The health and fitness industry is booming, but so is competition and client standards.
From world-class corporate gyms to boutique local fitness centers, there is one common criteria that gyms must uphold to keep customers coming back; equipment maintenance and facilities management.
Priced on per user or per location basis
Available on iOS, Android and Web
Due to heavy use, gym equipment is prone to issues, and out-of-order machines are a primary driver of complaints and negative online reviews. Furthermore, facilities such as locker rooms, saunas, tanning beds are a core differentiating factor from at-home options, thus must be pristine to keep customers happy.
This guide covers everything you need to know about gym equipment maintenance and facilities management so that you can grow your business effectively.
Recommended Resources:
- Gym Equipment Maintenance Software
- Equipment Management Software
- Maintenance Management Software
- 10 Best CMMS Software For Small Business In 2024
- 8 Best & Free Digital Inspection Software in 2024
What is Gym Maintenance Management?
Gym maintenance management is the process of ensuring that gym equipment and facilities are clean, safe and reliable for use. Effective maintenance management programs cover both preventive and corrective maintenance as well as cleaning and inspection protocols for quality control.
This typically includes the regular inspection, cleaning, and repair of gym equipment as well as managing the inventory of parts used to repair broken equipment.
Gym equipment maintenance management is necessary to keep the public safe from injury due to faulty equipment as well as to prevent damage to the building structure due to excessive wear and tear on weight machines and other pieces of exercise equipment.
- Streamline Gym Asset & Equipment maintenance with Xenia. Book a Demo Today
The core benefits of gym equipment maintenance management are:
1. Safety
Lawsuits are the boogieman of any gym owner. Proper maintenance management and quality control can alleviate risk associated with heavy, moving equipment. Routine safety inspections on all machines ensure that faulty equipment is not the root cause of personal injury.
Documenting safety checks also helps protect you from liability if the clients injure themselves from a machine due to their fault and try to blame it on lack of management or machines.
2. Quality Control
Customer satisfaction is the epitome of any ongoing business’s success.
As a business owner, you need to ensure that your clients are happy and satisfied with how you run your business; otherwise, they will leave, and you won't be able to convince them to come back.
Pulley machines and saunas are prone to breakdowns, which cause customer complaints and tarnish brand image. It is essential for gym owners to provide preventive maintenance measures to minimize downtime risk, as well as reactive protocols to get the equipment up and running as soon as possible.
Furthermore, gym owners must keep their facilities clean and safe to navigate. Effective maintenance management sets standard operating procedures and task tracking to power regular facilities inspections that ensure the property is free from hazards and litter.
3. Maximize Equipment Lifespan
The primary costs to gym owners is the fixed cost of equipment and facilities. This means that to protect your bottom line, it is crucial to extend asset lifespan as much as possible.
The best way to do this is to create preventive maintenance schedules for each asset and ensure your teams conduct and record the maintenance for management to review.
Over the long run, effective maintenance is what protects your gym’s bottom line.
4. Minimize Equipment Downtime
Equipment being down for one day is much less destructive than that same equipment being down for a week or longer. Without the proper processes in place, it is common for pulley equipment and saunas to remain out of order for weeks, causing clients to reconsider why they are paying for a membership.
Effective maintenance programs have protocols waiting and ready to be deployed in the event of equipment failure. This speeds up the time to resolution and creates a better, safer client experience.
What are the Steps of the Gym Equipment Maintenance Process?
Proper maintenance management spans many processes, thus can be difficult to organize and measure. Mastering this is crucial to protect the bottom line and keep clients coming back each day.
Here are the steps included in the gym equipment maintenance process, which we will then discuss in detail.
- Equipment Cleaning
- Preventive Maintenance
- Equipment Repair
- Maintenance Data Tracking
- Equipment Replacement
Let's look at these steps and find out how you can create a gym equipment maintenance process for your own business.
1. Equipment Cleaning
The first step in a gym equipment maintenance process is thoroughly cleaning the equipment. Every piece of equipment comes with a manufacturer's guide on cleaning best practices but there is significant overlap between types of equipment.
The key to effective cleaning is communication. Creating standardized process checklists for each type of equipment ensures that the job is done right no matter who is doing the work. This is critical due to high employee turnover and lack of detailed training.
2. Preventive Maintenance
Preventive maintenance is required as a baseline activity when it comes to maintaining your gym equipment. Typically, gyms will create a calendar for each asset that has weekly, monthly, semi-annual and annual maintenance to be conducted. These schedules are assigned to maintenance staff to ensure that work is being done proactively. Digitizing this process empowers data driven understanding of facility health that drives better decision making.
3. Equipment Repair
As a gym owner or even a business owner, you know that no matter the measure, there will come a day when equipment will break down. This is normal, however excessive downtime is not.
Regular inspections increase the likelihood of management seeing symptoms that lead to equipment failure before it occurs. This allows management to either proactively fix the problem by replacing a part, or buying the replacement part in advance so that it is on hand if (and when) the breakdown happens.
A good repair can extend the life cycle of your machine which helps you to get the maximum value for your investment. The key is to improve timing to reduce client disruption. With inventory, install procedures and proper communication channels, equipment downtime is significantly reduced and clients are kept happy.
4. Maintenance Data Tracking
Every time your equipment is cleaned, inspected or worked on, there should be a digital record of that work. Without this, management is left in the dark and equipment is more likely to experience a failure. Task management solutions, like Xenia, ensure that protocol is followed and work is recorded every time whether it is a preventive or reactive work order.
5. Equipment Replacement
As with any asset, there comes a point where repairing gym equipment is no longer advantageous and replacement is the primary option.
Organized data helps management know when it is time to replace a piece of equipment. With proper record, management can see how often the equipment has broken down, the cost of those repairs and the total downtime the equipment has experienced.
With this data, the cost of replacement can be properly compared to the cost of continual repair. Without the data, equipment may be replaced too early or kept in the facility beyond the useful life.
How to Create a Gym Preventive Maintenance Schedule
Let's talk about the five steps included in creating a gym preventive maintenance schedule.
1. Taking Inventory of All of your Assets
The first thing to do while creating a gym preventive maintenance schedule is to take inventory of all of the assets at your disposal. While taking inventory, note the assets that require routine maintenance.
Here are some of the questions you need to ask yourself about an inventory item while creating a maintenance schedule.
- Is the machinery in question critical to the success and failure of the organization?
- Are there failure warning signs that can be identified with regular inspections and maintenance?
- How difficult is it to source a part or repair labor to correct a failure?
- How much time should be devoted to preventative maintenance on this equipment?
2. Prioritize your Assets
Limited resources is a common problem for gym owners to solve. Use the answers to the inventory questions to prioritize and rank equipment from most to least important. In general, focus on the most expensive, most critical equipment before moving on to the rest.
3. Determining Ideal Preventive Maintenance Intervals
As we discussed above, all of the machines in your arsenal are different and will require different maintenance intervals
You should use the asset's manufacturing manual as a guide and the historical maintenance data in your database to determine the appropriate interval for each piece of machinery at your establishment.
4. Schedule Recurring Maintenance Tasks
The next step is to make sure that you track and manage all of the maintenance tasks that must be performed and schedule them via your maintenance tracking software. This reduces the need to manually inform your team and, instead, notifies the proper employee at the right time with the necessary resources attached.
5. Monitor and Improve Your Schedule
Last but not least is monitoring all the schedules you set for your machinery. It is important to check up on these schedules so that you can have an idea about their effectiveness and whether or not you need to change anything to make the schedule more effective.
Benefits of Digitizing Gym Equipment Maintenance Management
Here are the benefits you can get by using software to manage your gym equipment maintenance process.
- Manage work orders efficiently
- Eliminate paperwork
- Reduce downtime and repair costs
- Plan and schedule preventative maintenance
- Manage spare parts inventory
- Enhance productivity
- Increase safety
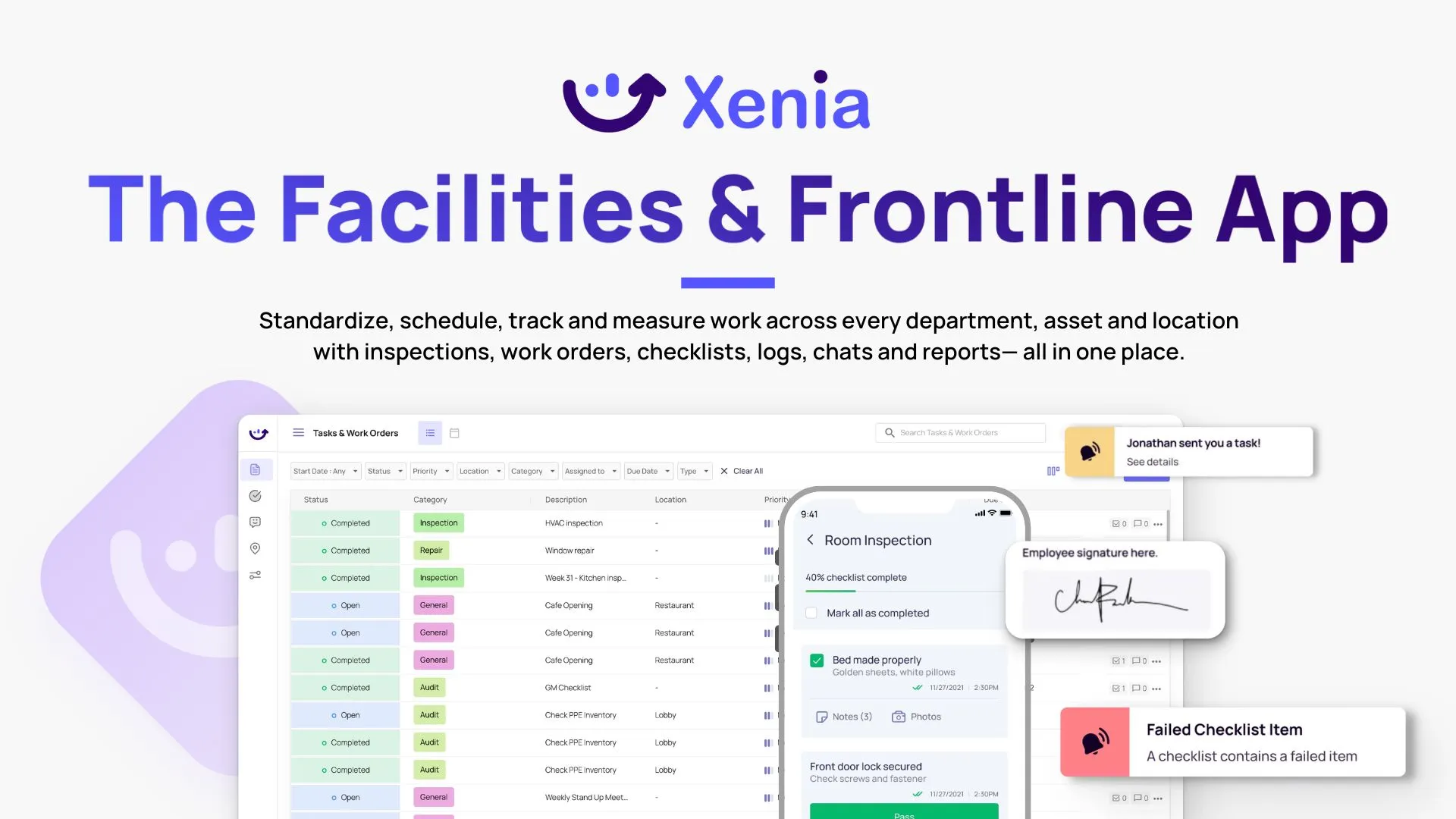
Use Xenia for Gym Equipment Maintenance and Facilities Management
Xenia is one of the best workforce and maintenance management applications in the market right now.
The application is perfect when it comes to managing all your gym maintenance management tasks. With its checklist builder, you can easily create standard procedures for every asset. There is even a pre-built library to get you started on day one.
Xenia powers preventive maintenance calendars to streamline planning and communication. In the event of equipment failure, the platform enables quick task assignment to handle work order management with data tracking, checklist, photo and note attachments. Xenia also has built in chat to loop in team mates and update management on progress.
Xenia is designed specifically for frontline ease of use with powerful features in a simple app across desktop and mobile devices. Check out the free checklist library or start your free trial today to get started improving your gym operations!
.webp)
%201%20(1).webp)