Construction accidents are some of the most common workplace incidents that can have devastating consequences for workers and the companies they work for. According to the Occupational Safety and Health Administration (OSHA), construction accidents account for a significant percentage of workplace fatalities each year. In 2019, there were 1,061 fatalities in the construction industry, accounting for 20.9% of all private industry worker fatalities. The most common causes of construction accidents include falls, electrocutions, struck-by accidents, and caught-in-between accidents.
Priced on per user or per location basis
Available on iOS, Android and Web
Construction managers have a responsibility to take steps to prevent these accidents and protect their workers. Failing to do so can result in not only human tragedy but also significant financial costs for the company. In addition to the cost of medical treatment and workers' compensation claims, construction accidents can also lead to project delays, damage to equipment and materials, and legal liabilities.
Fortunately, there are tools and technologies available that can help construction managers improve safety and prevent accidents. One such tool is Xenia, a software platform that enables maintenance management and deskless team operations to empower frontline workers and provide managers an integrated view of facility and employee health. With its range of features, including form templates, task and work order management, scheduling, messaging and chats, and reports and analytics, Xenia can help construction managers identify potential hazards, track progress in real-time, and ensure compliance with safety regulations.
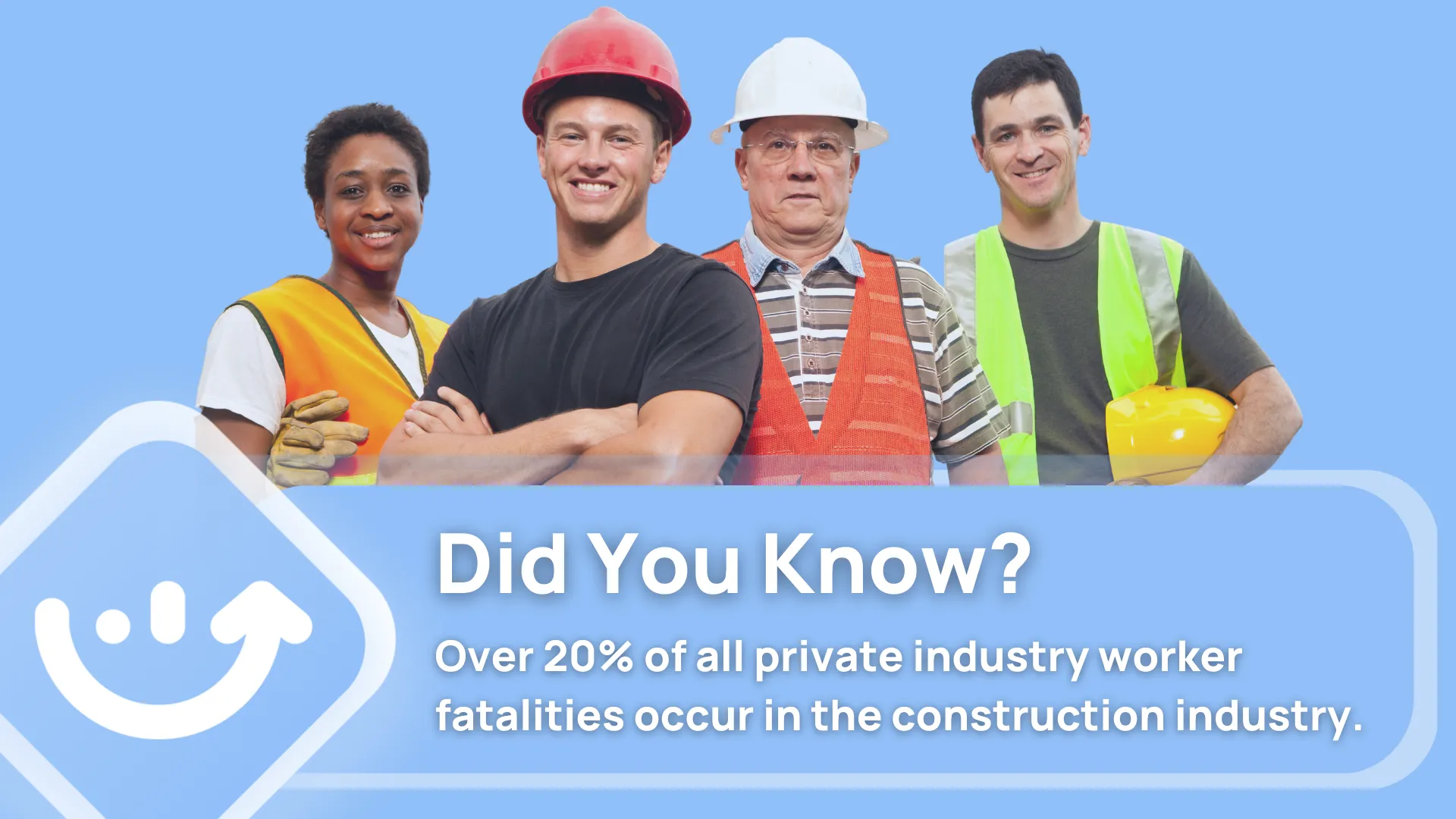
In the rest of this article, we'll explore the common causes of construction accidents, the benefits of using Xenia for construction safety, and real-world examples of how construction companies have successfully used Xenia to improve safety and prevent accidents on their sites
Common Causes of Construction Accidents
Construction sites are inherently dangerous environments with many risks for workers, ranging from working at heights to operating heavy machinery and power tools. Unfortunately, accidents can and do happen, leading to severe injuries, disabilities, and even fatalities. As a result, it's critical for construction managers to be aware of the most common types of accidents on construction sites and take steps to mitigate them.
.webp)
The most frequent types of construction accidents include:
- Falls from heights, which account for nearly 40% of all construction fatalities.
- Electrocution from contact with live wires or electrical sources.
- Struck-by accidents from heavy machinery or falling objects.
- Caught-in-between accidents from equipment, such as being crushed or pinned.
By understanding these common types of accidents, construction managers can identify areas of risk and implement safety protocols and training to minimize their occurrence. For example, ensuring that all workers wear appropriate safety gear, such as hard hats, safety harnesses, and non-slip footwear, can reduce the risk of falls. Proper training on the safe operation of heavy machinery and equipment can help prevent struck-by and caught-in-between accidents. Moreover, regular safety inspections can help identify hazards and prevent accidents before they occur.
It's essential for construction managers to take steps to address the root causes of accidents on their sites. Through proper safety training, equipment, and inspections, the likelihood of a construction accident can be significantly reduced. This approach can help keep workers safe and minimize the impact of accidents on both employees and the company.
Digital Tools for Construction Accident Management
Construction accident management has evolved over time as a result of various factors, including increased awareness of safety issues in the workplace, changes in regulations, and advancements in technology. The following is a brief history of construction accident management:
- Early 20th century: Prior to the 1920s, there were few regulations governing workplace safety, and construction sites were particularly hazardous. As a result, accidents were common, and injury rates were high. However, in response to public pressure and a growing recognition of the need for workplace safety, the U.S. government passed the Occupational Safety and Health Act (OSHA) in 1970, which established minimum safety standards for workplaces and mandated regular inspections.
- Late 20th century: Throughout the 1980s and 1990s, the construction industry made significant strides in improving workplace safety through the implementation of safety programs, training programs, and the use of personal protective equipment (PPE).
- 21st century: In recent years, digital tools have been developed to enhance construction accident management. One such tool is Xenia, a software platform designed to help construction companies manage safety incidents and compliance. Xenia provides a centralized platform for tracking incidents, conducting investigations, and reporting on safety data.
.webp)
Digital tools are better than paper and pen for managing construction accidents and safety incidents because they enable tangible differences including faster response times, more accurate data collection, easier identification of trends and patterns, better incident management, and reduced administrative burden. Ultimately, using digital tools can help to create safer work environments here is why:
- Enhanced safety compliance tracking and management: Digital safety platforms allow for easy tracking and management of safety protocols, inspections, and incident reports, helping construction managers identify high-risk areas and take steps to mitigate risks.
- Real-time incident reporting: Mobile communication apps enable workers to report incidents and near-misses in real-time, allowing for swift action and investigation.
- Trend identification and analysis: Digital tools can help construction managers to identify trends in accidents and near-misses, allowing for proactive measures to be taken to reduce the risk of accidents.
- Improved communication and collaboration: Digital communication tools can facilitate regular safety meetings and training, and provide a platform for workers to raise safety concerns or suggest improvements.
- Efficient onboarding: Digital tools can streamline the onboarding process for new workers, ensuring that they receive the necessary safety training and information before starting work on a site.
- Accurate incident investigation: By digitizing the incident reporting process, construction managers can ensure that all incidents are promptly and accurately recorded, and that relevant stakeholders are notified.
Digital tools are essential for construction managers who are looking to develop a culture of safety and reduce the likelihood of accidents and injuries on their sites. By leveraging digital tools, construction managers can enhance safety compliance tracking and management, enable real-time incident reporting and investigation, identify trends in accidents and near-misses, improve communication and collaboration, streamline onboarding, and ensure efficient incident reporting and investigation.
The Benefits of Using Xenia for Construction Safety
Construction sites are inherently hazardous environments, but with the right tools and processes in place, accidents and injuries can be significantly reduced. Xenia is a powerful software platform that can help construction managers to improve safety and prevent accidents on their sites. Here are some of the key benefits of using Xenia for construction safety:
👷 Subcontractor management
This feature enables construction managers to assign tasks to subcontractors and track their progress in real-time, ensuring that they adhere to safety protocols and complete their work safely and on time. By centralizing communication and data collection, Xenia makes it easier for construction managers to monitor the safety performance of their subcontractors and address any potential hazards before they become accidents.
📒 Daily Logs
These logs serve as a primary mechanism for communication between construction managers and their clients. Xenia's daily logs feature allows construction managers to keep track of progress across multiple projects and subcontractors. It also enables workers to report any delays, safety issues, or materials used during construction. By having a centralized digital log of each day's activities, construction managers can quickly identify any potential safety concerns and take proactive measures to prevent accidents.
📝 Punch Lists
Quality assurance checklists that help identify and correct any errors or defects in the construction work before final payment is collected from the client. Xenia's checklist builder feature allows construction managers to create customized punch lists and attach them to specific tasks or work orders. By using Xenia to manage punch lists, construction managers can ensure that all safety-related issues are identified and addressed before the project is completed, reducing the likelihood of accidents and injuries.
🦺 Site Safety Management
Site safety management is a critical aspect of construction safety. Xenia's checklist builder feature allows construction managers to create checklists for site inspections, toolbox talks, and hazard reports. By using Xenia to manage site safety, construction managers can ensure that all workers are aware of potential hazards and have the necessary training and equipment to work safely. Real-time tracking and reporting of safety compliance enable construction managers to identify potential hazards and address them before they become accidents.
🏗️ Equipment Maintenance
Equipment maintenance is an essential part of construction safety. Xenia's task and work order management feature allows construction managers to create tasks for equipment maintenance and assign them to specific workers or subcontractors. Construction managers can ensure that all equipment is regularly inspected, cleaned, and maintained, reducing the likelihood of equipment failure and accidents.
📊 Enhanced Reporting and Analysis
Xenia offers a range of reporting and analysis tools that can help construction managers to better understand safety trends and risks across their sites. These tools can provide real-time data on safety performance, incident reporting and investigation, and compliance tracking. By analyzing this data, construction managers can identify areas for improvement and take proactive measures to prevent accidents and injuries. They can also use this data to provide evidence of compliance for audits or regulatory requirements, and to demonstrate their commitment to safety to clients and stakeholders.
Xenia is a powerful software platform that can help construction managers to improve safety and prevent accidents on their sites. Its various features and tools, such as subcontractor management, daily logs, punch lists, site safety management, and equipment maintenance, provide construction managers with the real-time tracking and reporting necessary to identify potential hazards and address them before they become accidents. By using Xenia to manage construction safety, construction managers can develop a culture of safety and reduce the likelihood of accidents and injuries.
.webp)
%201%20(1).webp)