Maintenance and reliability are essential to running a business in today’s economy. With increasing global competition and tightened markets, it’s critical to deliver a high-quality product consistently.
It’s also essential to offer your customers the best possible service—all while keeping costs down. If it sounds like a lot. That’s because it is.
Priced on per user or per location basis
Available on iOS, Android and Web
Managing a business in the manufacturing industry through an economic lens can sometimes feel like you're trying to squeeze blood from a turnip. But what if I said that you could increase output by up to 30% with advancements in maintenance strategies?
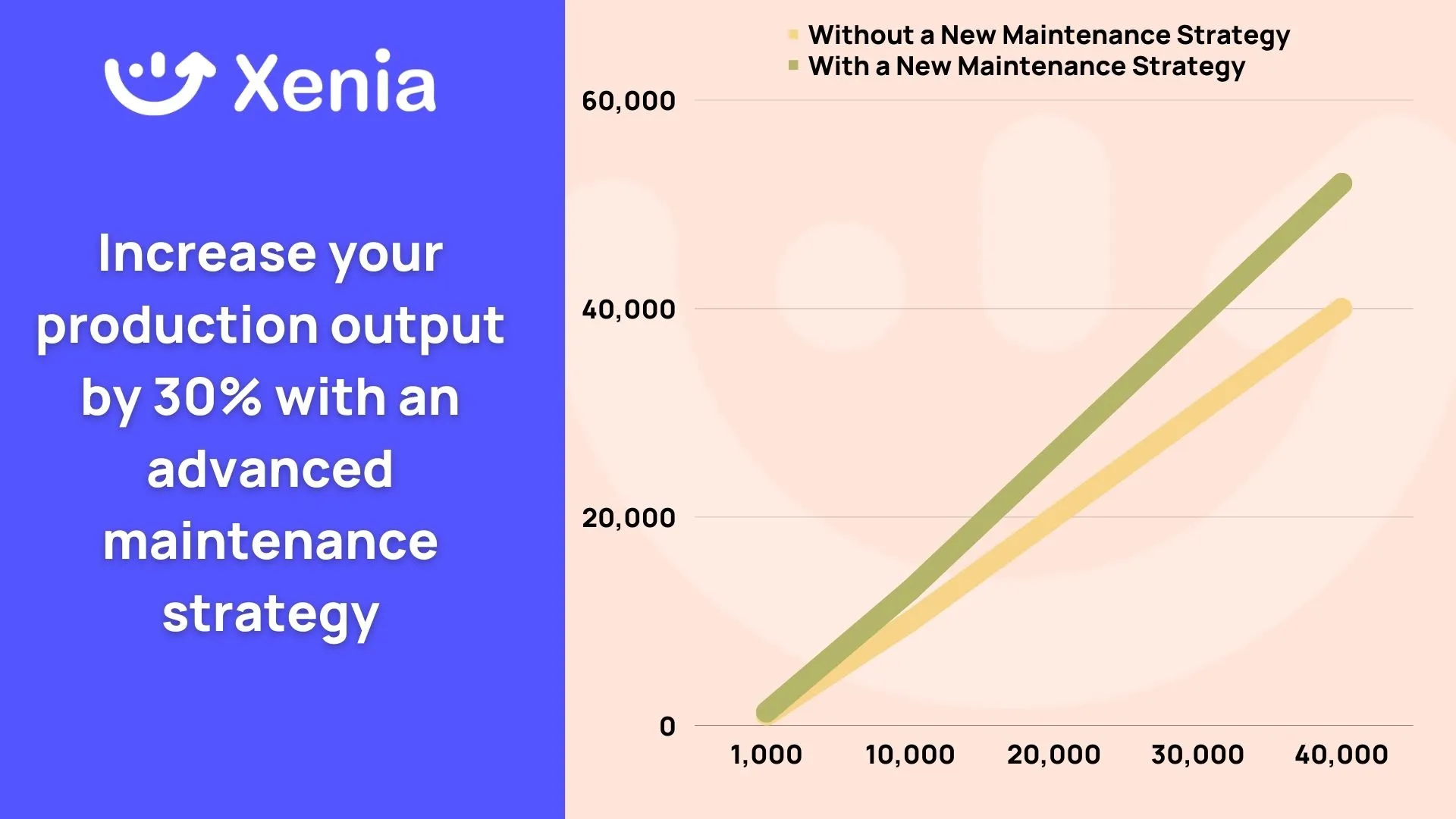
Adopting a new-age maintenance strategy will give you more control over your production schedule. You'll be able to predict when repairs will be needed, making it easier to schedule around them. This is especially important if you have a tight deadline or need to meet specific standards (like ISO).
A well-maintained machine produces better quality products with higher precision for a more extended time. This results in brand consistency, which means more satisfied customers.
10 Reasons Why Maintenance And Reliability are Critical For Success
Maintenance and reliability are two of the most critical factors in the manufacturing industry that can drive a business into success or failure. If you're not sure why this is the case, keep reading!
The manufacturing process is complex and requires many different components to work together to produce something worthwhile. The more complex a machine is, the more likely it is that something will go wrong during the operation. This means that companies in this industry need to be prepared for any kind of situation—and preparedness starts with maintenance and reliability.
If your company wants to stay competitive, you must ensure your machines are always properly maintained.
- It's Time to Streamline Maintenance Management with Xenia's Digital Solutions. Feel Free to Book a Demo
You also must ensure that every employee understands maintenance's importance for their job performance and safety. Everyone must be involved in this process—from designers to assembly line workers.
Let’s dive into the top ten reasons why maintenance and reliability matter for your organization.
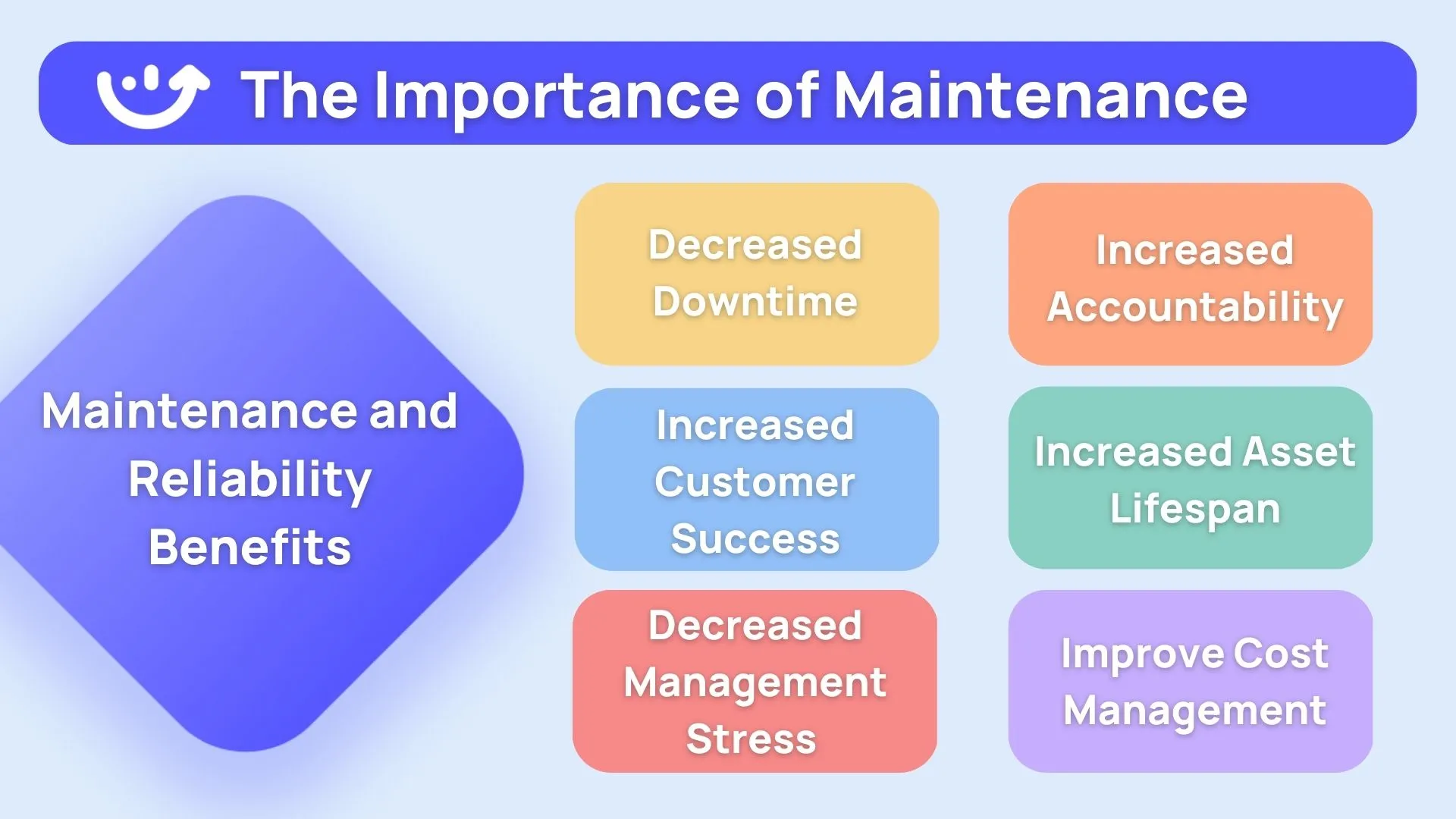
1) Improve safety and reduce the risk of accidents
A well-maintained facility will help improve equipment reliability, reducing the risk of accidents and improving productivity.
Therefore, proactive maintenance is an essential part of an ongoing program. It helps ensure that all equipment is working correctly and that safety systems are functioning as they should. For example, if a machine stops working unexpectedly or breaks down, the problem must be diagnosed immediately so the issue can be addressed before anyone gets hurt.
In addition to helping prevent accidents, keeping your equipment and facilities in good shape can ensure that your business complies with safety regulations. Employers must apply industry-specific OSHA standards; otherwise, they jeopardize losing their business.
2) Extend the lifespan of equipment and facilities
When it comes to maintenance and reliability, businesses are in a tough spot. They need to ensure that their equipment and facilities are working at peak capacity, but they also need to minimize the time and money spent on repairs.
Routine maintenance is the best way for a business to extend the lifespan of its equipment and facilities while reducing replacement costs and preventing premature wear and tear.
Replacing equipment can be costly. It's not just the money—you also have to factor in the time and expense of finding new suppliers and getting set up with a new system.
Plus, when you have older equipment or facilities that are falling apart, it can take longer for your workers to get their jobs done, which means lost productivity and higher costs for you.
The good news is that there is a way to detect the reliability of machinery about its age and use. Identifying asset indicators before they degrade will give you time to budget repairs and replacements accordingly. This will also lead to more sound financial decisions when purchasing equipment in the future.
3) Improve customer satisfaction and loyalty
Customer satisfaction is critical to the success of your business. Customers expect consistent products, clean facilities, and reliable service. When you don’t deliver on those expectations, your loyal relationships suffer.
Bain & Company found that even a 5% increase in customer retention rates will increase profits by more than 25%. When buyers like your product, they will buy more. And tell their friends.
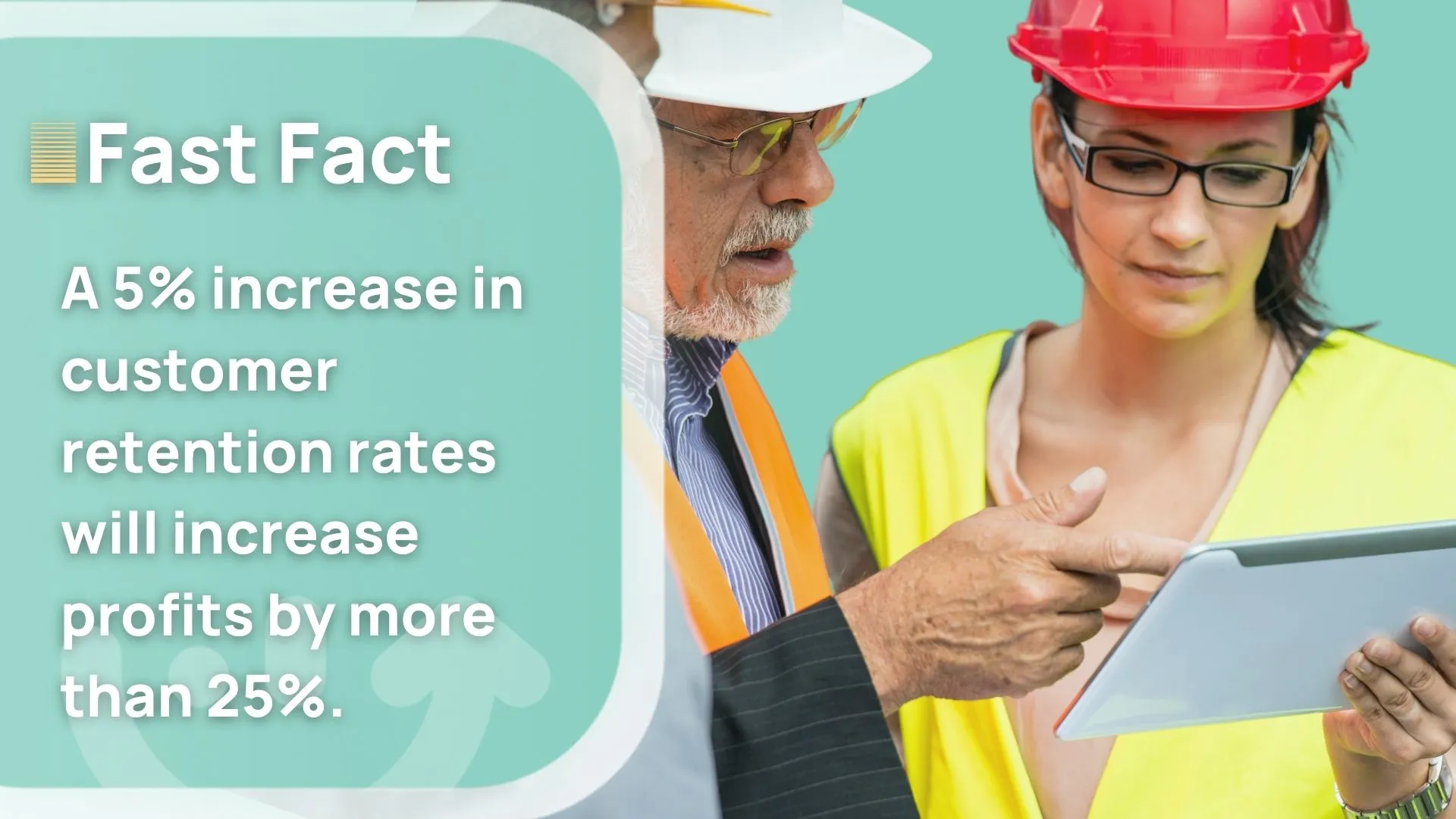
This critique can go as far as the aesthetic of your facility because customers expect a reliable experience as much as a high-quality product. Investing in the maintenance and reliability of your business is the best way to stay competitive and grow.
4) Prevent unexpected downtime and disruptions to business operations
While many companies believe that maintenance is just a cost of doing business, it doesn't have to be.
Maintenance is a necessary expense, but the right approach can save you money in the long run.
A proactive maintenance strategy will identify and address potential issues before they cause downtime. By scheduling routine maintenance on your equipment, you can be sure that it will continue to run reliably for years.
5) Improved reliability can lead to increased productivity and efficiency
It can be hard to get the job done if your equipment and facilities aren't reliable. Keeping productivity high is also challenging if you spend time fixing broken things or worrying about what might break next.
That's why it's crucial to invest in a proper maintenance strategy.
When you maintain your equipment and facilities, you'll reduce the likelihood that they will fail. When they fail, you'll find out quickly so you can take action before it affects anything else—and you'll have a much easier time getting them back up and running again.
Not only that, but if your employees have confidence that their equipment will perform as expected when they use it, they'll be able to focus on completing their jobs. This will lead to increased productivity and higher-quality output.
6) Identify and address potential problems that become costly issues
Routine maintenance can help you identify potential issues before they become expensive problems, which means you can address them quickly and reduce costly equipment failure and downtime.
When you identify problems early, you'll have more time to repair or replace parts before they become significant issues. This saves time, money, and resources that can be used for innovation and growth.
7) Enhance the reputation and credibility of a business
In manufacturing, reliability is more than just having a product that works as expected—it's also about being able to deliver your product on time and in good condition. If your facility is unreliable, shipping times will be delayed, and product quality will suffer.
Clients and customers will only stay loyal to a brand that delivers consistency.
So how do you create a reliable facility? You invest in maintenance. A well-maintained facility can enhance the reputation and credibility of a business by showing that it cares about its customers and clients enough to support this process.
8) Improve energy and reduce utility costs
Maintenance and reliability are essential in manufacturing because they help you improve energy efficiency, which will reduce utility costs.
It's no secret that manufacturing facilities are giant energy hogs. The Department of Energy released metrics explaining that around 76% of all electricity use is within the business sector.
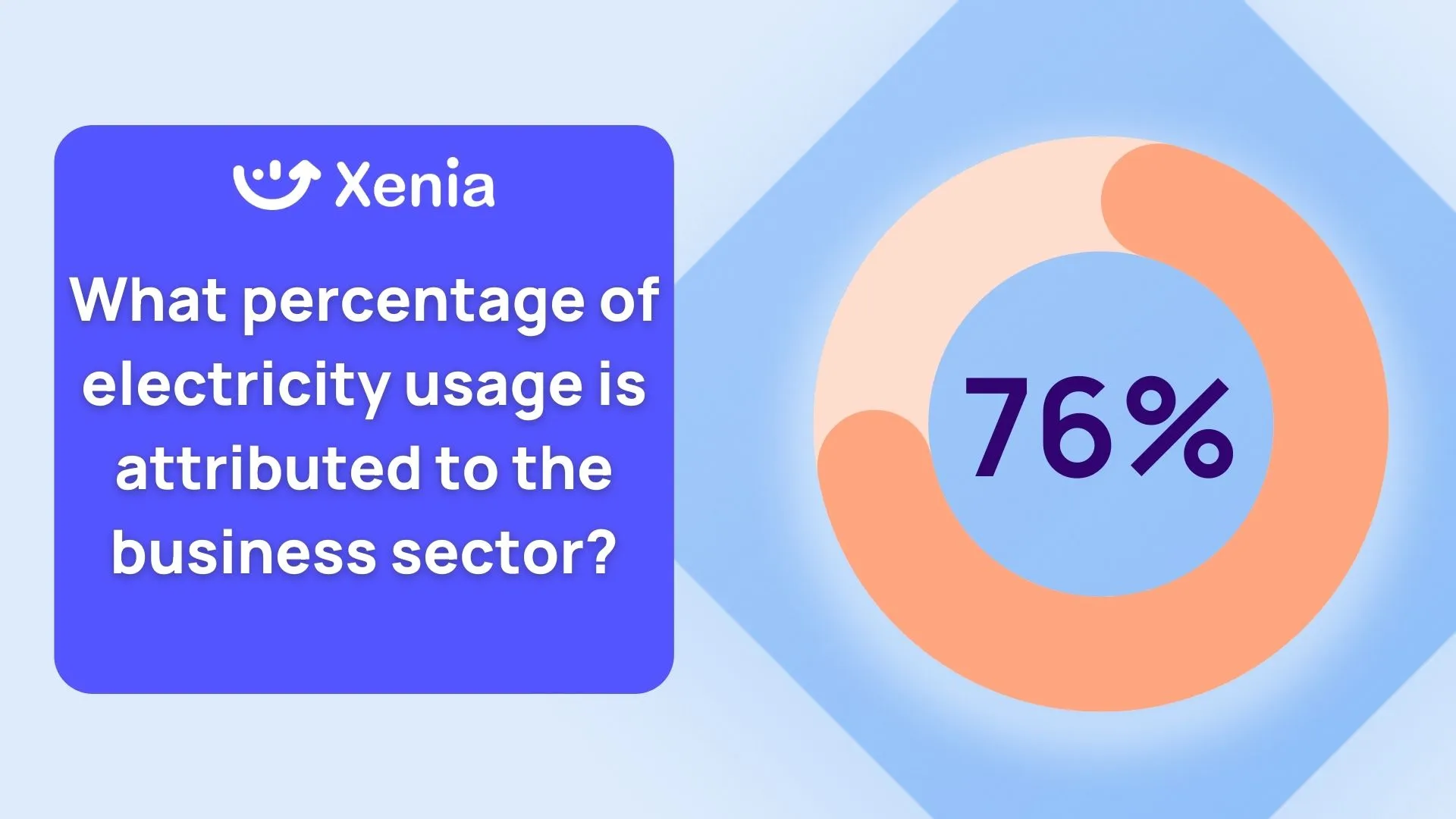
The good news is that you can reduce your business’s energy usage by anywhere between 20%-35% with cost-effective technologies. Up-to-date equipment is designed to run more economically by reducing energy consumption.
When your machines run efficiently, they're more likely to last longer and produce higher-quality output. And if you develop a comprehensive maintenance program for your factory, it may increase the overall efficiency of your facility without adding more equipment!
9) Provide a better working environment for employees
Employees are privy to safety standards, which makes reliable equipment a basic workplace expectation, primarily if they work in a high-risk environment where, in this case, if a piece of heavy machinery breaks down, it can cause injuries – or even worse, fatalities.
When workers feel unsafe, their performance will suffer. Production will decrease if they need more motivation from feeling uncared for or simply not having reliable equipment for each task.
Workforce productivity and safety go hand in hand. When management prioritizes worker safety, employee trust and loyalty in the company will rise. This confidence in safety will yield a more cohesive work culture that breeds motivation and success.
10) Demonstrate a commitment to sustainability
As mentioned above, the manufacturing industry is one of the largest consumers of energy in the US. And it’s time these businesses held themselves responsible.
Not only are more consumers aligning their purchases with social advocacy in the form of business representation, but our administration’s carbon reduction initiative offers various financial incentives. Your stance on protecting our ecosystem will affect your brand and your pocket.
Preventive maintenance is a great way to promote environmental sustainability. One of the best ways to do this is to monitor energy use and opt for technology that will reduce energy dependency.
For example, if you're looking to replace your old light bulbs with LEDs, it makes sense to do so in a way that reduces your carbon footprint and decreases waste by minimizing the number of bulbs you'll have to dispose of.
.webp)
%201%20(1).webp)