An equipment maintenance log book, sometimes underestimated, plays a fundamental role in the complex daily routine of a maintenance manager. It serves as a repository of crucial information about your machinery's health and history, streamlining the process of managing substantial equipment.
The importance of an equipment maintenance log book transcends industries, from manufacturing and construction to healthcare and hospitality. These sectors heavily rely on their machinery, which necessitates vigilant care and regular maintenance.
Moreover any high-quality machine maintenance log book holds the key to detailed records of all maintenance activities, irrespective of their scale.
Envision not just managing, but significantly improving the performance, safety, and longevity of your machinery through your maintenance log book. This resourceful tool can guide you through the complicated terrain of maintenance management, helping you evade obstacles and streamline your operations.
Priced on per user or per location basis
Available on iOS, Android and Web
In this comprehensive guide, we'll dissect the intricacies of the maintenance log book. We'll delve into its essential role in maintenance management, understand its benefits, and show how it enhances operational efficiency and reliability.
Let’s dive into the chapters that follow, where we unpack the concept of the maintenance log book, explain its critical role, and present best practices for keeping one.
We'll also explore how it's evolving with the digital age and introduce you to powerful tools like Xenia, designed to revolutionize your approach to maintenance log book management. Are you ready to turn the page?
Let's begin.
.webp)
Understanding the Equipment Maintenance Logbook
An equipment maintenance log book is a detailed document that archives all maintenance activities related to a specific piece of equipment. Much like a health record for your machinery, it captures vital data points such as the maintenance date and time, the technician assigned, and the tasks executed.
In that order, a machine maintenance logbook, or an equipment maintenance log serves as a communication tool between maintenance staff and other stakeholders.
They provide a shared source of information that can be accessed by technicians, supervisors, and managers. It facilitates effective communication regarding equipment status, maintenance schedules, and any issues or observations noted during inspections.
If managed meticulously, these log books then become instrumental in preventive maintenance strategies, shedding light on the equipment’s maintenance trajectory.
Here’s a quick look into the core components of a typical equipment service log:
Time Stamps
The date and time of each maintenance action play a crucial role in a maintenance log book. These timestamps help track maintenance frequency and aid in scheduling future preventive maintenance, optimizing equipment health.
Ensuring Accountability
By recording the name of the maintenance technician, accountability is ensured and a point of contact is established for follow-ups. This data proves instrumental in fostering a culture of responsibility and maintaining high standards of maintenance.
Recording Detailed Tasks
A thorough record of maintenance tasks performed is a key element in the maintenance log book. This record helps diagnose future issues and identify recurring problems, thereby improving the overall maintenance strategy.
Keeping Track of Replacement Parts
Recording replacement parts used during maintenance is critical for effective inventory management. This record aids in planning future parts procurement and helps anticipate potential part failures, minimizing equipment downtime.
Capturing Observational Insights
Recording observations made during maintenance serves as an early warning system for future issues. These observations aid in preventive measures and deepen understanding of equipment behavior, thereby promoting operational efficiency.
A Tool for Effective Management Strategies
A meticulously maintained maintenance log book becomes an indispensable tool for predictive and preventive maintenance strategies. Providing a comprehensive overview of the equipment's history, it supports informed decision-making and boosts the effectiveness of maintenance management.
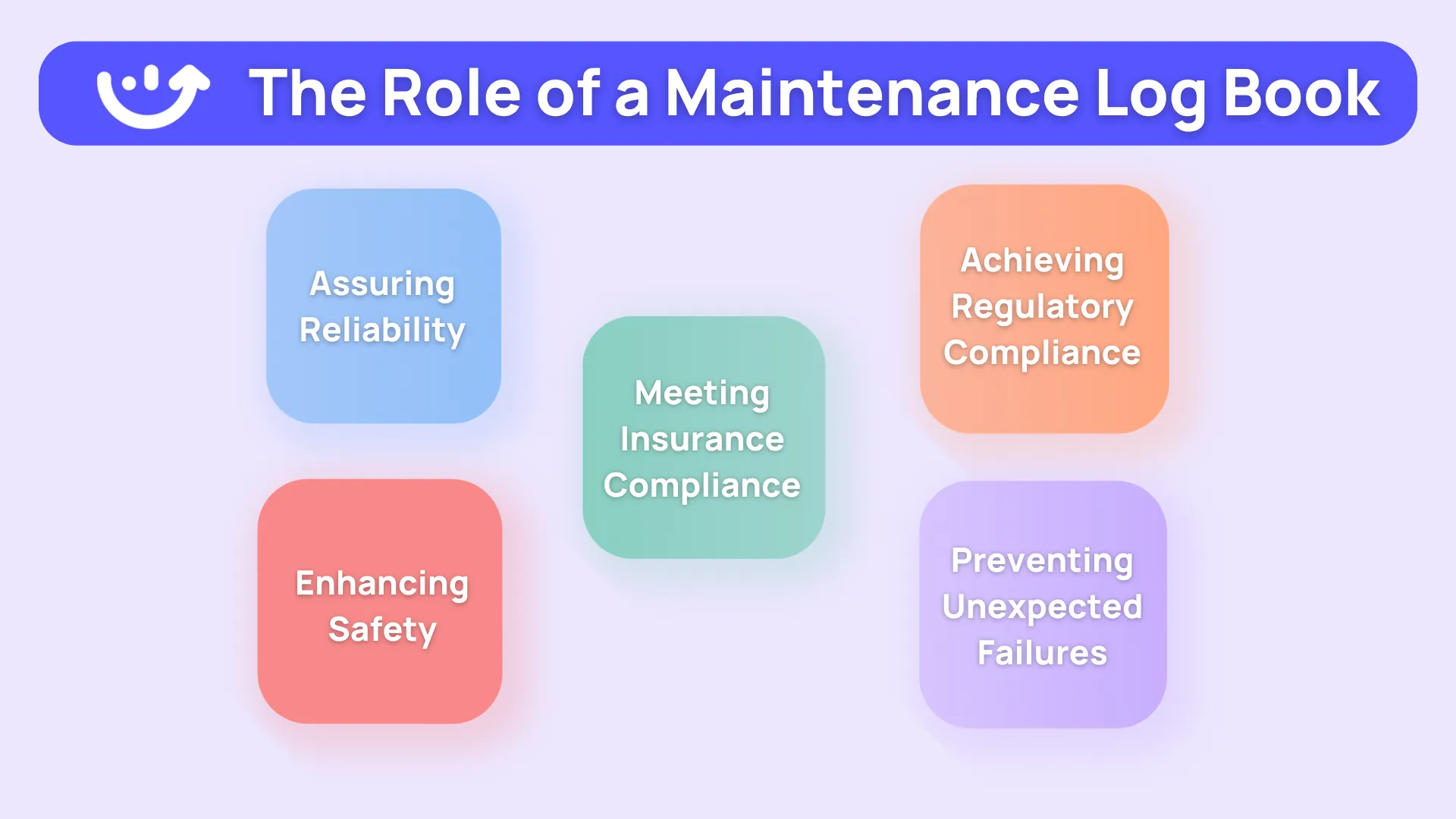
The Role of a Machine Maintenance Log Book
A regularly updated maintenance log book is pivotal in prolonging the lifespan of your machinery.
Assuring Reliability
A detailed maintenance log book serves as a reliable source of insights into your equipment's condition. It helps maintain, and even improve, equipment reliability by providing a thorough record of all maintenance activities.
This consistent tracking of machine health prevents unexpected breakdowns and aids in maintaining a steady workflow.
Enhancing Safety
The safety of operators and other personnel is paramount in any industry. Maintenance log books can reveal potential safety concerns before they grow into significant problems, thereby enabling preemptive action and ensuring safe equipment service log and/or said operation.
Achieving Regulatory Compliance
Regulatory compliance is crucial in industries that heavily depend on machinery. A comprehensive maintenance log book serves as tangible proof of adherence to maintenance standards and regulations, thus protecting your organization from potential penalties.
Meeting Insurance Compliance
Insurance policies often require proof of proper preventive maintenance, and a well-maintained maintenance log book provides this evidence.
These equipment service logs serve as verifiable proof of regular and appropriate preventive maintenance, meeting the requirements set by insurance providers.
Preventing Unexpected Failures
Unexpected equipment failures can result in expensive repairs and prolonged downtime. A detailed maintenance log book can help anticipate potential issues, allowing for preventive action, minimizing costly breakdowns, and improving productivity.
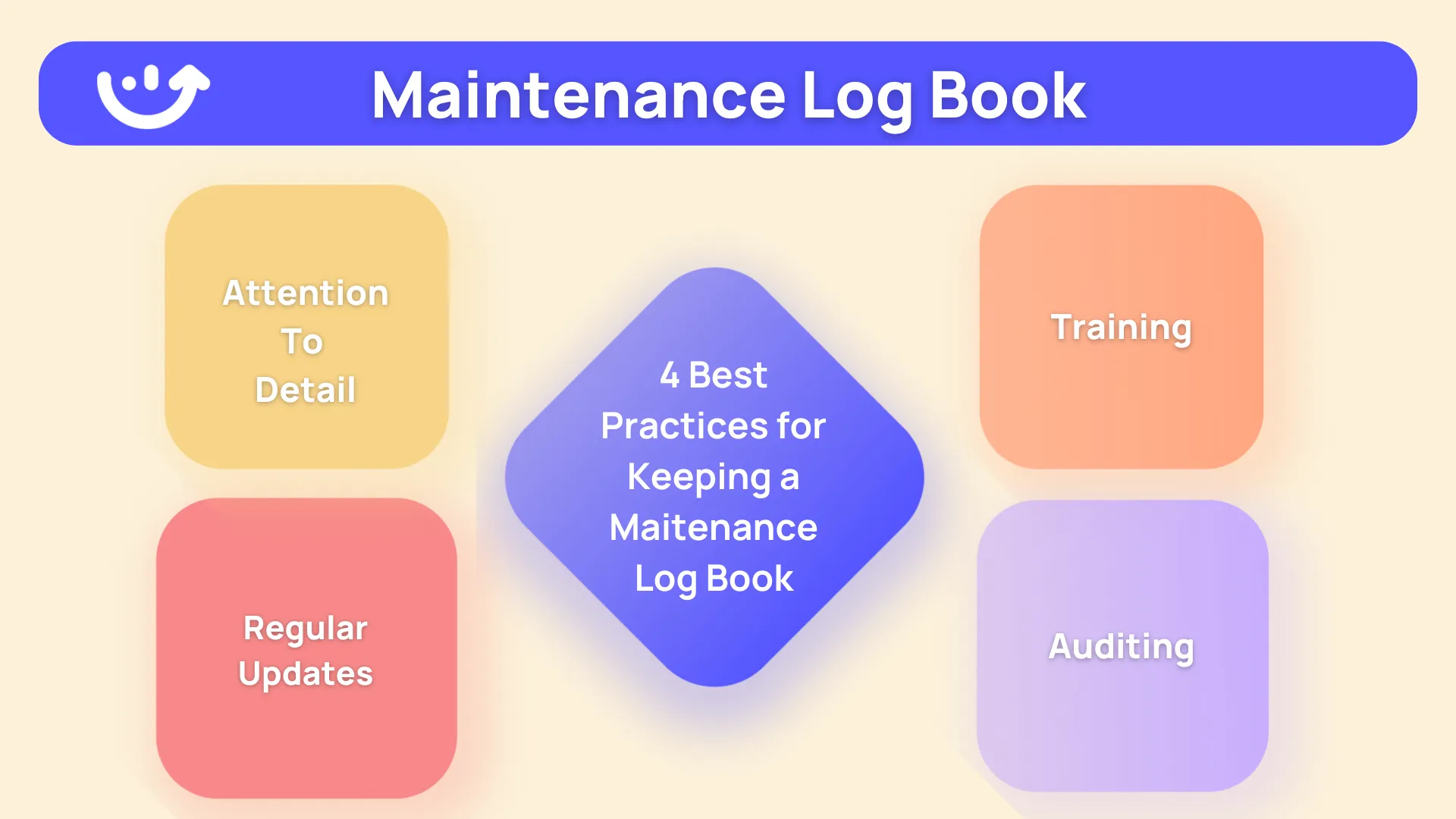
Best Practices for Keeping a Maintenance Log Book
Maintaining a maintenance log book requires a commitment to consistent record-keeping.
It's crucial to diligently log all maintenance activities, no matter how insignificant they may seem. Consistent recording contributes to a reliable and useful log book, which proves instrumental in effective planning and decision-making.
1. Attention to Detail
Attention to detail includes accurately recording all relevant data such as the date and time of maintenance, personnel involved, tasks performed, and any replacement parts used.
Also, any observations or anomalies noted during maintenance should be recorded, allowing potential issues to be detected early and preventive measures to be enacted.
2. Regular Updates
Keeping the log book up-to-date is crucial for its effectiveness.
The maintenance manager's role involves ensuring that the log book reflects the most recent maintenance activities.
Regular updates contribute to the accuracy and reliability of the log book, making it a beneficial tool for preventive maintenance strategies and compliance requirements.
3. Training
Regular training sessions can instill an understanding of the importance of these log books among team members.
These sessions should emphasize the critical role that log books play in preventive maintenance, equipment longevity, and regulatory compliance.
Each team member should know how to accurately contribute to the log book.
4. Auditing
Regular audits of the maintenance log books can maintain their integrity. By reviewing the log books, any inconsistencies or gaps can be identified and corrected, ensuring adherence to log book practices.
Moving to Digital Maintenance Log Books
In a world of rapid digital innovation, the use of digital software solutions for managing maintenance log books has become a necessity.
These solutions come packed with features designed to meet the needs of contemporary maintenance managers, offering a comprehensive platform to simplify and improve maintenance management processes.
Key characteristics of digital solutions for maintenance log book management include:
UI UX Dynamics of Equipment Service Logbooks
Modern digital solutions are user-centric, with intuitive interfaces that simplify the task of logging maintenance activities. This user-friendly design ensures that all team members, regardless of their technical proficiency, can efficiently interact with the platform.
Real-Time Updates
One major advantage of digital tools is the ability to provide real-time updates.
This feature allows for immediate documentation of maintenance activities, giving a real-time overview of equipment health.
Secure Data Storage
Digital log book platforms ensure that data is securely stored and easily accessible.
Data Analysis Capabilities
Digital solutions allow maintenance managers to quickly analyze log book data to uncover useful insights.
Accessibility
Digital solutions can be accessed anytime, anywhere, offering greater flexibility and faster information retrieval. This is particularly beneficial for teams working across multiple locations or shifts.
Integration with Existing Systems
Modern digital tools are designed to integrate seamlessly with existing systems, improving data consistency and reducing the likelihood of data duplication or loss.
Many facilities have transitioned to digital solutions for their maintenance log book management, enjoying the benefits of a streamlined, digitized process.
The implementation of such digital tools ensures that maintenance log books are accurately maintained and easily accessible, thus improving maintenance strategies and optimizing equipment performance.
.webp)
Unleash the Power of Xenia in Maintenance Log Book Management
How can we elevate the maintenance log book management even further?
It’s a bleeding-edge tool that brings numerous advantages to your maintenance log book management strategy, thereby making the life of a maintenance manager much easier.
Key Features of Xenia - The No. 1 Equipment Service Log Book Software
1. Streamlined Data Entry
Xenia greatly simplifies the process of logging maintenance activities.
With its intuitive interface, data entry is a breeze, making it easy for team members of all technical proficiencies to contribute accurate, timely information.
2. Automated Analysis
You can effortlessly analyze your maintenance log book data to identify trends, forecast equipment failure, and optimize maintenance schedules.
3. Seamless Integration
Xenia is designed to integrate seamlessly with existing systems, creating a unified, reliable data repository.
This not only enhances data consistency, but also minimizes the risk of data duplication or loss. This is a significant advantage in today's interconnected business environment where smooth data flow is key to efficiency.
4. Mobile Accessibility
Whether you're at the office or on the go, you can easily access your maintenance logs, schedule preventive maintenance, or update records.
5. Improved Compliance
Staying on top of regulatory compliance can be a daunting task.
Xenia's automated tracking and reporting features simplify this process, making it easier to demonstrate adherence to maintenance standards and regulations.
6. Automated Scheduling
One of the most noteworthy features of Xenia is its ability to automate scheduling for maintenance tasks.
After inputting the necessary data related to equipment health and maintenance frequency,
Use Xenia To Manage Your Maintenance Log Book Today!
The importance of a diligently maintained log book can't be overstated.
The shift from traditional paper and pen methods to an organized digital platform can enhance your operations, offering a seamless transition with benefits that span far beyond mere record-keeping.
Upgrade your strategy, improve your operations, and ensure the longevity of your machinery with Xenia.
.webp)
%201%20(1).webp)