systems and address changes to improve efficiency. This can lead to cost savings and increased productivity for the team.
🦺 Improve safety
Influential leaders prioritize the safety of their team members and work to implement measures to prevent accidents and injuries.
An effective maintenance crew leader can inspire and motivate their team, foster a sense of teamwork and collaboration, and ensure that everyone is working towards a common goal. They can also communicate clearly and build strong relationships with team members, supervisors, and other stakeholders.
By developing these skills and adopting the right leadership style, maintenance crew leaders can drive performance and improve the effectiveness of their teams.
🤩 Characteristics of High-Performing Maintenance Management
Maintenance processes are evolving and improving in response to changing business needs and technological advancements. This shift is helping businesses grow and scale their current operations.
By continuously improving and innovating these processes, businesses can ensure that they can meet the changing needs of their customers and remain competitive in their industry. It is essential for businesses to have a proactive approach to maintenance and to invest in the development and improvement of their maintenance processes to achieve long-term success.
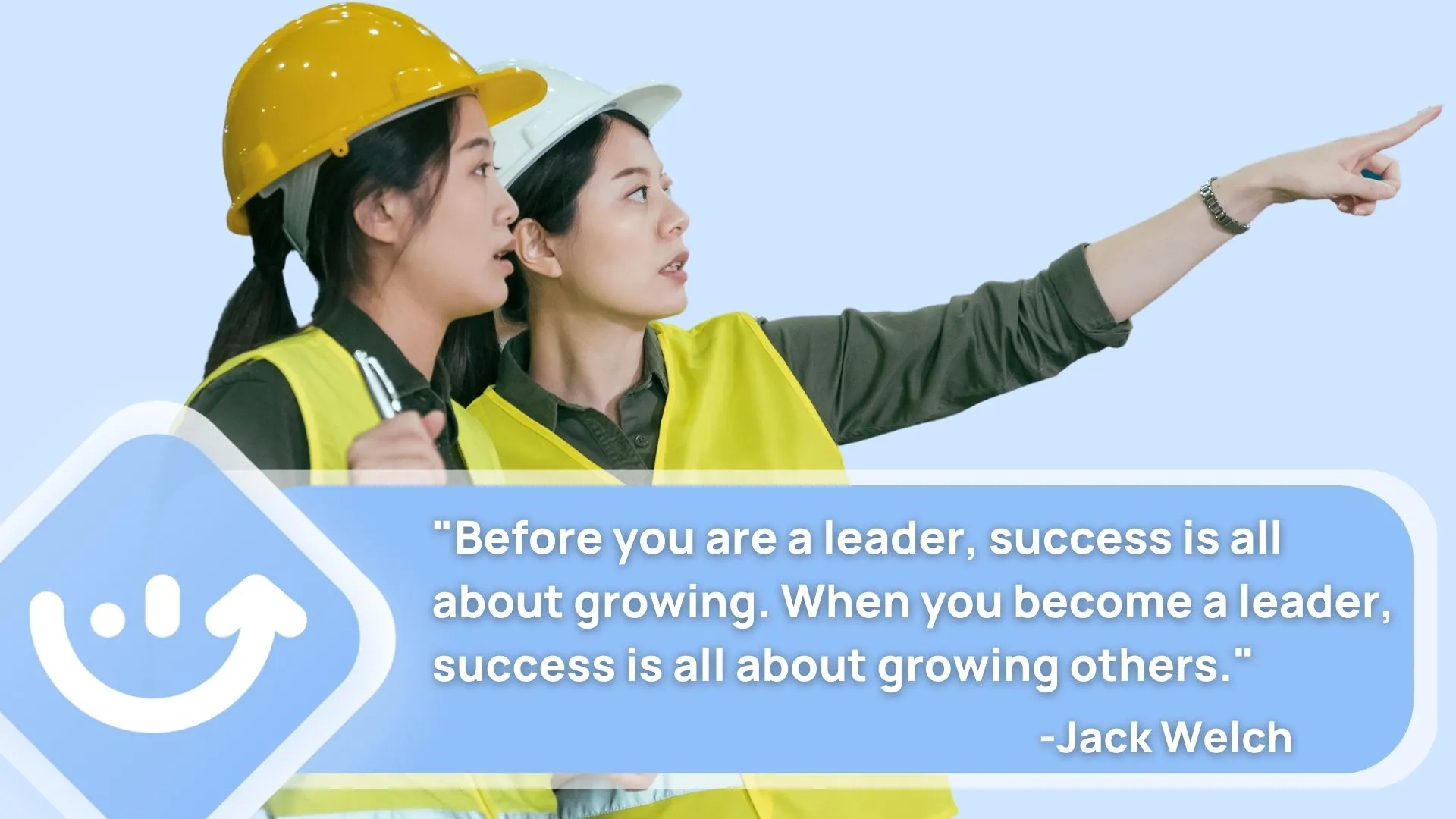
Here are four characteristics of modern maintenance management to stay ahead:
Proactive approach
Modern maintenance management is characterized by a proactive approach to maintenance, in which maintenance tasks are scheduled and planned rather than waiting for equipment to fail. This helps to reduce downtime and improve overall equipment reliability.
Use of technology
Modern maintenance management uses various technologies, such as condition monitoring equipment, mobile CMMS, energy management systems, and predictive analytics, to support maintenance efforts and improve efficiency.
Adoption of industry best practices
Maintenance management is committed to staying up-to-date with industry best practices and continuously improving processes and procedures to optimize maintenance efforts.
Collaborative approach
Modern maintenance management involves collaboration with other departments and stakeholders, including production, engineering, and supply chain, to optimize maintenance efforts and align them with business objectives. This may involve clear lines of communication and cross-functional teamwork.
😎 How to Maintain a Well-Functioning Maintenance Crew
Maintaining a high-performing maintenance team can help improve employee satisfaction and retention.
When team members feel supported and have opportunities to learn and grow, they are more likely to be satisfied with their jobs and less likely to leave the organization. This can reduce turnover and improve your maintenance crew's overall stability and performance.
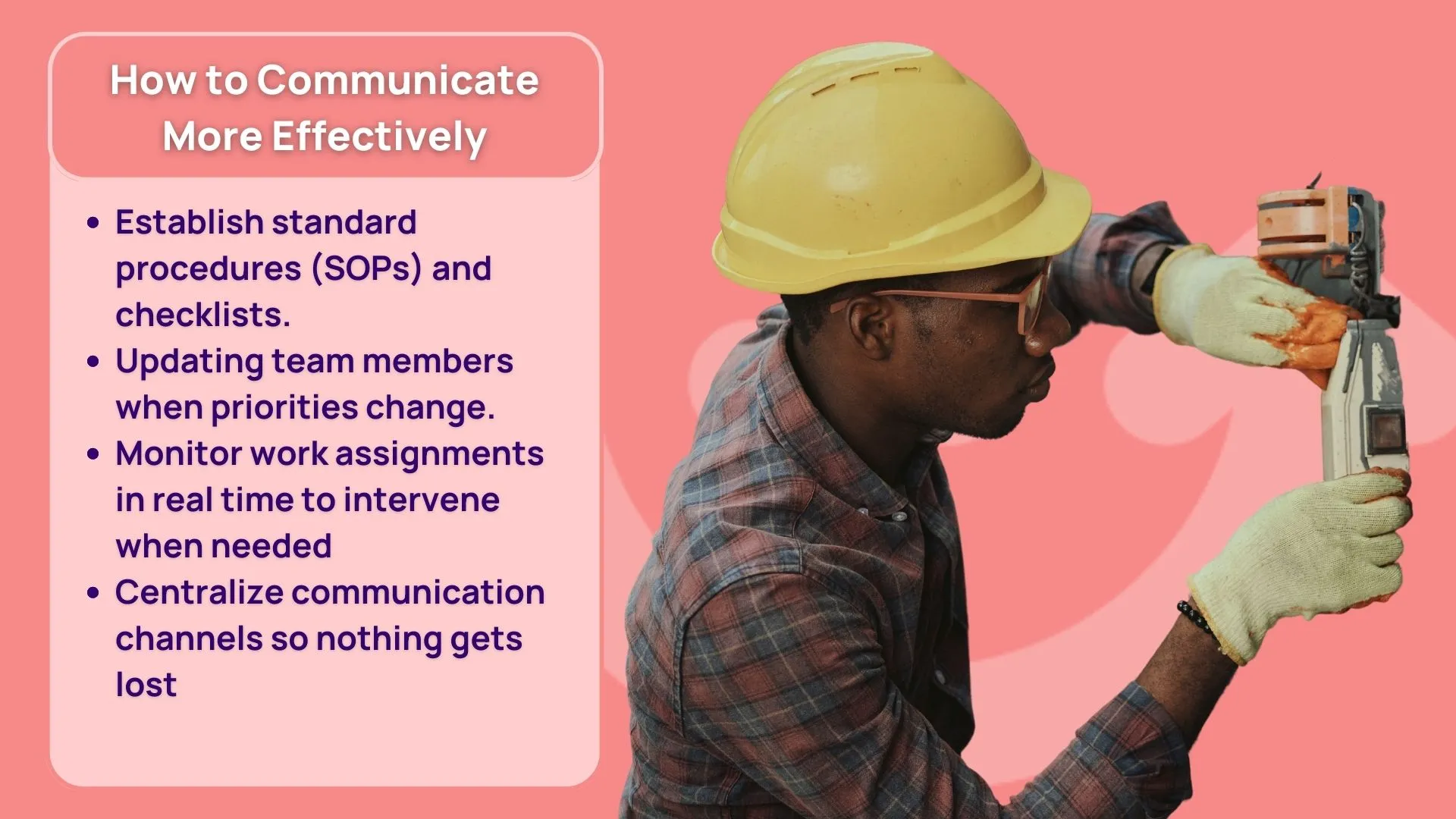
Here are some tips for maintaining a high-performing maintenance team:
Encourage teamwork and collaboration
Foster a team-oriented culture by promoting teamwork and collaboration. Encourage team members to collaborate and share ideas, and provide opportunities for team members to collaborate on projects.
Establish a positive and professional work environment
Create a positive and professional work environment by setting clear expectations for behavior and performance and by promoting a culture of respect and inclusion.
Set clear goals and expectations
Indicate clear goals and expectations for the team, and communicate these goals to team members. This helps ensure everyone is working toward a common objective and that team members understand their roles and responsibilities.
Provide ongoing support and development opportunities
Offer ongoing training and development opportunities to help team members stay current in their field and develop new skills. This can help to improve performance and drive success.
Communicate openly and regularly with team members
Maintain open lines of communication with team members, and encourage them to share their ideas and concerns. This can help build trust and improve the team's overall performance.
Encourage and reward good performance
Recognize and reward team members for good performance, and provide regular feedback to help team members understand what they are doing well and what they can improve upon. This can motivate team members and drive continuous improvement.
.webp)
%201%20(1).webp)