Total American construction spending in 2023 surpassed $2.1 trillion.
When it comes to construction, quality assurance is a fundamental part of the industry, and as such, should be included in all projects. Construction has many dynamics and factors that define the industry. However, many other aspects of construction relate directly to QA. These include safety, planning, estimating, materials management, subcontracting, and construction equipment.
While most construction managers use quality control (QC) to help minimize any deficiencies in the finished product, quality assurance (QA) usually involves customer expectations being included in the contract.
Quality Assurance (QA) has a vital role in construction project management by focusing on the prevention of error at the beginning of the planning stage of the forming processes to reduce the risks, costs, and project outcomes. QA serves as a precautionary action for defects by evaluating the project to check if all the necessary legal or regulatory standards have been applied and protecting the stakeholder’s interest.
In a construction project, quality assurance entails the development and implementation of a system to ensure that the final product meets the specified requirements. Since mistakes in a construction project can result in serious safety risks for the project’s potential future occupants, it’s vital to ensure the quality of the project during the construction process.
This post explains the benefits of quality assurance in construction, its importance in developing safe buildings, as well as the benefits of using Xenia for quality assurance.
Priced on per user or per location basis
Available on iOS, Android and Web
What is Quality Assurance?
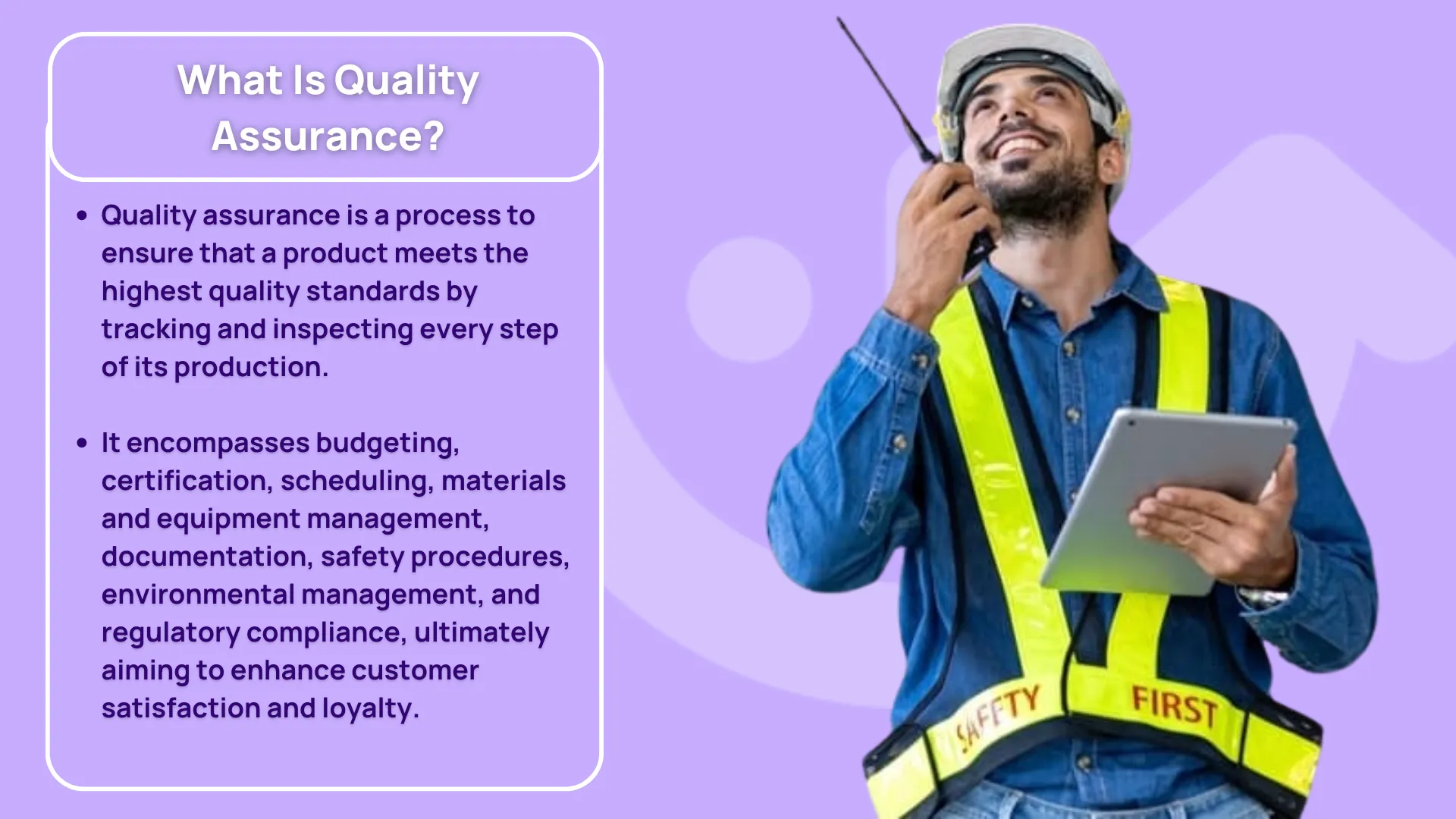
Quality assurance is a process or set of actions to ensure that a product is the best of quality. QA is used to track the process of product representation that is also used in prevention, comparing the quality and inspection of the product.
QA is done at every step and in any other sector, production of a certain product. The main benefit of QA is customer satisfaction and confidence in your product has increased and over time it will increase the loyalty of the customers and increase the sales.
The scope of quality assurance covers the following elements of the construction process
- Budgeting
- Certification
- Scheduling
- Materials and equipment management
- Documentation
- Safety procedures
- Environmental management
- Regulatory compliance
Most Common Construction Issues
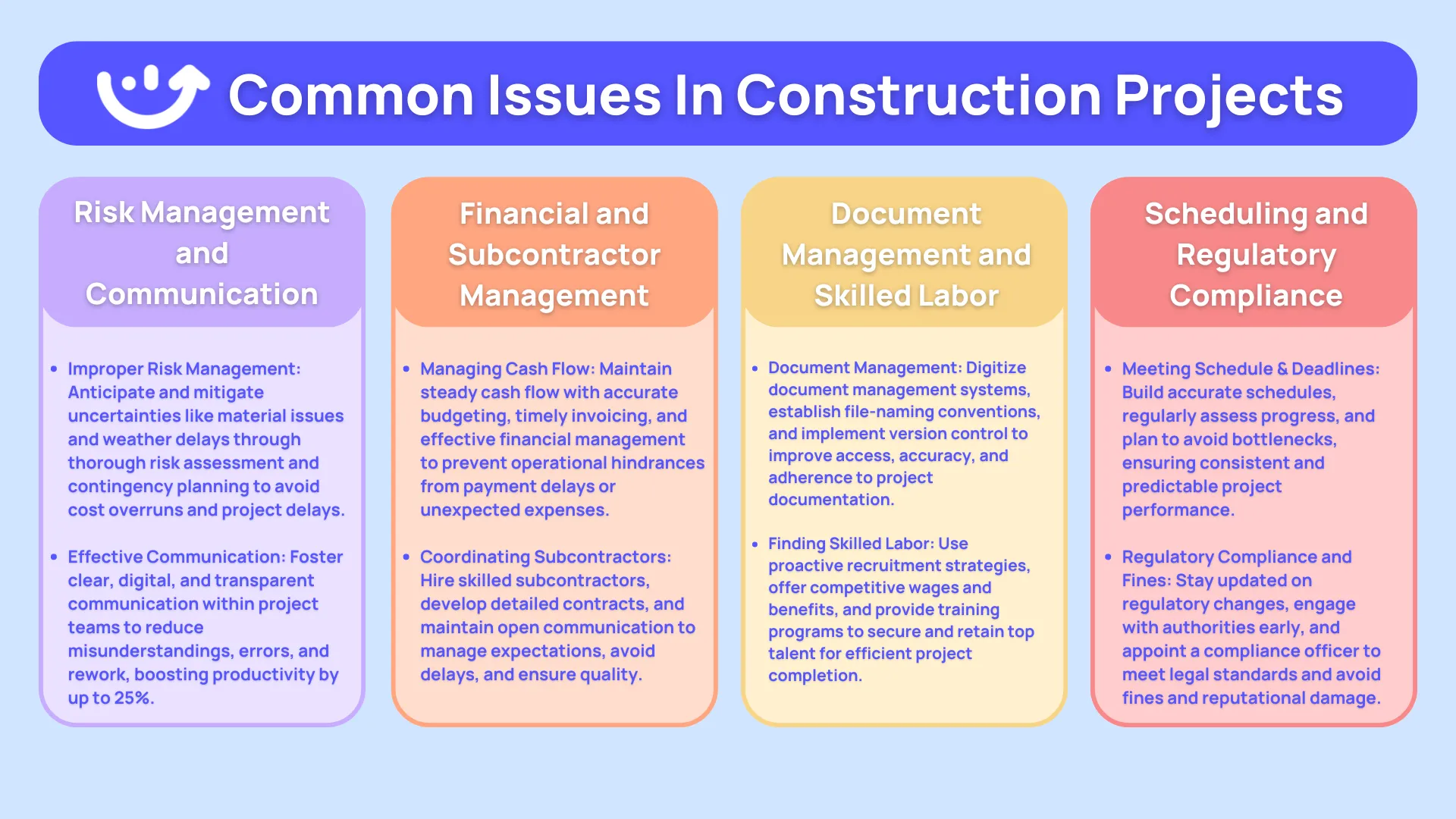
Knowing and acting in advance to mitigate any problems can save you a lot of time, money, and grief. Let’s take a look at some of the big boys in the construction industry and some ways to deal with them.
Improper Risk Management: Many uncertainties can plague the construction field, ranging from material issues to weather delays. Without anticipation or some type of mitigation, these issues can cause cost run-ups as well as project blow delays. 72% of companies report that projects have exceeded their expected duration.
By being proactive and taking the time to perform a thorough risk assessment as well as putting in place contingency plans, the impacts of these events can be mitigated.
Communication: Effective communication is the foundation on which successful construction projects are built. Effective communication within teams may lead to a significant productivity boost of up to 25%. Misunderstandings among designers, contractors, or subcontractors can lead to mistakes, rework, and unsatisfied clients.
By clearly defining communication, managing by a digital record, and fostering a culture of collaboration and transparency, project teams can significantly reduce these costly errors and minimize the risk of running over budget or off schedule.
Managing Cash Flow: Maintaining enough cash flow is critical to keeping a project progressing by sustaining the operations of the project. Delays in payment from clients or supplies along with unexpected expenses can critically hinder project operations.
Implementing good project financial management methodologies, such as creating an accurate budget, and promptly and accurately invoicing project households can maintain a steady cash flow throughout a project.
Coordinating Subcontractors: Coordinating with subcontractors increases complexities in project management as it involves coordinating with multiple entities that have different schedules and expertise. Poor subcontractor management results in delays, quality issues, and disputes.
Ensure investment time in hiring subcontractors, ensure to development of detailed contracts to manage expectations, and maintain open lines of communication to make sure relationships are productive and ultimately, maintain an efficient workflow.
Document Management: In the age of digital operations, finding your project team drowning in file folders is a very real concern for many construction professionals. Failure to manage documents like blueprints, permits, and contracts carefully can lead to confusion, legal disputes, and delays.
Digitizing your document management system, establishing a file-naming convention, and implementing a system for version control and revisions, is a fast track to improved access, accuracy, and adherence.
Finding Skilled Labor: The demand for skilled labor often outweighs the supply in many areas of the construction industry. This can lead to quality and timeline challenges if a competent workforce is not attained.
Using proactive recruitment strategies, offering competitive wages and benefits, and providing training and development programs can ensure access to and retention of top talent to complete construction projects efficiently.
Meeting Schedule & Deadlines: In the construction industry, time is money. Deviations from the schedule affect everything, especially costs and client satisfaction. Many factors can affect this schedule on the field, such as weather, material delays, and manpower problems.
Building good schedules, assessing the progress of all activities, and planning to avoid bottlenecks are key to consistent, predictable performance.
Regulatory Compliance and Fines: Obtaining the necessary permits is one of the major tasks of project management in construction. The regulatory requirements and potential fines for non-compliance can be staggering, from project delays to damage to the company’s reputation.
Staying updated of regulatory changes, engaging with regulatory authorities early in the planning process, and appointing a knowledgeable compliance officer can help ensure legal and risk standards are met.
Benefits of Quality Assurance in Construction Projects
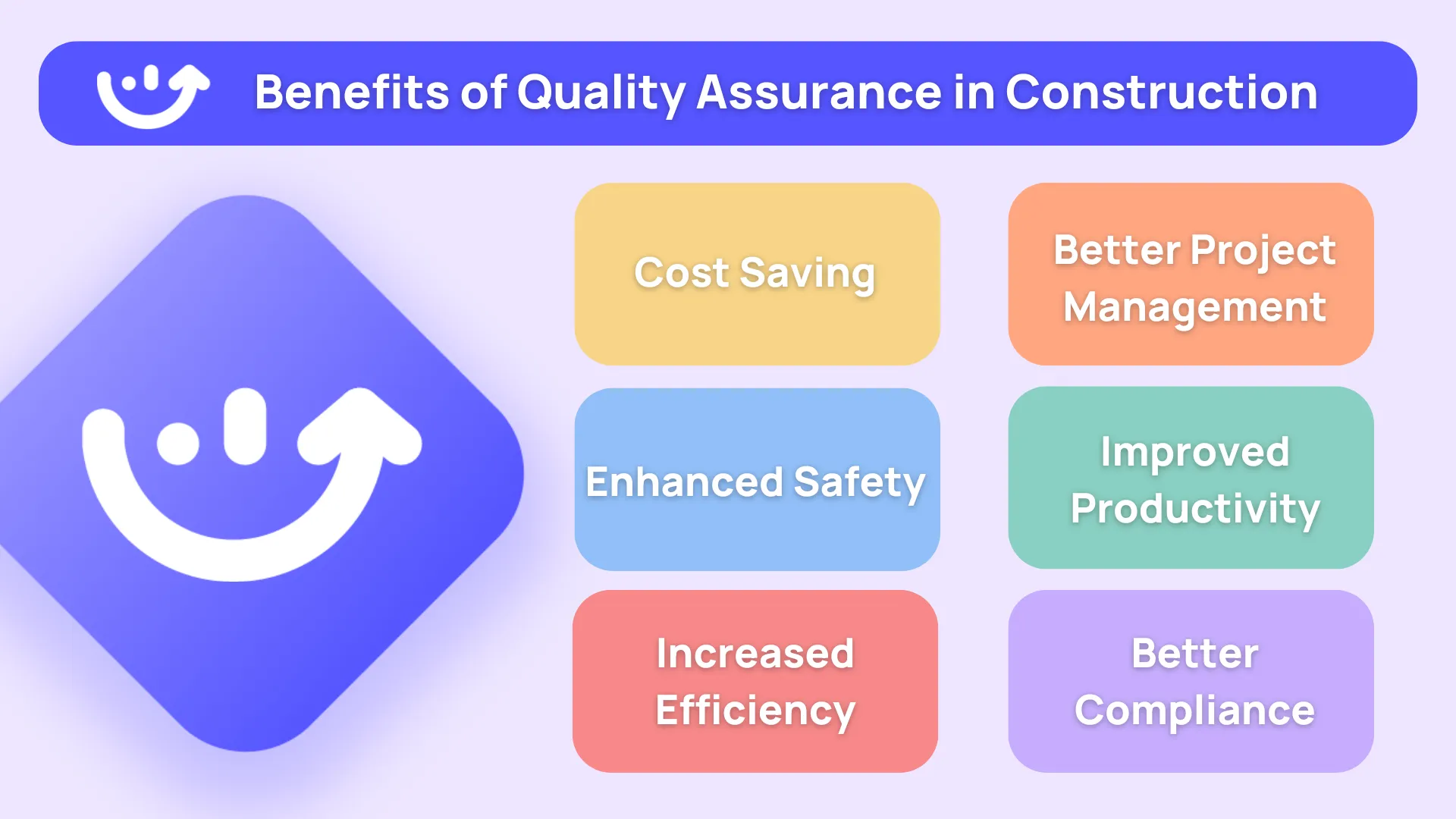
Construction companies must bring in Quality Assurance (QA) practices to enhance operational efficiency, compliance adherence, communication clarity, worker safety, and customer satisfaction.
1. Improved Operational Efficiency
Almost everything in construction links back to operational efficiency. This includes profit margins, sticking to scheduled timeframes, and customer satisfaction.
One of the several benefits of quality assurance in construction is enhanced operational efficiency by creating realistic timelines, cash flow analyses, and the cost-benefit analysis of purchasing materials.
Estimating future problems to avoid poorly budgeted projects. All of which aid in staying within budgetary constraints. By managing these features, construction safeguards the uber-high standards to notch up operational efficiency.
2. Properly implement the standards
Following the multitude of regulation guidelines and keeping up the pace of the safety precautions can be very daunting for construction project managers.
Another benefit of quality assurance in construction in this regard is compliance, helping the stakeholders by guiding them through the maze of documentation and the required safety standards.
The companies following the best practices as recommended by QA not only save themselves from the huge number of fines but also show they are committed to the safety culture of their entity along with regulatory compliance which finally contributes a lot in gaining high-performance outcomes and maintaining the business in the long run.
3. Reduce Communication Issues
Effective communication is critical within temperatures with the intricacy of construction.
But the noise and language separation affect the flow of communication consequently information is shared differently and therefore this motivation hinders good communication flow.
The benefits of quality assurance in construction also include addressing those communication gaps by creating transparency between construction environments and standardizing the guidance on how information should be shared.
Having a common language standardized for the managers and the workers/ deployers on the construction sites and also having a clear command Chain of command, QA provides a fruitful construction communication environment which directly reduces the risks and improves the operation.
4. Improved Worker Safety
There are about 651,279 fatalities recorded worldwide each year due to illnesses caused by toxic chemicals in construction.
The inviolability of any construction project hinges on the safety and well-being of its workforce.
QA brings in a paradigm shift in the safety protocols by identifying and preventing accidents before they happen.
Starting from the material handling procedures to equipment management is being addressed by QA and this new intervention in the construction industry ensures the smooth and strong scaffolds of the worker safety, thereby promoting the consciousness and adherence to the best practice.
5. Customer Satisfaction
The main litmus test of every construction venture is customer satisfaction. This is where excellence rather than mere compliance turns up. While QC can cater to surface aesthetics, the benefits of quality assurance in construction go further, it ensures the key factors of structural soundness and functional efficiency.
By consistently exceeding customer expectations in terms of both quality and reliability, QA creates client loyalty.
How to Implement QA in Construction Projects
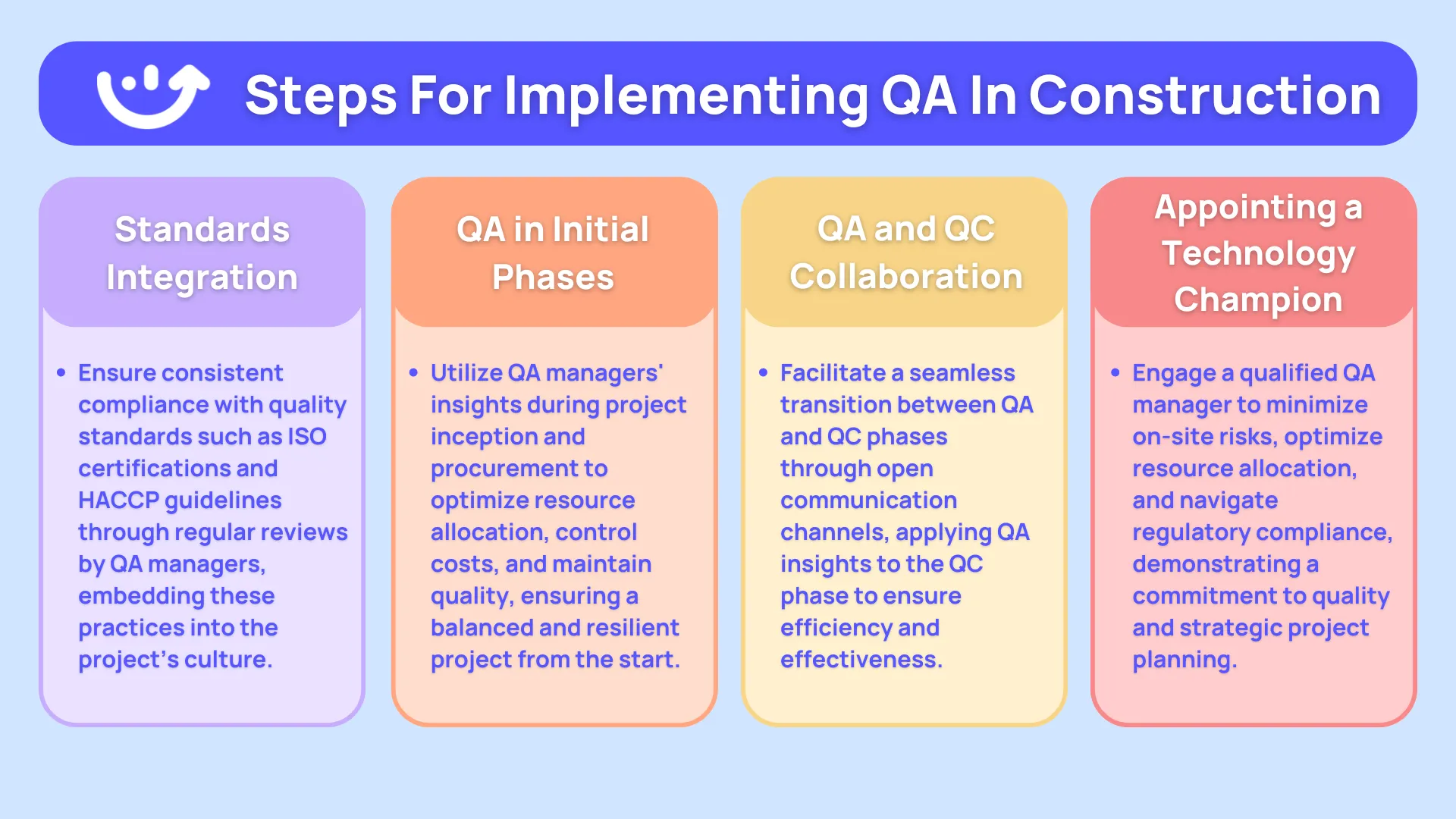
Integrating and reviewing the proper standards
When it comes to developing a truly effective QA program, the common denominator is consistent and regular compliance with set quality standards.
From ISO certifications to HACCP guidelines and standard operating procedures, all practices must substantively align with laid-out quality benchmarks.
Regular reviews by QA managers ensure that quality standards are not merely checked off as completed, but are a lived and practiced standard driving your food safety and quality culture through any of their construction projects.
Establish a Communication Chain of Command
Communication serves as the lifeblood of construction projects, orchestrating a symphony of actions and decisions across diverse stakeholders. Establishing a robust communication chain of command, whether through traditional hierarchies or digital collaboration platforms, engenders clarity and accountability, mitigating the risk of errors and misunderstandings.
By fostering seamless communication pathways, QA becomes the linchpin that binds disparate elements of the project ecosystem into a cohesive whole, amplifying transparency and efficiency.
Lean ON QA During Initiation and Procurement Phases
The inception and procurement stages of construction outline the very success of the project right from scratch wherein the quality Assurance Managers play a vital role by providing their expert insight on optimum resource allocation and a procurement strategy that merges the cost variance with quality.
The Quality Assurance insights help stakeholders to filter out the right material at the right time and at the right cost leading to an optimal cost control of the project keeping elements like quality not at stake.
By embracing Quality Assurance in the very first phase of the construction enables resilience of the project with balanced options of quality and cost.
Active Testing and Review
Through each stage of construction, QA professionals employ and implement active testing and reviews throughout the project process from start to finish and examine the project cycle with a proactive way of thinking.
Quality Assurance embeds compliance and quality checks at specific points in the life of a project ensuring that projects stay on track linked to defined specifications avoiding deviations therefore enforcing confidence in the final output.
Create a Smooth Handoff Between QA and QC
The seamless transition between QA and Quality Control (QC) heralds the culmination of meticulous planning and rigorous oversight.
Registering this accomplishment facilitates the creation of open communication channels, which promotes a symbiotic relationship between QA and QC professionals.
The insights gained from QA processes are then applied to the QC phase, solidifying this symbiosis.
By promoting transparency and collaboration, all stakeholders can be assured they are combining their efforts to deliver projects most efficiently and effectively.
Find an experienced QA Manager
To ensure construction excellence, an experienced QA manager is a must. By engaging a qualified QA expert, you are not only demonstrating your commitment to quality but also planning strategically to minimize on-site risk and optimize resource allocation.
A qualified QA manager familiar with both QA and QC methodologies will act as the custodian for the integrity of your project, leading all project stakeholders through the maze of regulatory compliance and operational complexity.
.webp)
%201%20(1).webp)