Construction projects are no small feat—they demand precision, planning, and an unwavering commitment to quality. Yet, with 4.5 medically consulted injuries per 100 workers and risks of subpar construction inflating costs by over 50%, the stakes couldn’t be higher.
To build structures that are safe, durable, and meet industry standards, quality assurance (QA) is non-negotiable.
QA in construction is more than a box to tick; it’s the foundation for success. From meticulous inspections and testing to rigorous quality control measures, every step ensures the safety of workers, compliance with standards, and long-term reliability of the build. Neglecting these processes can lead to costly repairs, delays, and a tarnished reputation—problems no builder can afford.
This article is your blueprint for understanding and implementing quality assurance in construction. We’ll walk you through essential QA practices, the benefits they bring, and how they safeguard your projects. Whether you’re managing infrastructure, residential, or commercial builds, these best practices will help you deliver excellence at every stage.
Curious about how QA transforms projects? Dive in to learn how thorough planning, open communication, and routine assessments can elevate your construction game and leave a lasting impression of quality and reliability.
Priced on per user or per location basis
Available on iOS, Android and Web
What is Quality Assurance in Construction Projects?
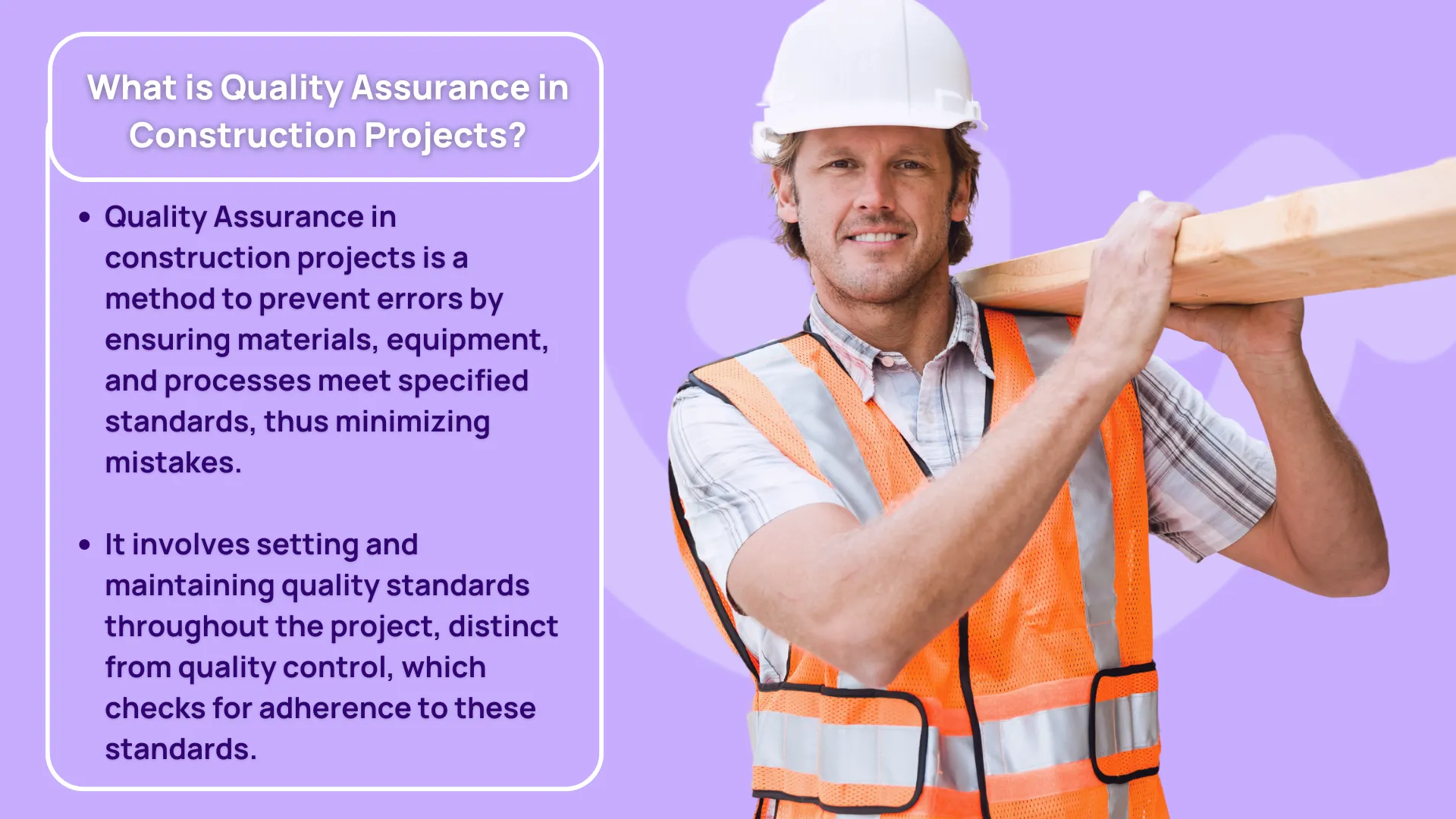
Quality Assurance is a method to prevent any mistakes/errors that may occur in a project, by producing/testing a certain level of products. This ensures that the company minimizes mistakes/errors in the projects.
The process mainly focuses on:
- Materials used: Are they of the proper size, shape, and material?
- Equipment: Will it function in the environment and is it safe?
- Quality measurement standards: What constitutes 'good'?
- Project management: Includes timetables, fair bidding procedures, agreed-upon budgets, and so forth.
- Certificates and skills: Do your employees possess the necessary skills for the job?
By building quality into decision-making throughout your projects, you can make sure you’re ordering the right materials, are using the right approaches, the right equipment, or that everyone on site knows what high standards to meet.
On that note, you need to know that quality assurance is different from quality control.
Whilst the two go hand in hand where quality assurance is about setting the standards regarding the work you do, which in turn sets the expectations of the client, quality control is the process of checking to make sure the structures or elements on site conform to the standards and expectations set by the client.
Understanding Quality Assurance In Construction
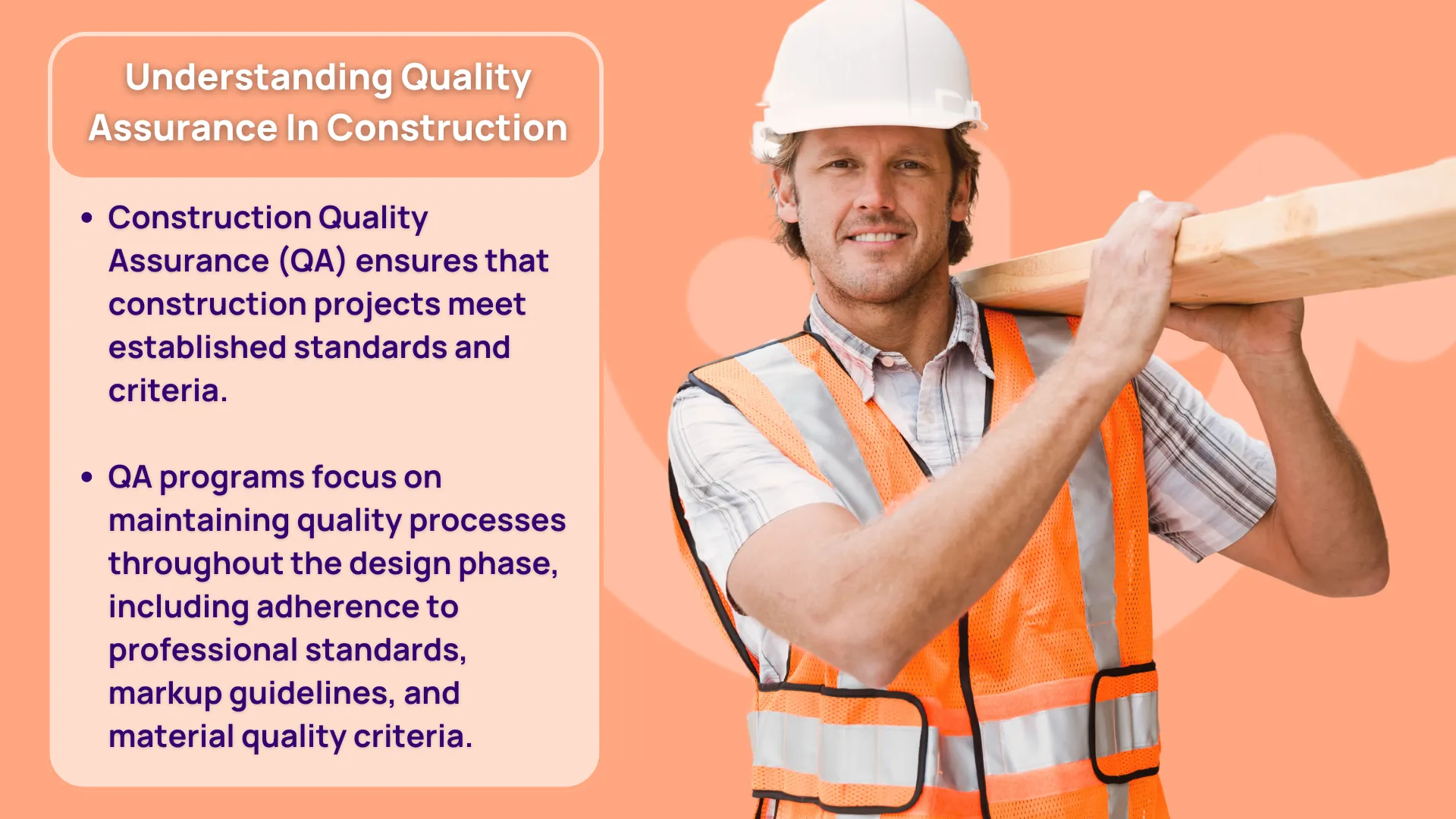
To grasp the concept of Construction Quality Assurance, one must be familiar with the steps used to ensure that a service or product being created in the construction sector satisfies all of the standards.
When it comes to building projects, quality standards are like a North Star; they point the way to a successful completion.
However, without navigational skills, a star is useless. Therein lies the use of assurance approaches. They are like a reliable compass that keeps you on the straight and narrow.
Quality Assurance is like the security guard at your favorite private club. You can be certain that only the most qualified individuals will be able to dance their hearts out on your building site because of this. It prevents careless labor, low-quality materials, and inefficient processes from spoiling your celebration.
How then can you win over this security guard? Through familiarity with and use of quality assurance procedures and standards. Keep in mind that these aren't just esoteric words you can use to wow your trivia night buddies. To make sure your building projects are up to par, they are essential components.
The goal of a quality assurance program is to guarantee that the construction project's quality processes adhere to the company's set criteria for service, performance, and production throughout the design phase. Here are the main specifications:
- Standards for the professions of engineering, architecture, and design
- Guidelines for the use of markup in the stages before, during, and after the approval of plans and drawings
- Additionally, you can be certain that the materials you have chosen meet the quality criteria set by your organization.
Importance of Quality Assurance in Construction
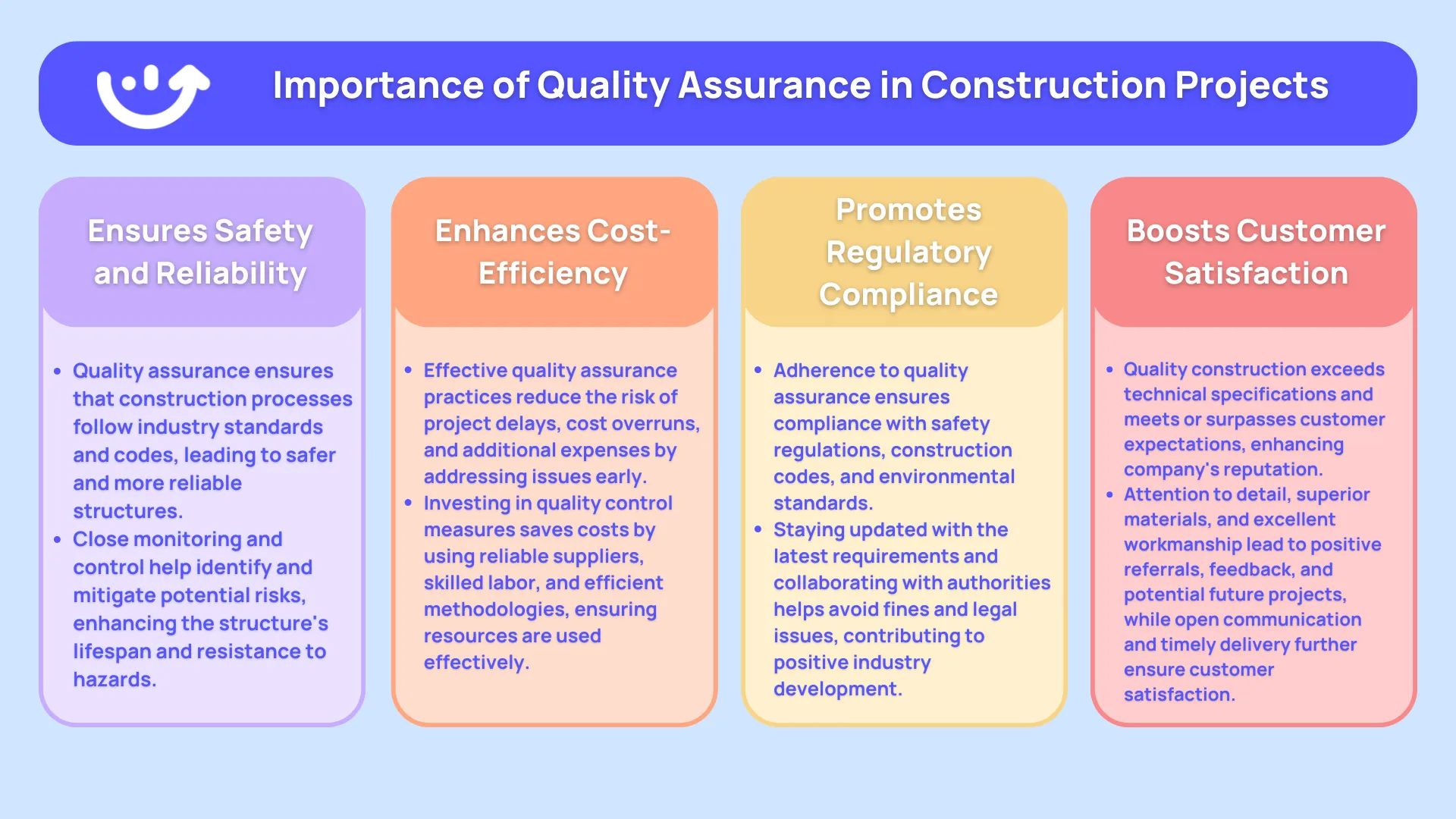
Scalability
First and foremost, the safety and reliability of the built structures are of prime importance Quality assurance is the key to achieving this. Construction professionals have to follow the industry, standards, and codes strictly to build a strong structure.
This can only be achieved if the process of the construction is monitored closely and the system is put in place to make sure everything is done correctly. This monitoring system is in place throughout the construction project by inspection, then testing, and after that monitoring and system handed over.
The close monitoring and control of the construction process enables the potential risks to be identified and mitigated. This proactive approach not only ensures occupant and user safety but also enhances the life of the structure by making it more resistant to hazards.
Cost-Efficiency
97% of contractors reported a moderate to high effect on their operations due to material cost variations. Successful Quality Assurance practices are not only important in meeting safety standards but also as smart financial decisions. When issues are addressed upfront and strict control measures are in place the risk of project delays, cost overruns, and additional expenses is greatly reduced.
Early investment in quality control measures saves substantial costs over the life of the project construction by using reliable suppliers, employing skilled labor, and efficient construction methodology. Paying attention to detail and adhering to the standards for quality In construction, will ensure that the right resources are used when they are required and they are not wasted and that will result in the project not only being efficient but economically profitable.
Regulatory compliance
In 2020, about 48.6% of all construction inspections conducted by OSHA revealed safety violations. In an industry where regulations and standards are a central concern, guarantees of quality are essential. Conformance with the prevailing statutory regulations must also ensure the highest degree of safety, construction codes, and environmentally friendly.
Compliance with the rules is done by acquainting oneself with the latest and newest requirements each time on site and through collaboration with the relevant authorities during the construction process thereby signifying a high level of commitment.
Consequently, by adhering strictly to legal and regulatory compliance, a contractor can avoid fines, and cases being taken to court, and trend positively in the country’s overall development of its built environment.
Customer Satisfaction
According to a survey, 83% of clients would go elsewhere if they have a negative experience.
Quality construction goes beyond meeting technical specifications; it is about surpassing customer demands. Providing a quality project not only satisfies the owner, it helps solidify a company’s reputation. Your consistent pipe systems that lack leaks may warrant praise from the owner of a commercial building. This, in turn, can manifest in positive referrals, positive feedback, and potential work together on future projects. Both owners and end users alike will get a heightened level of satisfaction when close attention is given to aesthetic details, superior materials, or excellent workmanship. Finally, open communication and timely project delivery contribute to our core principle of customer satisfaction.
Risk Mitigation
A comprehensive quality assurance program will help identify and handle any potential risks early in the construction process. You surely agree that this type of risk management is critical since many unexpected items that occur during or after construction typically have both financial and timing constraints required to resolve.
Golden Rules For Maintaining Quality in Construction
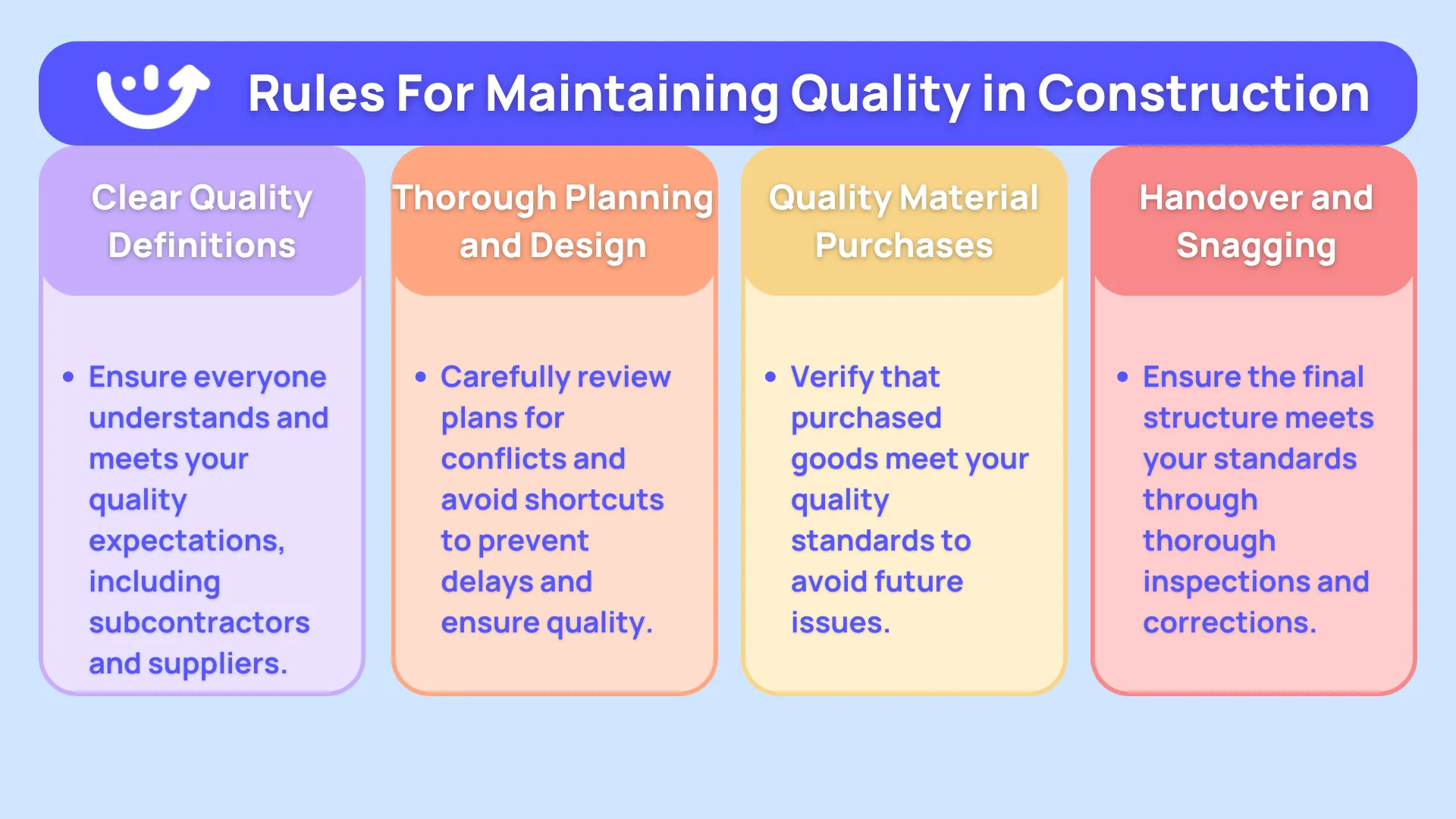
Everyone is accountable for the long and hard work that goes into achieving excellence in building. Making sure choices and work are up to par with quality assurance standards is what it's all about.
The most recognized certification for enhancing quality is the International Organization for Standardization's ISO 9000 standard. ISO 9000 places emphasis on thorough documentation, setting quality objectives, and implementing iterative cycles of planning, execution, and evaluation.
Here are five golden rules for quality assurance on your projects:
1. Clear Definitions of 'Quality’: Make sure that everyone involved in a project has a firm grasp on your definition of "quality" and your expectations for it. Take notes and make sure everyone involved (suppliers, subcontractors, and project managers) understands the specifics.
For instance, you may opt for a level of soundproofing that exceeds the 45 dB threshold required by law for newly constructed buildings. As a result, subcontractors must keep this in mind when they make selections about insulation.
2. Planning, Design, and Development of Plans: Assessing plans thoroughly, checking for conflicts, and avoiding shortcuts are all responsibilities of designers and project managers.
Delays during the construction itself are less likely to occur if problems can be identified and fixed immediately. Building information modeling (BIM) software now can detect conflicts automatically, which improves construction quality.
3. Material Purchasing: Verify that the quality of the goods and equipment you buy is up to your expectations. While it may be tempting to skimp on quality in favor of price, doing so might lead to issues in the road. Making sure your providers can really fulfill your need is another important part of quality assurance while purchasing.
4. Continuous Interaction During Build: Effective communication, problem-solving, and progress verification are essential skills for any project member. If you want your construction project to be of high quality, you need a site manager who will keep a close eye on everything to make sure it's up to par.
5. Construction Inspections TechniquesHandover and Snagging: At the snagging and handover stages, quality assurance is also relevant after the structure itself is up. Making sure the as-built structure is up to your requirements is what this is all about.
Construction Inspections Techniques
Moving on with our topic of construction quality assurance, let’s go through numerous construction inspection techniques that can be used to ensure that structures are built according to specified quality plans and methods. Here are the most commonly used methods.
Visual Inspections
- Visual inspections are frequent in the construction industry, and they are generally used to ensure the quality of work and materials.
- Inspectors carefully inspect visible faults to ensure they meet design requirements and standards.
- These inspections occur throughout the project lifecycle, from pre-construction to completion, allowing for early detection and issue management.
Non-destructive Testing (NDT)
- NDT techniques is a non-invasive method for measuring material integrity without causing harm.
- Ultrasonic testing, radiographic testing, and magnetic particle testing are used to identify faults in materials.
- NDT is very beneficial in analyzing essential components such as structural steel and concrete foundations, allowing proactive problem-solving.
Quality assurance Audits
- Quality assurance audits offer an in-depth evaluation of compliance with quality standards and laws.
- These audits can be carried out internally by the contractor's quality control team or externally by independent third-party auditors.
- Auditors ensure that every work meets stated standards and criteria by reviewing documents, conducting interviews, and inspecting it.
Benefits of Quality Assurance in Construction
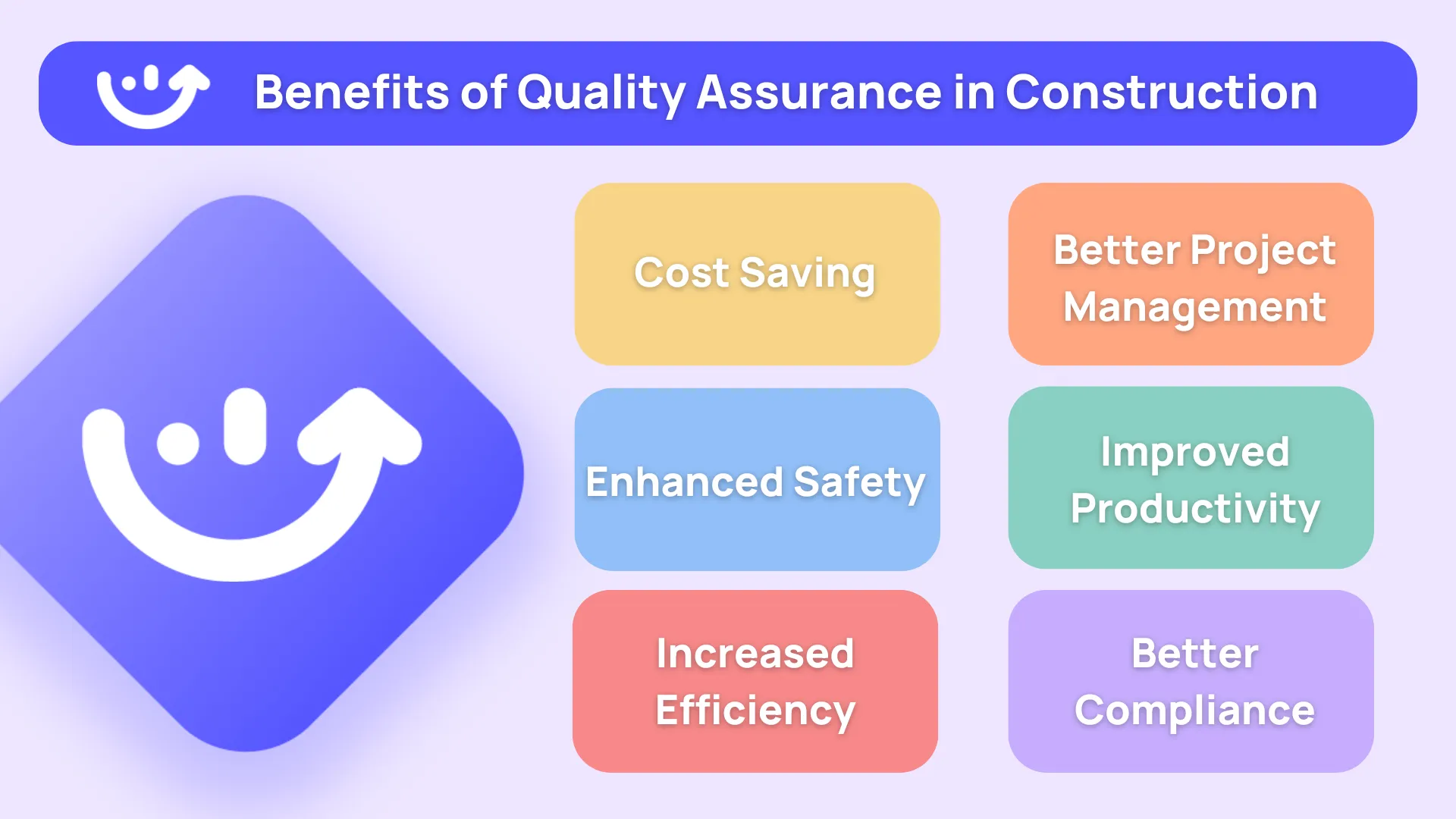
The advantages of quality assurance (QA) for building projects surpass those of more conventional quality control methods.
Successful QA methods, together with new breakthroughs like Xenia, may help identify possible faults early on, reducing or eliminating the need for QC post-completion inspection.
Here are a few reasons why QA is crucial for keeping projects on track: better communication between team members, better risk management (thanks to earlier defect identification), and more efficient use of resources (because preventive actions are taken instead of reactive ones).
Cost Saving
Construction spending in the United States topped $2.1 billion in 2023. Construction projects rely heavily on quality assurance (QA) as it is an effective cost-cutting measure.
Quality assurance (QA) is a useful tool for construction project managers and other interested parties to make sure the work being done follows the plans exactly.
Among these tasks might be the examination of building materials or components, the confirmation of routine maintenance, and other similar tasks.
Construction teams can save a lot of time and money by being proactive with quality assurance methods; this way, expensive repairs or catastrophes can be avoided down the road. To prevent the recurrence of such problems, QA also offers helpful information about the proper planning of building projects.
Better Project Management
When it comes to managing construction projects, quality assurance is king. A construction project manager can guarantee the project's accuracy and safety by making sure it follows all the rules and regulations. The goal of quality assurance in the construction industry is to get people to anticipate and prepare for possible issues before they escalate into costly crises.
In addition to facilitating better planning, quality assurance methods clarify construction schedules and provide teams with comprehensive checklists covering every facet of the project.
Quality assurance methods help construction project managers streamline the process, which in turn reduces stress for everyone involved and increases the likelihood of successful results.
Enhanced Safety
Construction sites are more secure when quality assurance procedures are used.
When carried out correctly, it evaluates current and prospective safety measures critically, setting a high bar for the design and construction of safe buildings and other infrastructure.
To lessen the likelihood of dangerous situations developing before, during, or after construction, quality assurance is an important control mechanism. Starting with the design phase and continuing through to completion, it assesses safety measures at each stage.
Quality Assurance helps in the completion of safe construction projects by using safety-related checkpoints and guaranteeing that safety measures adhere to recognized standards throughout the project.
The best way to ensure that a construction project complies with all applicable safety and environmental laws is to use quality assurance processes. In addition to promoting sustainability via effective use of resources and less waste, this also protects against unforeseen costs and guarantees compliance with all relevant legislation.
Improved Productivity
Construction projects rely heavily on quality assurance. It guarantees that all building activities are carried out following safety regulations, industry standards, and client specifications.
Timely, efficient, and high-quality completion of all construction projects is the objective. Reduced construction delays and expensive errors that lead to budget overruns and subpar supplies or labor are two ways in which quality assurance can improve productivity.
Quality assurance expedites and secures the completion of construction projects by allowing teams to proactively detect and solve any faults before they reach completion. Building to a high standard not only benefits the client but also the building crew.
Increased Efficiency
Quality assurance provides accurate assurance that assets are or will be constructed to expectations through routine monitoring and control testing of material and workmanship quality.
The proper use of QA procedures can help avoid unexpected increases in efficiency while reducing costs. Therefore, quality assurance not only ensures that constructed assets are efficient but also accelerates the completion of building projects.
How Digital Technology Enhances Quality Assurance
In the past, quality assurance methods required physically comparing each part of a building to its blueprints. This was expensive and prone to errors by humans, which meant that measurements may be inaccurate or not taken at all.
It is now much simpler to digitally record construction data and then utilize that data to build automated solutions for quality assurance in the construction industry.
In the construction industry, for instance, digital communication with workers may greatly cut down on paperwork while also improving data analysis accuracy.
Construction defect monitoring systems and other digital technologies provide real-time information on construction performance throughout all stages of a project. By using this data, quality engineers may detect construction concerns early on and resolve them before they escalate.
The objective is to prevent construction projects from going over budget or behind time while yet achieving the required quality.
That is precisely the benefits of quality assurance digital technology and what it can do by giving rise to more intelligent, efficient, and cost-effective solutions for construction quality assurance.
- Quality Control (QC) Plan – Quality control plans include inspection and testing schedules, among other measures, to guarantee quality throughout construction.
- Inspection and Testing of Materials and Equipment – Verifying that all building supplies and tools are up to code is an important part of this procedure.
- Inspection Checklists – Using a checklist guarantees that no detail of the building process is overlooked.
- Non-Conformance Reports (NCRs) – When construction deviates from the plans or specifications, NCRs are used to record the occurrence.
- Corrective and Preventive Action (CAPA) – The goal of the Corrective and Preventive Action (CAPA) procedure is to find and fix quality issues so that they don't arise again.
- Audits – To find out how well the QA and QC procedures are working and where they might be improved, auditors conduct audits.
- Statistical Process Control (SPC) – Statistical process control (SPC) is a tool for controlling and monitoring construction processes via the use of statistical methods to identify process variances.
- Building Information Modeling (BIM) – Stakeholders in the design and construction phase may use this technology to see the building's digital twin and verify compliance and potential conflicts.
How Do Quality Management Tools help in the Construction Industry?
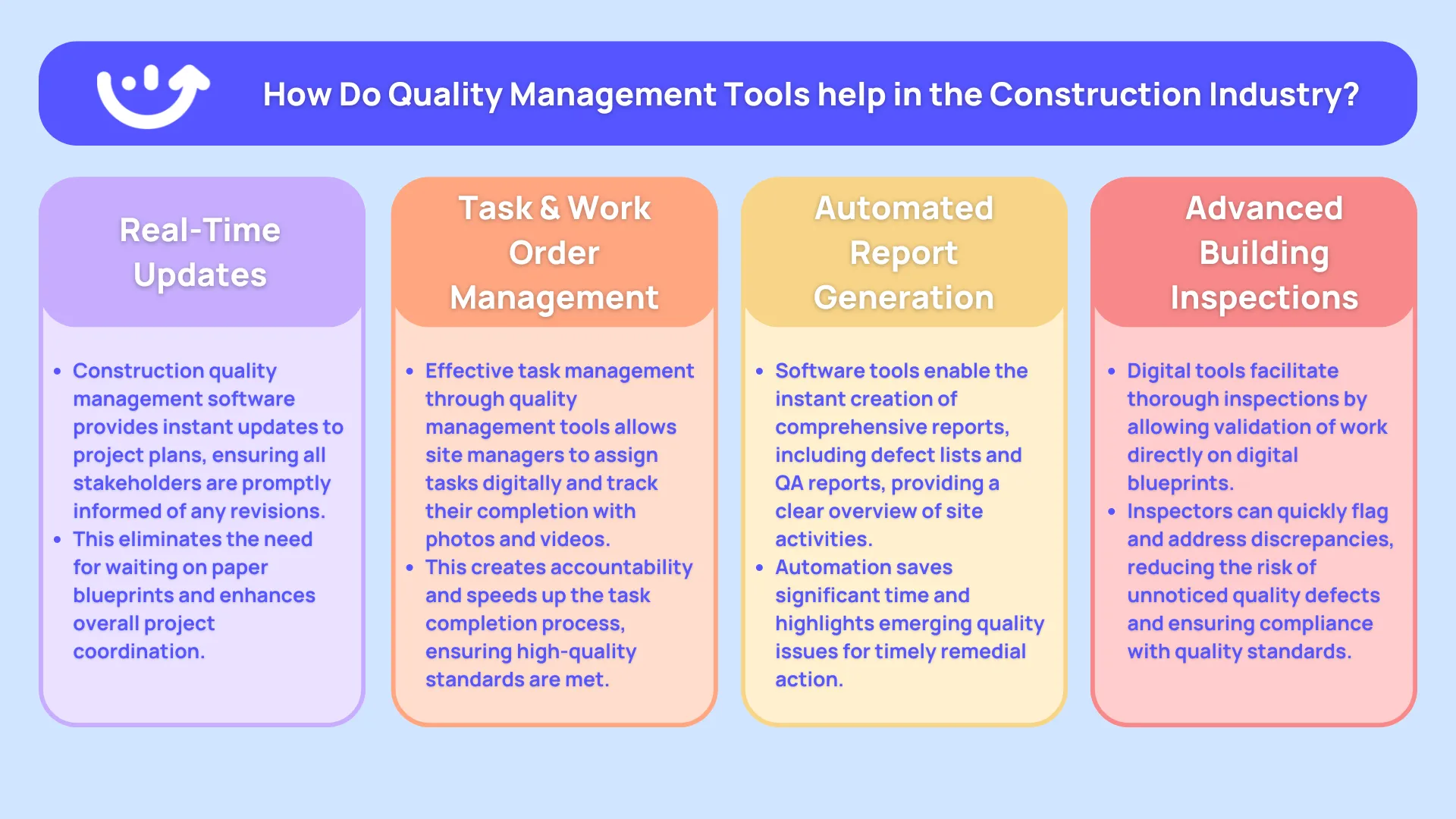
Quality management systems (QMS) in construction play a major role in improving the quality of a project and hence the expected result.
On a related note, a robust QMS is a well-defined system that includes policies, procedures, and guidelines for planning/removing/assessing the quality of the relevant goods/services.
QMS also has a major role in the cost of the project, the efficiency of the project, the overall improvement of the services, and the satisfaction of the clients.
Real-Time Updates
One of the most impressive features of construction quality management software is the ability for real-time updates to project plans. Any revisions or modifications to the architectural plans, are instantly and automatically sent to all stakeholders involved in the project so you never need to wait for paper blueprints.
Task Management
One of the most fundamental building blocks of quality assurance in the construction industry is the effective management of tasks.
This all-important document can be dropped into a system or software for construction quality management and then the site manager can assign it to the people who need to take it out on site. This could then be accessed on their phone or workstation, complete the task, and get the people on the platforms on site to verify with photos and videos.
This creates accountability, which is essential in any organization and it speeds things up.
Automated Report Generation
The days of manually compiling defect lists, snag sheets and QA reports are over. Using construction quality management software, site managers can generate instant comprehensive reports featuring a crystal clear overview of virtually everything going on at the site. In one click, stakeholders are offered an invaluable sundowner re-preview of the project, with emerging quality issues easily and vividly highlighted.
Automation of this calculates to invaluable saved time, therefore adding to the time efficiency of remedial action.
Advanced Building Inspections:
Thorough building inspections are essential to ensure that construction work meets quality requirements. Construction quality management software makes inspections easier by allowing inspectors to validate completed work directly on digital blueprints.
Inspectors can flag any issues or discrepancies so that they can be addressed right away, reducing the risk of quality defects going unnoticed.
Seamless Communication
Effective communication is the key to every successful construction project, and construction quality management software makes it easy for all stakeholders to communicate seamlessly.
Whatever the case, having the ability to ask a question, give out instructions, or solve a concern, the app enables quick response ensuring that everything stays aligned with the quality objectives.
Xenia -The Ultimate Quality Inspection Platform For Construction Projects
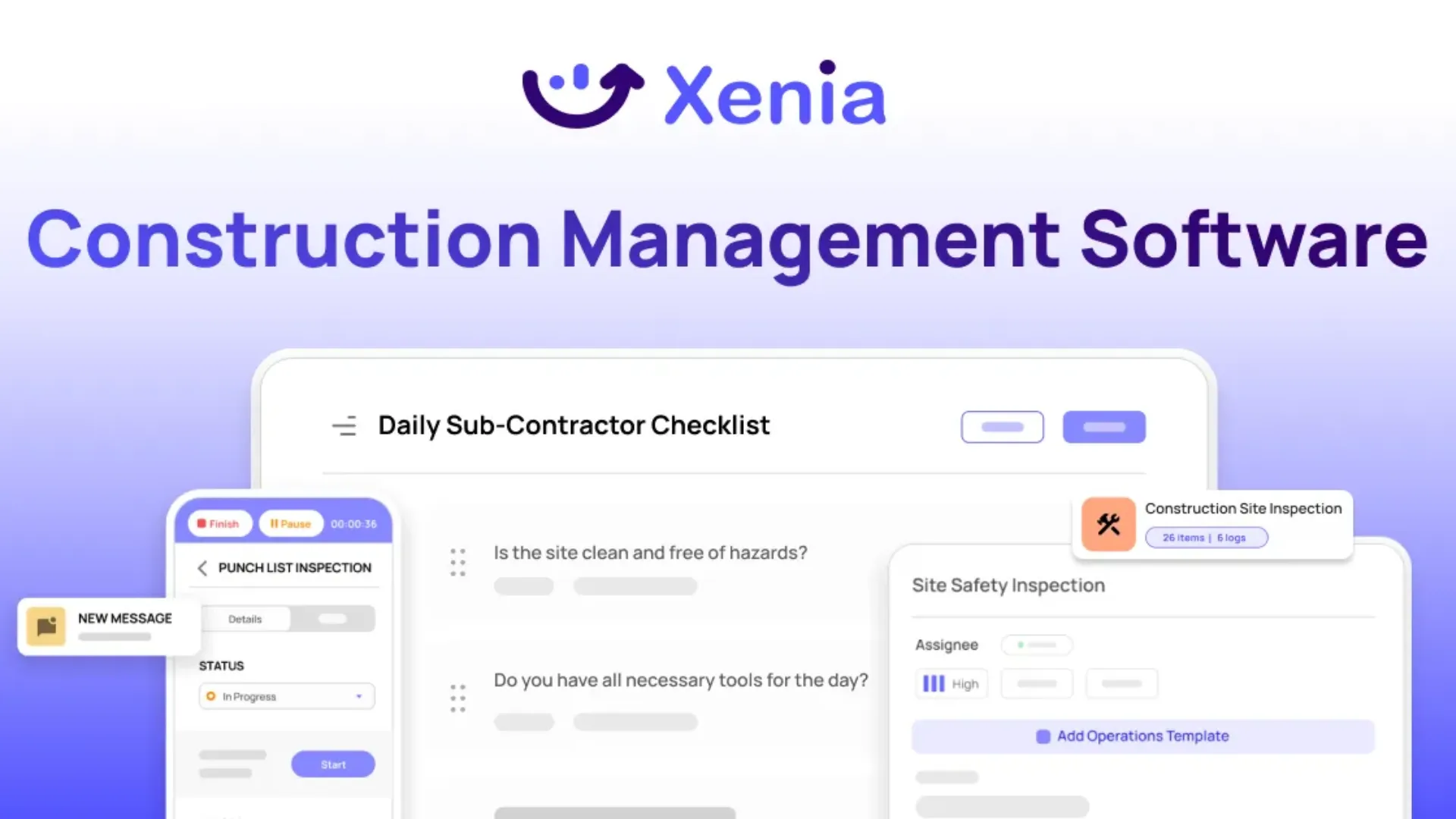
The quality control and assurance platform you use for your construction projects can make all the difference in improving standards across your organization.
Of the many available inspection platforms to choose from, Xenia is a top-notch quality assurance platform with an all-inclusive selection of tools to help streamline your quality inspections and improve the quality of your projects.
Xenia provides a simple and efficient solution to perform quality inspections and monitor quality data.
Thanks to the mobile inspection app that is easy and pleasant to use, quality inspections don’t require any paperwork anymore, and the time spent in managing quality inspection is reduced to its bare minimum. Thus, a quality control manager can underline all the performances of the current construction project from a quality perspective.
Furthermore, Xenia’s powerful workflow automation capacity permits users to create and then implement extensive inspection processes easily, transforming construction managers’ ability to enforce the most stringent quality standards throughout the life cycle of the project. With customizable checklists and automated remedial actions, construction managers will have the tools at their fingertips to build as much dependence on the Xenia portal as they choose.
By collecting real-time quality data and graphing quality trends over time, Xenia port users make effective, proactive decisions and are highly committed to emphasizing any continuous improvement initiatives.
What sets Xenia apart is its intuitive user interface. Everything is designed to make the creation and deployment of quality inspections easier than ever. Using a simple drag-and-drop interface, construction managers can build quality workflows that meet the needs of their projects. That’s why Xenia is loved by so many.
If you already have a process in place, Xenia is flexible enough to match your workflow. We can track whatever you need to test; we adjust and build workflows to match your folder and file structure. We have the most flexible, easy-to-use construction quality system.
Why Use Xenia?
- Operations Template Builder: Use an advanced builder and customizable pre-built templates to speed up manufacturing operations and inspections.
- Smart Inspections: Identify problems, speed up product quality inspections, automate corrective actions, and upload photos to the cloud.
- Work-Order Management: Use images, comments, and templates to improve uniformity and accountability in your task management.
- Scheduled Inspection Tasks: Increase productivity by creating clear task plans and delivering mobile team updates.
- Requests and Approvals: Centralize request management, expedite approvals, and track associated costs and resources.
- Incident Reports: Enhance problem management with mobile reporting, remedial actions, and live progress monitoring.
- Analytics and reporting: Improve decision-making with detailed work analytics, powerful filters, and configurable data exports.
Bottomline
Understanding quality assurance in construction is paramount for successful development projects. By ensuring that quality standards are met, you can avoid costly repairs and site delays, saving both money and time.
To optimize your resources and efforts, consider automating your quality assurance operations. By streamlining processes, you can redirect resources to other areas of your organization while still maintaining high standards of quality.
Furthermore, embracing digital solutions for data collection and analysis can provide valuable insights into your operations. Needless to say, through digitization, you can enhance efficiency, accuracy, and transparency, ultimately leading to improved project outcomes.
.webp)
%201%20(1).webp)