An equipment maintenance log can become the beacon of clarity in the complex daily routine of a maintenance manager.
This tool, often overlooked, is pivotal in bringing order and efficiency to managing heavy machinery.
Priced on per user or per location basis
Available on iOS, Android and Web
Each equipment maintenance log acts as a detailed record, a time capsule holding invaluable data about your equipment's health and history.
The role of an equipment maintenance management log in industries like manufacturing, construction, healthcare, and hospitality cannot be overstated.
Machinery, the heart of these industries, requires vigilant care and consistent upkeep.
In that order, an equipment maintenance management log proves its worth by providing a comprehensive overview of every maintenance action, minor or major.
Imagine not just managing, but enhancing the performance, safety, and longevity of your machinery with the aid of your equipment maintenance log.
In this post, we will delve into the intricacies of the equipment maintenance log, alongside the best practices for maintenance management etc.
Moreover, this exploration is designed to help you fine-tune your maintenance strategy, leveraging the power of a well-orchestrated equipment maintenance solution.
Read on…
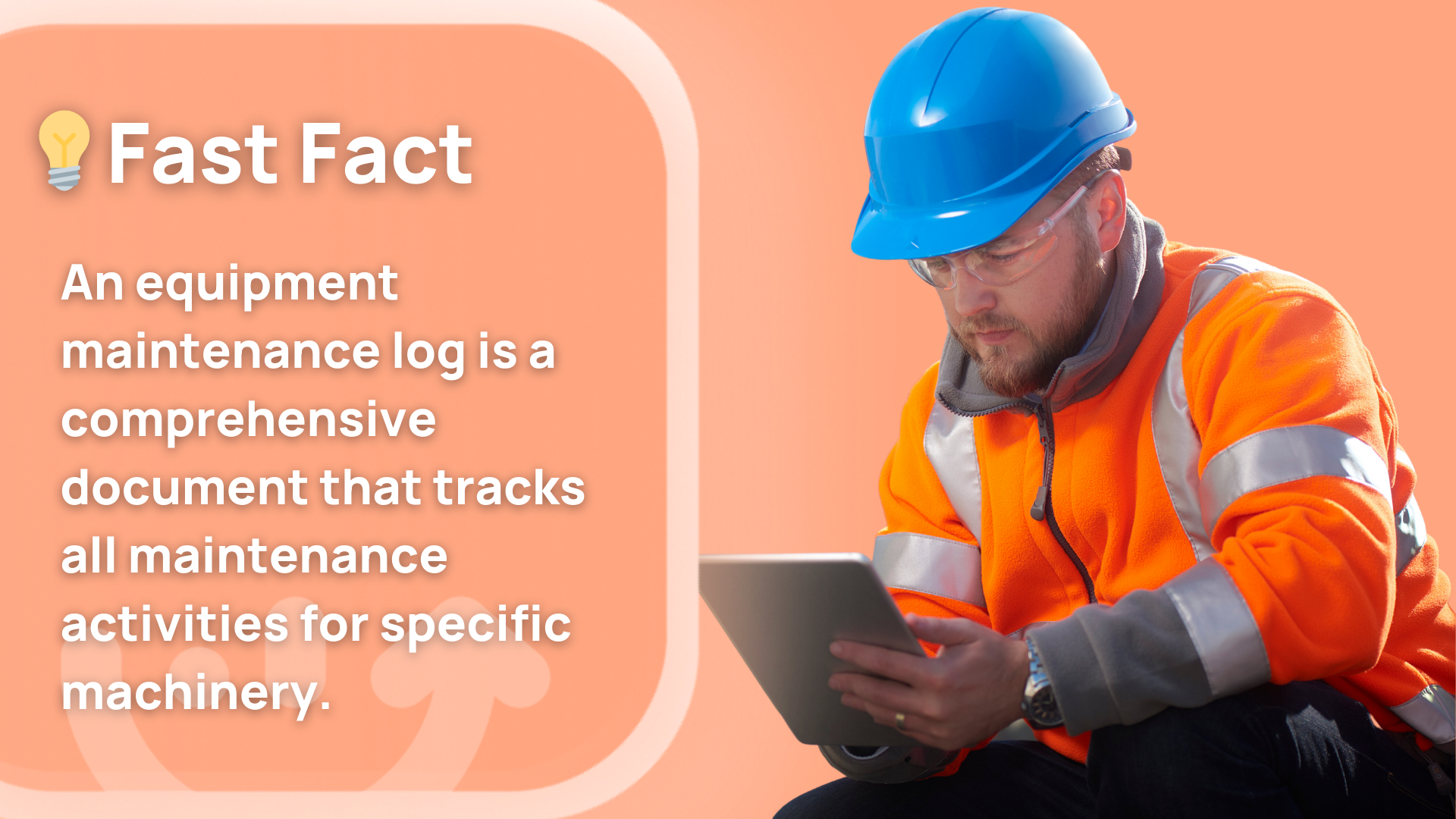
What Is An Equipment Maintenance Log?
An equipment maintenance log, alternatively known as an equipment maintenance management log, is a comprehensive document that chronicles all the maintenance equipment activities related to a specific piece of machinery.
It's akin to a health record for your equipment, capturing crucial data points like the date and time of maintenance, the assigned technician, and the specific tasks carried out.
When carefully maintained, these logs evolve into fundamental resources for preventive maintenance strategies, shedding light on the maintenance trajectory of the equipment.
.png)
6 Important Components of A Maintenance Equipment Log:
Let’s double down on the important aspects of a commonly used maintenance equipment log:
1. Time Stamps For Maintenance Equipment Activities
The date and time of each maintenance activity are critical in a maintenance log. These timestamps aid in tracking the frequency of maintenance and effectively scheduling future preventive care, thus optimizing equipment health.
2. Accountability Through Personnel Identification
Identifying the maintenance technician ensures accountability and provides a contact point for follow-ups. This information is instrumental in maintaining high standards of maintenance, fostering a culture of responsibility.
3. Detailed Task Record (*As Part of Equipment Maintenance Solution)
A comprehensive account of the maintenance tasks performed is a key element in the equipment maintenance log. It helps diagnose future issues and identifies recurring problems, thereby enhancing the overall maintenance strategy.
4. Replacement Parts Tracking
Recording the replacement parts used during maintenance is essential for efficient inventory management. This tracking aids in future parts procurement planning and helps anticipate potential part failures, minimizing equipment downtime.
5. Observational Insights
Noting observations during maintenance serves as an early warning system for future issues.
These notes contribute to preventive measures and enrich the understanding of equipment behavior, promoting operational efficiency.
6. Effective Management Tool
When properly maintained with due diligence, such equipment logs are an indispensable tool for predictive and preventive maintenance strategies.
Based on a comprehensive overview of the equipment's history, it supports informed decision-making and boosts maintenance management effectiveness.
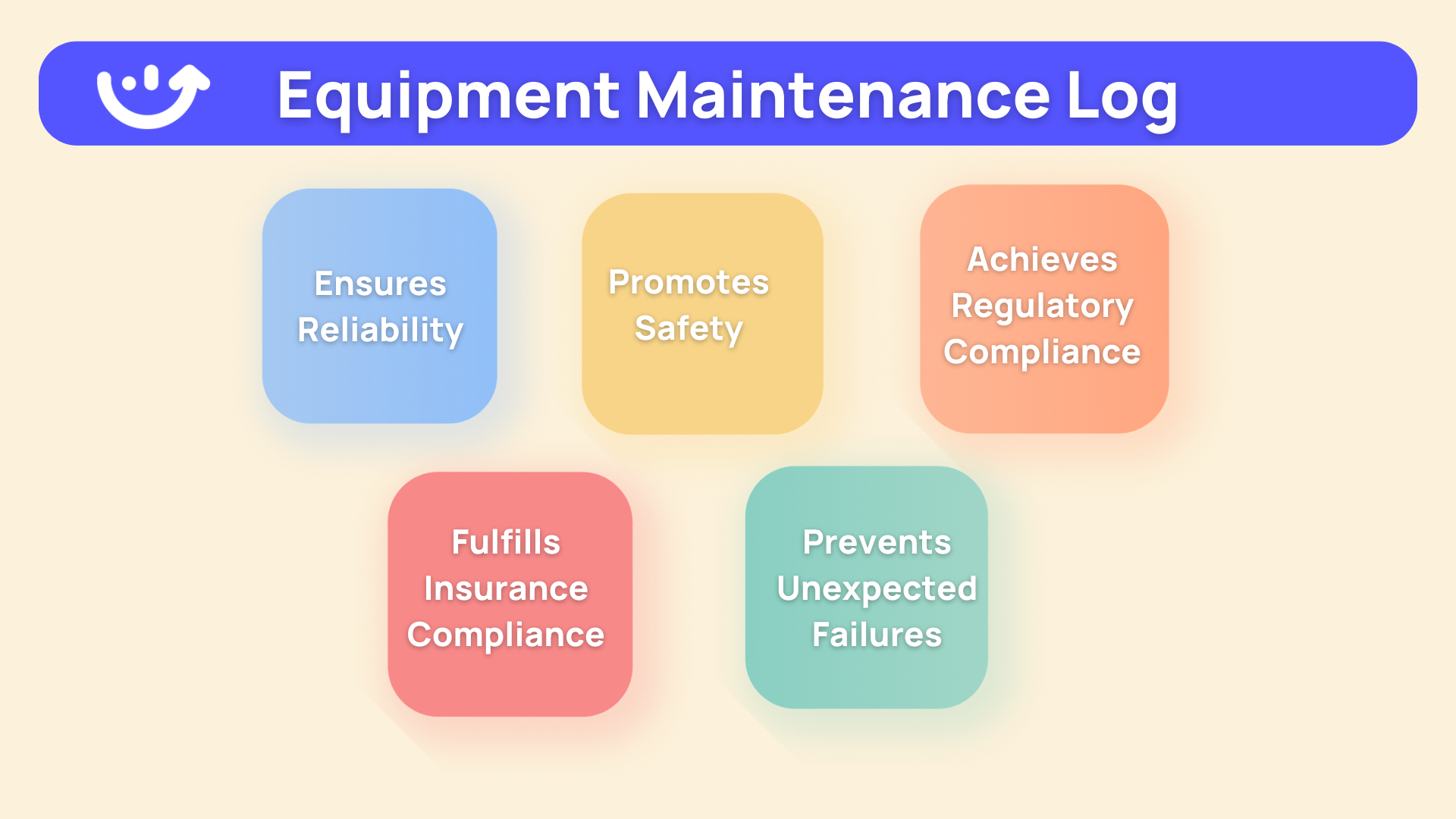
The Significance of a Maintenance Equipment Log
A routinely updated maintenance equipment log plays a crucial role in prolonging the life of your machinery.
By recording all servicing and upkeep activities, these logs empower maintenance managers to schedule preventive maintenance proactively.
This proactive approach can significantly enhance the lifespan of equipment, ensuring optimal performance for an extended period.
Ensuring Reliability
A comprehensive log serves as a reliable source of insights into your equipment's condition.
Promoting Safety
The safety of operators and other personnel is paramount in any industry.
Equipment maintenance logs can highlight potential safety concerns before they escalate into significant issues.
Achieving Regulatory Compliance
Regulatory compliance is vital in industries reliant on heavy machinery.
On that note, a well-thought-out and comprehensive log acts as tangible proof of adherence to maintenance standards and regulations.
These logs, demonstrating a commitment to the stipulated guidelines, can safeguard your organization against potential penalties.
Fulfilling Insurance Compliance
Insurance policies often require proof of proper preventive maintenance, and this is where a well-maintained equipment maintenance solution shines.
These logs serve as verifiable evidence of regular and appropriate preventive maintenance, fulfilling the requirements set by insurance providers.
Preventing Unexpected Failures
Unforeseen equipment failures can lead to expensive repairs and prolonged downtime.
The said equipment maintenance solution or a maintenance equipment log can help anticipate potential issues, enabling preventive action, and consequently, minimizing costly breakdowns and enhancing productivity.
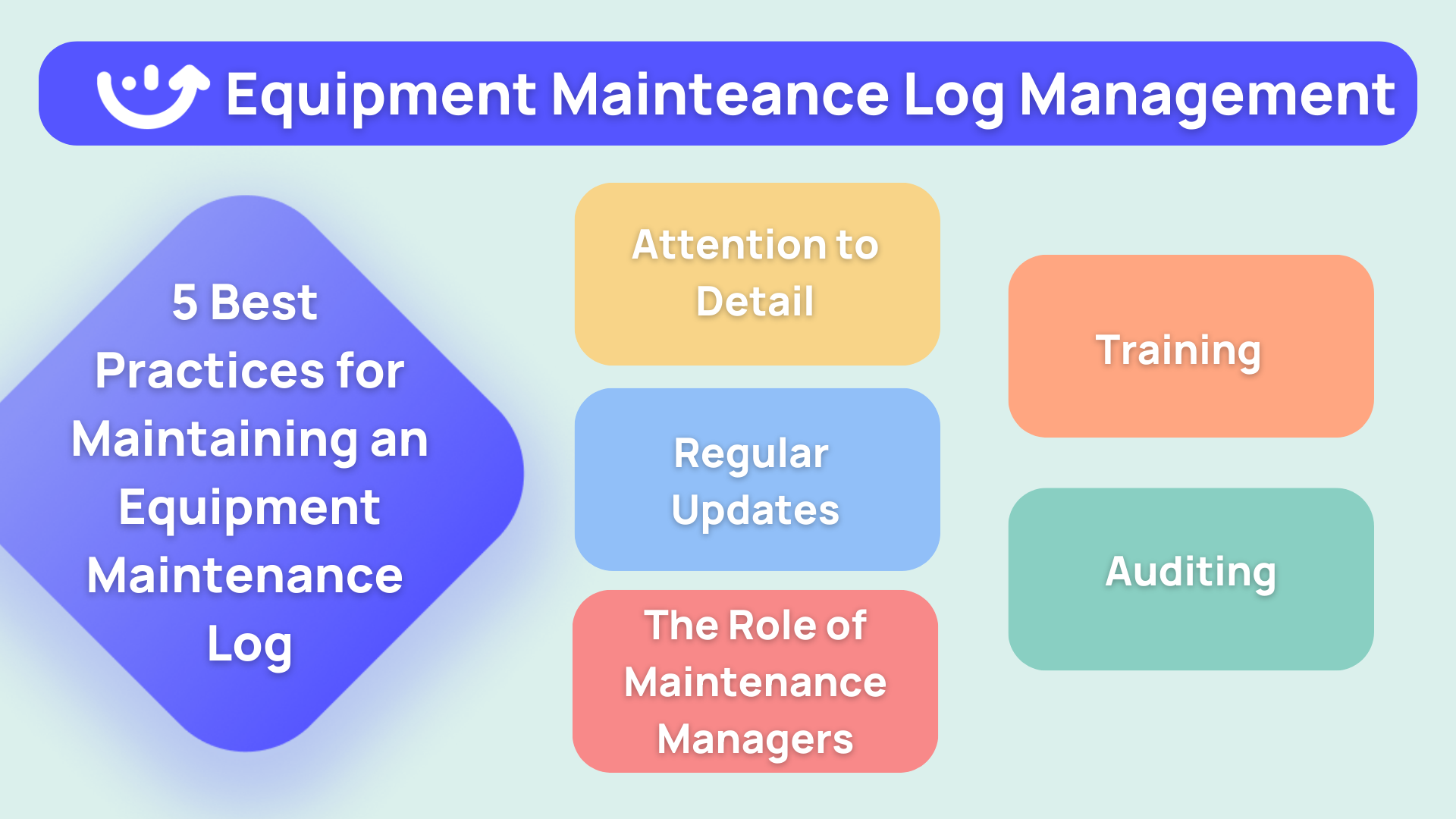
5 Best Practices for Maintenance Management In 2024
Maintaining an equipment maintenance log calls for a commitment to consistent recording.
Here are 5 all-time best practices for maintenance management that contribute to the log-based aspect of things.
1. Attention to Detail
Attention to detail includes accurately logging all relevant data such as the date and time of maintenance, personnel involved, tasks performed, and any replacement parts used.
In addition, any observations or anomalies noted during maintenance should be recorded, allowing potential issues to be caught early and preventive measures to be taken.
2. Regular Updates
Keeping the log up-to-date is essential for its efficacy.
The maintenance manager's role includes ensuring that the log reflects the most recent maintenance activities.
Regular updates contribute to the log's accuracy and reliability, making it a useful tool for preventive maintenance strategies and compliance requirements.
3. Training
Regular training sessions help instill an understanding of the importance of these logs among team members.
These sessions should emphasize the critical role that logs play in preventive maintenance, equipment longevity, and regulatory compliance. Every employee involved should know how to accurately contribute to the log.
4. Auditing
Regular audits of the equipment maintenance logs can help maintain their integrity.
Reviewing the logs allows for identification and correction of any inconsistencies or gaps, ensuring that the log's practices are being followed correctly.
5. The Role of Maintenance Managers
The maintenance manager plays the most important role in the process of maintaining an equipment maintenance log.
They are responsible for ensuring the log's accuracy and utility, making sure that every detail is correctly recorded and that the log is regularly updated.
The Digitization of Equipment Maintenance Solutions In 2024
In an era of rapid digital innovation, the use of digital software for equipment maintenance solution has become a necessity.
These equipment maintenance solutions come with a wealth of features specifically designed to meet the demands of today's maintenance managers. While also offering a comprehensive platform that simplifies and improves maintenance management processes.
Here are the key characteristics of digital solutions for maintenance log management:
User-Friendly Interface
Modern digital solutions are designed with users at their core, featuring intuitive interfaces that simplify the task of logging maintenance activities.
Such a user-friendly design ensures that team members, regardless of their tech savviness, can interact with the platform efficiently.
Real-Time Updates
One significant advantage of digital tools is their ability to provide real-time updates.
Secure Data Storage
Digital log platforms ensure data is securely stored and easily accessible.
Data Analysis Capabilities
With digital solutions, maintenance managers can swiftly analyze equipment log data to uncover useful insights.
Accessibility
Digital solutions can be accessed from anywhere, at any time, providing greater flexibility and faster information retrieval.
Integration with Existing Systems
Modern digital tools are designed to integrate seamlessly with existing systems, improving data consistency and minimizing the chances of data duplication or loss.
Many facilities have successfully transitioned to digital solutions for their maintenance log management, reaping the benefits of a streamlined, digitized process.
The implementation of such digital tools not only ensures that equipment maintenance logs are accurately maintained and readily available, but also contributes to enhancing the efficiency and effectiveness of maintenance operations.
.webp)
Leveraging Xenia for Enhanced Equipment Maintenance Management
In the quest for superior equipment maintenance management, Xenia emerges as a leading contender.
The platform offers a comprehensive solution that prioritizes efficiency, precision, and flexibility. With
Xenia's solution, discover a more proficient and effective method to minimize equipment downtime, prolong equipment lifespan, and guarantee regulatory compliance.
6 Key components of Xenia's Platform:
1. Asset Management
This feature lets you track and manage all your assets from one centralized platform.
From logging maintenance tasks to analyzing asset performance, Xenia's asset management tool offers a comprehensive solution for optimal asset upkeep and longevity.
2. Scheduling and Reminders
Efficient maintenance is often about timing.
With Xenia, you can schedule routine maintenance tasks and set reminders, ensuring no crucial maintenance work falls through the cracks.
This leads to increased equipment lifespan and reduced downtime.
3. Documentation Storage
Xenia provides a safe and accessible place to store all your critical documentation, from maintenance records to regulatory compliance certificates.
This feature simplifies document retrieval and ensures crucial information is always at your fingertips.
4. Task and Work Order Management
This tool empowers managers to monitor ongoing, completed, and future maintenance tasks.
It provides a simplified method to delegate tasks, track progress, and confirm completion, ensuring no maintenance tasks are overlooked or postponed.
5. Operations Template Library and Builder
Xenia simplifies the standardization of maintenance procedures across all equipment.
With its operations template library and builder, you can create, alter, and use templates for routine maintenance tasks, ensuring consistency and precision in your maintenance operations.
6. Robust Reporting Module
In order to make informed decisions, maintenance managers require access to comprehensive and easily digestible data.
Xenia's robust reporting tool(s) transforms raw data from your equipment maintenance logs into actionable insights.
This allows managers to recognize patterns, anticipate problems, and fine-tune maintenance schedules.
Use Xenia for Equipment Maintenance Management
In an increasingly mechanized world, mastering efficient maintenance management is a necessity.
One pivotal aspect is the creation and preservation of detailed equipment maintenance.
Such records, meticulously kept, pave the way for improved equipment reliability, extended service life, and seamless regulatory compliance.
Taking a leap towards digital transformation with solutions like Xenia presents an opportunity to reap further benefits.
Xenia's digital equipment maintenance solution(s) elevate the maintenance process by providing instant insights, allowing easy access to records, and facilitating the efficient analysis of data.
Embracing Xenia for maintenance equipment management is more than adopting a digital tool.
The phenomenon represents a strategic approach towards reinforcing preventive maintenance, promoting operational efficiency, and building a culture of continuous improvement in your organization's maintenance practices.
Why wait?
Seize the opportunity to elevate your maintenance management strategy today.
Start your free trial of Xenia and witness the transformation in your maintenance operations.
.webp)
%201%20(1).webp)