As a facility manager, you know that the electrical inspection report is a critical tool in keeping your building and equipment in tip-top shape. Welcome to the world of facility management, where every day is a new adventure filled with surprises, challenges, and oh-so-many electrical wires. As a facility manager, you know that keeping your building and equipment in tip-top shape is crucial for ensuring the safety and comfort of your occupants and maintaining your company's reputation and revenue.
One of the most important aspects of facility management is electrical inspections, which can help prevent electrical hazards and keep your equipment running smoothly. But let's face it; electrical inspections can be daunting - from ensuring compliance with regulations to finding qualified personnel to maintaining accurate and efficient reporting systems. It's no wonder many facility managers feel like they're in the dark regarding electrical inspections.
Priced on per user or per location basis
Available on iOS, Android and Web
But fear not because we're here to shed some light on the subject and help you navigate the electrifying world of electrical inspections. In this blog post, we'll explore the key components of electrical inspection reports, the risks and consequences of inadequate inspections, common challenges in electrical inspections, and, most importantly, the solutions and digital tools that can help facility managers improve their inspection processes and minimize risk.
So whether you're a seasoned facility manager or just starting out, grab your hard hat and safety goggles, and let's dive into the electrifying world of electrical inspections with Xenia!
What is an Electrical Inspection Report?
An electrical inspection report is a formal document that summarizes the findings of an electrical inspection and outlines the steps taken to address any issues. It typically includes details about the property or facility being inspected, the date of the inspection, identification of the inspector and their qualifications, scope of the inspection, description of any hazards or violations identified, recommendations for corrective actions, verification that the recommended actions have been completed, and signatures of the inspector and facility manager.
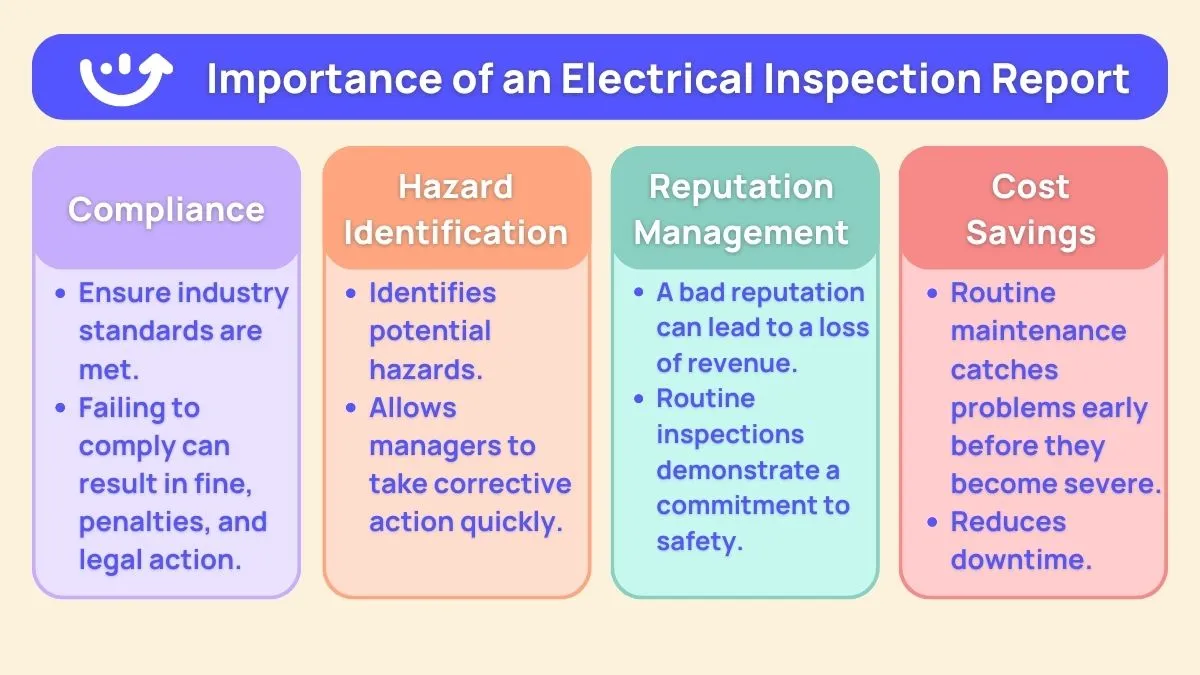
Facility managers and property owners primarily use electrical inspection reports to ensure compliance with industry standards and regulations, identify potential hazards, and take corrective actions to prevent property damage, equipment failure, or injury to employees or customers. Many jurisdictions require regular electrical inspections for public safety and liability reasons, and failure to comply with these requirements can result in fines, penalties, and legal liabilities.
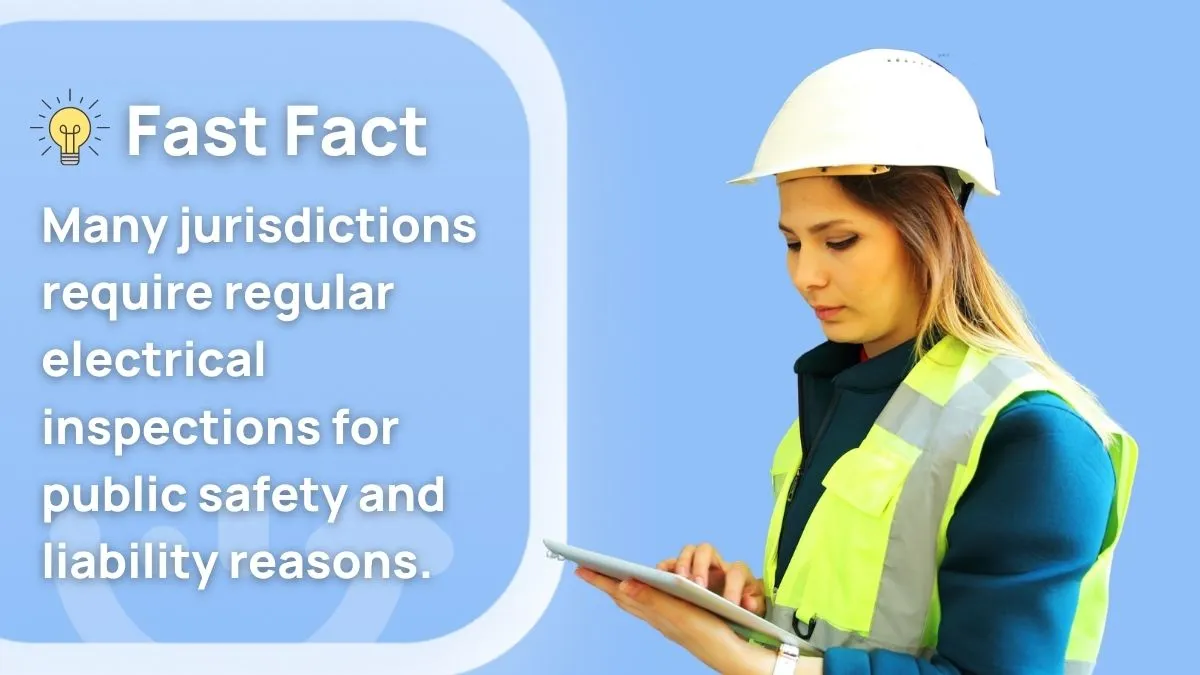
An electrical inspection report is a formal document that summarizes the findings of an electrical inspection and outlines the steps taken to address any issues. It plays a crucial role in facility management for the following reasons:
- Compliance: Electrical inspection reports help facility managers ensure compliance with industry standards and regulations. Many jurisdictions require regular electrical inspections for public safety and liability reasons, and failing to comply with these requirements can result in fines, penalties, and legal liabilities.
- Hazard identification: Electrical inspection reports help identify potential hazards and take corrective actions before they cause damage or injuries. Electrical hazards can result in property damage, equipment failure, and injury or death to employees or customers. By documenting and addressing these hazards, facility managers can minimize the risks and consequences of electrical accidents.
- Reputation management: Inadequate electrical inspections can lead to loss of revenue and a negative impact on the company's reputation. By conducting regular and thorough electrical inspections and documenting their findings, facility managers can demonstrate their commitment to safety and compliance and protect their brand image.
- Cost savings: Regular electrical inspections can help identify potential issues before they become more severe, saving time and money in the long run. By scheduling regular inspections and addressing any issues promptly, facility managers can avoid costly equipment failures and downtime.
Common Challenges in Electrical Inspections
While electrical inspection reports are crucial for maintaining safety and compliance in facility management, there are common challenges that can hinder the effectiveness of these reports. Facility managers may face the following challenges:
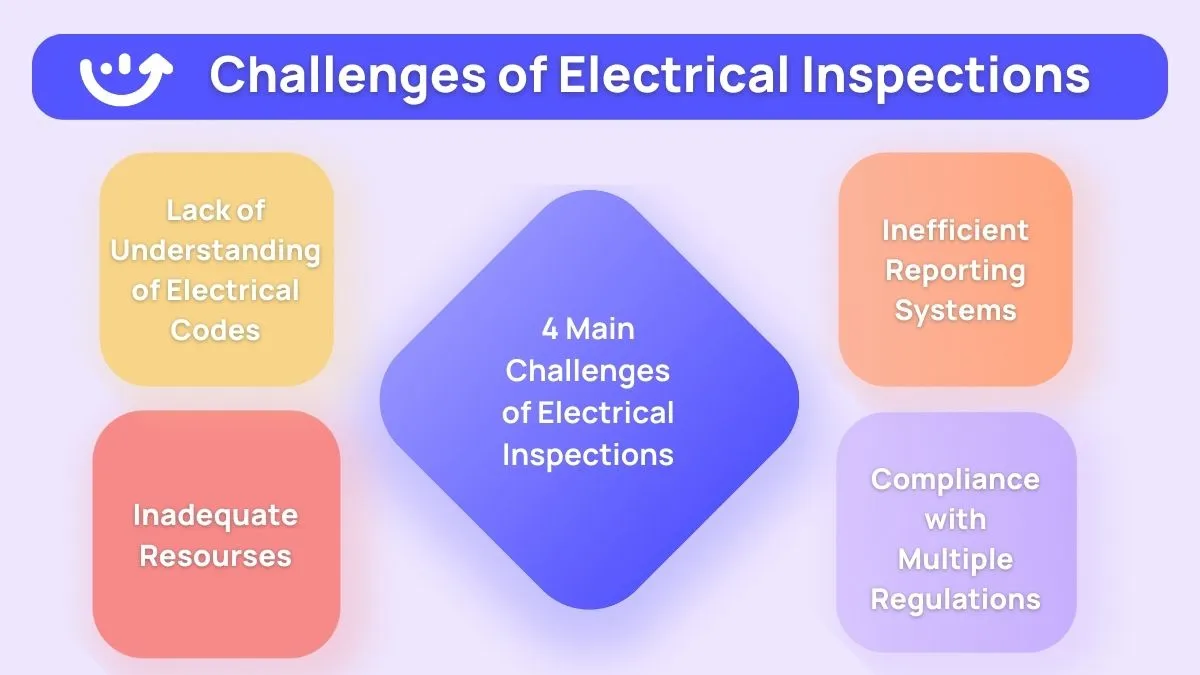
- Lack of understanding of electrical codes and regulations: Some facility managers may not be familiar with the latest electrical codes and regulations, leading to inadequate inspections and missed safety issues.
- Inadequate resources: Facility managers may lack the resources to conduct thorough electrical inspections, such as qualified personnel, equipment, or time.
- Inefficient reporting systems: Reporting systems that are not efficient, accurate, or timely can lead to delays in identifying and addressing issues, which can increase the risks of electrical hazards.
- Compliance with multiple regulations: Facilities that operate in multiple jurisdictions may be subject to different electrical codes and regulations, making it difficult to maintain compliance and conduct effective inspections.
Solutions to Electrical Inspections
Despite these challenges, facility managers can take steps to overcome them and ensure effective electrical inspection report management. These steps include:
- Staying up-to-date on electrical codes and regulations: Facility managers can stay informed about the latest electrical codes and regulations by attending training courses, subscribing to industry publications, and seeking guidance from electrical experts.
- Allocating resources for inspections: Facility managers can allocate the necessary resources for inspections, such as hiring qualified personnel, investing in equipment, and scheduling inspections at appropriate intervals.
- Implementing efficient reporting systems: Facility managers can implement digital tools such as inspection management software, mobile inspection apps, and real-time monitoring systems to streamline the inspection process and ensure accurate and timely reporting.
- Conducting regular reviews and audits: Facility managers can review inspection reports and conduct regular audits to identify areas for improvement and ensure that corrective actions are being taken in a timely and effective manner.
By taking these steps, facility managers can ensure that their electrical inspection processes are effective and compliant, minimizing the risks and consequences of inadequate electrical inspections. The next section will provide more detailed solutions to improve electrical inspections.
Digital Software Tools for Electrical Inspections
Digital software tools are revolutionizing the electrical inspection process by eliminating the need for pen and paper and streamlining data collection and reporting. Some key features of digital software tools for electrical inspections include:
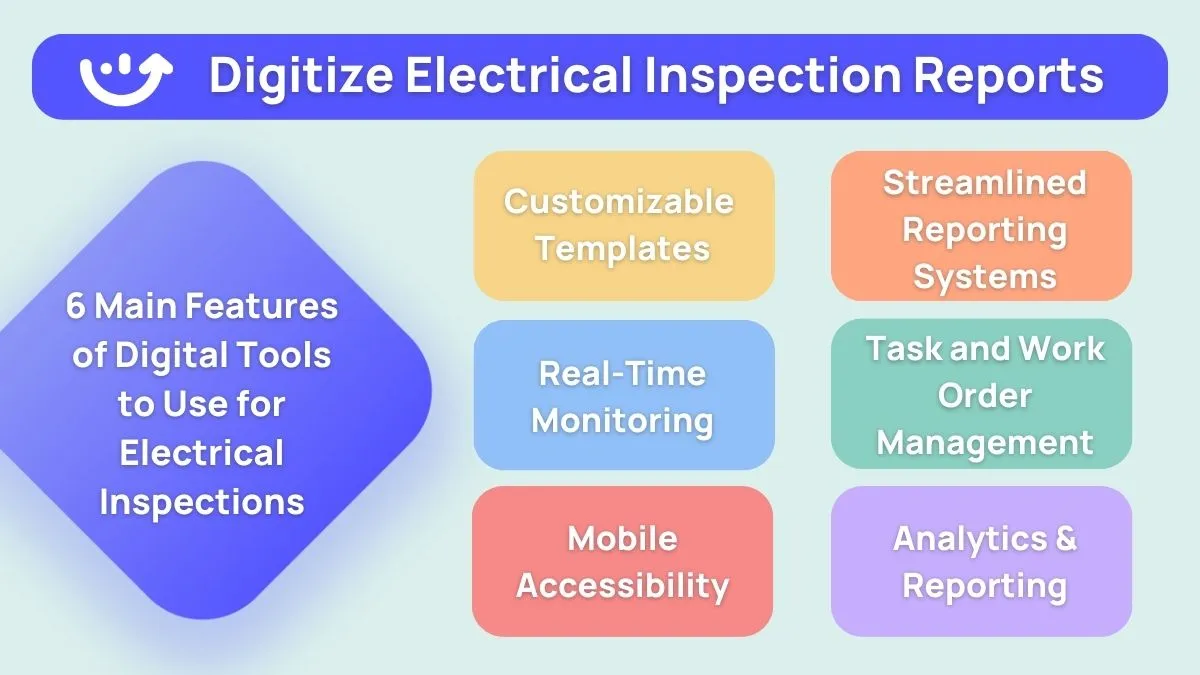
- Customizable templates: Digital software tools can be used to create checklists, logs, standard operating procedures, inspections, meeting agendas, and more. These templates can be tailored to meet the specific needs of a facility's electrical inspection process and can include different response types such as checkbox, pass/fail, text input, number input, temperature, length, weight, and multiple choice.
- Efficient reporting systems: Digital software tools allow for efficient reporting systems that can streamline the inspection process and ensure accurate and timely reporting. Inspection results can be recorded and reported digitally, reducing the likelihood of human error and ensuring that issues are addressed in a timely manner.
- Real-time monitoring: Real-time monitoring systems can be integrated with digital software tools to alert facility managers to potential issues before they become more severe. These systems use sensors and other technologies to monitor equipment and systems in real-time, allowing facility managers to identify and address issues as soon as they arise.
- Task and work order management: Digital software tools for electrical inspections also offer task and work order management features that allow facility managers to quickly assign tasks to teams or individuals, prioritize tasks, and attach templates to tasks. All task data is saved for review and reporting, allowing facility managers to track progress in real-time and ensure that tasks are completed in a timely manner.
- Mobile accessibility: Most digital software tools for electrical inspections are accessible on mobile devices, allowing inspections to be conducted on-the-go. Mobile inspection apps can be used to record and report inspection data, identify hazards and issues, and generate reports, making it easier for facility managers to conduct inspections in the field.
- Analytics and reporting: Digital software tools for electrical inspections offer analytics and reporting features that allow facility managers to easily organize and export reports based on details such as priority, location, category, status, and more. These reports can be exported as a PDF or CSV file and provide valuable data that can be used to improve the overall electrical inspection process.
Benefits of Using Digital Tools for Electrical Inspections
The use of digital tools for electrical inspections can benefit a range of stakeholders beyond facility managers. Engineers and technicians responsible for performing the inspections can benefit from increased accuracy, streamlined processes, and improved data management through digital tools. Building owners and operators can benefit from improved safety and reduced costs associated with electrical maintenance and repairs. Additionally, occupants and visitors of the building can benefit from a safer and more comfortable environment resulting from more accurate and thorough inspections.
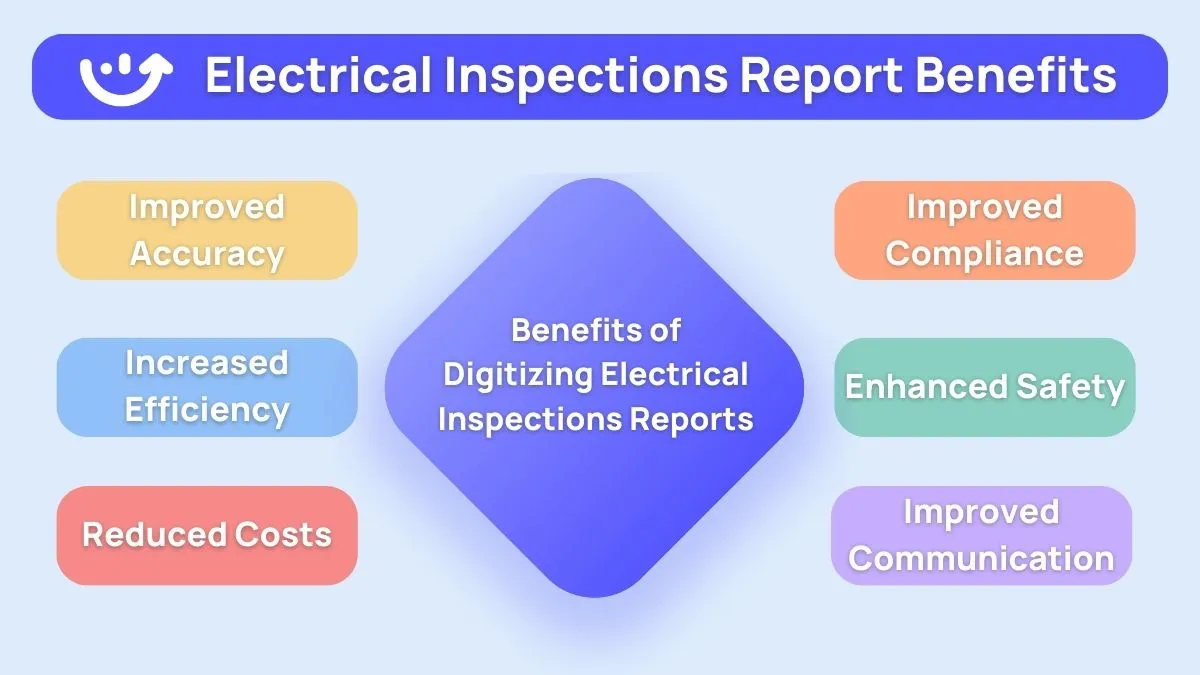
The use of digital tools in electrical inspections benefits are the following:
- Improved accuracy: Digital tools provide accurate data collection and reporting, reducing the risk of human error and inconsistencies in the inspection process. With digital tools, inspections can be standardized, ensuring that every aspect of the inspection is completed to the same level of accuracy and detail.
- Increased efficiency: Digital tools can streamline the inspection process, reducing the time and resources required to conduct inspections. With mobile inspection apps and real-time monitoring systems, facility managers can complete inspections more efficiently and respond to issues more quickly.
- Reduced costs: Digital tools can help facility managers save costs associated with electrical inspections by minimizing equipment downtime, reducing repair costs, and avoiding fines and penalties associated with compliance violations. With real-time monitoring and digital reporting, facility managers can quickly identify issues and take corrective actions before they become more severe.
- Improved compliance: Digital tools help ensure compliance with industry standards and regulations, reducing the risk of liability issues and potential legal consequences. With digital tools, facility managers can quickly identify and address compliance issues, reducing the risk of penalties and fines.
- Enhanced safety: By identifying electrical hazards and taking corrective actions quickly, digital tools can help facility managers enhance the safety of their employees and customers. With real-time monitoring and digital reporting, facility managers can respond to issues more quickly and efficiently, reducing the risk of accidents and injuries.
- Improved communication: Digital tools can help facility managers communicate more effectively with their staff and stakeholders. This can include real-time reporting, automated alerts, and collaborative features that allow team members to share information and work together more efficiently.
Implementation of Digital Tools for Electrical Inspections
Now that you understand the benefits of using digital tools for electrical inspections, it's time to implement them in your facility management processes. Here are some tips on how to successfully implement digital tools for electrical inspections:
- Choose the right tools: The first step in implementing digital tools for electrical inspections is to research and evaluate the available options. Look for tools that are specifically designed for electrical inspections and have features that match your facility's needs. Consider factors such as cost, ease of use, and customer support when making your decision.
- Train your staff: Provide detailed instructions on how to navigate the tools and how to use them to complete electrical inspections. Continue ongoing support to ensure that your staff is comfortable with the new tools and that they are using them correctly.
- Integrate the tools with existing inspection processes: This may involve modifying your current inspection procedures to include the use of digital tools, or creating new procedures that incorporate the tools seamlessly. Be sure to communicate any changes to your staff and provide training on the new processes.
- Establish clear roles and responsibilities: Clearly define who is responsible for conducting the inspections, who is responsible for recording and reporting the data, and who is responsible for ensuring that corrective actions are taken in a timely manner.
.webp)
%201%20(1).webp)