Welcome to your one-stop guide to construction inventory management! Construction inventory management is more than just keeping tabs on your materials—it's an art of juggling various tasks, including tracking, ordering, storing, and utilizing construction assets effectively.
Amidst the hustle and bustle of a project, this might seem daunting, but fear not! Our guide and Xenia, a transformative solution in the industry, are here to make this task easier.
So, brace yourselves to unlock the secret of efficient inventory management and discover how inventory management systems like Xenia are transforming the way construction businesses operate.
Stick with us till the end, and you'll walk away with a wealth of knowledge, ready to revolutionize your construction inventory management practices. So, without further ado, let's dig into the bedrock of construction inventory management. Ready?
Let's build!
Priced on per user or per location basis
Available on iOS, Android and Web
Understanding Construction Inventory Management
.webp)
Construction inventory management is an intricate, multifaceted process that extends far beyond mere counting of bricks and tracking of heavy equipment. It encompasses a systematic approach to tracking, ordering, storing, and utilizing construction materials and equipment.
At its core, it's about possessing a comprehensive knowledge of what materials you have, where they're located, and how they're being used in your ongoing projects. With this vital understanding, construction companies can streamline operations, reduce waste, optimize usage of resources, and minimize project delays, significantly enhancing their overall productivity and bottom-line profitability.
Inventory management in the construction world is not just about maintaining a balanced stock of materials and equipment but also about ensuring that every resource invested delivers the maximum possible value. An efficient inventory management system helps construction firms to avoid overstocking or understocking, both of which can have serious financial implications.
Key Components of Construction Inventory Management
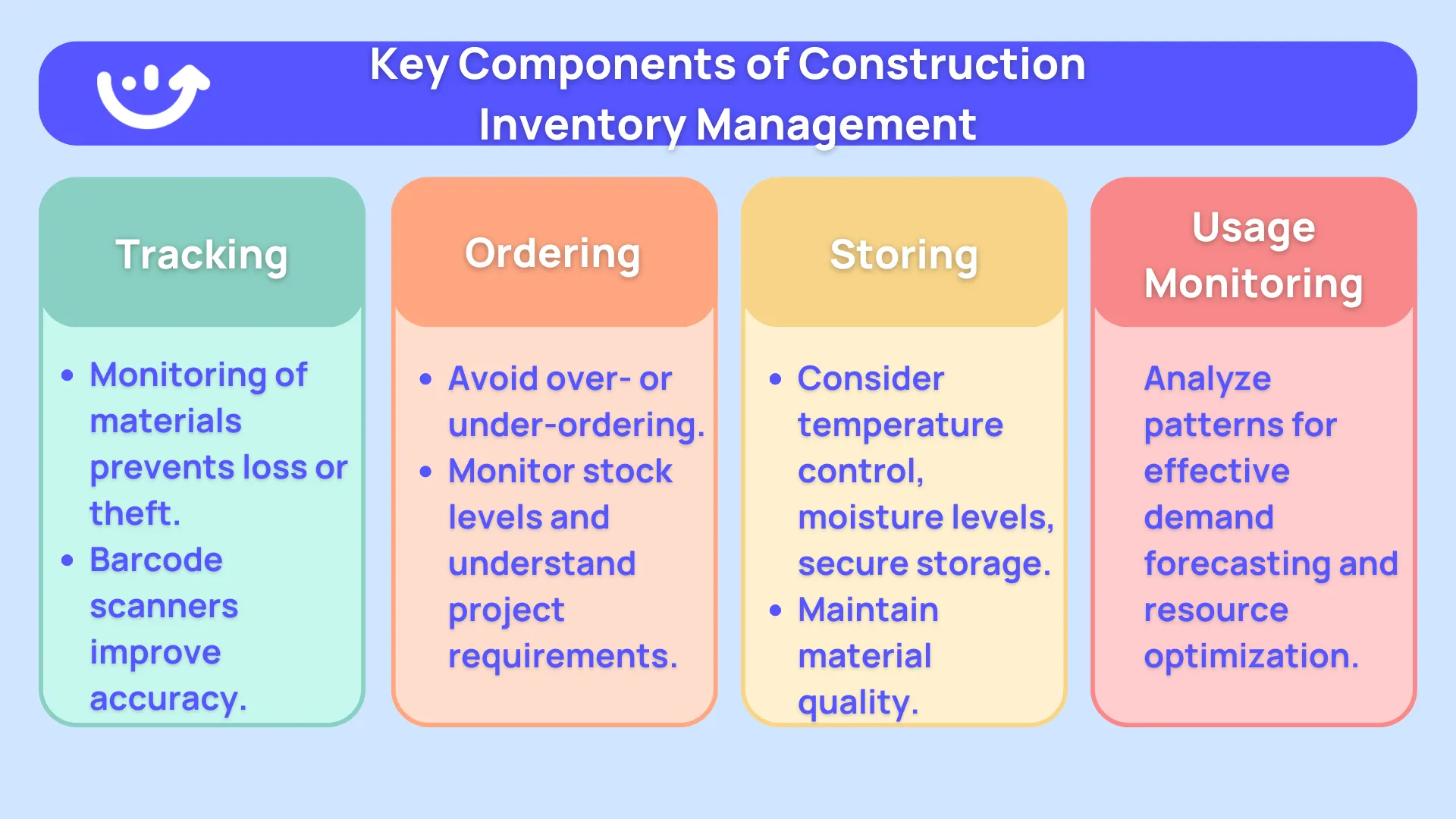
Construction inventory management is typically the responsibility of the construction project manager or a designated inventory manager within the construction company.
Inventory management should be implemented from the beginning of a construction project and continue throughout its duration to ensure efficient and effective project execution.
Let’s review key components, each equally significant in contributing towards a smoothly functioning inventory control system:
Tracking
This is the backbone of inventory management. It involves keeping meticulous tabs on all construction materials and equipment, right down to the last nut and bolt, to prevent loss or theft. Modern technologies like RFID and barcode scanners can make this task more manageable and accurate.
Ordering
Effective inventory management is synonymous with astute purchasing decisions. It ensures that only necessary materials are ordered at the right time in the right quantity, avoiding costly over- or under-ordering. This requires continuous monitoring of stock levels and a keen understanding of the project's current and future requirements.
Storing
Proper storage practices are integral to inventory management. They prevent damage, degradation, and expiration of materials, ensuring that they are in optimal condition when needed. This includes considering aspects such as temperature control, moisture levels, secure storage, and proper organization.
Usage Monitoring
Keeping track of material usage is a critical aspect of inventory management. By observing and analyzing patterns in material usage, construction companies can gain valuable insights that allow for effective demand forecasting. This understanding enables better planning for future projects and helps optimize resources.
The Importance of Construction Inventory Management
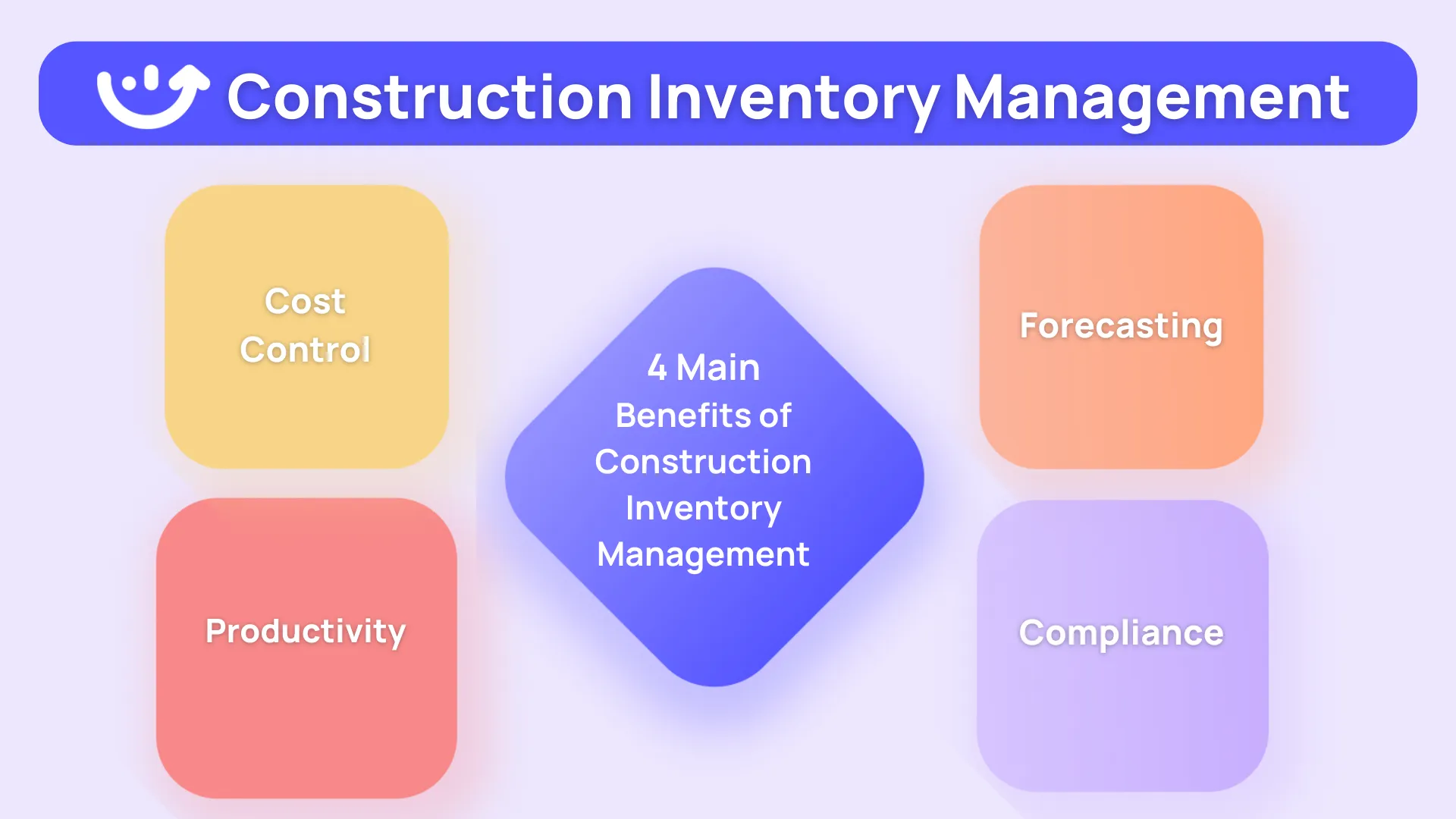
One of the critical aspects that directly impacts a project's success, often overlooked, is construction inventory management. Proper management of materials and equipment is as essential as having a skilled workforce or a well-drawn plan. The reason behind this is multifold.
Effective construction inventory management ensures that the right materials and equipment are available at the right time, prevents project delays, helps control costs, and contributes significantly to the bottom line. In an age where sustainability and compliance are at the forefront, good inventory practices play a crucial role.
Managing construction inventory efficiently is critical for several reasons:
Cost Control
Over-ordering, theft, and damage can lead to unnecessary costs. However, with effective construction inventory management, these costs can be significantly reduced or even completely eliminated. By continuously monitoring inventory levels, construction firms can ensure they only order materials as and when required, avoiding costly overstocking.
Productivity
Having the right materials and equipment on hand when needed can boost productivity, thereby preventing project delays. By accurately tracking and managing inventory, construction firms can ensure the smooth flow of work, leading to improved project timelines and increased worker productivity.
Forecasting
Understanding your inventory usage can aid with demand forecasting, enabling better project planning. By examining past inventory usage data, construction managers can anticipate the future materials and equipment requirements for similar projects. This foresight enables more accurate purchasing decisions and project scheduling, reducing the risk of project overruns in terms of both time and cost.
Compliance
Proper tracking of materials helps in maintaining compliance with construction regulations and standards. Many construction materials have strict guidelines regarding their storage and usage. Accurate inventory records can help maintain visibility of material locations, batch numbers, expiry dates, and more, simplifying compliance tasks and reducing the risk of regulatory infractions.
The Challenges of Construction Inventory Management
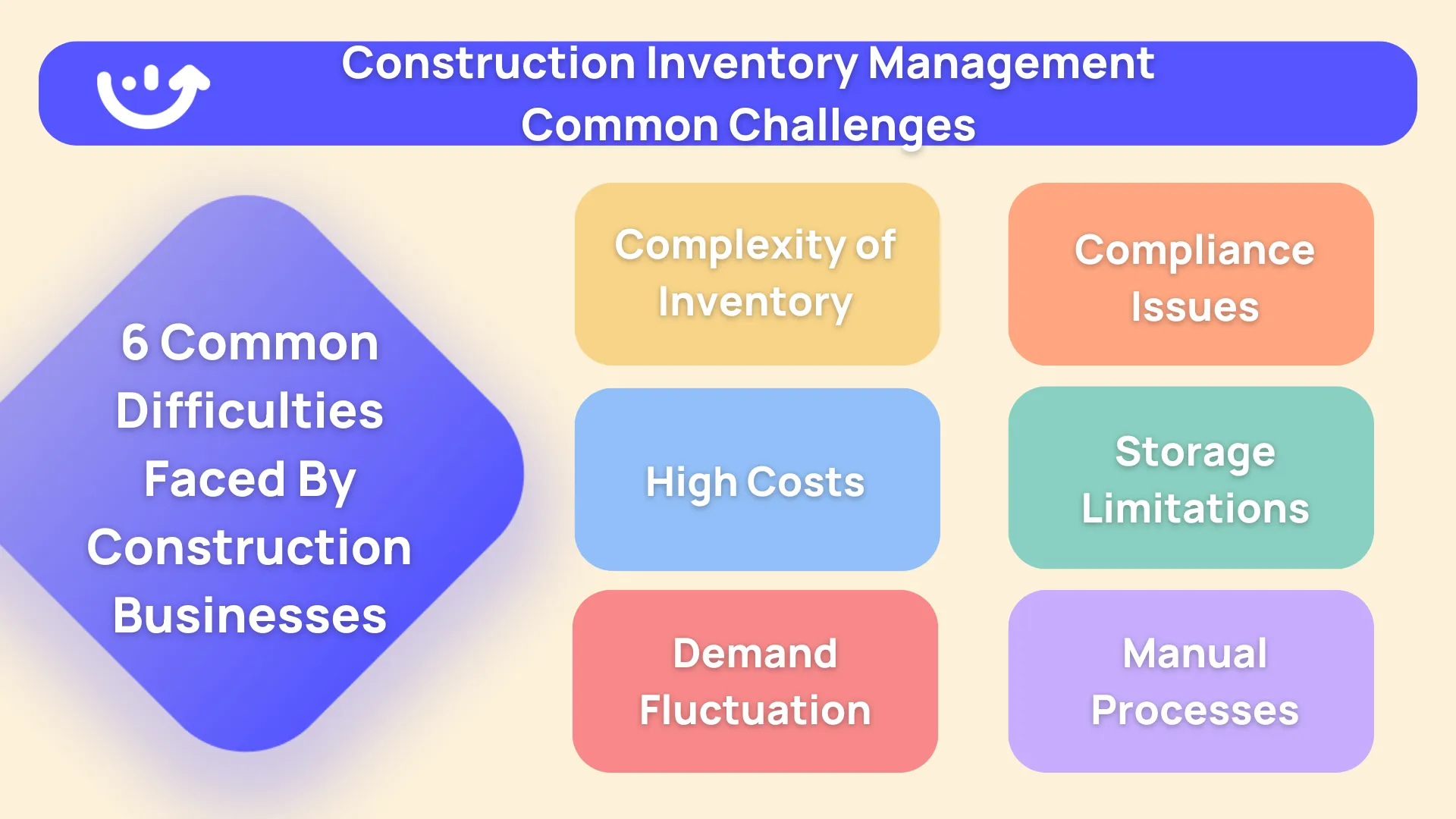
While the importance of construction inventory management cannot be understated, it's not without its challenges. Here are some of the common difficulties faced by construction businesses and how to address them:
Complexity of Inventory
In construction, inventory management covers a vast spectrum of items, including expensive machinery, specialized tools, safety equipment, consumables, and more. The need to account for the condition, location, and quantity of such a wide array of items presents a significant challenge to construction firms.
High Costs
Construction materials and equipment often carry high price tags, making the cost of inventory substantial. Any loss, theft, or damage can result in significant financial implications, escalating project costs unexpectedly. This emphasizes the importance of effective inventory tracking to mitigate such risks and prevent financial losses.
Demand Fluctuation
Demand for construction materials can fluctuate wildly based on multiple factors, including the project's phase, seasonal changes, and market trends. Predicting these fluctuations accurately is a challenging endeavor that requires sophisticated forecasting tools and experienced judgment. An incorrect prediction can lead to overstocking or understocking, each having its own set of complications.
Compliance Issues
Adherence to construction regulations and standards is crucial to maintain the legal and ethical integrity of a company. Non-compliance can result in hefty fines, legal action, and can severely damage a company's reputation. Keeping track of materials, particularly hazardous substances or regulated items, requires meticulous record-keeping and is a challenging aspect of construction inventory management.
Storage Limitations
Construction sites often have limited and variable storage space, which must be efficiently utilized to accommodate materials and equipment. Navigating this logistical challenge requires strategic planning and careful inventory management to prevent overcrowding, ensure accessibility, and minimize the risk of damage.
Manual Processes
Despite technological advances, many construction companies still rely on manual processes for inventory management. These outdated methods are time-consuming, labor-intensive, and susceptible to human error. The administrative burden of manual inventory management is a significant challenge, often leading to inefficiencies and inaccuracies that can compromise the entire project.
How Digital Solutions Optimize Construction Inventory Management
.webp)
In an age where technology permeates every aspect of our lives, the construction industry is no exception. Integrating digital solutions into construction inventory management processes can significantly streamline operations and drive efficiency. Here are some ways in which digital solutions optimize construction inventory management:
Real-Time Inventory Tracking
One of the primary benefits of using digital solutions is real-time inventory tracking. This feature enables managers to know exactly what items are on hand, where they are located, and when they will need to be replenished. This real-time visibility reduces the risk of overstocking or understocking, mitigates loss, and ensures that materials are readily available when needed.
Automated Processes
Manual inventory processes are not only time-consuming but also prone to human error. Digital solutions automate these processes, significantly reducing the risk of mistakes and freeing up your team to focus on other essential tasks. They can automatically update inventory levels as materials are used, send alerts when stock is low, and generate purchase orders when it's time to reorder.
Data-Driven Decision Making
Digital solutions offer powerful analytics capabilities that can provide valuable insights for decision-making. By analyzing past usage patterns and trends, these tools can forecast future demand, allowing managers to make proactive purchasing decisions. This data-driven approach minimizes waste, reduces costs, and ensures that the right materials are available at the right time.
Improved Collaboration
Construction projects often involve multiple stakeholders, including contractors, subcontractors, and suppliers. Digital solutions foster better collaboration among these parties by providing a centralized platform for communication and information sharing. This ensures that everyone is on the same page, improving coordination and efficiency.
Space Optimization
Limited storage space is a common challenge in construction sites. Digital inventory solutions can help optimize this space by providing visibility into what materials are on hand and where they are stored. This enables efficient use of space and prevents overcrowding.
Regulatory Compliance
Compliance with construction regulations and safety standards is crucial. Digital solutions can help maintain compliance by providing accurate, up-to-date records of materials. This can be especially useful during audits or inspections.
How to Optimize Construction Inventory Management with Xenia
As the construction industry becomes increasingly complex, managing inventory manually becomes more challenging.
That's where Xenia comes in. Xenia provides an all-encompassing solution for construction inventory management.This robust software solution is designed to streamline construction inventory management, saving time, and reducing costs.
Here are the ways Xenia can revolutionize your construction inventory management:
Comprehensive Tracking
With Xenia, you can track every piece of equipment and material in your inventory in real-time. It records essential details like location, status, and maintenance records, making it easier to manage your inventory.
Streamlined Ordering
Xenia's advanced features allow you to automate your ordering process. Based on usage patterns and forecasted demand, the software can generate order lists, ensuring that you have the right materials at the right time.
Optimized Storage
Xenia helps manage your storage effectively. It keeps track of your storage space, helping you to maximize its use and prevent overcrowding or underutilization.
Accurate Usage Monitoring
Xenia provides detailed reports on material and equipment usage. This valuable data can inform your purchasing decisions and help in demand forecasting.
User-Friendly Interface
Xenia’s intuitive design makes it easy for all team members to use. With its mobile app functionality, you can manage your inventory on-the-go, anytime, anywhere.
Seamless Integration
Xenia seamlessly integrates with other systems, allowing for real-time updates across all platforms. This can significantly improve your team's coordination and efficiency.
Use Xenia for Construction Inventory Management Today!
Effective construction inventory management transcends the fundamental principle of understanding what materials and equipment are available—it's a dynamic process that revolves around proficiently controlling, monitoring, and utilizing your resources to fuel growth, profitability, and productivity in your construction operations. This process, however, can be a challenging task, requiring meticulous attention to detail, careful planning, and the right tools.
This exploration of construction inventory management would not be complete without addressing the transformative impact of digital solutions like Xenia's software platform. Xenia is a comprehensive, user-friendly platform that revolutionizes inventory management in construction. This is more than a simple inventory tracking tool—it's an investment in efficiency, decision-making, and sustainability.
By leveraging Xenia's software solution, construction companies can not only streamline the intricate processes of tracking, ordering, storing, and usage monitoring but also gain a bird's eye view of their entire inventory lifecycle. This level of control and insight paves the way for data-driven decisions, more accurate forecasting, and ultimately, superior project outcomes.
Join the digital revolution in construction inventory management—see how Xenia can make a significant difference in your operations, decision-making, and overall business performance.
.webp)
%201%20(1).webp)