The exchange of value is the lifeblood of every company. When you generate value via a product or service, your consumers will pay for it. A practical example of this would be work orders.
Whether client-raised or internal, preventative or corrective, executing work order requests effectively supports smooth business cycles.
Businesses often struggle to locate and disseminate critical procedures to new employees and team members, even though these processes are the result of hours of development and documentation. This is an all-too-common occurrence in many businesses.
The right work order software will assist you in processing and tracking incoming and outgoing work orders, which will improve team collaboration and asset management. CMMS solutions can recover 10 to 50 percent of lost productivity annually. That includes software like Upkeep and MaintainX CMMS.
Both provide a variety of tools to assist you in managing your operations, but which is best for your organization?
To address this issue, we'll look at the particular strengths and adaptability of Maintainx vs Upkeep in maintaining business operations. Understanding the advantages and disadvantages of each software will allow you to make an educated choice when selecting the one that best meets your requirements.
Keeping this in mind, our top two options provide an ideal mix of lean maintenance scheduling software and more dynamic CMMSs with scheduling features.
Priced on per user or per location basis
Available on iOS, Android and Web
The CMMS software price comparison below is intended to serve as a starting point as you begin your search for Maintainx vs Upkeep Alternative(s) that will improve your company's maintenance practices.
What Is Work Order Management Software?
Work order management software is a centralized platform that facility managers use to track, allocate, and monitor preventative maintenance work, react to facility requests, and establish action plans.
Work order management software, often known as computerized maintenance management systems (CMMS), is used by up to 53% of organizations.
Every maintenance team will reach a tipping point when work order software becomes critical to everyday operations. Facility managers in charge of asset management will soon want the simple categorization that only a digital system can deliver.
Work order software solutions essentially provide operational managers with a bird's-eye perspective of which maintenance tasks are in the works, who is accountable for performing them, and a more user-friendly job prioritizing approach.
Most current work order management software solutions, on the other hand, do much more than just plan recurring work orders. While simple software applications exist, the bulk of today's apps also serve as data management systems.
This maintenance software enables businesses to simplify operations by calculating useful data, known as Key Performance Indicators (KPIs), to guide more cost-effective maintenance plans.
Though work order management software is used in a variety of sectors, it is most typically employed by manufacturing facilities that need to coordinate large volumes of daily work orders under a centralized application.
What Should You Look for in Work Order Software?
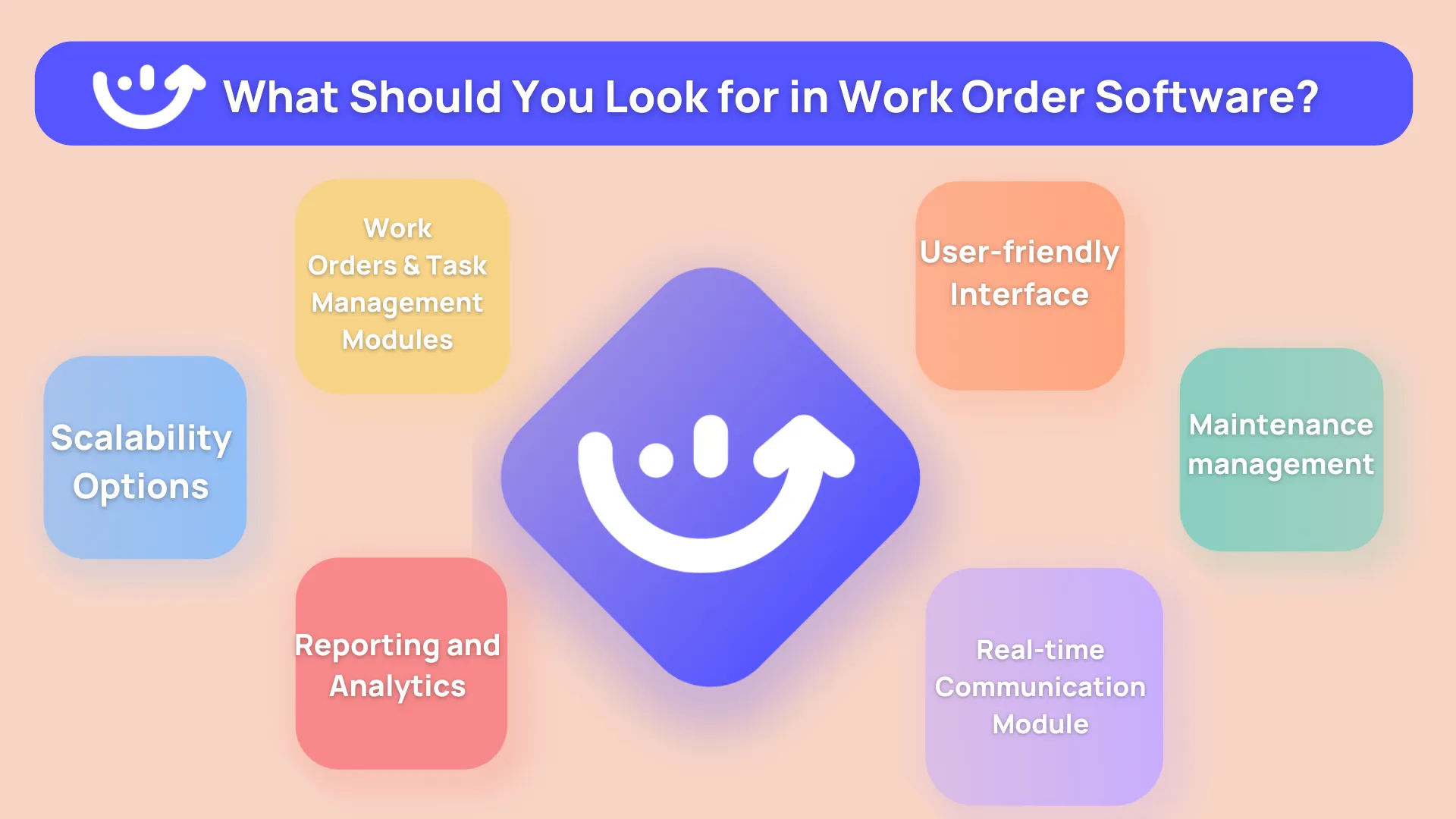
Consider features that facilitate maintenance management and boost operational efficiency when choosing work order software. Here are some important things to check for:
- User-friendly Interface: The program should feature straightforward dashboards and an easy-to-navigate process flow.
- Comprehensive Maintenance Management: Look for features like automatic maintenance scheduling and real-time status updates that allow for full monitoring of repair requests, scheduling, and execution.
- Tools for Real-time Communication: Communication channels inside the program, such as in-app chat and notification alerts, will improve team cooperation.
- Work Orders: Work orders are the most important component of any work order management software. Work orders are modular templates that may be tailored to industry and individual requirements.
- Mobile Accessibility: Features like push notifications and mobile-responsive design enable distant access and updates.
- Work Requests: Work requests are concerned with how maintenance or repair work is requested. Anyone in the system may submit a work request, which is then assigned to the appropriate maintenance team based on parameters such as the location, the kind of maintenance work required, and the maintenance schedule.
- Reporting and Analytics: Understanding maintenance operations and their implications, such as downtime monitoring and cost analysis, is critical for continuous improvement.
- Workflow Customization: The ability to modify the software to your own operational procedures, such as changing task prioritizing criteria or personalizing request forms.
- Cost-effectiveness: Examine the price structure to verify that it fits within your budget and provides good value for money.
Which Types of Maintenance Work Order System Do You Need?
There is a spectrum of work order systems.
There are no-frills systems that merely let you handle job requests and work orders. Then there are solid corporate management systems that include work order modules as part of their wide feature set. Most people fall somewhere around the middle.
Work order systems can be divided into three broad types to help you make a selection.
1) Barebones Work Order Systems
Work order systems at their most basic are intended to generate, allocate, track, and close work orders. They provide rudimentary functionality like work assignments and progress updates, as well as a mechanism to submit service requests and basic reporting capabilities.
While simple WO systems are excellent for tracking work orders, they may lack more complex capabilities like as inventory management, preventative maintenance scheduling, or advanced analytics.
They can be an excellent choice for small businesses that handle a limited number of maintenance activities regularly and want to abandon spreadsheets and paper forms.
They can also be utilized by bigger teams and organizations that need a simple method to manage incoming service requests and ensure that the necessary work is completed on time.
This scenario included a wide variety of use cases, including facilities management, property management, and general contractors, as well as hotels, contact centers, and even software development.
It is getting more difficult to find systems that are just focused on handling work orders. Most software suppliers gradually add more functionality, transforming their basic WO system into a CMMS.
2) Computerized Maintenance Management Software (CMMS)
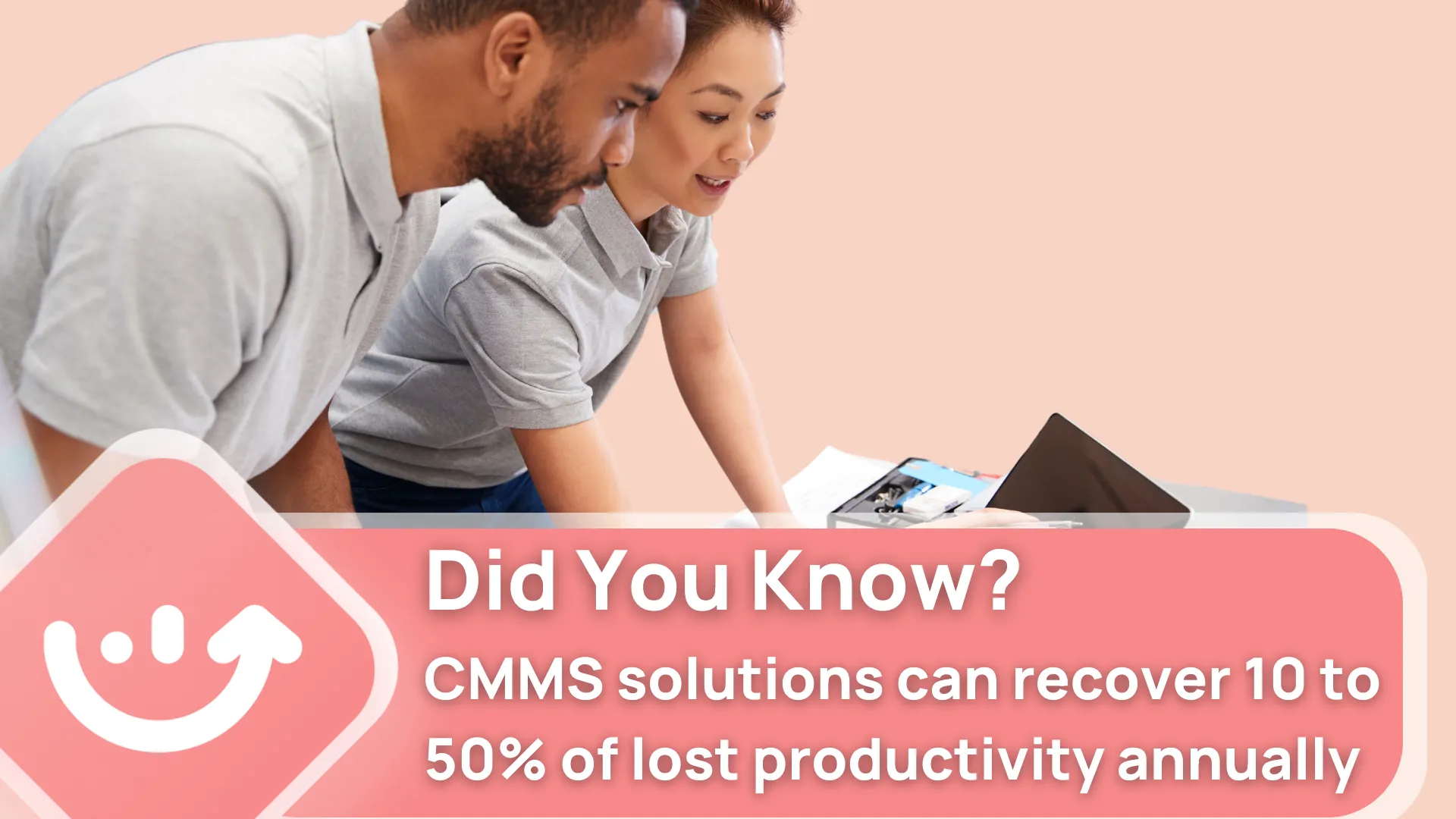
CMMS systems are designed to assist enterprises in automating, streamlining, and simplifying all maintenance activities.
A CMMS often contains capabilities like as asset management, preventive and predictive maintenance scheduling, inventory control, vendor management, cost monitoring, and thorough reporting and analytics in addition to work order management.
Having all of your maintenance information in one place and accessible by mobile device allows maintenance and facility managers to increase productivity, reduce operating costs, and improve asset performance and durability.
While there are industry-specific solutions, such as fleet management systems, standard CMMS software is adaptable and can serve a broad variety of use cases:
- It may be utilized by organizations of all sizes (though certain CMMSs are designed primarily for corporations).
- It monitors and controls all physical assets as well as maintenance work.
- It may be utilized in almost any sector. Manufacturing, construction, hotels, commercial facilities, energy & utilities, and government agencies are among the most common industries.
3) Field Service Management Software (FSM)
FSM software is intended to manage and coordinate field activities by using a mobile workforce. While it does not cover all of the broad asset management operations of a CMMS, it does offer tools for job scheduling and dispatching, inventory management, customer information management, work order management, billing and invoicing, and other services.
The software often includes a mobile application that enables field technicians to obtain all relevant information, efficiently communicate, and update task status from the field.
Businesses that offer on-site services generally utilize Field Service Management Software (FSM). Here are some examples of common applications:
- FSM is used by businesses that provide repair and maintenance services such as HVAC, plumbing, janitorial, or electrical repair to book service appointments, allocate them to workers, manage time and materials utilized, and handle invoicing and billing.
- FSM software is used by telecommunications and cable providers to handle equipment installation, servicing, and repair at client sites.
- FSM software helps in the scheduling and management of complex machinery and equipment in the oil and gas sector.
- Construction and landscaping companies utilize FSM software to plan and dispatch personnel, manage supplies and equipment, monitor project progress, and manage expenses and invoices.
Benefits of Work Order Management Software
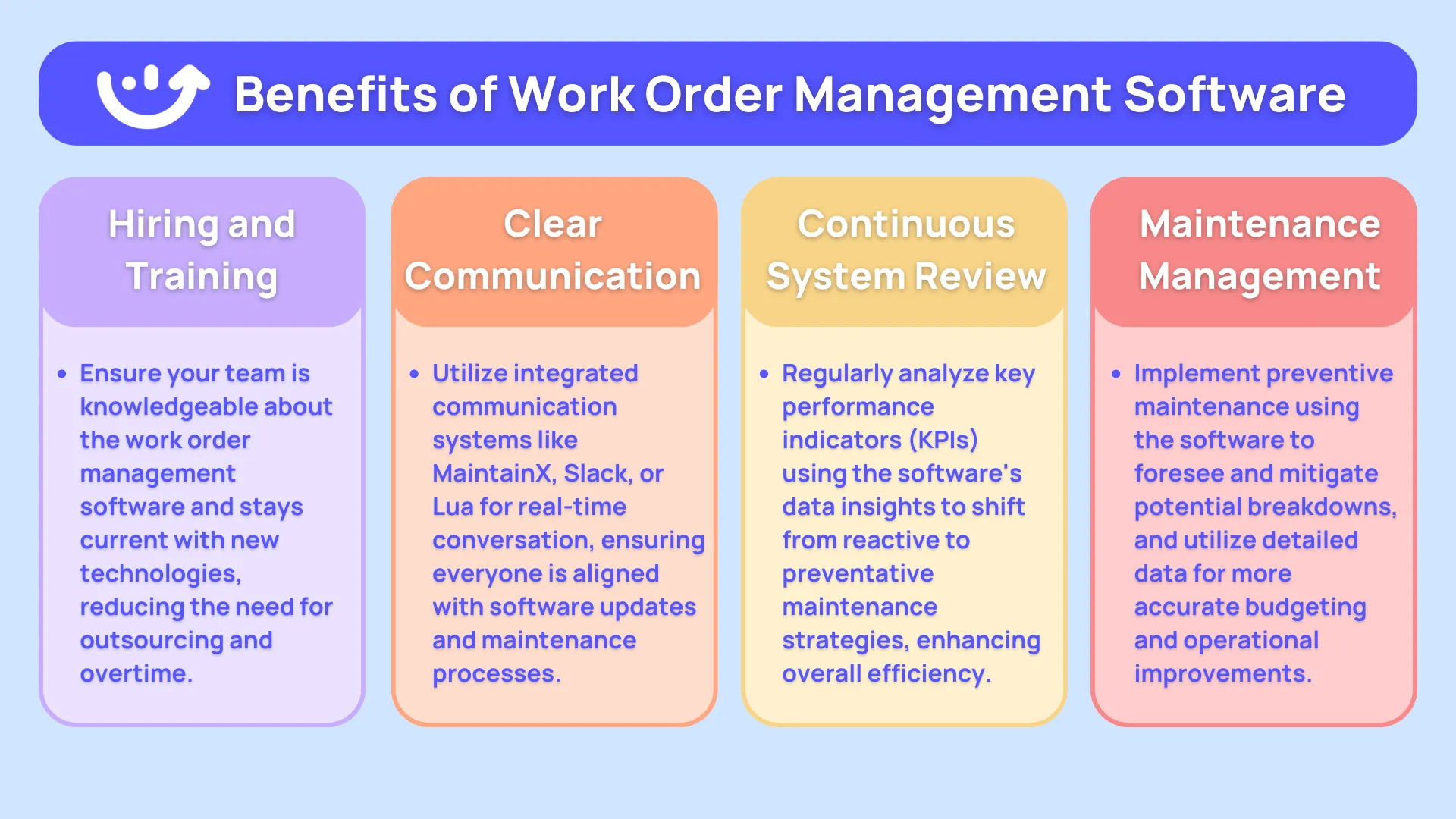
Work order management software is only a tool. It will not miraculously convert your maintenance department into a well-oiled machine. Prioritize the following tasks while building your software:
- Hire Qualified Maintenance Personnel: Your staff should be educated about the work order management software you're utilizing. People you recruit should also be open to learning since new technologies arise every day, and your staff will need to keep current on the newest technologies in use. Hiring unqualified employees increases the demand for outsourcing and, eventually, over time.
- Well-Defined Communication Lines: When communication lines are well-defined, everything becomes a lot simpler and problems can be managed successfully. To guarantee that everyone is on the same page with program modifications, use a connected workforce system such as MaintainX app, Slack, or Lua that provides real-time conversation.
- Consistently Review And Improve Systems: Work order management software delivers informative data that often exposes deeper insights for development. Set aside time each month to analyze your organization's key performance indicators (KPIs) and increase your team's ratio of preventative to reactive maintenance activities.
- Unexpected Problem Reduction: Preventive maintenance is critical in decreasing unexpected issues. Work order software allows you to arrange preventive maintenance work, which prevents breakdowns by predicting probable problems. Work order software also helps to simplify and automate processes by reducing the incidence of emergency repair and assigning staff-ordered preventative maintenance chores.
- Detailed Data/Improved Budgeting: Work order software gives you a detailed look at how maintenance jobs are executed and supported over time. You can continually improve your maintenance operations by comparing real-time data to KPIs or specific targets. Up-to-date information, or even real-time data, allows management to plan and budget more correctly.
- Increase Efficiency: Maintenance automation saves a lot of time. Work order management software eliminates the need for paper tickets and other paperwork by allowing you to manage everything from a single dashboard on your computer or mobile device. Process automation decreases the likelihood of errors, disorganization, duplication, and inefficiencies.
Remember, you don't have to start huge. Creating a firm foundation by creating a preventative maintenance program that includes your most vital pieces of equipment and is backed by user-friendly work order management software can pay big benefits in the long run. As your team's expertise grows, you may always add new assets to the database.
Getting to Know Maintainx vs Upkeep
MaintainX
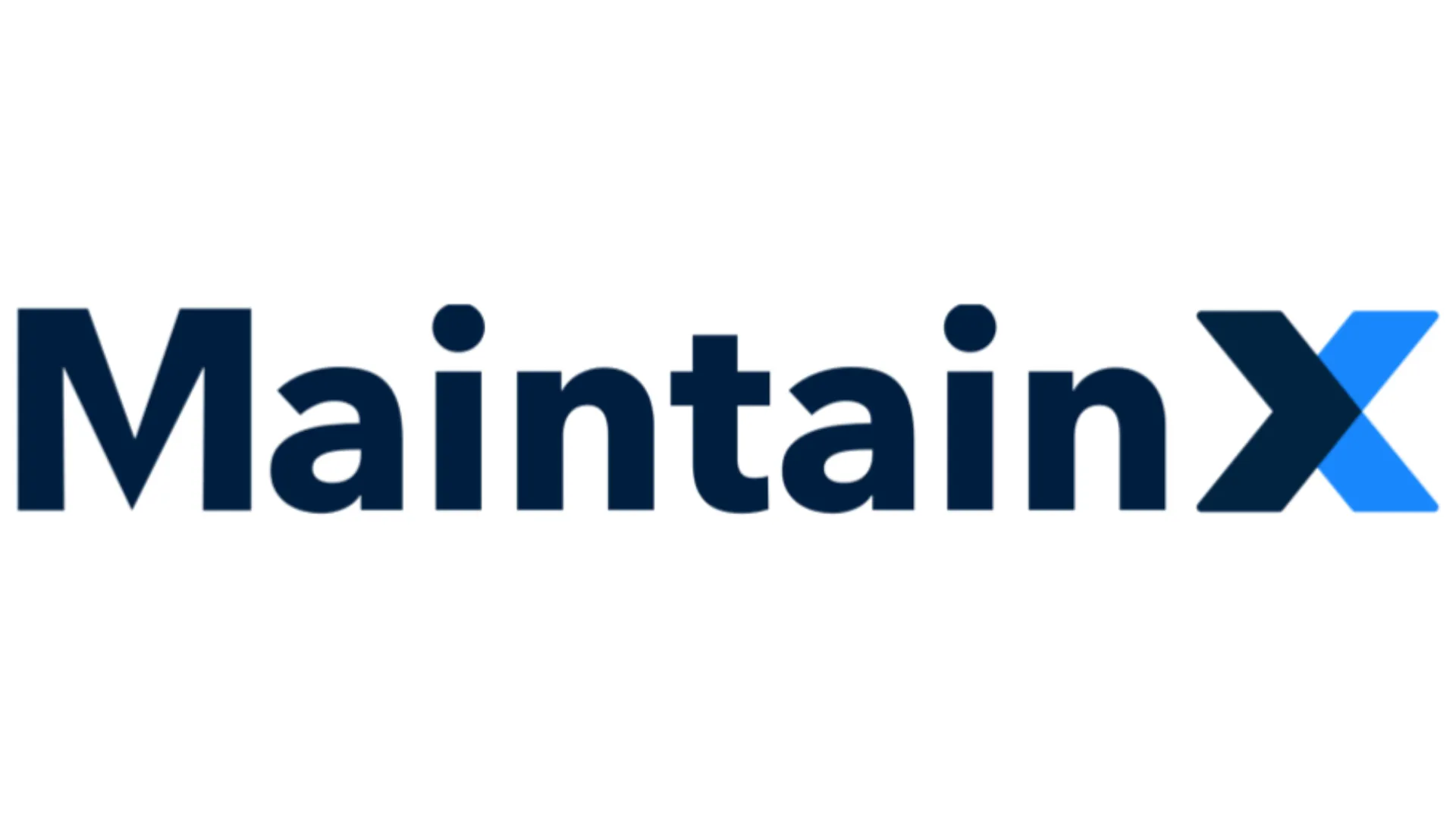
MaintainX app is, unsurprisingly, the world's first CMMS platform to include real-time conversation.
In other words, operational managers, maintenance personnel, and key stakeholders can instant message one another straight from MaintainX work order CMMS in the app.
MaintainX is a company that focuses on maintenance management. It has a procedure documentation tool that lets you write and maintain procedures for maintenance and operations activities.
It has advanced tools for organizing MaintainX work orders CMMS, asset monitoring, and safety audits. This makes it an excellent alternative for companies involved in maintenance and operations.
So, what is MaintainX?
MaintainX CMMS, in other words, does a little bit of everything.
The most appealing attraction for MaintainX software, however, is the wealth of functionality included in the app's freemium plan, which makes the software accessible to SMBs and large businesses.
Because of its focus on maintenance management, it may not be the greatest choice for firms in other sectors that need a more general-purpose documentation solution.
Best For
1-1000+ users
This complete solution is perfect for managing operations effectively and is suitable for a wide variety of sectors and organizational sizes. This software meets the demands of manufacturing facilities, industrial operations, government entities, schools, hospitality establishments, and operational teams.
Its capabilities are expanded to include fleet managers, restaurants, warehouses, churches, retail organizations, and safety/EHS leaders.
With scalability ranging from small and medium-sized companies (SMB) to enterprise-level, this adaptable solution is intended to improve productivity and effectiveness across a wide range of industries according to MaintainX reviews.
Noteworthy Features
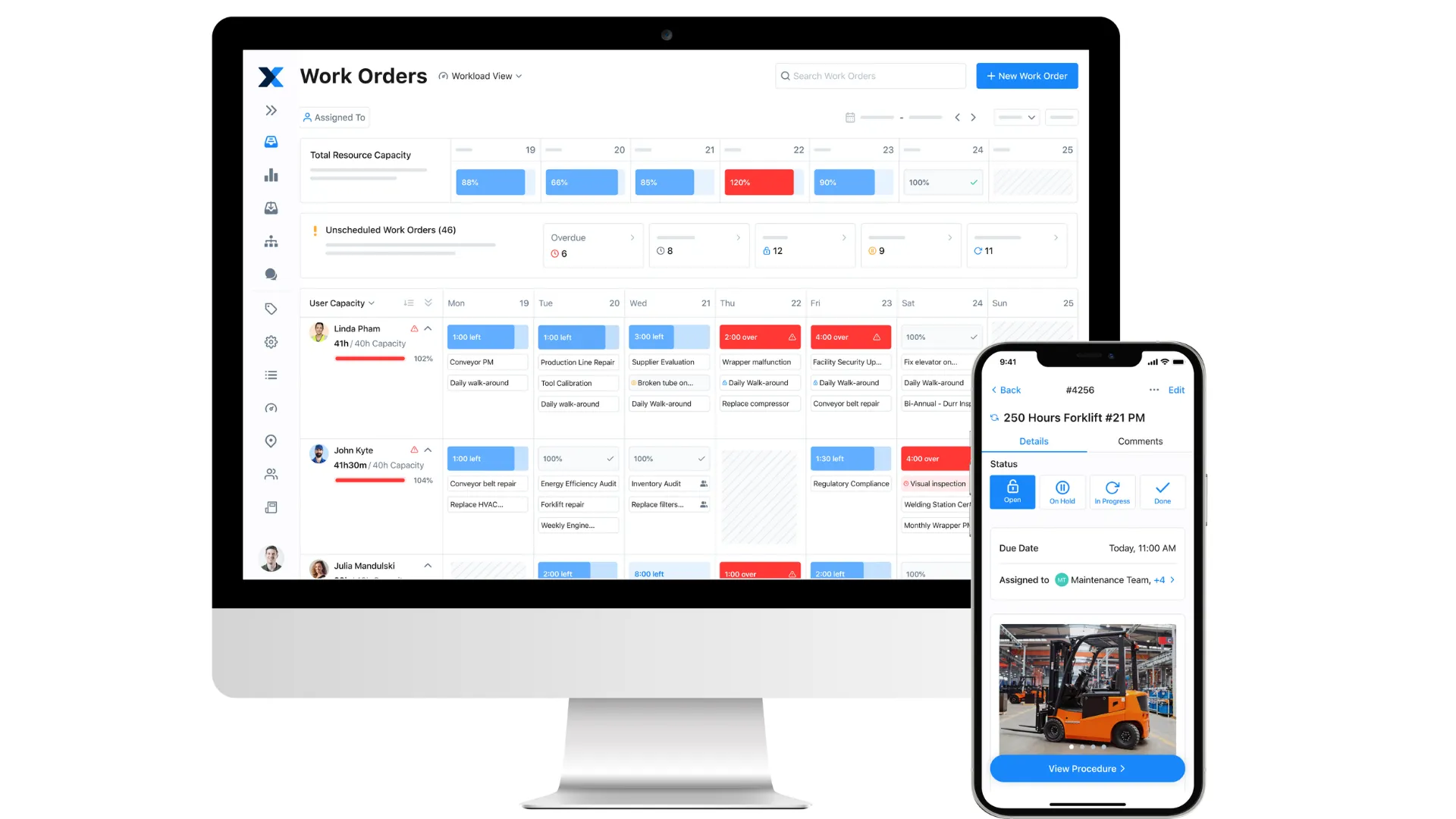
- Instant Messaging: Filter chat discussions by persons, groups, departments, themes, and more.
- Work Order Commenting: Chat with professionals directly inside individual work orders to troubleshoot in real-time.
- Photo Uploading: Share (and mark up) photographs of equipment failures, component difficulties, or maintenance quandaries to better clarify what's going on.
- Management of Assets: Take care of tools, vehicles, buildings, and equipment. Track expenses, downtime, and uptime, including warnings when an asset fails to be assigned to a proper specialist.
- Reporting: Examine asset repair costs, components utilized during maintenance, asset downtime and uptime, and work order fulfillment. On a single screen, see the history of specific assets.
- Management of Work Orders: Assign and monitor work orders for buildings, equipment, forklifts, and other items. Submit work orders without having to fill out paperwork, and track staff performance by examining work order history. Create recurring work orders on a calendar or have the runtime based in seconds.
- Communication: Instead of having a disconnected discussion across email, phone conversations, and text messages, easily link people from multiple departments, plants, shifts, and facilities with a common hub for communication. With real-time communication and permanent time stamps, you can keep everyone informed and in sync.
- Compliance: Develop and assign inspection methods, paperwork, and compliance processes to ensure OSHA and other applicable standards are met.
- Safety Inspection: Create a repeated work order with an associated form for frequent safety checks. Set the frequency to daily, weekly, or monthly to get alerts before the inspection.
- Audit Trails: Record inspection dates and times, attach images, files, and signature blocks, and quickly export completed inspections.
- Escalation Protocols: Inform the escalation team when an inspection item is flagged or fails, and develop and assign remedial actions.
- Quality Control: Measure and standardize quality control procedures, determine the underlying cause of quality concerns and implement remedial measures across the business.
- Mobile App: Access a real-time chat and work order system, as well as the option to attach photographs to work orders to clarify issues. Prioritize and arrange work orders depending on urgency, all of which may be seen on a single screen. Available for Android, iOS, and iPad.
- Inventory Management: Set a restriction on the quantity of a component required and be informed when stock runs short. Using customizable data, make capital choices and monitor where components are utilized. Scan barcodes connected to items and assets to add them to work orders.
Deployment
- Cloud, SaaS, Web-Based
- Desktop - Mac
- Desktop - Windows
- Desktop - Linux
- Desktop - Chromebook
- Mobile - Android
- Mobile - iPhone
- Mobile - iPad
Training Resources
- Documentation
- In Person
- Live Online
- Videos
- Webinars
Support
- Phone
- Chat
- FAQ
- Forum
- Knowledge Base
- 24/7 Live Support
MaintainX Pros
- Enjoy a simple user interface for quick navigating
- A mobile app allows you to manage everything on the fly
- Create and manage work orders with photographs attached
- Obtain dynamic SOPs that respond to user inputs
- Use the built-in chat to boost team collaboration
MaintainX Cons
- Advanced capabilities, such as IoT sensor integrations, are only accessible in corporate subscriptions.
- Problems with compatibility with various systems or devices
MaintainX Ratings and Reviews
- G2: 4.8/5 (500+ reviews)
- Capterra: 4.8/5 (500+ reviews)
MaintainX CMMS Pricing
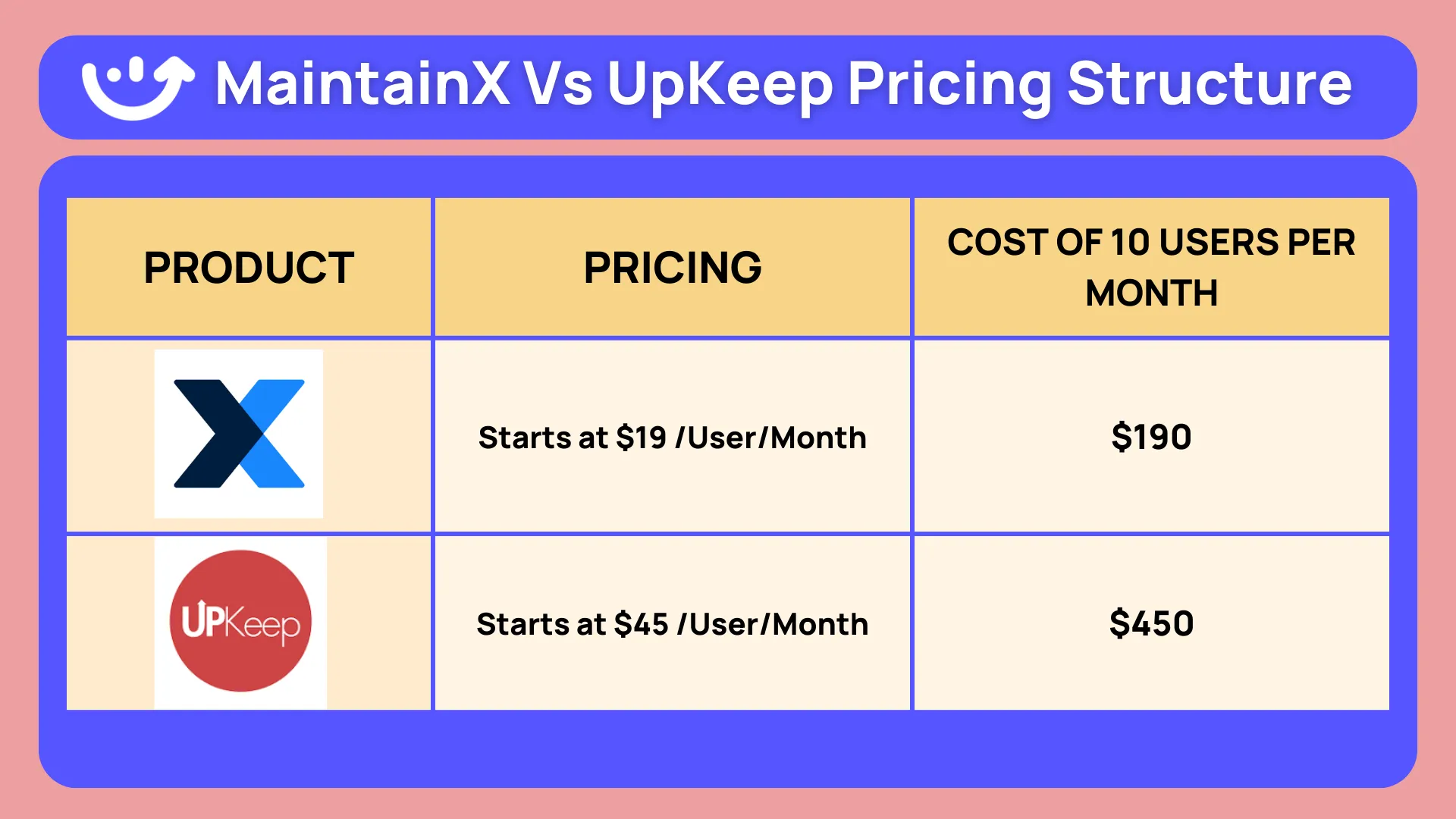
Basic MaintainX cost
- Free
Features
- Unlimited Work Orders
- Unlimited requester users
- Real-time messaging
- 2 active repeating Work Orders
- 2 Work Orders with attached Procedures
- 1-month access to Advanced Analytics
Essential
- $19 /User/Month
Features
- Includes features of Basic plan, plus:
- Unlimited Work Orders with attached images
- Unlimited repeating Work Orders
- 3 Work Orders with attached Procedures
- 3-month access to Advanced Analytics
Premium
- $49 /User/Month
Features
- Includes features of Essential plan, plus
- Unlimited Work Orders with attached Procedures
- Unlimited access to Advanced Analytics
- Meter-based maintenance
- Parts inventory management
- Purchase order management
- Time and cost tracking
- Open REST API access
Enterprise
- Custom
Features
- Includes features of Premium plan, plus
- Escalation protocols
- Custom permissions
- IoT sensor integrations
- Advanced control and security, including SSO
- Multi-site management tools and reporting
- Dedicated Account Manager
UpKeep
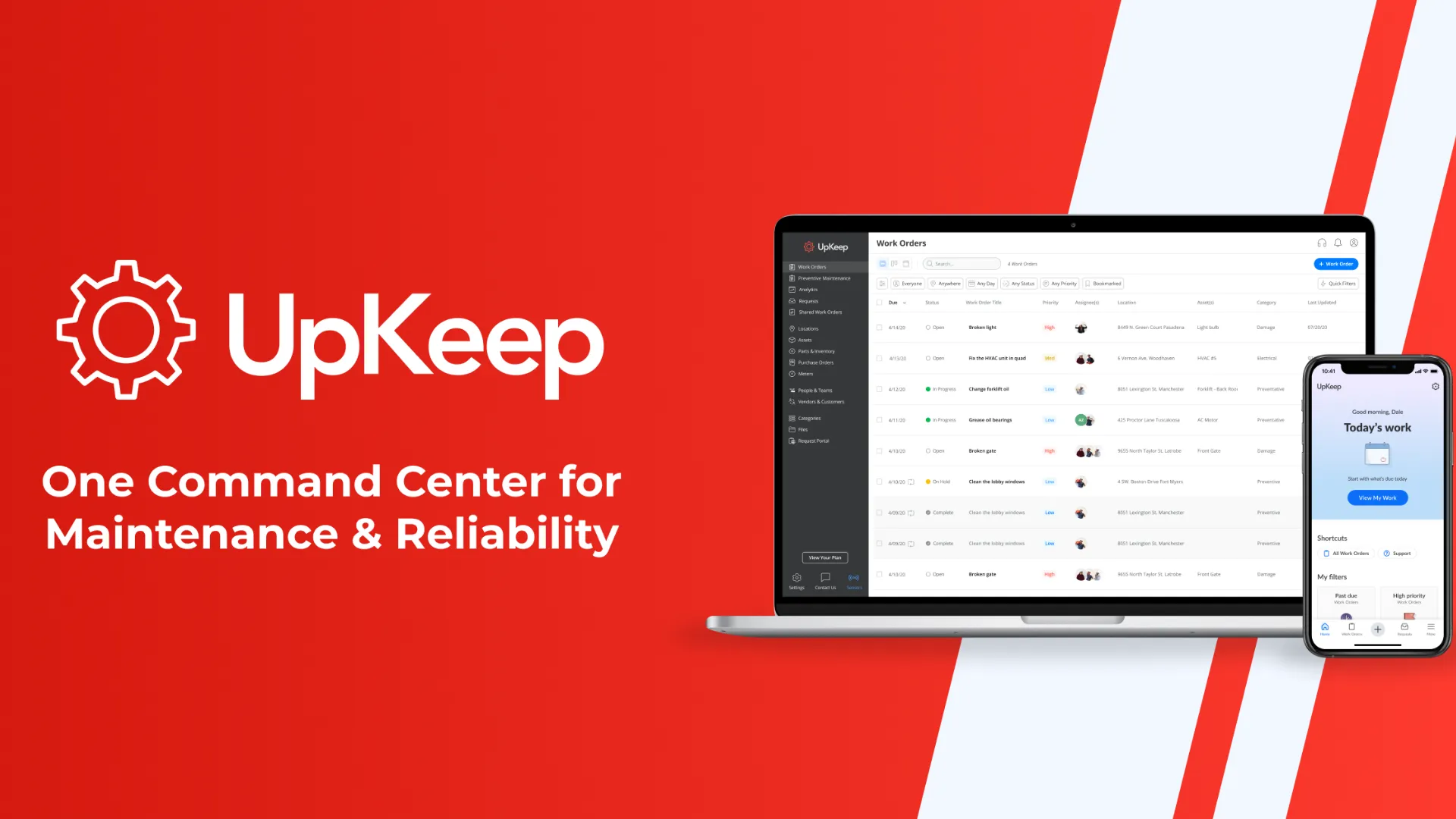
UpKeep is a cloud-based, contemporary asset management and maintenance software that can handle all of your asset and inventory management requirements. UpKeep, a maintenance software tool, also obtains good marks for usability, functionality, and customer service.
The mobile software, which was created exclusively for mobile use in 2014, enables maintenance workers to generate and manage recurring work orders, maintain inventories, perform billing/invoicing, manage calibrations, control keys/locks, and much more.
It is easily accessible from any device, whether a PC, mobile app, or tablet, from anywhere and at any time. UpKeep puts inspecting and tracking the lifetime of your assets and inventories at your fingertips, even while you're on the road.
The software allows you to create work orders, get notifications when work is completed, and even receive alerts when equipment breaks down while on the go, allowing you to make more effective and efficient choices without wasting time.
UpKeep enables custom construction of the system as per the team's needs, making it incredibly responsive, familiar, user-friendly, and cost-efficient. It has amazing tools and capabilities to use and an easy-to-learn interface. You can now employ this program to simplify each technician's job performance and keep everyone on target and the same page, even on their smartphone.
Furthermore, we've received a lot of excellent comments from property managers about UpKeep's requester site! It's also worth noting that UpKeep's freemium version was designed to enable consumers to "try before they buy" and isn't intended to be a full CMMS solution.
Best For
1-1000+ users
Catering to a wide spectrum of industries and accommodating user groups ranging from 1 to 1000+, this robust solution is well-suited for diverse sectors. Whether you operate in manufacturing, healthcare, agriculture, food processing, facilities management, fleet management, hotels, oil & gas, construction, distribution, warehousing, utilities, or packaging, this software is tailored to meet your specific needs.
Its versatility makes it an ideal choice for various businesses, providing comprehensive tools for streamlined operations and effective management across different industries.
Noteworthy Features

- Available in three languages: English, French, German, and Spanish.
- Media Uploading: To further show what's occurring, you may upload (and annotate) images of equipment failures, component problems, or maintenance challenges.
- Uploading PDFs: Directly upload crucial PDFs, manufacturer's recommendations, training manuals, and business rules into particular work processes.
- E-Signatures: Technicians may use the app's time stamp function to sign off on completed work for further accountability.
- Work Order Management: Accept customer work order requests or construct them on the fly. On your mobile device, manage these work orders and establish technician schedules to assign work. View and update outstanding work requests before accepting them, and provide role-based access to govern who is permitted to cancel work orders after they have been declared complete.
- Preventive Maintenance Scheduling: Use the PM scheduler to generate preventive maintenance plans that are both calendar-based and runtime-based. Create regular work orders to ensure timely maintenance and lessen the possibility that someone would forget to schedule maintenance when the time arrives.
- Asset Management: Entails keeping track of asset performance (uptime and downtime). Get a complete picture of the asset life cycle, repair costs, and other critical asset profile information.
- Inventory Management: Involves setting threshold values to particular components in order to track stockroom levels. Receive alerts when that figure is achieved, allowing users to reorder the required replacement parts or inventories.
- Cost Analysis and Forecasting: Compare depreciation data with downtime data to evaluate if an item is worth repairing, selling, or scrapping. Keep track of depreciation and maintenance costs to develop more accurate cost projections for future asset purchases. Track technician hours and divide labor time across activities to discover issue areas.
Deployment
- Cloud, SaaS, Web-Based
- Desktop - Mac
- Desktop - Windows
- Desktop - Linux
- Desktop - Chromebook
- On-Premise - Windows
- On-Premise - Linux
- Mobile - Android
- Mobile - iPhone
- Mobile - iPad
Training Resources
- In Person
- Live Online
- Webinars
- Documentation
- Videos
Support
- Phone
- Chat
- FAQ
- Forum
- Knowledge Base
- 24/7 Live Support
UpKeep Pros
- Streamline maintenance work order generation, evaluation, prioritizing, and measurement.
- Work orders may be assigned and filtered based on parameters such as technician, location, and priority.
- Reduce response times by automating data gathering and reporting.
- Mobile tools for handling work orders while on the move
UpKeep Cons
- New users may have a learning curve.
- Compatibility with current systems or special business requirements necessitates further modification or integration work.
UpKeep Ratings and Reviews
- G2: 4.5/5 (800+ reviews)
- Capterra: 4.7/5 (1300+ reviews)
Upkeep Software Pricing
Community
- Free
- For small businesses that want to streamline work orders, track assets, and move into the digital world.
Features
- Data Importing
- Work Order Management
- Location Management
- Asset Management
- Inventory Management
- Barcode Scanning
- Unlimited View-Only Users
- Unlimited Vendors
- Unlimited Requesters
- Push Notifications
Starter
- $45 /User/Month
- For small businesses that want to streamline work orders, track assets, and move into the digital world.
Features
- Data Importing
- Checklists
- Work Order Management
- Preventive Maintenance
- Time and Cost Tracking
- Offline Mode
- Location Management
- Asset Management
- Inventory Management
- Barcode Scanning
- Meter Readings
- File Upload
- Full Drill-Down Reporting & History: 30 Days
- PDF and CSV Exporting
- Itemized Time Reporting
- User Log-in Reports
- Requests Analysis
Professional
- $75 /User/Month
- For small and medium-sized businesses that want advanced reporting around maintenance activities.
Features
- Data Importing
- Checklists
- Work Order Management
- Preventive Maintenance
- Signature Capture
- Time and Cost Tracking
- Offline Mode
- Request Portal
- Location Management
- Asset Management
- Inventory Management
- Barcode Scanning
- Meter Readings
- File Upload
- Full Drill-Down Reporting & History : Full
- PDF and CSV Exporting
- Itemized Time Reporting
- User Log-in Reports
Business Plus
- $120 /User/Month
- For businesses that want advanced asset tracking, maintenance scheduling, and reporting with APIs. 5 users minimum.
Features
Data Importing
- Checklists
- Work Order Management
- Preventive Maintenance
- Workflow Automation
- Signature Capture
- Time and Cost Tracking
- Offline Mode
- Request Portal
- Location Management
- Asset Management
- Inventory Management
And tons more!
Maintainx vs Upkeep Alternative(s) - Xenia
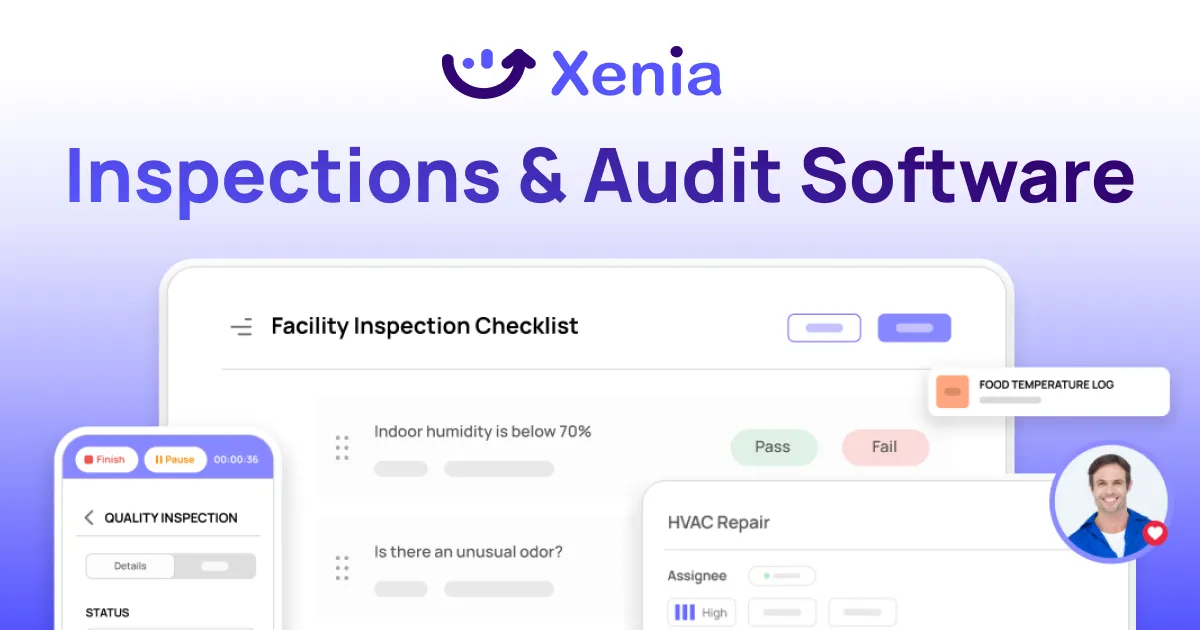
Xenia is the best platform for integrated work order management. Xenia's platform is designed with frontline workers in mind, with a pleasant, customizable, and versatile online and mobile interface.
This MaintainX vs Upkeep alternative is adaptable and adjustable for large, remote sites as well as local property management teams, with solutions for team communication, work orders, preventive maintenance, internal chats, accountability monitoring, inspections, and analytics.
Moreover, the platform is the ideal option for hospitality staff, since it includes capabilities for:
- Maintenance Work Orders
- Calendars for Preventive Maintenance
- Requests from Guests
- Communication and Quality Assurance
- Audits and inspections
And The Winner Is?
Work orders are an essential component of good maintenance. When effectively managed, they provide your team with the stability and structure it needs to be efficient. A well-designed maintenance work order and work order workflow facilitates the establishment of a preventative maintenance program and the response to unplanned repair.
Roles have been established, procedures have been improved, tasks have been monitored, and information has been well-documented. The last and most important piece of the jigsaw is selecting the correct tools and systems for managing work orders. When everything comes together, your organization will be able to understand the foundations of maintenance while also looking for new methods to expand and flourish.
MaintainX vs Upkeep? So who is the winner? The answer to this question will vary from business to business.
Before looking for a solution to your organization's demands, take the time to examine them.
.webp)
%201%20(1).webp)