Managing maintenance tasks in today’s fast-paced industries is no small feat. From routine inspections to emergency repairs, chief engineers and maintenance managers juggle countless responsibilities, all while ensuring safety, compliance, and profitability.
The key to handling these demands effectively? A streamlined, digitized work order system.
Work orders are the backbone of maintenance management, offering a structured approach to assigning, tracking, and completing tasks across various industries like construction, manufacturing, and facility maintenance.
They’re more than just task lists—they provide detailed instructions, priorities, technical requirements, and even cost evaluations, ensuring no detail is overlooked.
Whether it’s preventive maintenance, corrective actions, or urgent repairs, the right work order process keeps operations smooth and efficient. This guide dives deep into everything you need to know about work orders, from their components and types to their lifecycle and importance.
Plus, you’ll find free checklists to help you implement or enhance your own system.
By mastering work orders, you can optimize workflows, prevent costly delays, and maintain operational excellence. Ready to take your maintenance management to the next level? Let’s explore how work orders can transform the way you handle tasks, one request at a time.
Priced on per user or per location basis
Available on iOS, Android and Web
What is a Work Order?
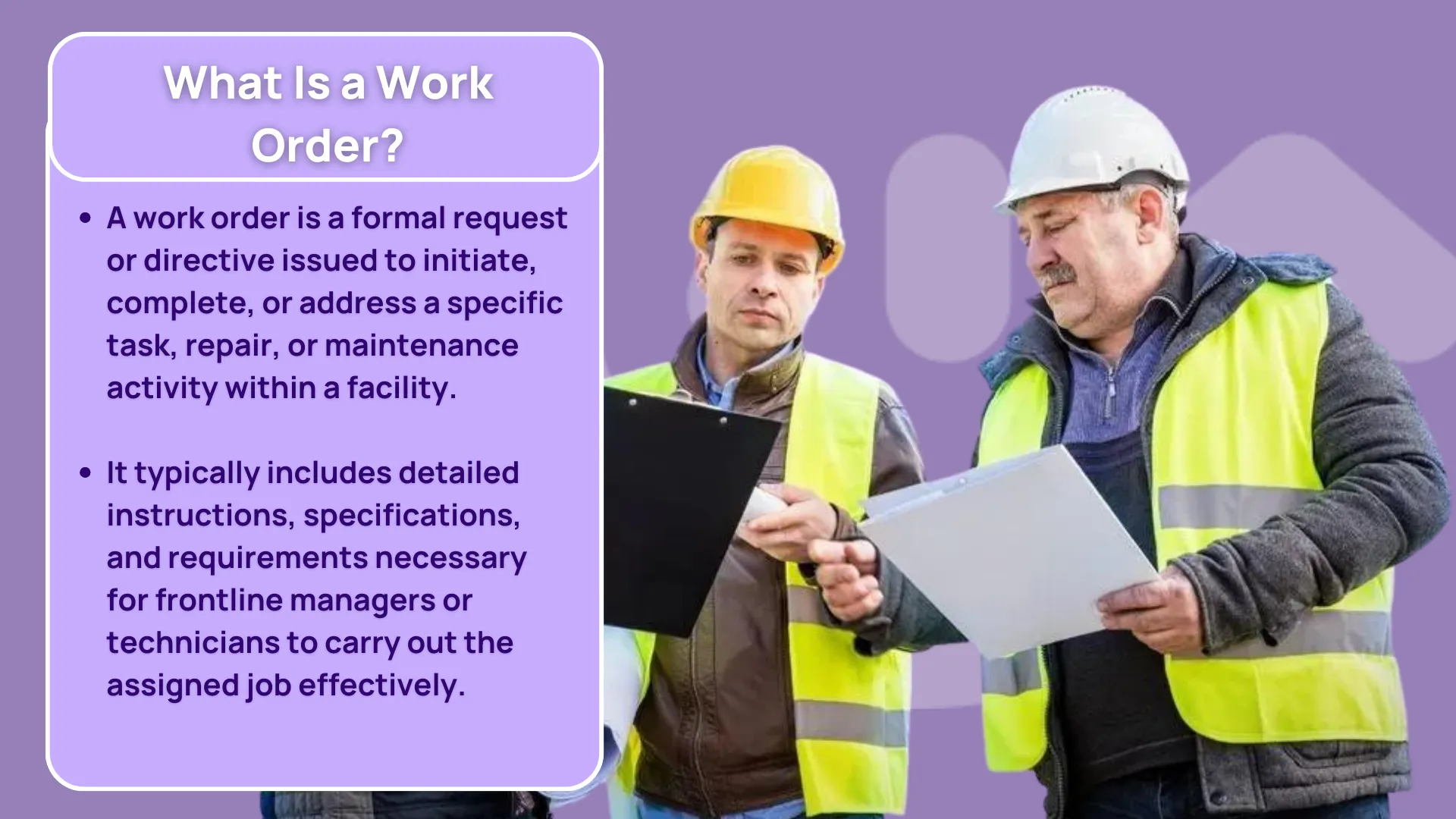
A work order is a formal document that encompasses the power of a task that one needs to perform under the scope of work restricted.
To complete a job successfully, each work order has specific requirements and specifications that one must follow.
Moreover, beginner level frontline managers should know that any work order is a comprehensive directive that includes various types of information as possible.
These orders are extensively used in a variety of industries such as Construction, Manufacturing, and Maintenance to organize and execute a job in a reasonably fast and effective way.
Types of Work Order Requests
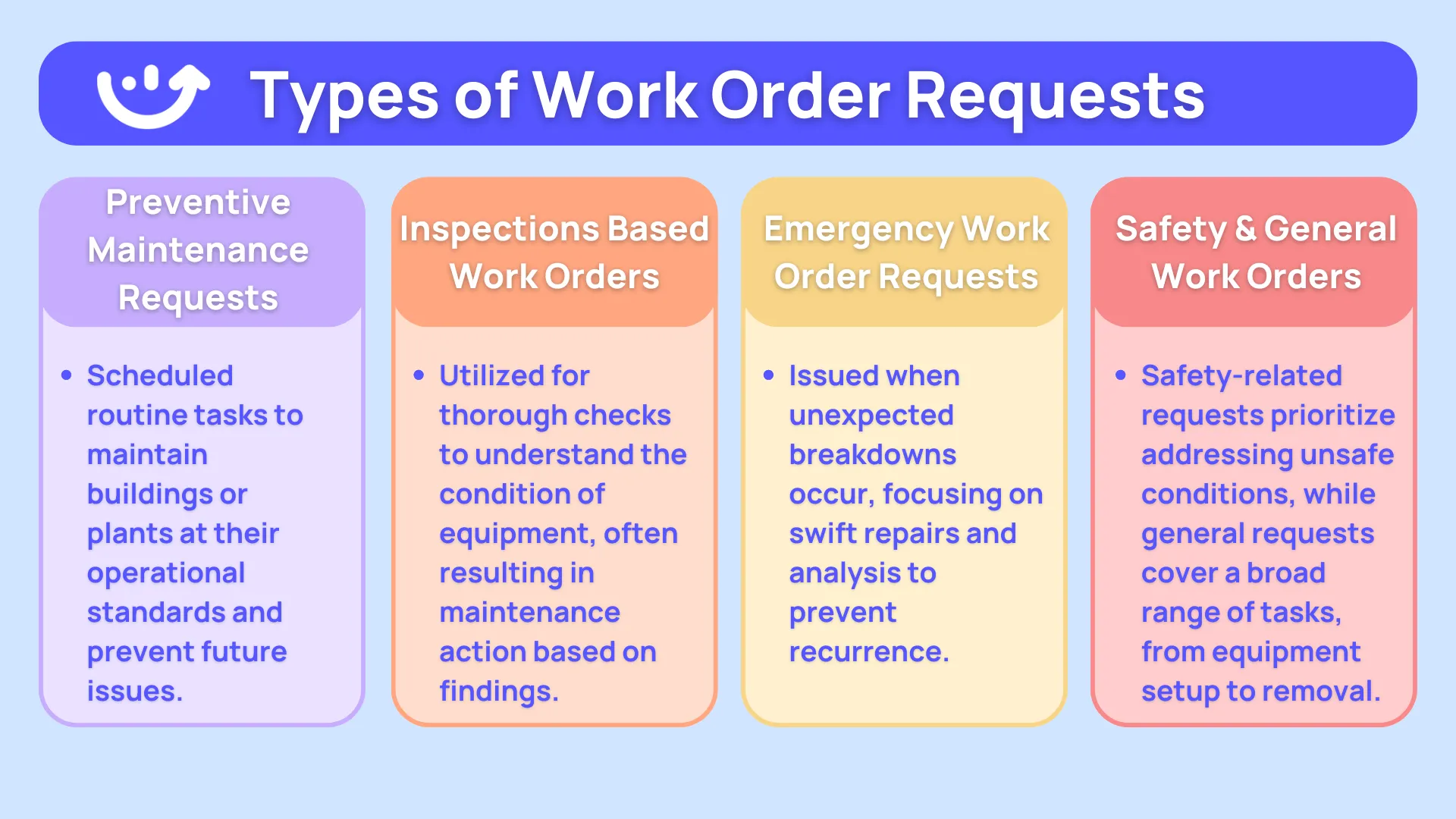
- Preventive Maintenance Based Work Orders - Normal routine work that is scheduled to keep a building or physical plant operating, and up to the standards that the organization demands.
- Inspections & Audit Related Work Orders- When a maintenance technician needs to see the full condition of the machine, then an Inspection work request form template is created.
- Emergency Work Order Requests - Emergencies happen no matter how careful your team is—sometimes things break. This is when you’d use an Emergency work order. Not only to track the repair but to also analyze it to prevent it from happening in the future.
- Corrective Maintenance - Work order requests falling under this category are deployed to when maintenance processes need to be executed to remedy a machine failure, asset management issue, or anything related to on site equipment etc.
- Safety Related Work Orders - These work order requests comprised of these is that having discussing how the action was unsafe
- General Work Orders - General - This category is just about any maintenance that doesn’t fit in the other categories. General work orders can range from new equipment set up or a piece of equipment that needs to be removed.
Components of Work Order
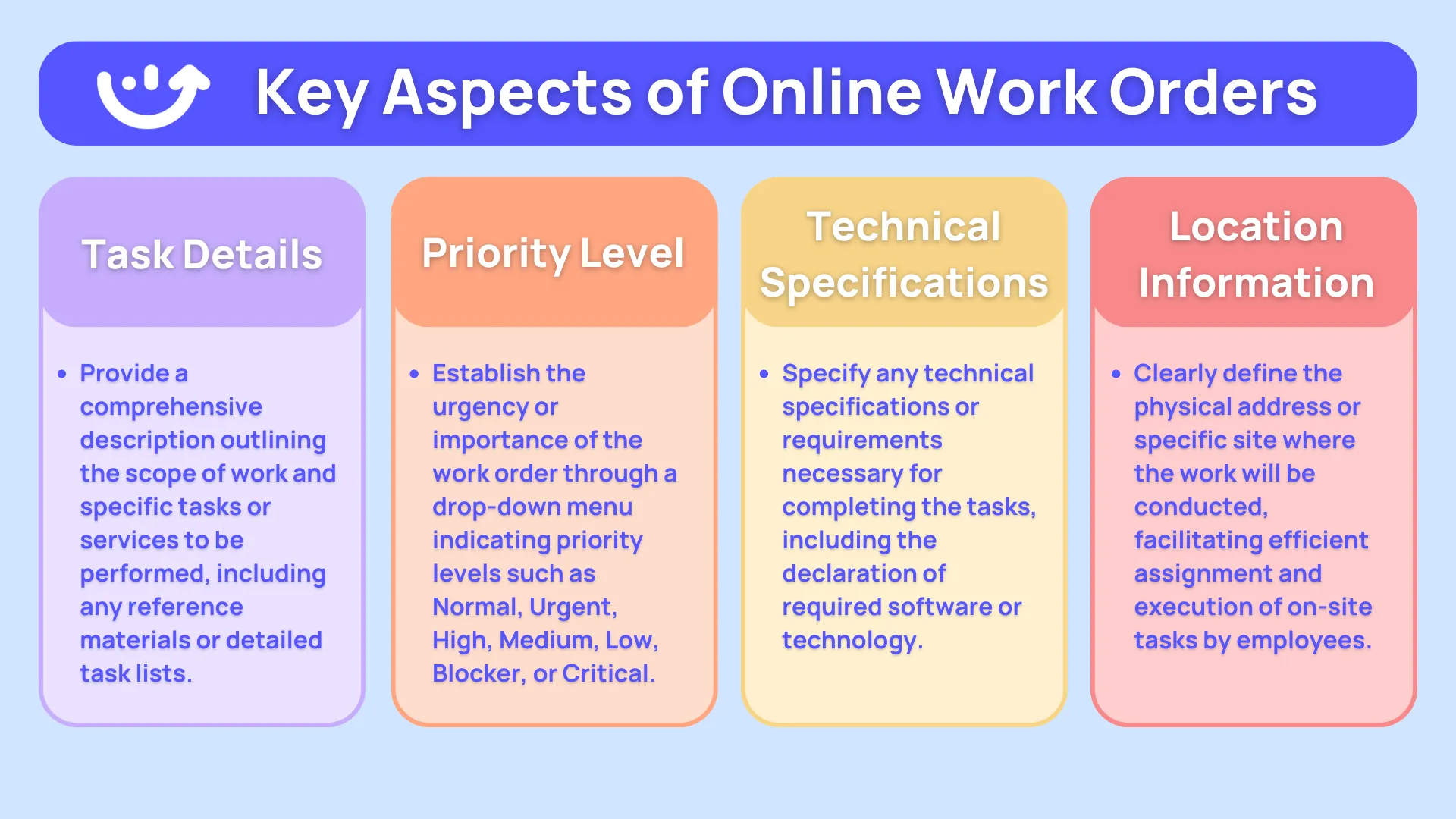
Task Details
- Provide a clear description of the tasks or services to be performed. The description should include enough information to allow a Receiver to obtain a clear understanding of the services or tasks.
- Be specific and outline the scope of work. Examples may include documents as reference material or a specific detailed list of tasks.
Priority Level
- Indicate the urgency or importance of the Work Order. The urgency level should be established to differentiate an urgent task from a normal task or a high-priority task from a medium-priority task.
This is in the form of a drop-down menu. Eg. Normal, Urgent, High, Medium, Low, Blocker, Critical.
Technical Specifications/Requirements
- Any specific technical specifications or requirements related to completing the tasks or services should be provided here.
- The Provider must declare if a specific software or technology is needed to perform the requested task.
Location Information
- Determine the physical address or specific site where the work will be done. This is important for on-site jobs so the employees know where to go to perform their assigned work.
Dates and Times
- These specify the start and end dates for each maintenance task assigned. These also communicate the availability and therefore the delivery time for a task.
Materials and Resources
- Will include any item needed to be used to carry out a task.
- Mention all resources that are used to complete a task. The resources help in the planning and resource allocation.
Cost Evaluation
- Any budgetary data that can be determined about the work order.
- The estimated costs for labor, materials, and other expenses related to the work.
Safety and Compliance
- Anything related to safety guidelines, compliance regulations, or requirements needed to perform the work.
- Ensures that the work is completed safely and complies with what is legal.
Importance of Work Order
Work orders organize jobs, ensure accurate and timely maintenance, and provide additional information to allow a more in-depth look at the internals of those industries.
The importance of work orders is the control of which they provide over the tasks or services at hand.
They do this by giving clear, formal, and concise instructions as to what the task is. By breaking down the work to be done and giving a detailed instruction they act as a blueprint to what is expected. During this, the sometimes vague door of communication between production/engineering and management can be opened a little wider.
Moreover, job/work order can be used to categorize the jobs based on urgency and importance.
Doing so enables organizations to allocate resources to prioritize the job/work order accordingly and deal with the most crucial work/order promptly.
Furthermore, it helps a lot when multiple works need to be done as early as possible, we can prioritize it and do the assigned job/work first which is in high priority therefore there will be no delay in work and the important work/order(s) can be done at early as possible which needs immediate action.
Maintenance work orders are critical for tracking the upkeep or repair needs of equipment.
They allow maintenance to be scheduled with detailed instructions and dates/times for possible use of tools, equipment, and other resources.
To that effect, these online orders can also be written to develop Proactive maintenance as contrasted to breakdown maintenance.
Life Cycle of Work Order
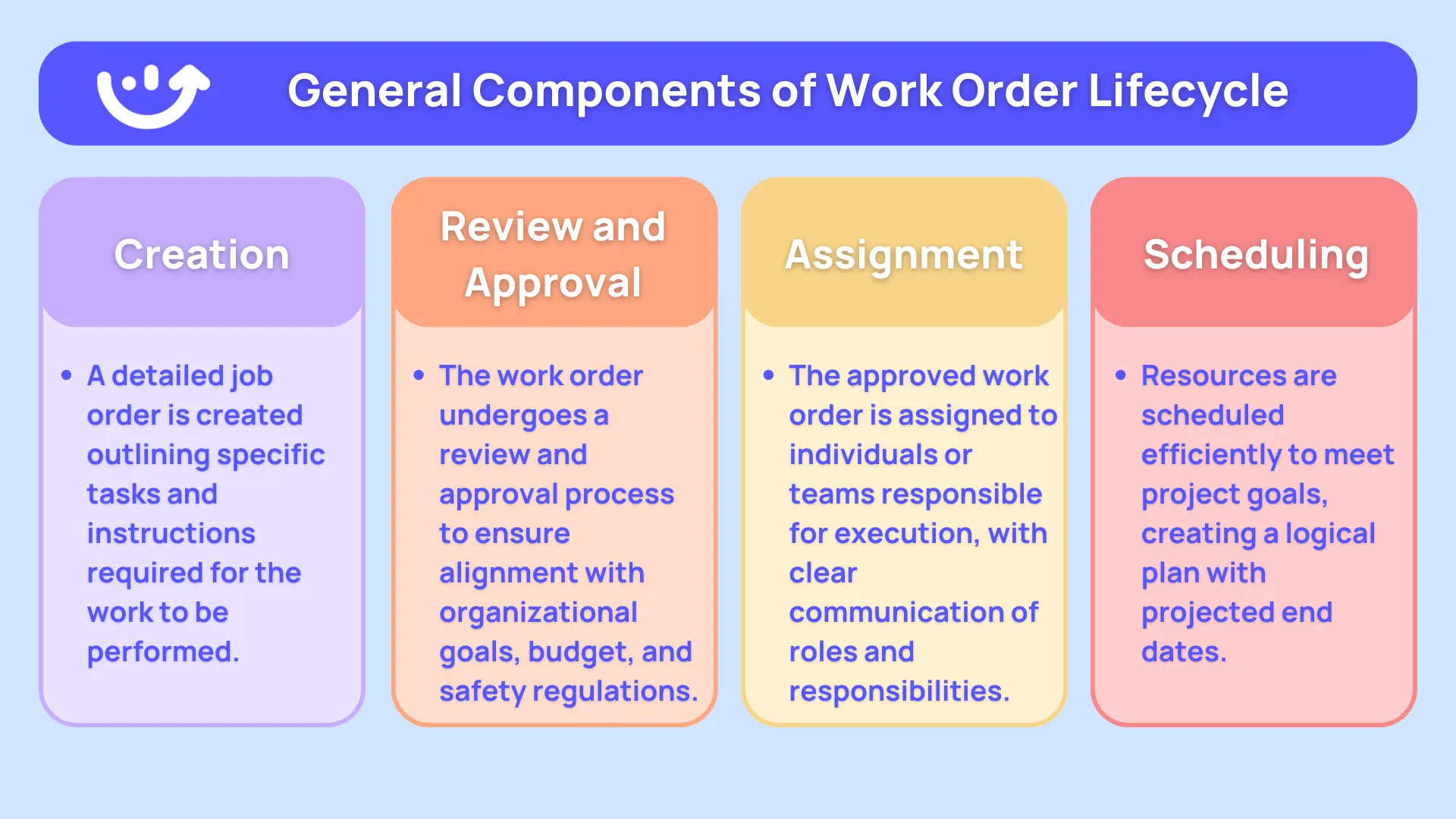
- Creation
During this stage, the manager or authorized person creates a job order. The job order contains a thorough detail about the specific tasks or services to be performed.
The job order form is one of the most important work order requirements that captures all the necessary details to carry out work for an approved job.
The clarity in the task descriptions, priorities, quantity, and other instructions is very crucial to set the base of a successful work order.
- Review and Approval
Before the scheduling of resources and execution of work is initiated the work order is typically subject to a review and approval process. The purpose of this step is to ensure that the work tasks are in alignment with the goals of the organization, budgetary constraints, and safety regulations.
Gaining the necessary approvals establishes a formally authorized state for the work to be executed.
- Assignment
After the approval, the work order gets assigned to the individuals or teams responsible for the execution. It is very important at this stage to communicate properly to avoid any more confusion and also to keep everyone aware of their responsibilities.
- Scheduling
Scheduling involves making sure that you have the ready or available resources you need to carry out your goal. Scheduling helps you to manage your resources efficiently, it helps you to create a logical plan for your project and provides a projected end date you want to achieve.
The main point of this topic is that it helps with everything as long as you have resources.
- Execution
To complete a project it needs to be executed promptly. It is important to understand task descriptions because doing the job wrong can lead to insufficient work being done.
Adhering to safety protocols is important because anything dangerous should be brought to the immediate attention of the contractor. Efficient utilization of resources helps in the smooth execution of the project.
- Monitoring and Tracking
Continuous progress monitoring is essential for ensuring that the managers stay on course and follow the time frames set. It allows for quick intervention if there are any issues, which could potentially lead to delays or deviations from the original plan.
- Completion
Once the job has been completed, the work order then goes to the completion process.
This entire process consists of validating that the job has been completed, you may have to do some inspections, confirm all of the job requirements have been met, and make sure your documentation backs you up that the job is fully completed.
- Documentation
The last step is the closures and the documentation portion of the work order.
Closing out the work order involves wrapping up any administrative items like the final dollar spent, customer feedback, or the necessary signatures or approvals.
Documenting the work order from start to finish serves as a valuable resource when performing any future reference, auditing, or continuous improvement initiatives.
- Feedback
Feedback is critical in evaluating how well the work order process was executed.
Gathering feedback from all parties involved in the process is critical in evaluating its success. There’s always room for improvement and there are always things to be learned from the last work order.
What Is a Work Order Request?
A work order is a formal document that communicates the critical details of any maintenance inspection, preventive or corrective action that drives workplace safety, compliance and quality.
A work order request is the process of identifying, documenting and communicating issues that require work orders to fix to the correct team member. Work order request processes must be consistent and detailed to ensure communication is clear and documentation is standardized over time.
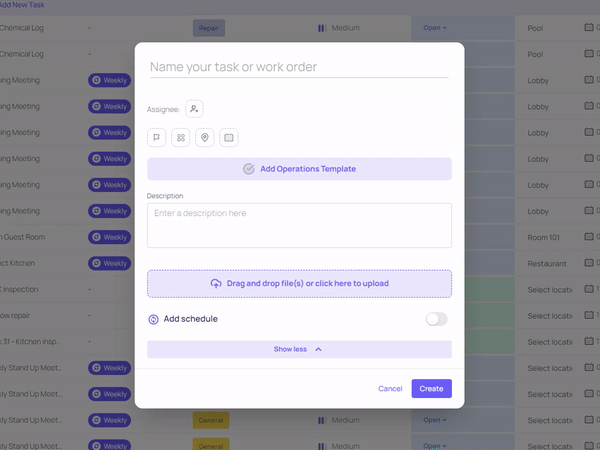
Historically, this task has been handled with pen, paper, clip boards and radio in a well-defined process that must be followed by all maintenance staff. Work orders act like a guiding compass that helps workers and managers to navigate through complex, deadline-oriented processes for successful completion. The goal of each work order request is clear and timely communication of relevant details to ensure proper action.
Before the inception of software solutions such as CMMS tools, facilities relied heavily on radios and long paper trails to complete a work order request. However, modern-day technological breakthroughs have simplified the process of maintaining and assigning a work order request, significantly decreasing the time to resolution and increasing asset lifespans.
Purpose of Work Order Request Forms
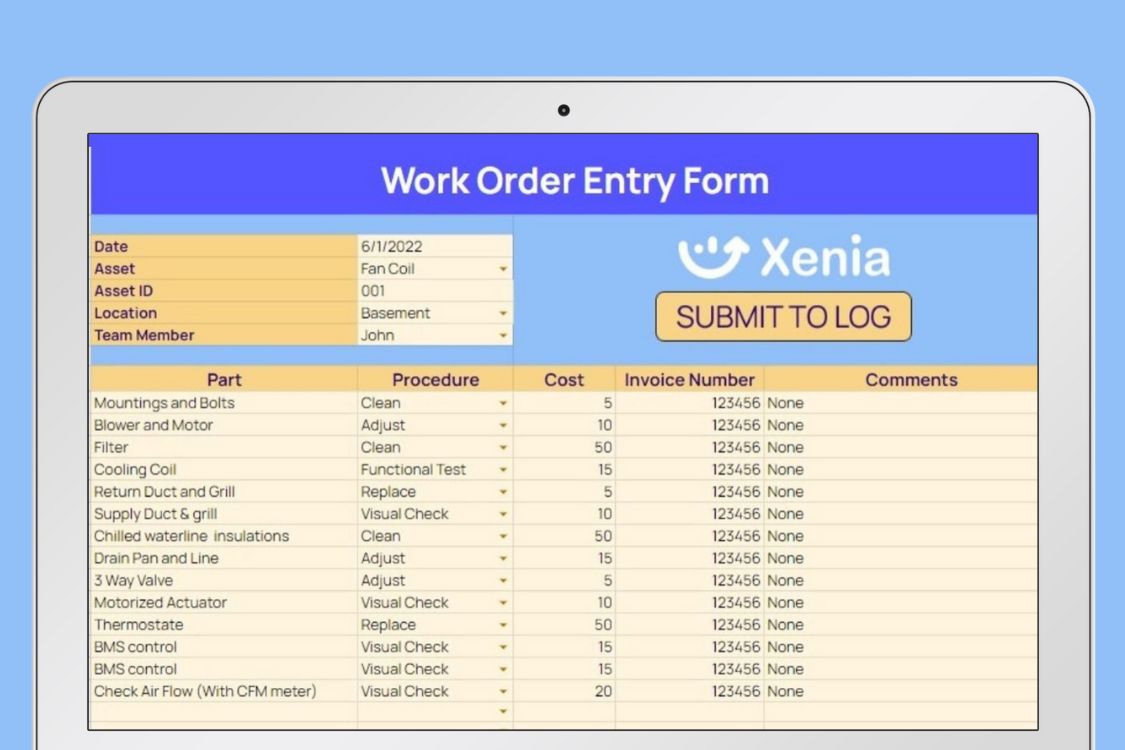
Capture All Necessary Information: Almost all work order request forms provide a structure for all the necessary information about the job or service being requested.
Work Order Request Forms help make sure the requester is giving all the details so it can minimize the risk of miscommunication when it comes to turning in forms that might not be completed.
Initiate Formal Requests: Work order request forms also provide initiation for a more formal request for the specifics of a particular job or to get a service for a company or organization dept.
They give a proper structure when it comes to ordering a work or service you need to be completed.
Provide Structure Work Order: A work order request form has all the necessary information to be completed about the details of a job given or services needed to be done to help see clearer about the type of work or job or needed to be completed if it is for the hospital or to mow the lawn.
Resource Prioritization and Allocation: It is common for work order request forms to include details about the priority of a given task, increasing organizations’ ability to efficiently prioritize and allocate resources.
In doing so, tasks that are urgent in nature are tended to promptly, leading to increased operational effectiveness as a whole.
Components of Work Order Request Form
Details of the requester
Information about the individual or department requesting the work request is accumulated here. This includes the name of the requester, contact information, and significant organizational details.
Description of task
A specific field for a detailed account of the services or tasks needed is maintained. Clear, detailed task descriptions are extremely beneficial for the accurate comprehension of the required work.
Level of Priority
Options or fields to determine the importance of the associated work request are included in this section. By distinguishing the importance of the given assignment, resources are efficiently allocated, and high-priority tasks are expedited.
Deadlines and Timelines
This section allows the requester to specify any deadlines or timeframes associated with the task. This information aids in scheduling and planning, contributing to timely task completion.
Location Information
This section includes a field to specify the physical location where the work is to be performed. This is particularly important for on-site tasks, ensuring that the assigned personnel are aware of the work location.
Attachments
This option allows the requester to attach any relevant documents, images, or files that support and provide additional context for the requested work. Attachments are an integral part of clear communication.
Work Order Description: What is the nature of the work? Is it a mechanical failure, maintenance-related issue, or scheduled inspection audit? The description needs to have a summary of the type of problem and (if possible) small details of the circumstances leading to it.
Work Order Assignee: Name of the technician or the technicians working on the task.
Location: The exact location where the work order needs to be executed. Some CMMS solutions can narrow down locations by site’s sub-levels. E.g., hotel rooms, floors, areas, etc.
Description of Completed Work: A brief description of work order completion and steps taken to rectify the problem.
Description of Incomplete Work: If the said team or a frontline technician couldn’t complete the work, what was the reason behind it?
Checklists: Summarize the steps to ensure successful work order execution and completion. Checklists are generally created in accordance with industry standards, compliance, and regulatory policies
Sign Off: Ensure that the issue has been resolved with third party review from a co-worker or manager. This protects against pencil whipping, a term used to describe workers who sign off on work that is not complete. Additionally a work order request may involve the following variables:
Work Order Priority: Often called task priority levels, they are used by managers to prioritize the task’s urgency. Xenia has different priority levels to enable escalation if required, as per the nature of the job.
Work Order Assigned Date: When was the work order created and assigned?
Expected Completion Date: When is the task scheduled to be turned over for a final fail or pass check from the supervisor or a concerned manager?
Documents: Many activities require photographic evidence of completion. The ability to take photos and upload them in the CMMS for managers to review makes it convenient for technicians to support their claim of successful task completion.
Work Request Form Template
![3 Ways to Manage a Maintenance Work Order System [+ Template]](https://cdn.prod.website-files.com/62294553e9aeea20d15d7bc2/66fc550f94e90a4f75a5ac9a_636d496051e53a0e57da3d06_Group%252048095895%2520(2).webp)
Template Functionality
- The use of a work request template ensures that pertinent information is systematically captured for different types of tasks.
- The standard format provides a simplified platform to enhance communication between the requesters and implementers by clearly defining necessary details.
Creating Customized Work Request Template
- Form owners can set up custom templates that cater to their specific line of work.
- Work request templates allow a wide range of response formats, such as text, numbers, multiple choice, and more, to fit individual tasks.
Automation and Logic Builder
- Utilizing automation and logic on forms allows tasks to be automated and specific actions to be taken depending on user responses, streamlining processes.
- The logic builder allows for inspections to occur allowing for forms to dynamically adapt to the user based on conditions, this leads to more accurate and efficient data collection.
Public Access through URLs & QR Codes
- Work request templates can be accessed by anyone through public URLs and QR codes.
- This feature makes external submissions easier, providing a convenient, user-friendly way for people outside of your organization to submit work requests.
Work Order Request System
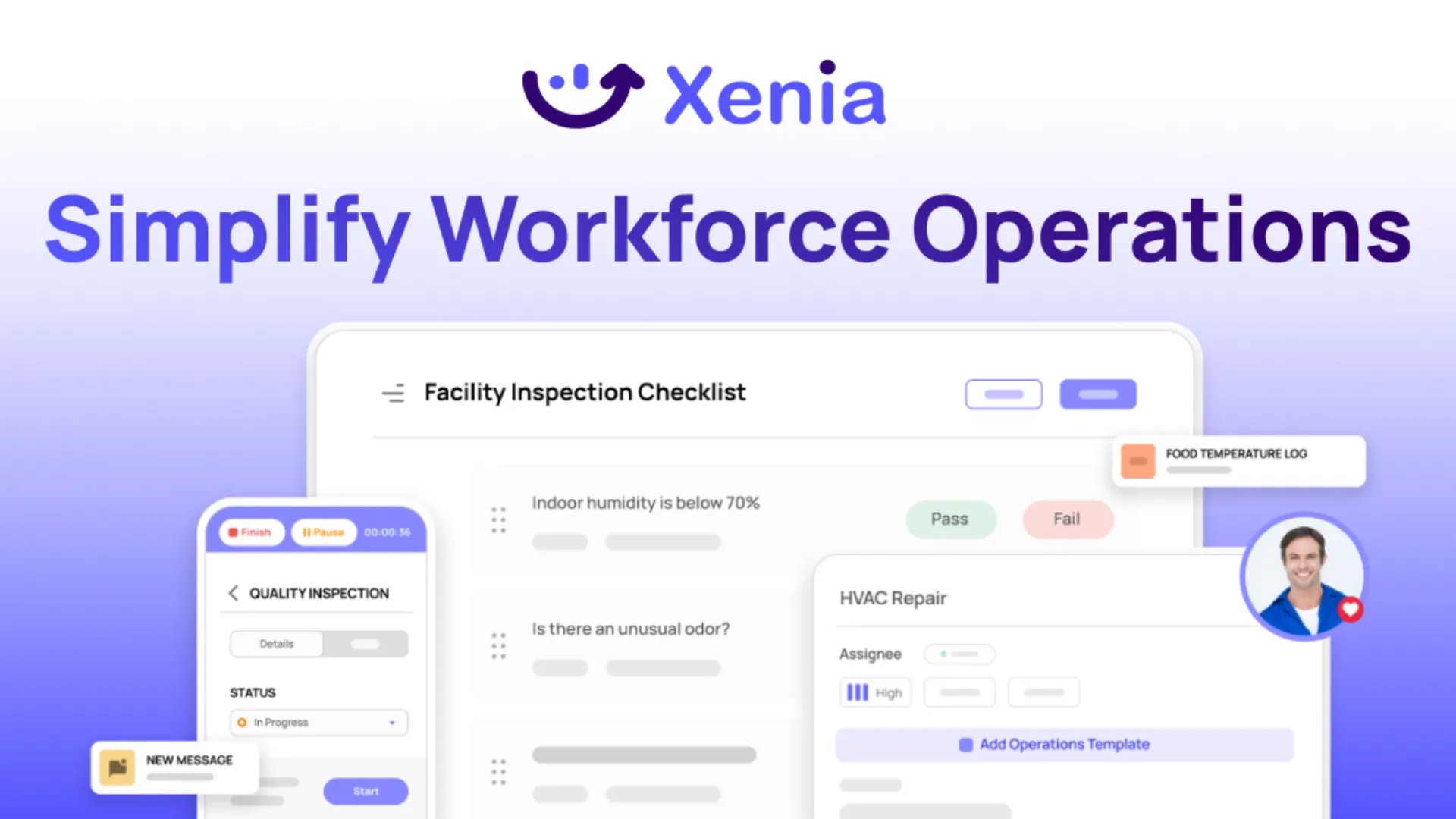
Work order request systems are software solutions that improve business organization in a streamlined process. They are mainly used to submit, register, and handle work order requests within an organization. Xenia is invaluable in organization sectors such as facility management, project management, and maintenance.
Work Order Submissions: Work order request systems provide a centralized area for users to submit work orders electronically. Most solutions offer user-friendly front-end interfaces, where individual requestors can enter details on the task, such as the description, priority level, and related documents.
Automated Routing: Automated routing helps data to be sent down the right paths since it directs it towards the right person or department to be reviewed, the approval workflow expedites the process and holds all parties accountable.
Task Scheduling: helps in assigning the different order of workloads to the various sets of the team which are allocated according to their skills and availability to get the work done as quickly as possible. it starts with Organising the tasks of each user and moves on to each stage of tasking.
Real-Time Tracking: This is the other important feature that enables all the users to track the various simple or complex workflows as it is moving from one stage to the other stages for helpdesk tickets. It updates each stage of the project in real-time such that are user can interfere directly if any obstacle occurs as is not done by the users.
Communication & Collaboration: Many work order request systems have built-in communication tools to make collaborating between team members even easier. This tool helps team members stay in touch as a way of working together on work order requests, it is used effectively between requesters or other stakeholders, and again it helps centralize all communication so the risk for miscommunication is extremely diminished.
Documentation & Attachments: Most work order forms can attach files and other documentation to the work order. This feature is useful to include other relevant information and documents, images, or other attachments to a work order. All documentation and media attached help other personnel make more informed decisions on the work to be done.
Mobile Accessibility: Mobile accessibility is a feature available in many modern systems allowing users to submit or track work orders from their mobile devices. This is particularly valuable for field personnel, who need access to and the ability to update work orders on the go.
Analytics and Reporting: Many Work Order Request Systems include analytics and reporting features.
These tools help organizations analyze data related to work order performance, resource allocation, and overall efficiency. Insights gained through analytics help inform decision-making and support continuous improvement initiatives.
Integration with Other Systems: The ability to integrate with other organizational systems such as asset management or inventory control ensures a more comprehensive Work Order Request System.
6 Common Use Cases of Work Order Requests
Seeing that work order requests cover different verticals in facility management and safekeeping, let’s take a look at some of them right now:
1. Scheduled Inspection
A scheduled inspection is a detailed review of the facility and its facilities maintenance.
This is done on a regularly to ensure that the facility is in compliance with all regulations, as well as to ensure that the facility is being taken care of properly.
Inspections can include checking for cracks in walls or floors; ensuring that doors open and close properly; checking for broken windows or lights; looking at fire alarms; checking for leaks in plumbing; testing air quality; and examining electrical systems.
Scheduled inspections are important because they provide a way for you to make sure that your facility is being taken care of properly by making sure you're following all regulations and standards.
2. Hazard Correction
A hazard is any factor that poses a threat to humans or their surroundings.
A hazard identification involves identifying all possible hazards in a given area, as well as determining whether those hazards can be corrected. Even if equipment or facilities are not broken or damaged, they can still be a hazard and require a work order request to resolve.
The most important part of hazard identification is making sure you have a system in place that allows you to identify hazards quickly and easily. If it takes too long for you to identify potential problems, then it might be too late by the time you do—and the solution might cost more than it's worth!
3. Preventive Maintenance
Preventive maintenance is the art of preventing a piece of equipment from breaking down.
It's important because it helps to ensure that your equipment is in top condition, which can save you time and money in the long run. Preventive maintenance work order requests can be asset inspections, cleaning , oiling or any other action that will decrease the likelihood of breakdown.
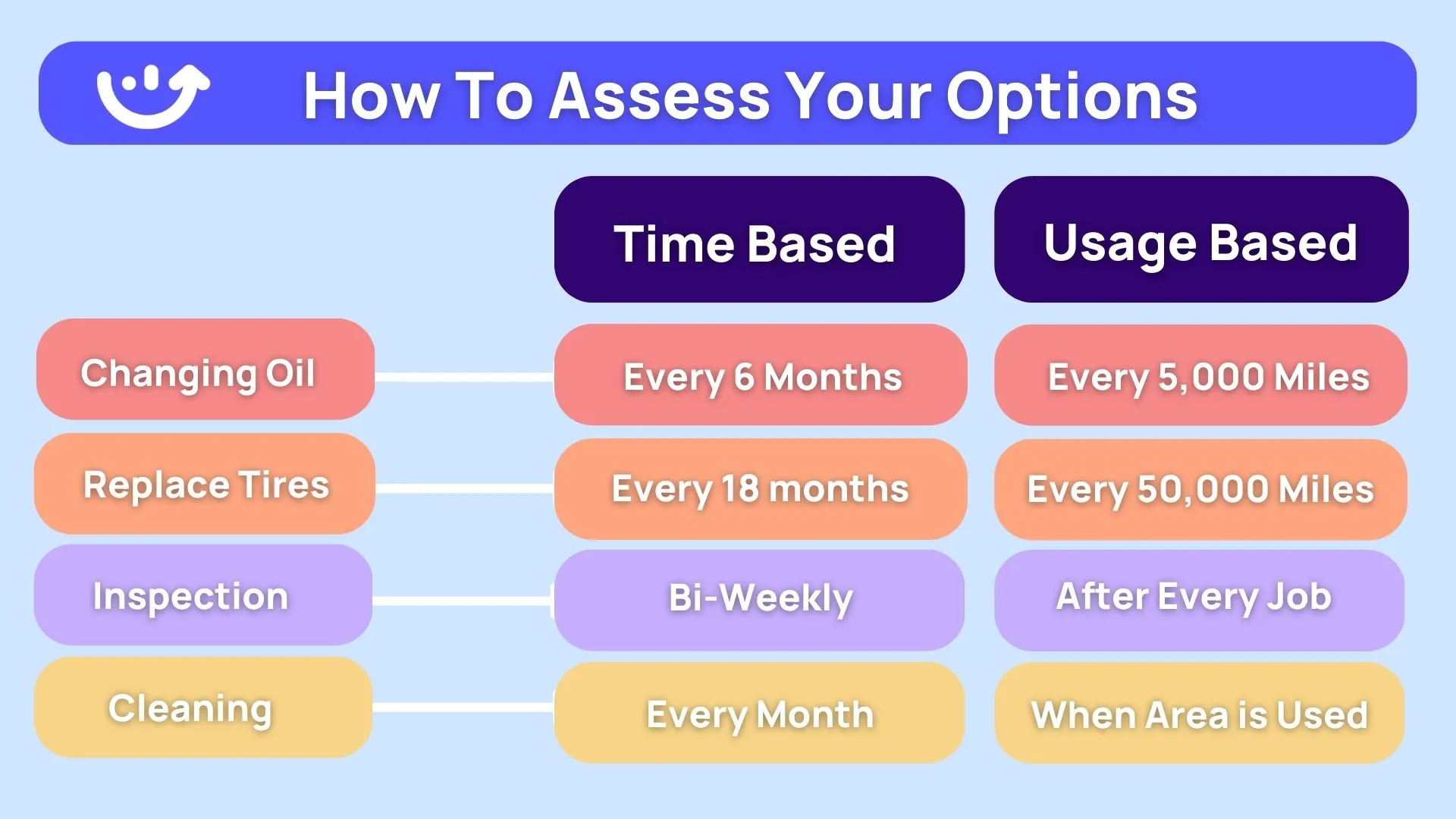
For example, if you notice that your air conditioning unit is starting to make strange noises, it might be a sign to create a work order request to analyze the system. It may just need a new filter or cleaning. Ignoring the noise, could lead to more serious issues, like a broken fan belt that requires corrective maintenance, which tends to be more expensive.
4. Corrective Maintenance
While working on preventive maintenance work order requests, if a technician stumbles upon something that needs to be fixed, an additional work order request is created to resolve the issue. Corrective maintenance is the process of fixing this broken or damaged property prior to significant technical or life-threatening problems.
It's important to facilities maintenance because it helps prevent these more serious problems from happening down the road. It also helps keep your building in good working order, which is good for you and your employees and customers.
Corrective maintenance is often done by a facilities manager or a contractor, but sometimes it's performed by someone with specialized knowledge or training.
The frequency of corrective maintenance depends on the type of property being maintained—if you're maintaining a warehouse with heavy machinery, you'll probably need to do more frequent corrective maintenance than if you're maintaining a small office building.
5. Emergency Maintenance
Emergency maintenance is maintenance that needs to be done immediately to protect the safety of staff and customers and continuation of business services. This differs from corrective maintenance in that the stakes are higher and the impact on operations is greater.
For example, if a technician notices that there is a crack in a wall, they may request a corrective work order. If that technician notices that crack in the wall is allowing bugs to infest a food storage room, emergency action is warranted. The issue in both of these situations is a crack in the wall. But the repercussions and urgency of the matter is very different.
Emergency work order requests require fast and detailed communication to resolve before the problem escalates further. More extensive post work inspection and sign off is needed before business operations can resume.
6. Asset Installation
Work orders aren’t only used to identify and put out fires. They are essential for facility improvement and ongoing renovation. For example, if a manager of a hotel needs a TV installed in 50 guest rooms, they create a work order request for the chief engineer to complete the task.
Work orders provide direction and tracking for these requests so that management can understand the cost and time needed to complete similar work in the future. This can also be used to compare the work efforts of multiple departments and employees to ensure that the best people for the job are assigned the work.
9 Benefits of Using a Digital Work Order Request Platform
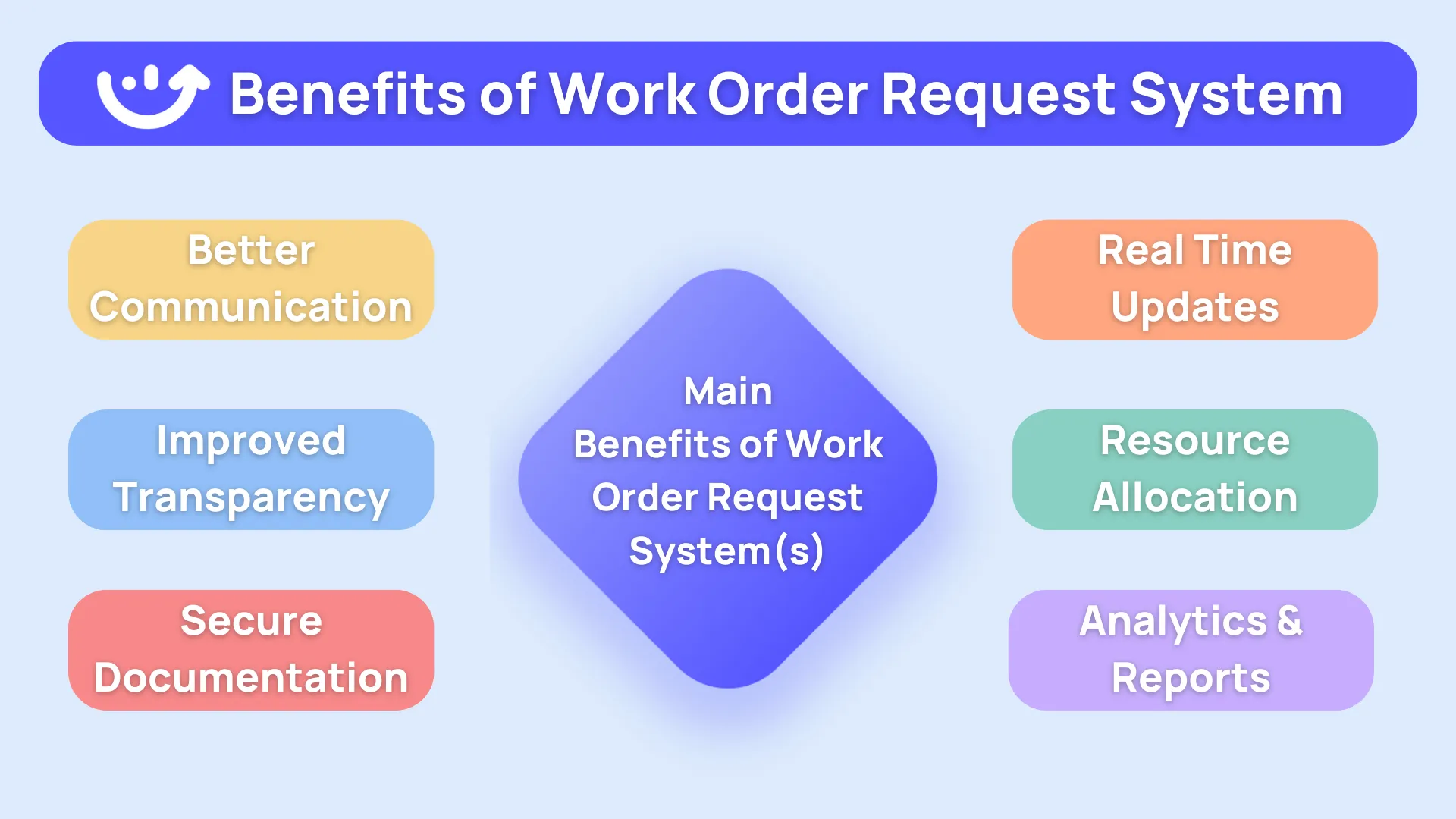
1. Increased Speed To Issue Resolution
In large facilities, there can be dozens of work orders that are created every day.
Maintenance managers can quickly get buried in requests, thus need to be able to organize and prioritize work to increase speed to resolution. Here are some ways a Centralized Maintenance Management System (CMMS) can help with this:
- Immediate communication with mobile push notifications
- Clear, typed description of work needed to eliminate handwriting decoding
- Task prioritization to ensure critical tasks are escalated
Furthermore, a CMMS can improve time tracking and provide data analytics to identify patterns to improve preventative maintenance and reactive work orders. All of these factors greatly increase speed to resolution.
2. Centralized Operation on Desktop and Mobile
With a digital work order request system, managers can finally ditch pen, paper and radio for a robust solution that works on both desktop and mobile devices. This improvement allows for multiple people to view the same work order and track progress to resolution in real time, no matter where the user is.
Assign work from a desk and have a technician begin work in the field immediately. No more lost paperwork or damaged reports. All of the data is safely and securely stored in the cloud of retrieval and analysis.
3. Easy Checklist and Procedures Attachment
Digital work order request systems often allow management to add comprehensive checklists detailing the steps to complete a specific work order request successfully. This cuts back on miscommunication and improves the likelihood of a successful work order.
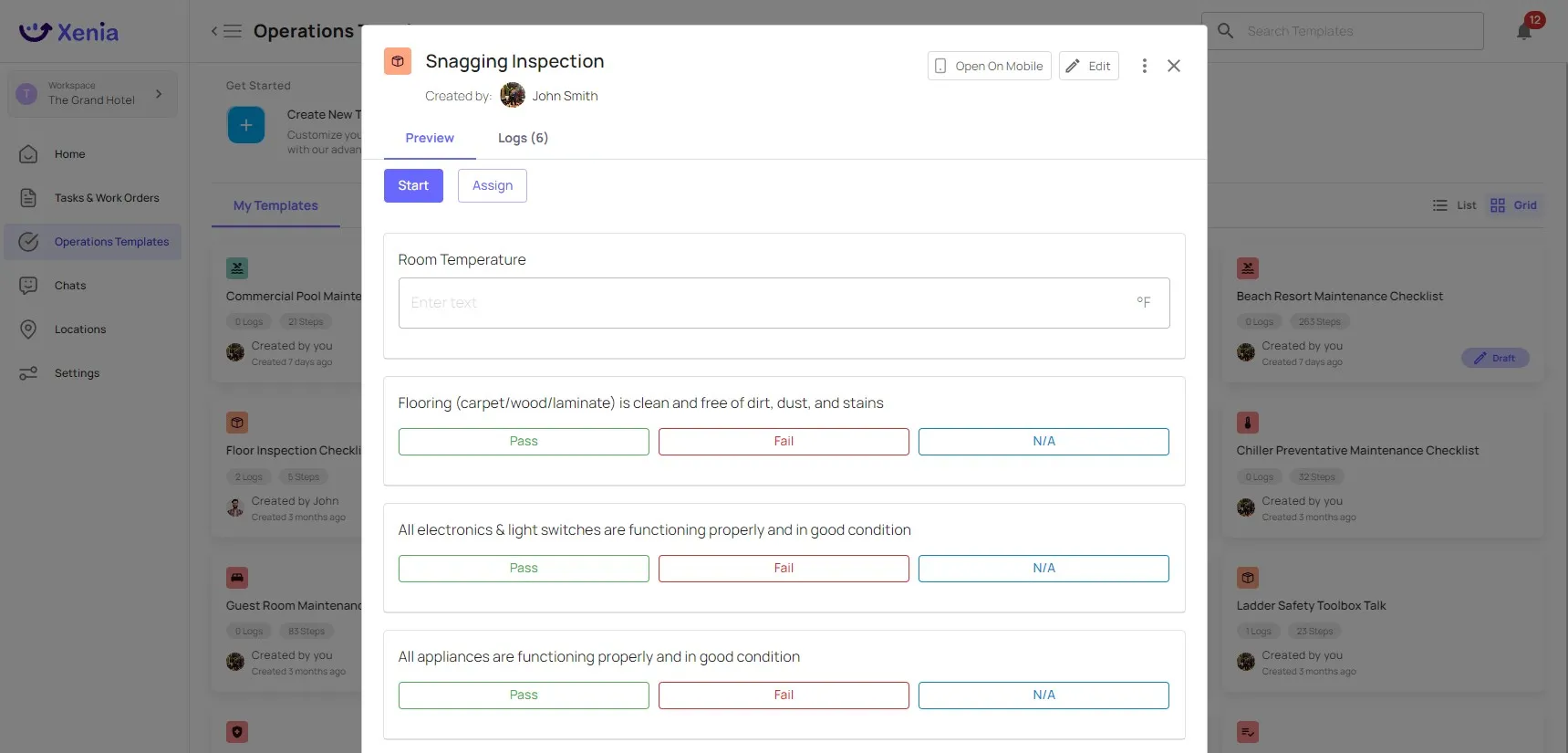
CMMS solutions, like Xenia, have a massive library of checklist templates that apply to different use cases ranging from inspections and preventive maintenance to emergency work order standard procedures. All of these tools can be modified and deployed in the field in seconds, acting as an in house operations consultant without the price tag.
4. Ability to Attach Images
Digital work order systems allow frontline workers to attach photographic evidence of work at every process step to ensure that management has a clear understanding of the scope and detail of the job. This is critical for quality management and accountability on the front line, especially when managers cannot review the work in person.
Furthermore, using a digital system will store these images in the cloud for future review and compliance audits. With a digital system, your documentation of asset work is clear, safe and easily accessible so that you can sleep easy knowing that any audit would be a breeze.
5. Ability to Maintain Work Logs
Computerized maintenance systems are versatile and can be used to record tons of different types of equipment data.
For example, if you are conducting preventative maintenance on a commercial washing machine, you could use the log to record fill and drain times. Over time, you will be able to identify changes in this time as a means of identifying a possible issue with the machinery.
Furthermore, some CMMS solutions, like Xenia, provide detailed report logs for every completed checklist. These logs show every work order step, with time-stamped digital audit trails so that any manager or supervisor can follow the entire activity from top to bottom. This feature equips managers to combat pencil whipping and lazy work effort.
6. Real-Time Collaboration
Finally, the time has come to put down the two-way radio.
On a digital system, work order assignees can easily collaborate with teammates or managers with the help of built in chats. Many CMMS solutions have a chat module built into the app, but some even allow you to loop in others into the work order itself for a more direct approach. This way, the person who is looped in, has all the details to easily and quickly understand the problem.
7. Enhance Communication
Improved Communication for Work Order Request Systems also increases the quality of communication by providing a central entry point for work requests that allows multiple users to post, update, and track the work request in real-time.
8. Improved Transparency
Work order request systems exemplify transparency throughout the entire lifecycle of a work order which allows stakeholders to effortlessly track tasks, and view real-time updates, and historical data.
The transparency enables the stakeholder to better hold the parties involved accountable, along with monitoring KPIs.
9. Efficient Resource Allocation
Want to make sure you have the right human resources at the right place at the right time?
The right system will let you know that the right people to perform certain tasks are available to do so, reducing downtime and increasing productivity accordingly. Stakeholders can easily track the progress of tasks, view real-time updates, and access historical data. This transparency fosters accountability and allows for better monitoring of key performance indicators.
4 Best Practices For Maintaining Work Order Requests
Now that you have a good understanding of what work order requests are and the benefits of digitizing them, we need to cover best practices for deploying them in the field. The following are our four favorite pieces of advice that we see managers use every day.
1. Align Goals & Expectations With Roles and Responsibilities of Staff
Before any work orders and work order requests are set up, it is helpful to clearly communicate that the data collection itself is just as important as the work being performed in the field.
Without consistent and complete data, the value of a CMMS is greatly limited. As a manager, communicate that you expect accurate and complete data to be collected and define your maintenance performance indicators to reflect this mission.
This ensures that your team understands their role and responsibilities in the effort to provide continuous facility improvement. It also helps management to identify high and low performers across both domains.
2. Understand In-House Abilities and What Needs to be Outsourced
Given the vast nature of the work order request, your staff may not always be equipped with the right tools or training to do the job. I
t is best to identify this early and understand what needs to be outsourced to a 3rd party for completion. With maintenance, it is never a good idea to wing it without proper training, as it can put the employee and asset in serious risk of harm.
3. Conduct After-Action Reviews For Performance Evaluation
An after-action review is when a manager analyzes a process from start to finish to determine areas to replicate or improve upon in the future.
For work orders, this means looking at how the issue was identified, the process that was taken to create the work order request, the process of completing the work order, the data collected from the action and the end result of the process. By breaking the process down into these steps, managers can identify the bottlenecks to correct, as well as measure the impact of previously improved processes.
4. Measure Time to Resolution and Cost of Repairs
Time to resolution is measured by recording the time that the issue was identified or the time the work order was created (depends on the software capabilities) and the time the work order was completed.
The span of time between these measurements is the time to resolution. This data can be used to evaluate averages across employees and processes to create a baseline for improvement.
In addition, managers should track the cost of repairs for each work order. This data is essential for accurate cost projections as well as determining whether a specific item should be repaired or replaced. Without this data, managers can waste money repairing faulty equipment that will continue to have issues in the near future.
Wrapping It Up
A study of healthcare institutions that used real-time monitoring found a 40% drop in patient death rates and a 30% gain in operational efficiency. An efficient work order system is necessary for uninterrupted operations, optimal resource deployment, and increased responsibility in companies.
This article compiled what is a work order and how to submit one, which is required for task registration, review, and delegation. On that basis, electronic forms, regular samples, and unified integration are strategies that should be used to get the desired results throughout work order management processes.
For increased productivity and responsiveness, it is crucial to employ forward-thinking technologies that can dramatically improve work order management.
One such innovation is Xenia, a work order management system that streamlines the entire process in ways unimaginable just a few short years ago.
With Xenia, you get user-friendly screens, customizable work request templates, and robust automation tools that keep the entire organization effortlessly focused on completing their assignments.
.webp)
%201%20(1).webp)