An improved understanding of the various maintenance levels enables better product maintenance. When deciding whether to bring in competent outside help or do an operation in-house, this categorization is a lifesaver as it guides you on critical data which addresses the ease of performing maintenance on a product.
The degree of expertise required to carry out processes, diagnose problems, and execute repairs increases as one moves up the complexity scale, which is used to categorize preventive and corrective maintenance.
Managers of facilities and maintenance can enhance productivity by assigning the appropriate workers to each job based on their degree of difficulty.
Priced on per user or per location basis
Available on iOS, Android and Web
What is a Maintenance Level?
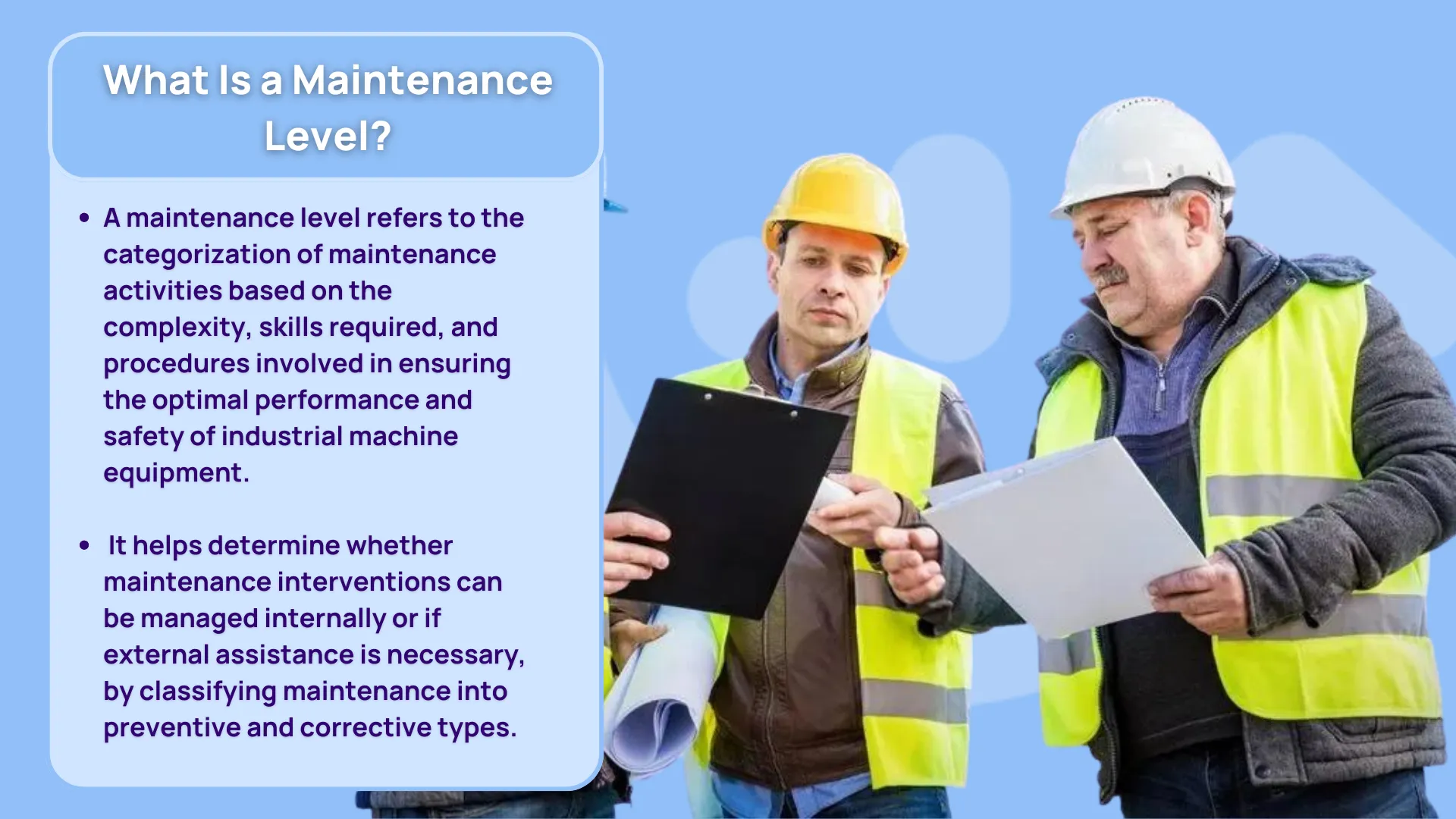
The goal of maintenance levels is to ensure that industrial machine equipment continues to provide optimal performance and safety, as well as maximum value. Attaining optimum maintenance requires a solid practical implementation of the various maintenance levels.
This categorization helps in figuring out what kind of skills are needed and what kind of procedures are necessary to complete an operation. It also helps in determining whether an intervention can be handled internally or if competent outside help is required.
There are essentially two types of maintenance i.e. Preventative and Corrective.
Preventative Maintenance Levels
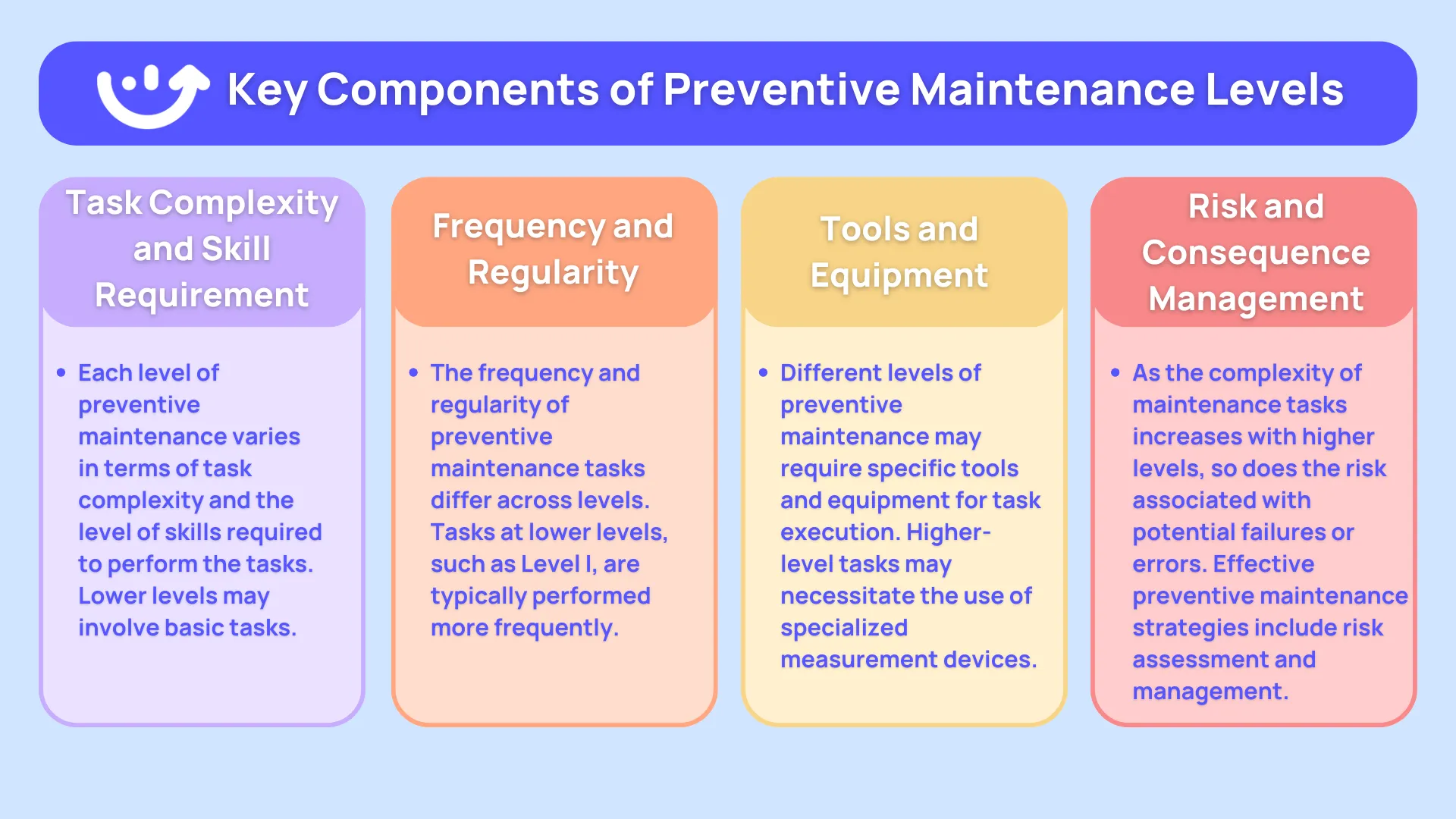
Any repair work done on machinery to lower the likelihood of failure is known as preventative maintenance.
All sorts of jobs, from those requiring only basic observational skills to those requiring advanced degrees and sophisticated measurement instruments, fall under this broad description. The following is a breakdown of the five types of preventive maintenance:
- Level I: Simple but essential upkeep like this can be performed with the help of machine-integrated support equipment safely and efficiently. Level one maintenance includes tasks like lubrication, condition monitoring, and filter clog removal, which should be done regularly.
- Level II: The effective performance of these treatments relies on the presence of appropriately competent and trained professionals, notwithstanding the relative simplicity of the processes involved. Regular maintenance includes tasks such as oiling moving parts, aligning pulleys or engines, and changing air filters that are difficult to reach.
- Level III: Performing preventive maintenance at level III involves more sophisticated operations that need the involvement of skilled personnel who are familiar with precise protocols. The use of external measurement devices, invasive tasks, and the gathering of technical parameters using specific collecting instruments are all examples.
- Level IV: Analysis of vibration and lubrication, usage of oscilloscopes, and infrared thermography are all examples of level IV jobs, which constitute the greatest degree of preventive maintenance that competent on-site personnel are likely to encounter.
- Level V: To do preventive maintenance at level V, machines may need to be disassembled in their whole and a great deal of specialized knowledge and tools are often only accessible from the equipment's manufacturer or third-party support systems.
Corrective Maintenance Levels
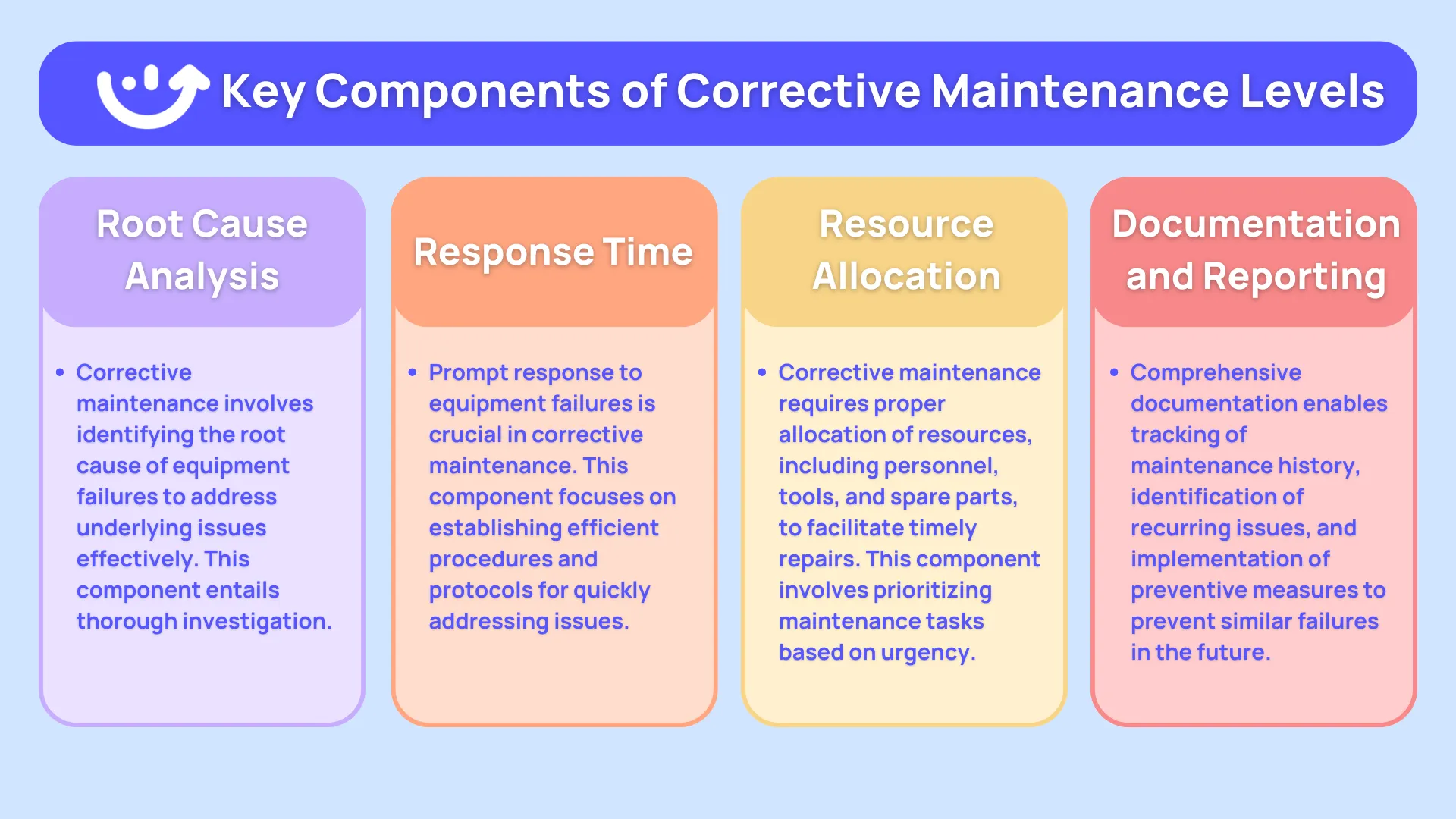
Any action needed to fix equipment and get it back to operating order falls under corrective maintenance. Just as with preventive maintenance, corrective maintenance levels signify escalating complexity in activities, necessitating more specialist knowledge and tools at higher levels. At each level, some tasks are suitable, such as:
- Level I: Fixing broken or obsolete parts on basic, readily accessible components and changing light bulbs are examples of this.
- Level II: Regular maintenance includes changing out air filters, fuses, and belts as well as old or worn-out components including chains, belting, slide rails, and rolls.
- Level III: Using specific diagnostic and measuring instruments, fixing refrigerant leaks, and replacing control cards, pumps, engines, and gears all fall under this category.
- Level IV: Complex diagnostic equipment are required for repairs including pump modifications and compressor valve replacements.
- Level V: Comprehensive refurbishment, geometrical or dimensional recovery, and sophisticated retrofitting equipment.
Level One Maintenance and CMMS
Simple interventions, essential and carried out on readily available components, constitute the first level of maintenance.
These tasks can be performed by the operator or individuals without specific training, without the need to open or disassemble the device.
They require very few consumables or replacement components, and if the necessary instructions are available, for example, in a handbook or on a screen, there is no specific danger to safety.
Adjusting interventions to match their corresponding maintenance level is seamless with an effective and user-friendly CMMS like Xenia.
For instance, a next-gen mobile CMMS simplifies attaching checklists to any piece of machinery and saves all the technical specs that repairmen need.
A community-based CMMS also facilitates accessing all the technical data offered by industrial suppliers and machine makers, essential for obtaining the parts needed for level 3 and 4 maintenance procedures.
For level 5 maintenance activities, it also streamlines the process of contacting manufacturers or authorized service providers.
What are Maintenance Management Strategies?
Several different kinds of sectors rely on maintenance management to keep their assets, equipment, and infrastructure running well and for a long time.
To maximize production while minimizing costs, good maintenance management is vital in all types of structures, including industrial plants, transportation networks, healthcare facilities, and residential buildings.
Unanticipated failures or breakdowns almost often cause major interruptions, income loss, and safety concerns in sectors where assets are fundamental to operations, such as transportation and manufacturing.
Maintenance is seen as a cost center by 59% of engineers and managers questioned, according to Plant Engineering's Maintenance Report.
Nonetheless, most people understand that maintenance is an i] investment that must be made to keep the machine running.
Recognizing the importance of maintenance in enhancing the overall capacity and efficiency of their facilities, 34% of respondents in the same research saw it as a profit center.
If businesses want to overcome maintenance obstacles and make sure their assets, equipment, and infrastructure are running at peak performance, they need a maintenance management plan. Implementing the right strategy allows firms to anticipate and resolve possible problems, limit unanticipated downtime, and lessen the likelihood of expensive failures.
According to the same data, a whopping 78% of the facilities examined had adopted a proactive maintenance strategy by implementing preventative maintenance.
Also, a CMMS helps organize and manage maintenance tasks; 61% of facilities utilize one. Curiously, 56 percent chose to deal with problems when they happen rather than try to avoid them in the first place.
6 Common Types of Maintenance Strategy

Preventative Maintenance Strategy
As previously discussed, preventative maintenance is a method of keeping assets in good working order by doing things like cleaning, adjusting, fixing, and replacing parts before they break or cause downtime.
Particularly for safety-critical assets and those that are vital to industrial output, this kind of approach helps to decrease the amount of corrective maintenance, which may become expensive.
Predictive Maintenance Strategy
This technique seeks to detect potential problems using data analysis and enable maintenance teams to rectify any flaws before equipment failure by employing monitoring instruments and software to analyze equipment performance.
Reliability-Centered Maintenance Strategy
In order to maximize the effectiveness of the maintenance strategy as a whole, this approach is utilized with the express purpose of making a facility more dependable and safer. In order to guarantee productivity via the use of cost-effective maintenance approaches, it is common practice to establish a unique plan for each asset.
Risk-Based Maintenance
To make sure that equipment's or facility's maintenance is optimized in a manner that lowers the chance of failure. This approach, which focuses on the most safety-critical assets, is beneficial for businesses seeking to execute the most cost-effective maintenance strategy because it gives priority to those assets whose failure would result in the greatest hazards. This right strategy is based on calculations and facts.
Run-To-Failure Maintenance Strategy
In this scenario, assets are left in operation until they malfunction, at which point no maintenance is performed. This technique can only be used on non-critical equipment when replacement parts and dependable personnel are available and when the failure of the equipment won't affect production or safety.
Scheduled Maintenance
Calender-based maintenance, as it is often called, will reduce the frequency of equipment failures even while it cannot stop catastrophic ones.
Experts advise using an 80/20 method, which is mostly based on the Pareto Principle and places 80% of maintenance operations on proactive work and the remaining 20% on reactive work, even if there is no "perfect" level of reactive maintenance.
Reducing failures reduces maintenance and capital expenses. Even while preventative maintenance isn't always the best maintenance plan, it does provide several benefits over a reactive strategy, including making it easier to identify the kinds of resources needed, how many, when, and for what duration.
Maintenance Strategy Centralization and Alignment
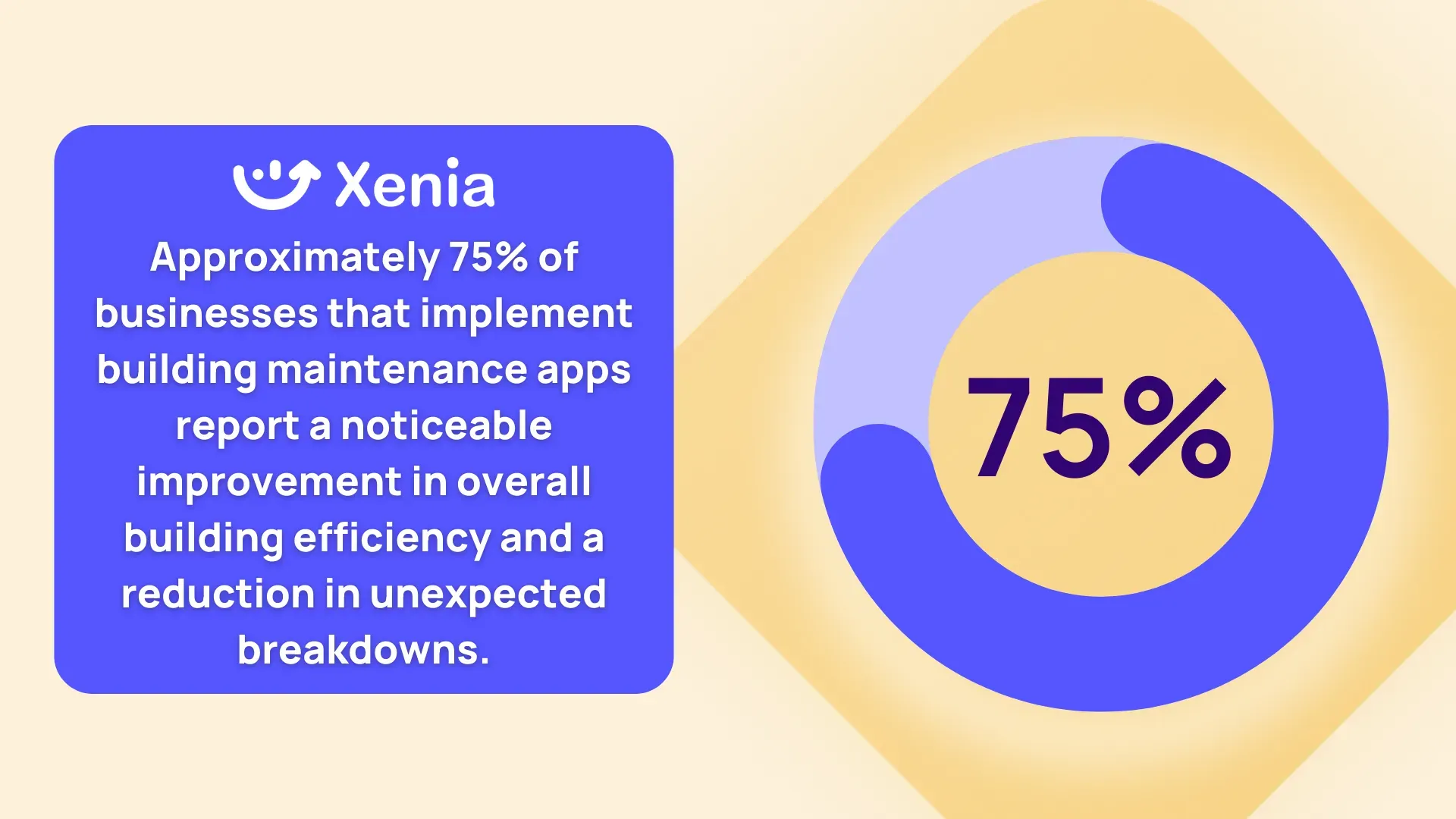
The alignment of maintenance strategies is crucial for the proper execution, scheduling, and budgeting of maintenance. This is because common equipment types across comparable applications need to be maintained to a minimal level.
Establishing a single maintenance department or team that is in charge of overseeing and coordinating all maintenance-related operations inside the business is the first step in the process of centralizing maintenance activities and resources. Developing a range of planned maintenance solutions in this manner leads to the following advantages and is essential to attaining maintenance excellence:
- Improved Efficiency
By consolidating maintenance tasks, businesses can conserve time and effort when servicing comparable pieces of equipment, find where they're lacking, and focus on improving those areas the most. This contributes to the reduction of redundant tasks, which in turn leads to enhanced efficiency and lower expenses.
- Better Resource Allocation
Centralization allows for better allocation of resources, including personnel, equipment, and supplies, ensuring that they are used effectively and efficiently. For instance, personnel can be transferred between assets effectively and efficiently due to a common approach and standards for maintenance.
- Standardization of Processes
Centralization improves the distribution of resources, such as people, machines, and materials, leading to more efficient and effective use of these assets. As an example, a standardized strategy and standards for maintenance allow for the quick and successful movement of staff across assets.
- Improved Communication
With a standardized maintenance plan template, departments and stakeholders may better communicate with one another, which in turn promotes teamwork and the exchange of information.
- Increased Safety
Equipment integrity and dependability may be enhanced, and the likelihood of accidents and injuries reduced, by centralizing maintenance processes. This helps to guarantee that safety procedures and protocols are regularly followed.
Implementing An Effective Maintenance Strategy in 7 Steps
If you've never prioritized maintenance before, it could appear like a difficult undertaking to create one. The process of creating a maintenance plan, however, can be boiled down into seven essential elements, which include assessing your present maintenance skills and handling the cultural shift that accompanies a new approach.
While the procedure may fluctuate for various firms with differing needs, every phase in the framework is essential to creating a precise and efficient maintenance plan that enables businesses to save expenses and increase productivity.
Step 1: Identify Critical Assets and Current Maintenance Capabilities
Identifying the assets that are vital to production and safety, together with your maintenance skills and maturity level, is the first step in developing an effective maintenance plan.
Simply put, how well-established are your current systems and procedures for maintenance, and how well are they serving your organizational needs?
As your team takes a more proactive approach, the ability to correct problems is only half the battle; planning, organization, and technical skills are all crucial for maintenance tasks.
Step 2: Analyze the Performance of Your Existing Operations
Before you can figure out what to do next, you need to take stock of your existing situation regarding the efficiency and effectiveness of your maintenance activities. By gathering and evaluating data on equipment availability, downtime locations, asset failure reasons, spending patterns, and return on investment with existing operations, you can establish maintenance goals that are both obvious and relevant for the future. All of these things need to be in sync with your operating facilities, company strategy, and long-term objectives.
Step 3: Decide on the Right Maintenance Approach for Your Assets
Making sure your operations are safe and cost-effective involves choosing the correct maintenance technique for each asset. The severity and state of your assets should guide your decision on whether to use a predictive, run-to-failure, or preventive strategy. When it comes to critical assets, it's important to choose the correct maintenance strategy for each kind of equipment failure so that the company can minimize the total cost of the failure.
Step 4: Develop a Clear Maintenance Plan
Finding a strategy allows you to develop a maintenance plan that is both efficient and successful, increasing the likelihood that you will achieve your goals. To carry out the maintenance tasks as planned, the plan must specify when and how often they are to be completed, as well as what materials and tools will be required. The maintenance crews can comply with these detailed and easy-to-understand instructions to perform their jobs well and know exactly what needs doing and why.
Step 5: Implement the Maintenance Plan
The next step is for the maintenance staff to put the plan into action. Planning and scheduling your maintenance entails dividing up resources, delegating responsibilities, and checking that everything is going according to plan. To avoid unnecessary setbacks and maximize the impact of your current efforts, it is recommended to use a disciplined project management method. Training is a great way to get everyone on board and make sure the changes stick, regardless of the size of the company.
Step 6: Monitor Results and Improve Your Strategy
It is critical to gather data to evaluate the outcomes of your ongoing asset performance monitoring in order to ascertain the efficacy of your maintenance approach. If you want to maximize production and improve safety in the future, you should use maintenance analytics and benchmarking tools to learn more about performance gaps, see where your time is going, and figure out if indeed it is the right strategy.
Step 7: Develop a Feedback Loop
Finding areas in your maintenance plan that might need improvement is one thing, but making sure your maintenance staff is consistently putting those suggestions into action is even more crucial.
To incorporate the results from evaluating the maintenance operations back into the maintenance plan and make improvements, it is necessary to develop a feedback loop. It is critical to regularly update and modify maintenance plans to meet changing company demands and objectives; these strategies should never be considered permanent.
Conclusion
Every company needs a systematic approach to maintenance management if it wants to succeed.
Spend less, get more out of your assets, and boost productivity with a maintenance management program. Asset management is already a breeze, but a computerized maintenance management system (CMMS) makes it much better.
The use of a CMMS could boost the efficiency of your maintenance operations by automating workflows and streamlining procedures.
Consider Xenia to remain ahead of the curve in maintenance management and discover more about how a CMMS can benefit your organization.
.webp)
%201%20(1).webp)