Machine maintenance is the process of regularly inspecting, repairing, and servicing machinery to ensure that it is operating at its best. This is an essential aspect of any business that relies on machinery.
Neglecting machine maintenance can lead to a number of negative consequences. When machinery is not maintained correctly, it can break down or malfunction more frequently, leading to prolonged downtime and reduced output.
Unplanned downtime can have significant financial and operational impacts on a business, resulting in lost revenue, decreased productivity, and customer dissatisfaction. Across industries, this is a significant problem.
Priced on per user or per location basis
Available on iOS, Android and Web
A recent survey of varying sectors saw 82% of companies report downtime within the last three years. And the cost of this unplanned downtime can be startling.
Businesses with higher production levels typically experience more significant amounts of lost revenue and productivity. However, any industry can suffer financially from downtime. Calculate your business’ downtime cost using this free tool!
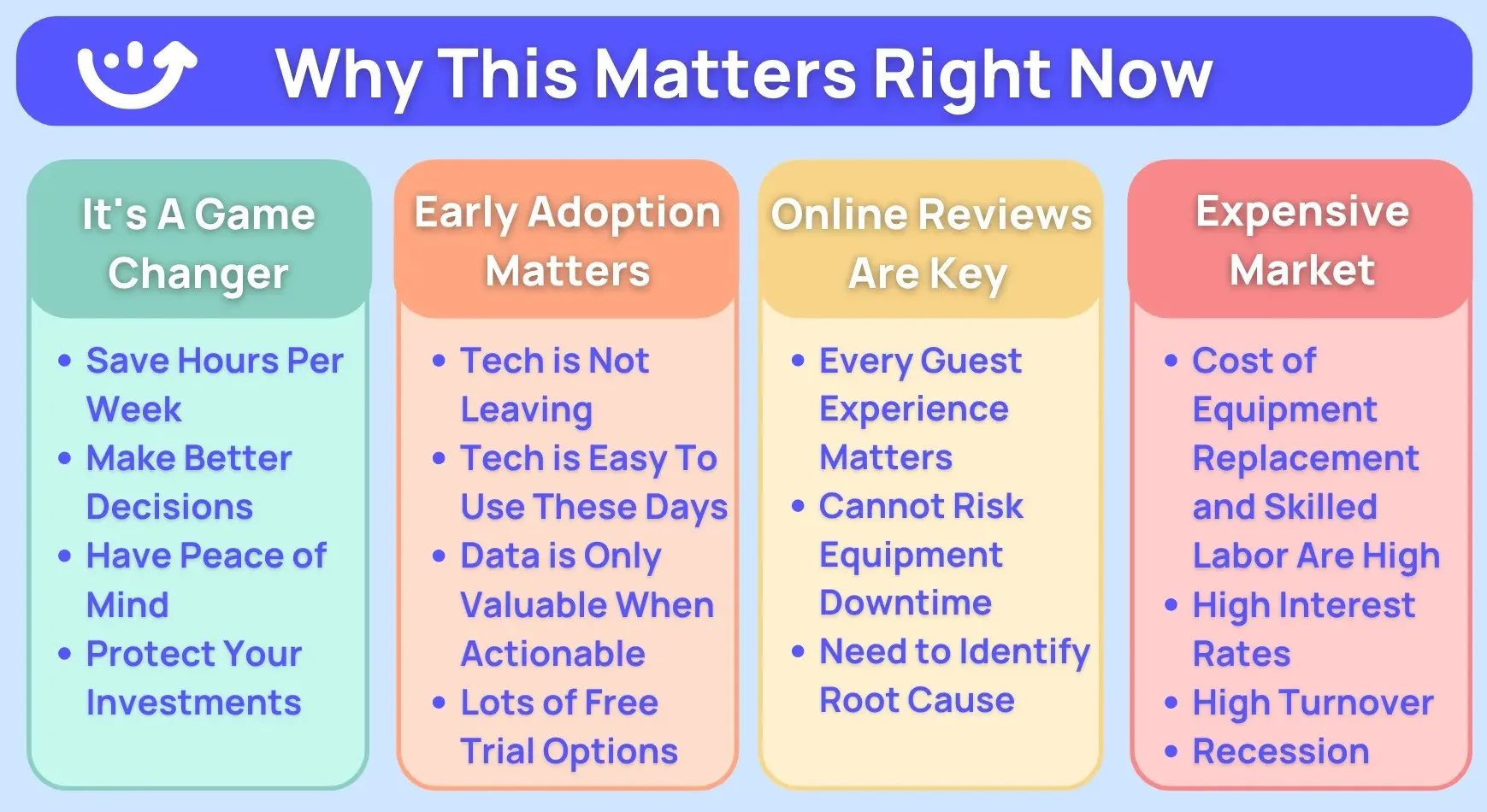
Furthermore, neglecting machine maintenance can also result in increased repair costs. If a machine is not maintained correctly, it is more likely to experience wear and tear, leading to more frequent repairs or even the need for complete replacement. This can be especially expensive if the machine is essential or cannot be easily replaced.
Businesses can follow machine maintenance best practices to ensure that their machinery is operating at peak performance. By proactively addressing potential issues and following the manufacturer's recommendations for maintenance, businesses can improve productivity, reduce downtime, and lower repair costs.
Recommended Resources:
- Equipment Management Software
- Maintenance Management Software
- 10 Best CMMS Software For Small Business In 2024
- Preventive Maintenance Software
- 5 Best Quality Control Checklist Apps For Businesses In 2024
- 8 Best & Free Digital Inspection Software in 2024
1) Lean on Preventive Maintenance, Not Reactive Work Orders
Preventive maintenance is a proactive approach to maintaining equipment that involves regularly scheduled inspections, cleaning, and repairs to prevent potential problems from arising. On the other hand, reactive maintenance, also known as breakdown maintenance, is a reactive approach that only occurs after an equipment failure or breakdown. Preventive maintenance is the key to keeping equipment in good working condition and avoiding costly breakdowns. By identifying and fixing potential issues before they occur, maintenance teams can save time and money, and prevent unexpected downtime.
In contrast, reactive maintenance can be costly, time-consuming, and can lead to unexpected equipment downtime, which can have a significant impact on productivity and profitability. In this article, we will explore the benefits of preventive maintenance and why maintenance teams are better off with it as opposed to relying on reactive work orders.
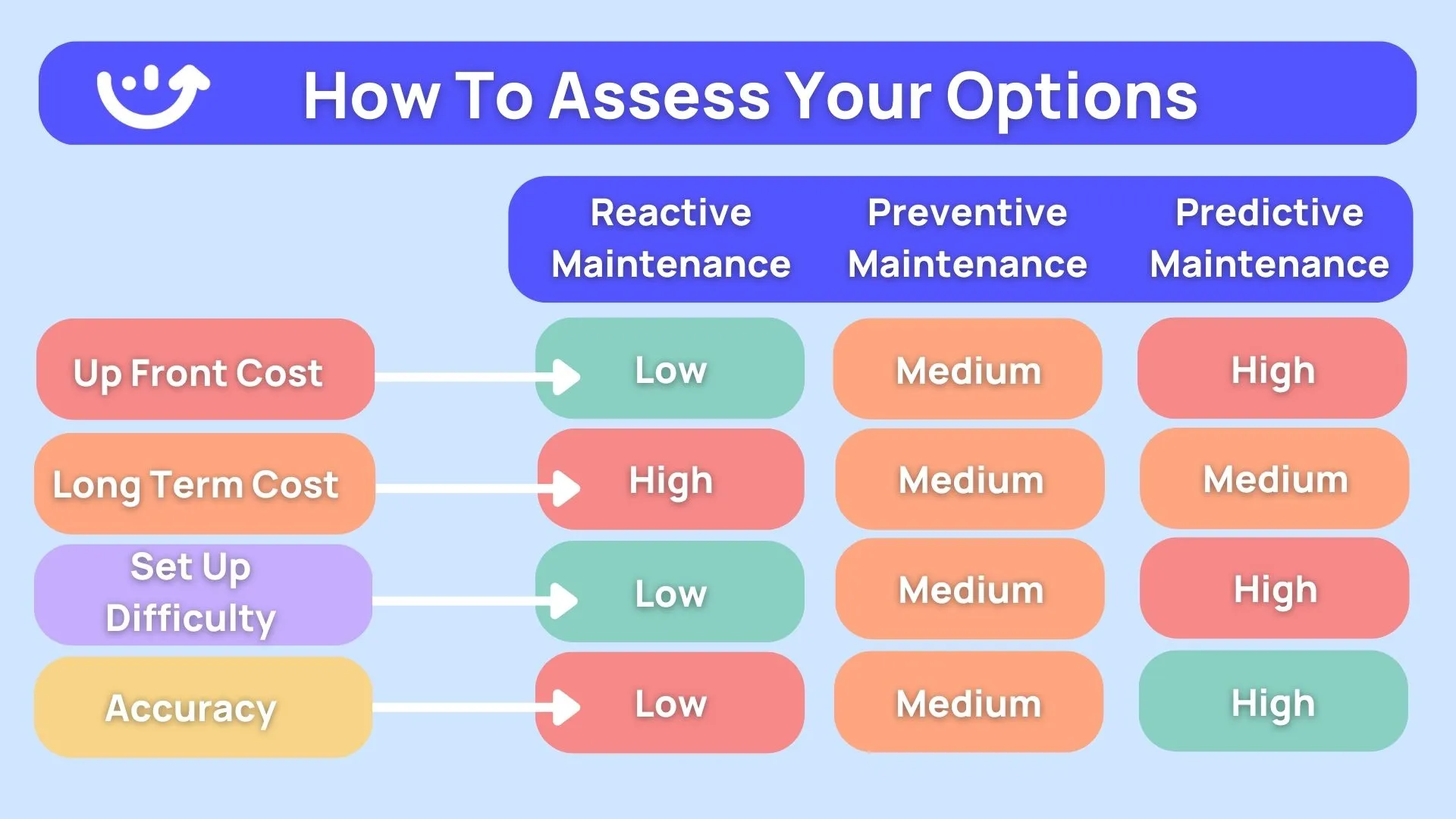
😢 Downside to Reactive Maintenance
📈 Increased downtime
Fixing problems as they occur will result in unexpected downtime that can significantly impact your business.
💲 Higher costs
Machinery problems are more costly to fix after they happen. This can lead to higher repair and maintenance costs overall.
🐌 Lower efficiency
Reactive maintenance requires more time and resources to fix problems that have already occurred rather than identifying and addressing potential issues before they occur.
🩹 Reduced safety
Businesses can suffer devastating losses when they wait for accidents or injuries to occur rather than identifying and addressing potential safety hazards.
Preventive maintenance is an alternative approach to machine maintenance. This involves regularly scheduled inspections, cleaning, and repairs. The goal of preventative maintenance is to identify and address potential problems before they occur to minimize downtime, extend the life of the equipment, and improve overall efficiency and performance.
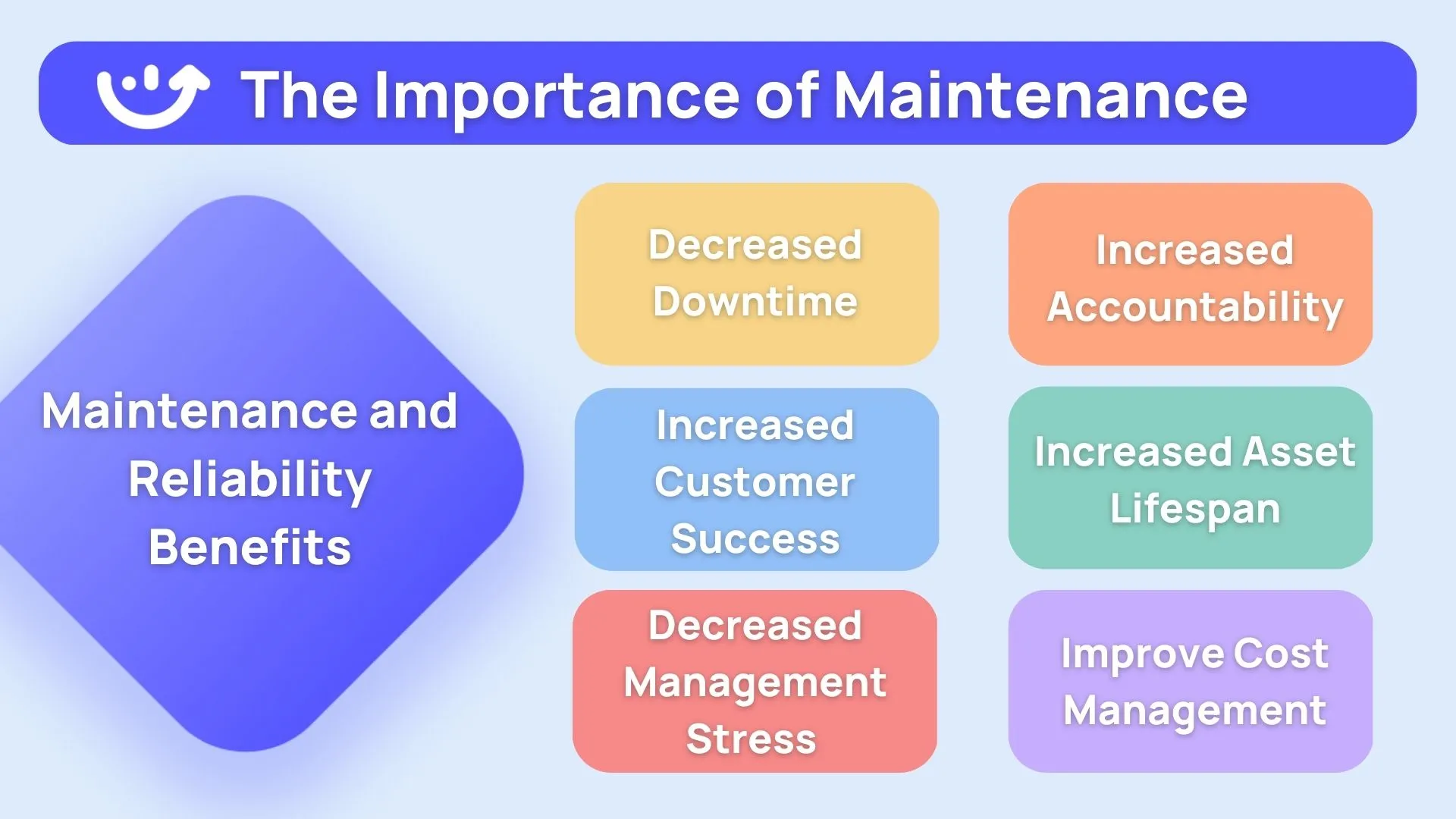
😄 Benefits of Preventive Maintenance
📊 Improved reliability
By regularly inspecting and maintaining equipment, you can identify and fix potential problems before they cause equipment failures or unexpected downtime.
🏎️ Increased efficiency
Well-maintained equipment tends to run more efficiently, which can lead to cost savings in the form of reduced energy consumption and fewer repairs.
🦺 Enhanced safety
Regular maintenance can help identify and fix potential safety hazards, such as frayed wiring or malfunctioning safety devices. This can help prevent accidents and injuries on the job.
💰 Cost savings
Preventive maintenance can extend the life of your equipment and reduce the need for costly repairs. It can also help you identify and prioritize equipment that may need to be replaced, allowing you to budget for those purchases in advance.
2) Follow the Manufacturer's Maintenance Recommendations
Following the maintenance recommendations from a manufacturer's guidelines is important because it ensures that the product will function properly and last as long as intended. These guidelines are based on the manufacturer's expertise and experience with the product, and they take into account factors such as the materials used, the expected usage, and the environment in which the product will be used. By following these guidelines, you can prevent damage to the product and avoid costly repairs or replacements. Additionally, following the manufacturer's guidelines can also help maintain the warranty and ensure that any potential issues are covered by it.
😉 Benefits of manufacturer's instructions for PPMs
📈 Optimal performance
Each machine is designed and built with specific maintenance requirements in mind. Following the manufacturer's instructions can help ensure that the device is maintained in a way that keeps it running at optimal performance.
🔧 Warranty compliance
Many manufacturers require that you follow their recommended maintenance procedures to maintain the warranty on the machine. Failing to do so could void the warranty and leave you responsible for paying for repairs out of pocket.
🥽 Safety
Following the manufacturer's instructions can help ensure the machine is maintained safely and reliably. This can help prevent accidents and injuries on the job.
🧬 Lifespan
Proper maintenance can help extend the machine's lifespan, and following the manufacturer's instructions can help ensure that the device is maintained in a way that maximizes its lifespan.
Taking the manufacturer's recommendations and putting them into standard operating procedures (SOPs) for your team is the best way to ensure accountability and consistency.
3) Keep a Detailed Record of Maintenance Tasks
Keeping a record of maintenance tasks and data is important for several reasons. First, it allows you to track the performance and condition of the equipment over time. This can help identify patterns and trends that may indicate a potential problem, allowing you to address it before it becomes a major issue. Additionally, having a record of when maintenance was performed and what was done can help you plan for future maintenance and budget for any necessary repairs or replacements.
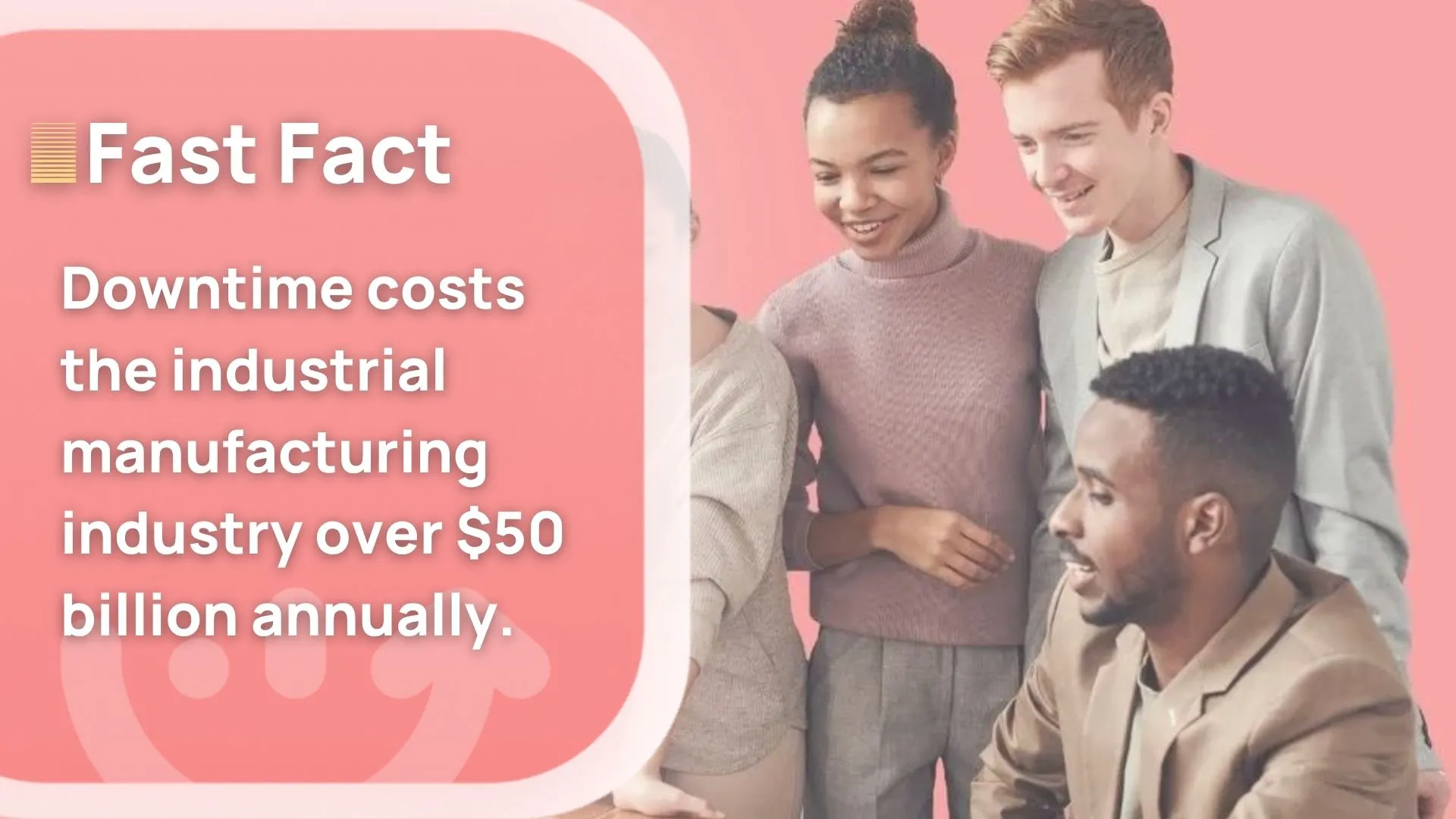
😀 Benefits of Maintenance Task Records
📅 Improved planning
You can better plan your resources and schedule future maintenance activities by keeping a record of all maintenance tasks. This can help improve the efficiency and effectiveness of your maintenance program.
🐾 Enhanced tracking
A record of maintenance tasks can help you track the performance and condition of your equipment over time. This can provide valuable insights into the maintenance needs of your equipment, allowing you to identify trends and prioritize repairs.
🦺 Enhanced safety
A record of maintenance tasks can help you identify potential safety hazards and address them promptly.
💪 Better decision making
A record of maintenance tasks can help you make informed decisions about the maintenance and repair of your equipment. For example, suppose you notice that a particular component is frequently failing. In that case, you will want to utilize the 50/50 rule and invest in a higher-quality replacement.
📓 Elements of Preventive Maintenance Documentation
📆 Date
It is crucial to record the date that maintenance tasks were performed, as this can help you track the performance and condition of your equipment over time.
🔩 Parts used
It is essential to document any parts used during maintenance tasks, as this can help you track the lifespan of those parts and plan for future replacements.
🚧 Issues identified or resolved
It is essential to document any issues identified or resolved during maintenance tasks, as this can help you recognize trends and potential problems, as well as track the effectiveness of your maintenance program.
✅ Checklists
Checklists ensure that all necessary maintenance tasks are completed consistently and accurately. They can also serve as a reference for future maintenance activities.
🖼️ Images
Images can help document maintenance tasks, as they can provide a visual reference for the condition of your equipment and any issues that were identified or resolved.
📝 Other documentation
Depending on the nature of your maintenance program, you may need to include other types of documentation, such as logs, reports, or certification documents.
4) Use High-Quality Parts and Lubricants
Proper maintenance is crucial for ensuring the longevity and performance of any piece of equipment. It not only keeps the equipment running smoothly, but it can also prevent costly repairs and replacements in the long run. However, not all maintenance practices are created equal. Using high-quality parts and lubricants is an essential aspect of effective maintenance, as it guarantees that the equipment will function properly and last as long as intended.
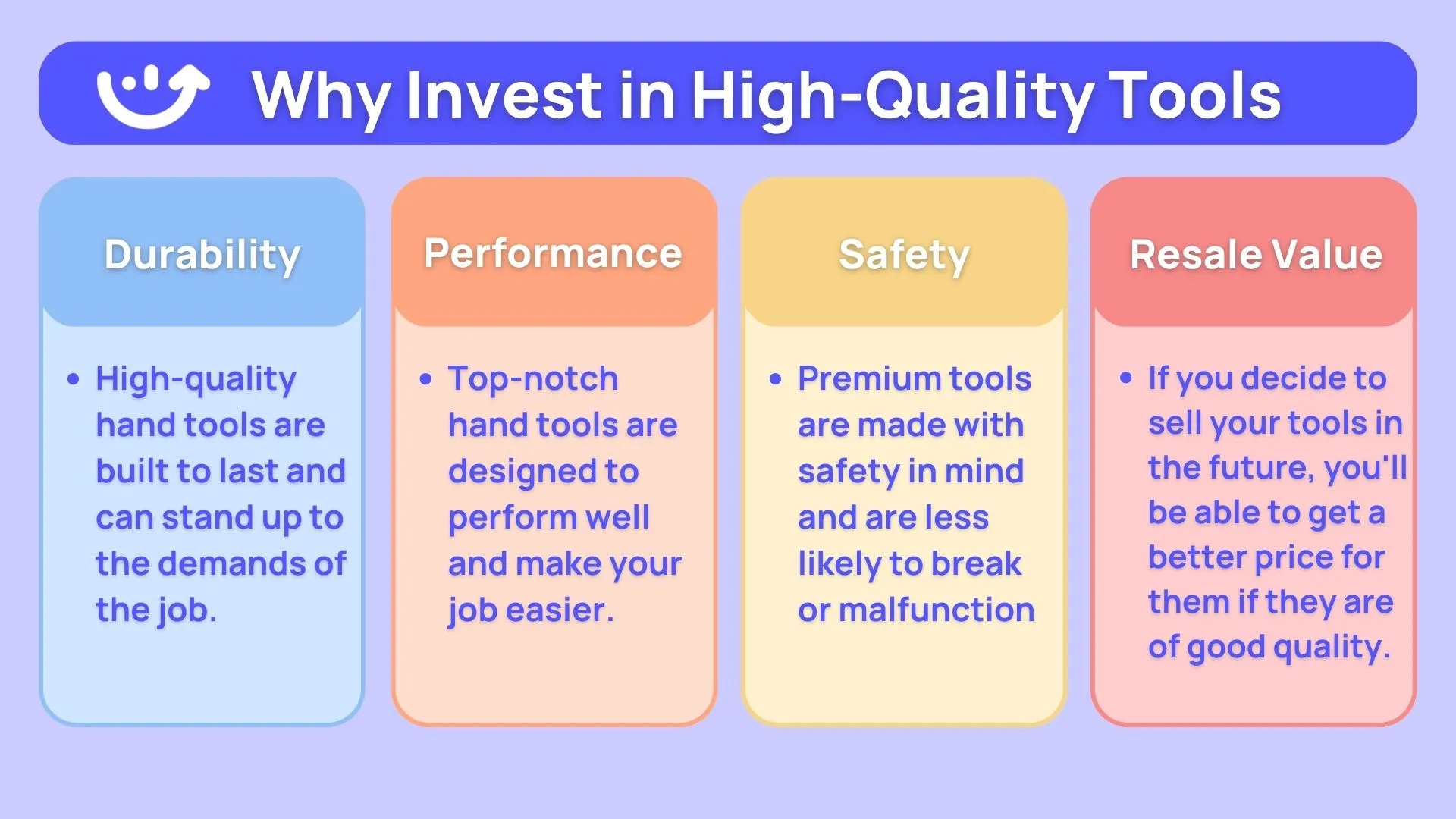
😃 Benefits of high quality parts and lubricants
💪 Enhanced performance
High-quality parts and lubricants are designed to meet the specific requirements of a machine and can help improve its overall performance.
🧬 Extended lifespan
Using high-quality parts and lubricants can help extend the lifespan of a machine by minimizing wear and tear on moving parts.
💲 Reduced maintenance costs
High-quality parts and lubricants may be more expensive upfront, but they can save you money in the long run by reducing the need for frequent repairs and replacements.
🥽 Improved safety
Using high-quality parts and lubricants can help reduce the risk of accidents and injuries on the job, as they are more likely to function correctly and without fail.
👥 Train Your Team
Having an adequately trained machine maintenance team can significantly improve these tasks' efficiency and effectiveness.
😊 Benefits of training maintenance team
🦺 Safety
Proper training can help technicians understand and follow safe work practices when performing maintenance tasks, reducing the risk of accidents and injuries.
📊 Efficiency
Training can help technicians understand how to properly perform maintenance tasks, which can help them complete tasks more efficiently and reduce downtime.
👍Quality
Training can help technicians understand how to properly maintain equipment and identify potential problems, which can help them provide higher-quality maintenance and extend the lifespan of the equipment.
💸 Cost savings
Proper training can help technicians identify and address problems before they become costly failures, which can help reduce maintenance costs.
🛻 Improved equipment performance
Training can help technicians understand how to properly maintain equipment and optimize its performance, which can help improve overall equipment performance.
🧠 Increased technician skill and knowledge
Training can help technicians develop the knowledge and skills needed to perform maintenance tasks effectively and efficiently. This can help technicians become more competent and confident in their work, leading to improved maintenance outcomes.
5) How Digital Tools Enhance Machine Maintenance Management
Digital tools help organizations track and manage their maintenance activities. This is beneficial for machine maintenance because it offers a range of features and benefits that can help your business improve the efficiency and effectiveness of its maintenance operations.
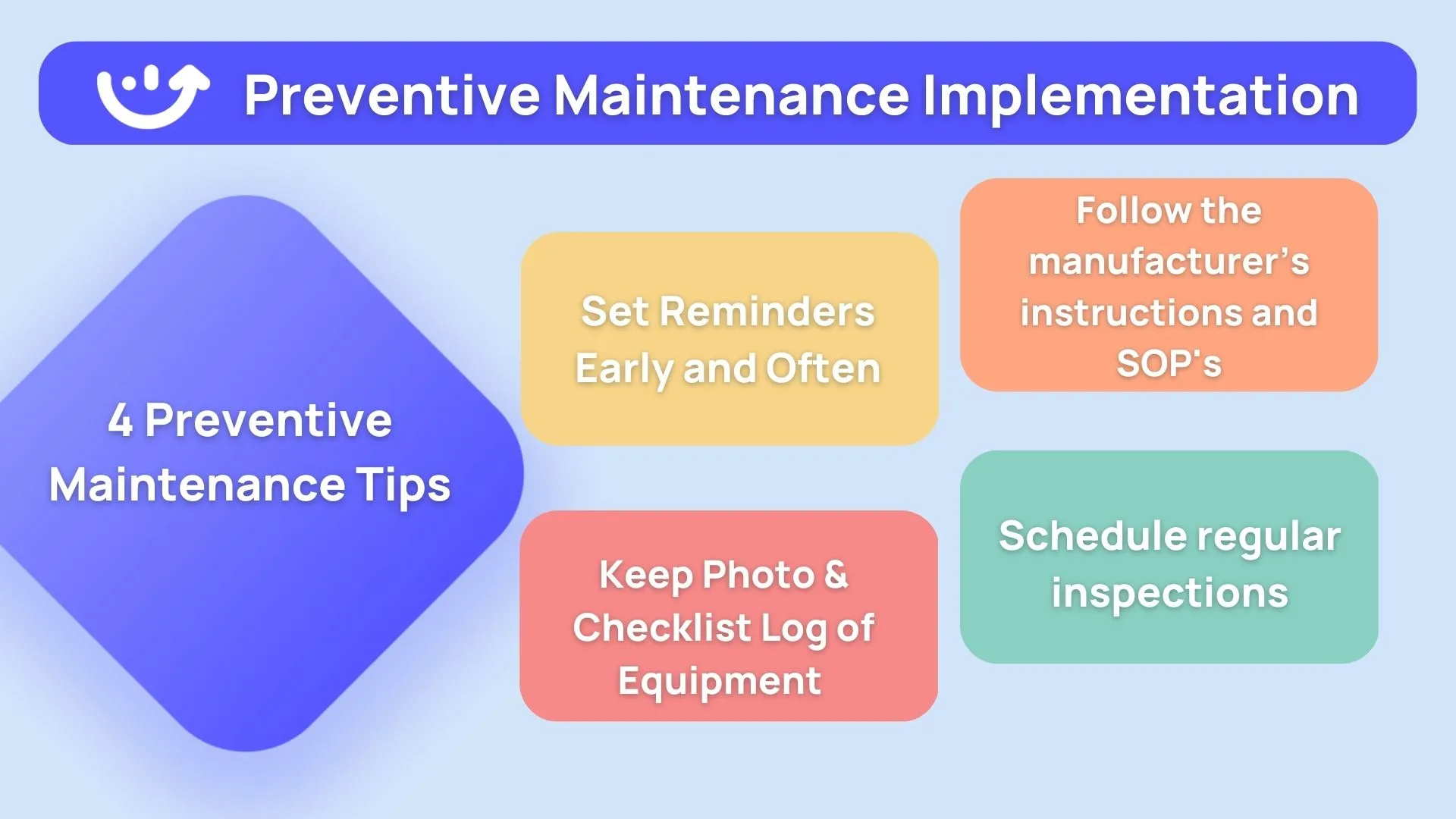
😃 Benefits of using digital tools for preventive maintenance
🔧 Improved accountability
Encourages maintenance task monitoring which can help improve the reliability and performance of your staff.
🤼 Greater flexibility and competitiveness
Digital tools can enable businesses to be more flexible and responsive to changing market conditions, as they can be accessed and used from any location with an internet connection.
😀 Transparency
Streamline maintenance activities by providing a clear, step-by-step guide for each task. This will reduce the time and resources required to complete maintenance tasks.
☁️ Centralized Database
A digital tool can facilitate communication between team members and provide a centralized location for all maintenance documentation, which helps ensure that everyone is on the same page and working towards the same goals.
🤝 Enhanced collaboration
Digital tools can facilitate communication and collaboration among team members, enabling them to collaborate more effectively and share information and resources in real-time.
📊 Enhanced tracking and reporting
A digital tool can help you track and record maintenance activities, providing valuable insights into your equipment's performance and condition. This can help you identify trends, prioritize repairs, and optimize your maintenance program.
A digital tool like Xenia can be particularly useful in this regard. It allows you to create custom checklists and SOPs based on the manufacturer's recommendations, which can help standardize maintenance processes and ensure that your team follows the necessary steps to keep your machines running smoothly and within warranty guidelines.
.webp)
%201%20(1).webp)