To compete in the fierce global market, most general manufacturers try to achieve ISO quality standards such as ISO 9000 and ISO 13485.
Both standards are focused on quality management and meeting customer and regulatory requirements by continuously improving the manufacturing quality control system.
Many general manufacturers also follow the Total Quality Management (TQM) philosophy, which was created in the 1940s by W. Edwards Deming. This management strategy in a manufacturing quality assurance system is focused on long-term success via customer satisfaction.
TQM and ISO both emphasize improving processes, goods, and services, as well as integrating quality into all parts of everyday operations. But what software is used in manufacturing, or in other words, what's a manufacuring quality inspection app used for?
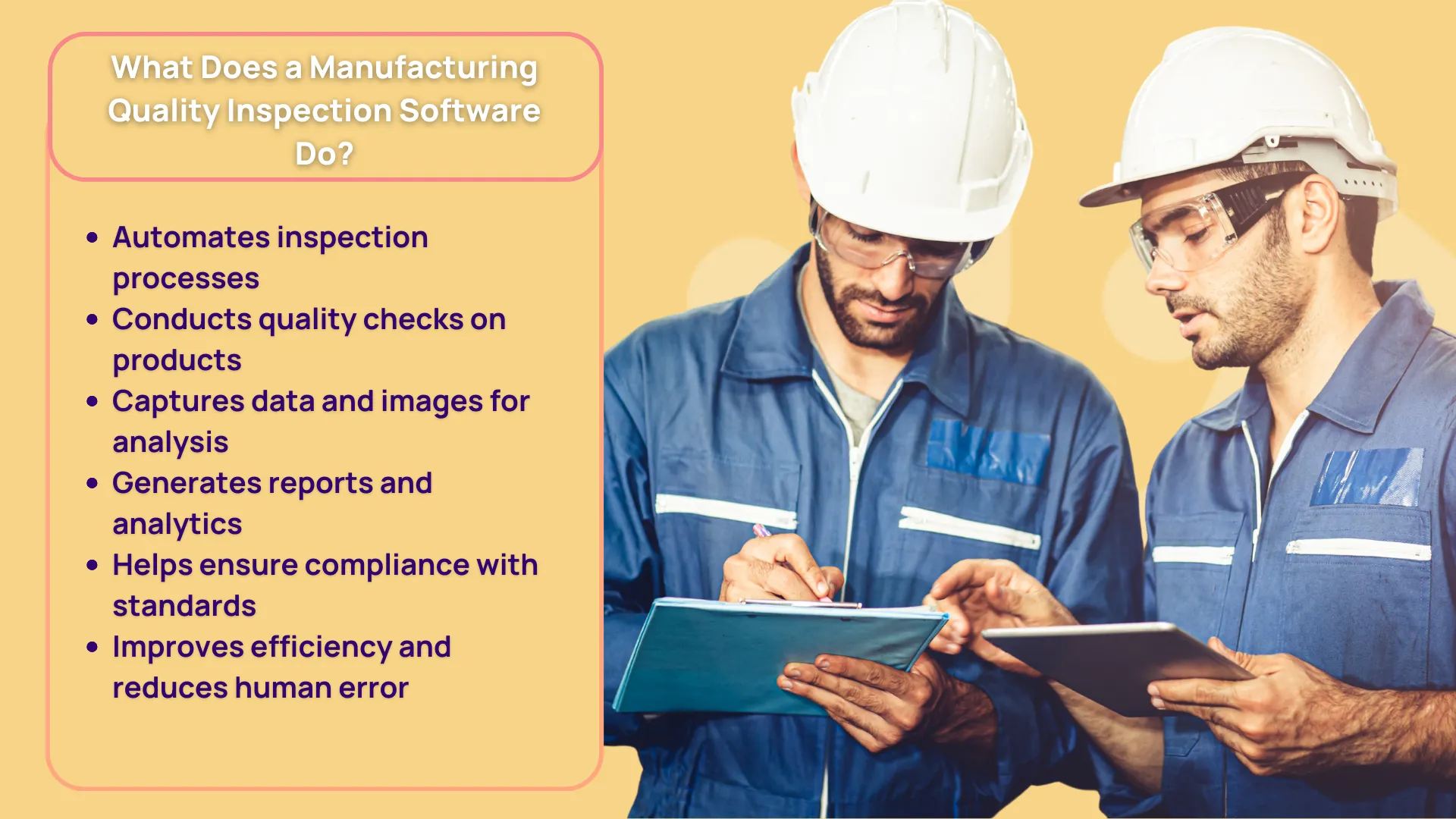
It is important to succeed in investing in the best manufacturing quality inspection software. Luckily, with so many alternatives available, determining which software best meets your requirements shouldn't be a problem.
We've created a list of the top 5 best manufacturing quality control inspection software available in 2024 to help you choose what works for you and your organization.
What is Manufacturing Quality Inspection Software?
Manufacturing quality control software is meant to assist businesses in ensuring that their products satisfy the highest standards of quality.
As a result, the program enables manufacturers to track, monitor, and report product concerns, including defects, nonconformances, and other quality issues. Moreover, a robust manufacturing quality inspection software can be utilized to create quality reports and monitor supplier performance.
Organizations can readily detect and fix quality problems with the correct tools before they become expensive or negatively influence customer satisfaction. It also assists them in maintaining compliance and reducing manufacturing-related safety hazards.
For example, a manufacturer can employ the best manufacturing quality inspection software to check a batch of goods and automatically detect any deviations from projected standards, such as inaccurate measurements, wrong labeling, or product faults. This enables the producer to take remedial action and ensure that all products meet the necessary quality standards.
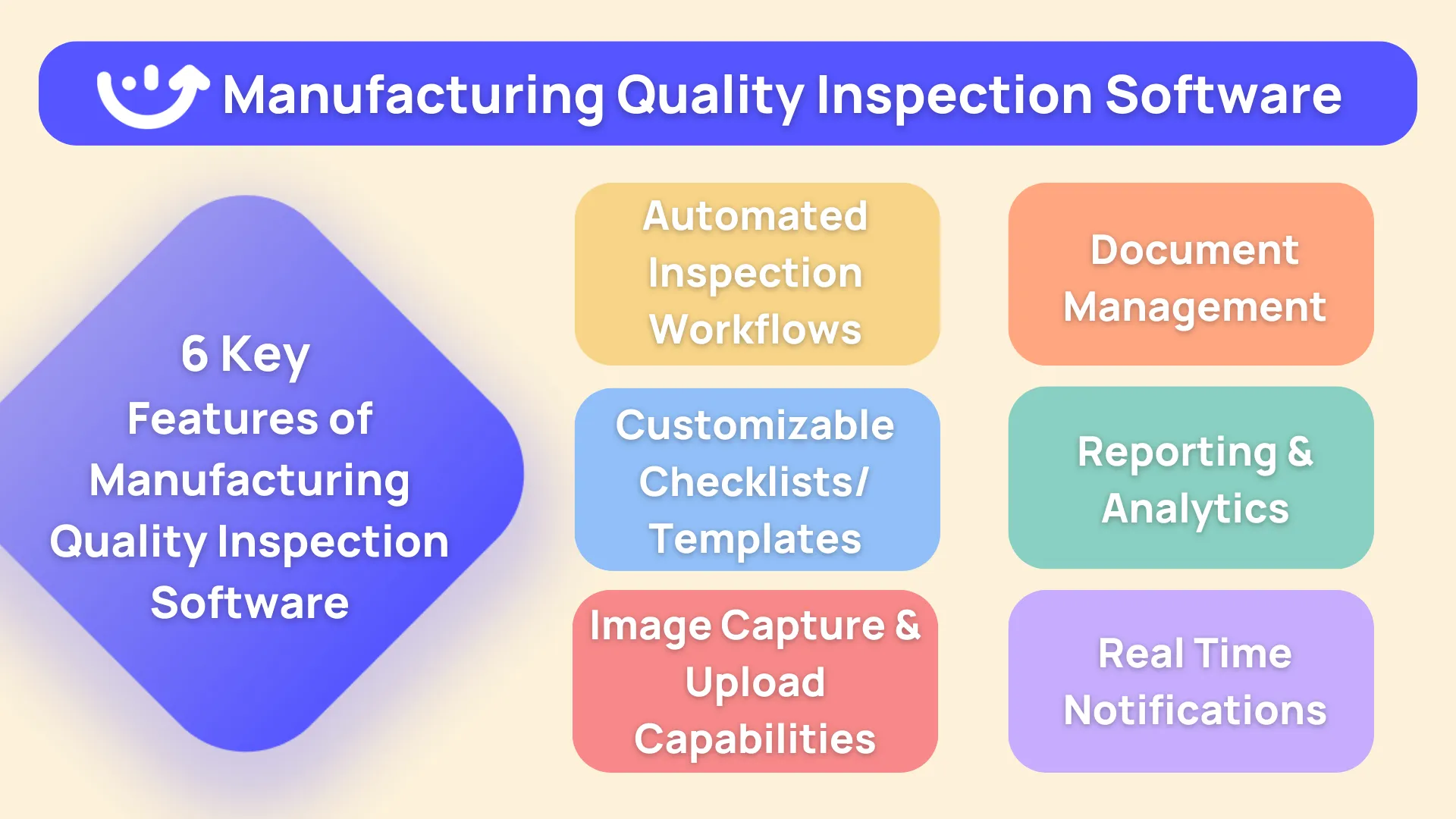
How Can Quality Inspection Software Help Cut Costs and Time?
When it comes to regulating the way your inspections are carried out and reported, who wouldn't want to save money in both domains without sacrificing quality?
- Cutting Out Mistakes
Nothing wastes time and money like incidental mistakes, particularly when it comes to quality inspections.
If a substandard batch of products gets through, it could damage the brand's reputation and even cost them repeat and future business. Using quality inspection software guarantees that the task is done in an organized way, reducing the possibility of errors.
- Clearing Out Paperwork
We've previously highlighted how employing software may save the time spent filling reports following inspections by having it all produced by the software on a mobile or tablet application.
Another benefit is that it eliminates much of the paperwork (physical or electronic files) that clutters up workplaces and PC desktops. The data is all kept in one location, accessible to everyone, preventing file duplication and corruption.
- Providing Statistics for Each Supplier
A one-size-fits-all approach to inspection assessments implies failing to gather enough information about vendors. Not all factories operate in the same way, and not every product includes the same variables.
When it comes to gathering and analyzing statistics, the conventional technique leaves much to be desired. Still, reliable software solutions provide a library of valuable information and analysis, enabling you to make decisions that guide your inspection procedures.
- Real-Time Reporting
Not only does reporting in real-time reduce time for inspectors, but it also allows purchasing managers and suppliers to view everything from the inspection as soon as the device is able to connect with it over wifi or cellular data.
This implies that everything can be put into action right away, and decisions can be made considerably faster.
- Identifying Recurring Issues
Another advantage of including the statistics module as part of the manufacturing quality inspection software is that it allows you to identify problems with a similar pattern that often occurs in factories.
These persistent flaws are clearly not being addressed by suppliers and may not even be noticed by inspectors, but they may be proven and handled with the use of quality inspection softwares.
10 Best Manufacturing Quality Inspection Software Apps In 2024
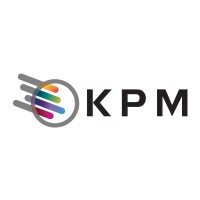
1. Xenia - Overall No. 1 Best manufacturing quality inspection software Program
.webp)
As one of the best online manufacturing quality inspection app, Xenia introduces a multitude of mobile-first quality control solutions through a variety of different features.
These features have reportedly helped to changed the face of quality inspections for manufacturers.
The program combines mobile cloud and database technology. Inspections are conducted on a native mobile app that’s easy to use and functions anywhere offline without the need of data connectivity.
It is a reliable partner in the process for improving the performance of your manufacturing line, whereas Xenia's integrated real-time monitoring technology enables a more effective planning, team scheduling, and workforce management.
Meanwhile, all the data concerning work orders and process advancement is captured automatically via online manufacturing inspection checklists and pre-made inspection templates, which are subsequently fed into analytical reports.
The best part is that these out of the box manufacturing inspection & operation tempaltes can be customized to fit any number of use cases.
Here are some of the key highlights of this program.
Key Features
- Operations Template Builder: Using customizable pre-built templates and a sophisticated builder, you can streamline manufacturing work processes and inspections
- Smart Inspections: Catch manufacturing errors in action, simplify inspections, automate corrective measures, follow-up inquiries, and upload photos to the cloud
- Scheduled Work: Increase productivity by creating clear job schedules and sending mobile team updates
- Task Management: Using images, notes, and templates for task management to replace jotting down notes for enhanced standardized procedures and accountability
- Work Requests and Approvals: Centralise request management, speed up approvals, and keep track of related expenses and resources
- Incident Reports: Use mobile reporting, remedial actions, and live progress monitoring to improve problem management
- Analytics & Reports: Use thorough work analytics, powerful filters, and configurable data exports to improve decision-making
Pricing
- Free Forever: 14-day free trial for up to 5 users
- Starter: $99 / month for 15 users
- Premium: $199 / month for 15 users with unlimited access to all the core features
- Custom: Need something tailored to your organization?
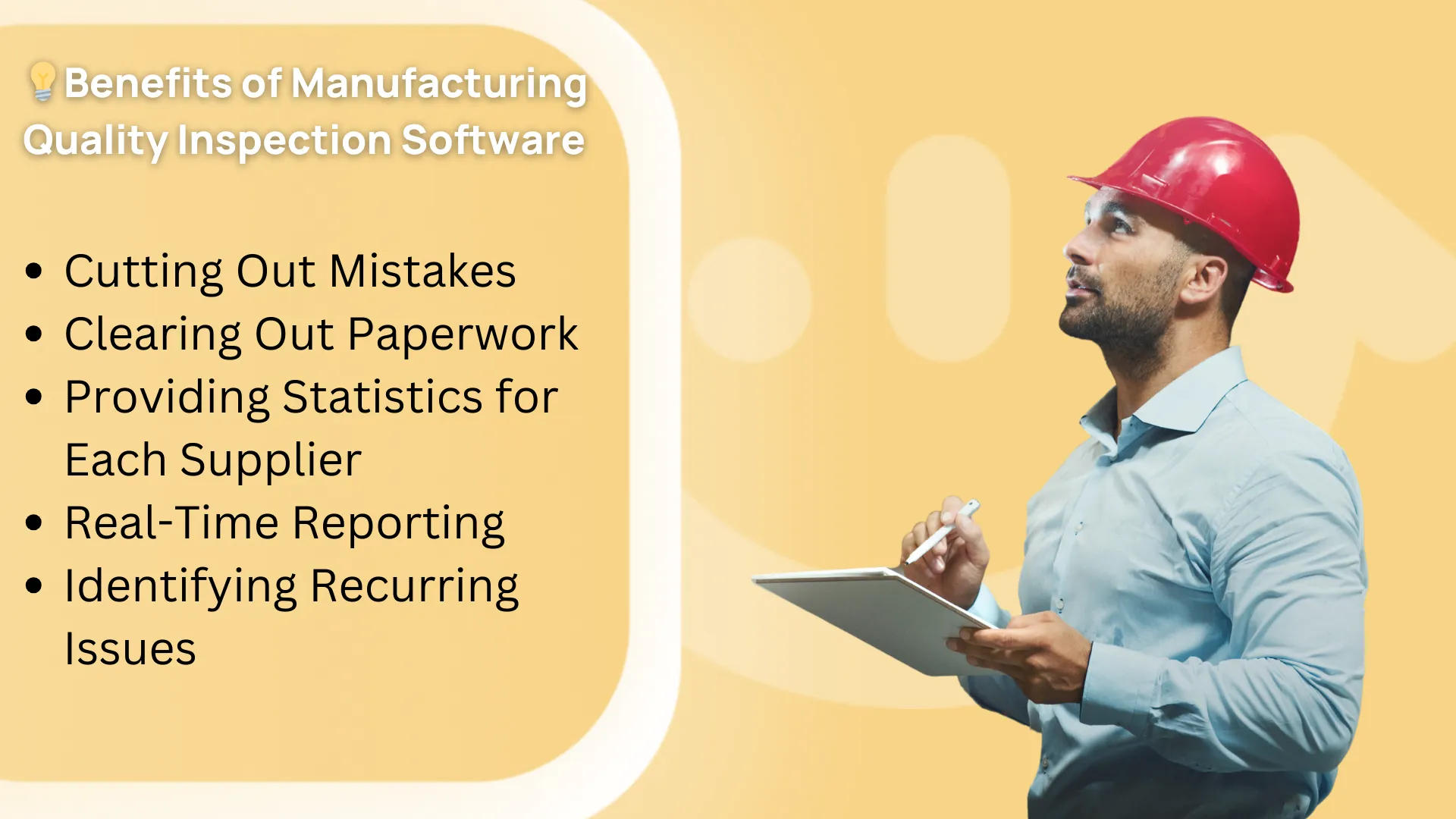
Priced on per user or per location basis
Available on iOS, Android and Web
2. iAuditor-Safety Culture
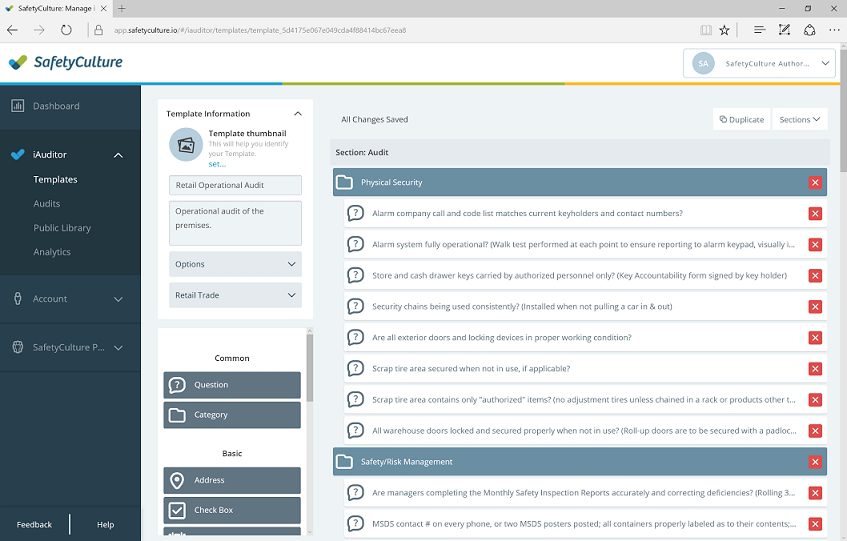
Moving on with our quality management software for manufacturing recommendation, we've got SafetyCulture on he list.
When it comes to manufacturing inspections and safety audits, nobody does it better than SafetyCulture iAuditor. It delivers tools that transform its user's inspections using smart, mobile forms.
Users can now digitize their checklists for use in the field and take them with them wherever they go. Not to mention, any kind of inspection can be performed with the help of its adaptability and efficiency.
The SafetyCulture iAuditor is a mobile app for collecting data in a secure way. Photos can be annotated, GPS locations added, electronic record signatures stored, performance ratings recorded, and much more.
When mobile devices are automatically synced with the desktop system, businesses can see exactly what's happening in the field in real-time and quickly zero in on any problems.
Key Features
- Digital Manufacturing Process Audit Checklist: Determine and resolve issues and inefficiencies in the production process.
- GMP Audit Checklist: A manufacturing company's adherence to manufacturing standards is assessed using a GMP Compliance Checklist.
- Manufacturing Audit Checklists: Maintain quality standards across your operations.
- Manufacturing Standard Operating Procedure (SOP): Verify that manufacturing SOPs are being followed using a simple mobile app to automate standard operating procedures in manufacturing.
- Machine Safety Checklist: Use a digital auditing solution to guarantee the health and safety of your employees as well as the appropriate operation of your equipment.
Pricing
- Free: For individuals or small teams looking to digitize their operations. Starting at $0/ user. Up to 10 users
- Premium: For teams who need deeper insights and collaboration to improve their business. Starting at $24/seat/month when billed annually
- Enterprise: For large businesses that need advanced integrations and dedicated support
3. KPM Analytics
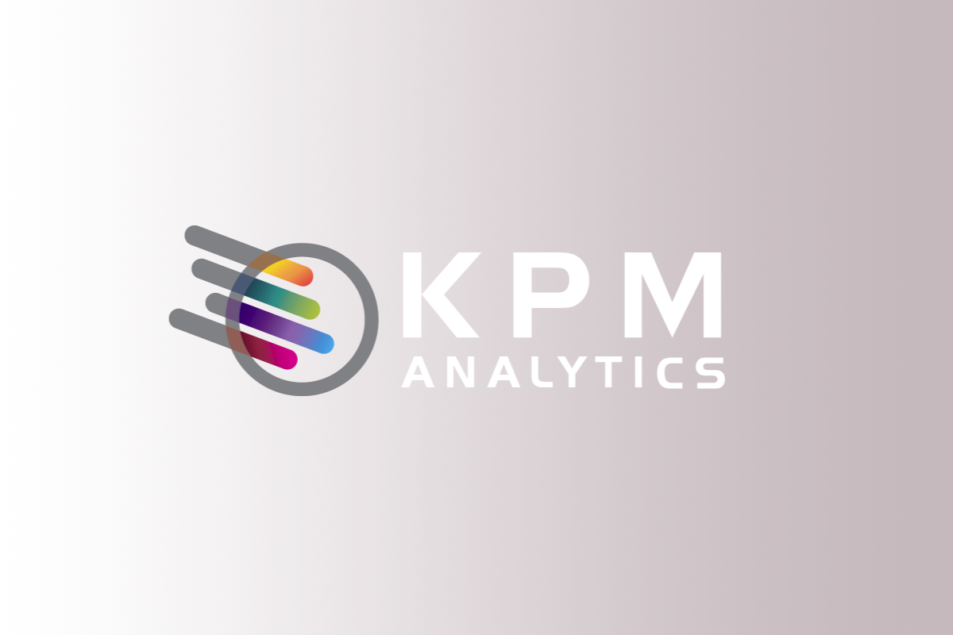
For process control, final product inspection, and other food applications, KPM Analytics offers cutting-edge analytical solutions.
KPM Analytics' solutions help businesses save costs and boost productivity by optimizing processing efficiency and improving product quality.
With the use of a number of high-speed cameras and image software, KPM Analytics' current vision technology solutions can identify and measure products at full-line speeds for form, colour, composition, and numerous other factors before packing.
Vision inspection technology reduces human error in the inspection process, automates quality control operations, and increases packing efficiency.
Key Features
- High-Precision NIR Instruments: Measurements are trustworthy when made using a linear monochromator with high accuracy.
- Guardian-HD Web Profiling: Simple to operate, calibrate, and standardize. Strong, airtight industrial frame and linear actuator tolerate the warm, muggy conditions of typical conversion operations.
- Process RF Analyzer: Provides board product diagnostics using proprietary manufacturing quality inspection software. Using trend time plots and data recording for statistical analysis.
Pricing
- Contact vendor for pricing info
4. UpKeep
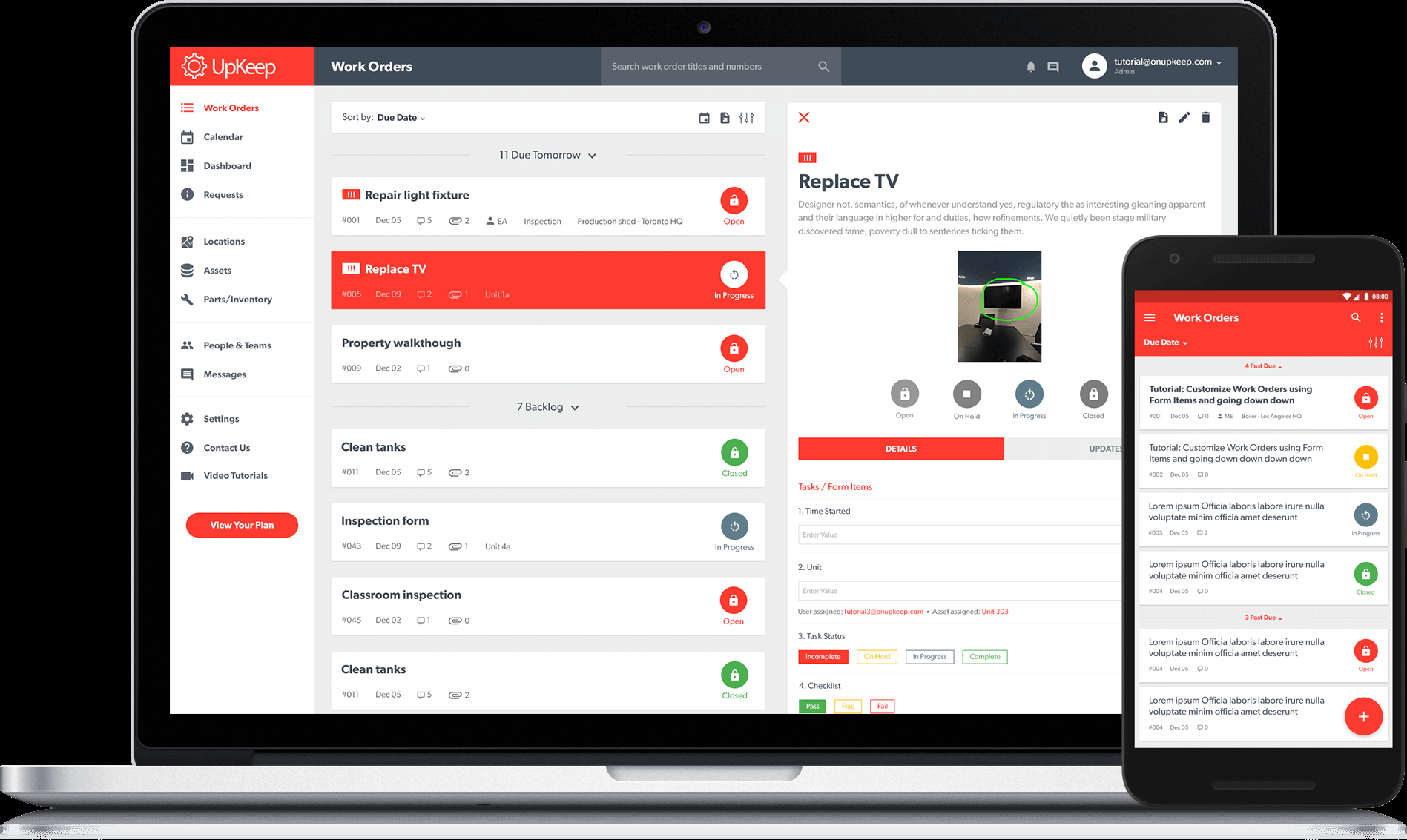
Up next on our list, we've got UpKeep as one of a kind qualty management software for manufacturing.
Owing to a set of different features, the program assists businesses in developing standardized procedures and simple-to-use inspection instruments to ensure that the procedures are being followed.
Whatever your business requirementsd are, UpKeep offers a solution that you can customize to maximize the performance of your team members and enable them to reach their full potential.
The versatility of UpKeep's inspection tools means that the possibilities for your company are limitless.
Furthermore, this manufacturing quality inspection app lowers labor costs while increasing employee productivity, accountability, and efficiency so you can remain on top of your business's affairs.
Key Features
- Streamlined Scheduling: With UpKeep's robust but user-friendly UI, users can easily design effective work plans. You may freely handle work schedules for many places by centrally managing them.
- Efficient Time Tracking: Every employee can clock in from anywhere at any time using a variety of devices, including mobile applications, thanks to the integrated time clock function.
- Simplified Compliance Management: With the Forms and Inspections tool from UpKeep, creating personalized audits and inspections is simple.
Pricing
- Contact vendor to get a Quote-based Plan
5. UniPoint
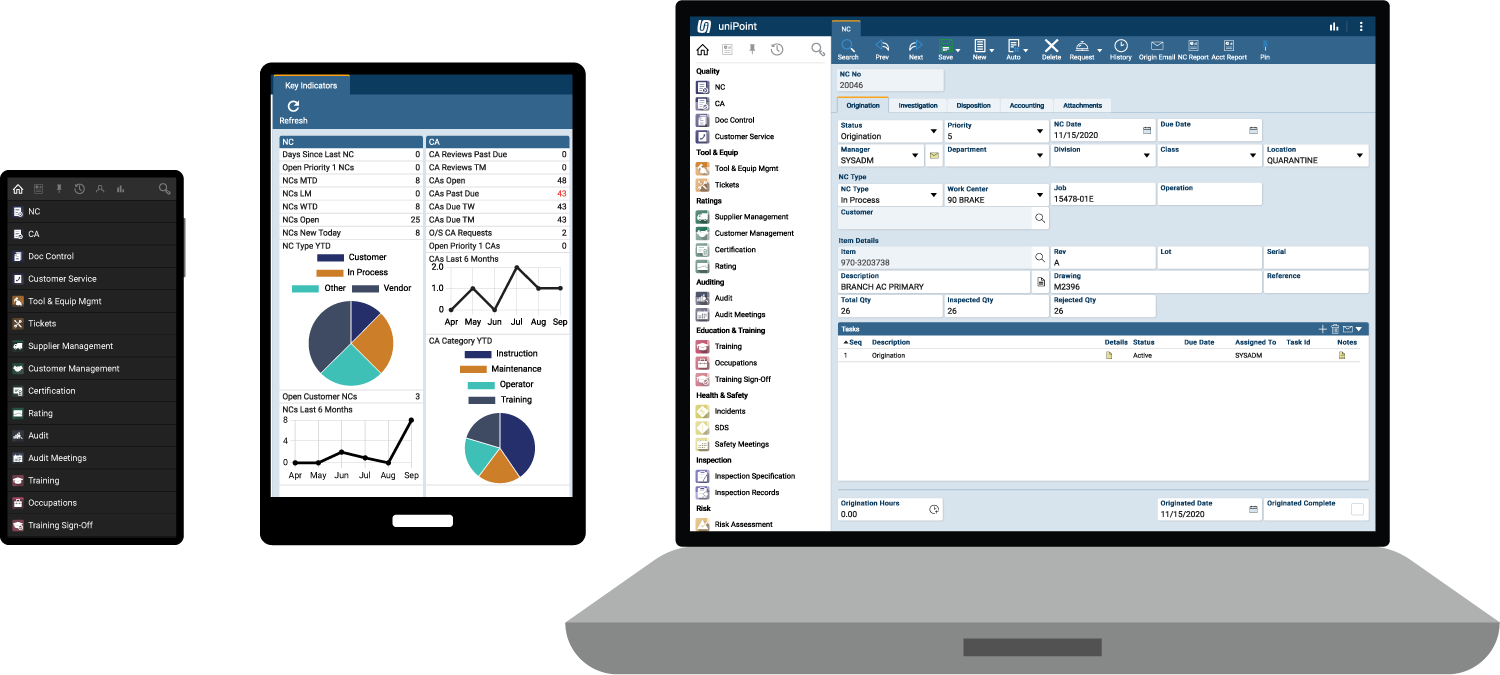
UniPoint is a pioneer in the area of industrial manufacturing quality inspection software (QMS).
It provides ERP-integrated quality management systems (QMS) that are suitable for numerous industries, including chemical, food & beverage, automotive, and medical.
The three elements of UniPoint—core, add-on, and web—comprise of its broad toolkit, which assists businesses in automating their quality control processes.
Features like document control, corrective and preventative action, and non-conformance are all included in the basic modules. You will also get validation, auditing, health and safety, and inspection from the add-on modules.
You can switch to a mobile QMS with mobile inspection and web requests by using the web modules.
Key Features
- ERP-Integrated QMS: An integrated QMS/ERP platform raises the standard by removing duplicate data entry and the possibility of input errors while also offering a single point of contact for all quality and compliance tasks.
- Flexible Deployment: A Mobile-First Design, enabling uniPoint Web to run with full functionality, SSL security, and optimized performance on any smartphone, tablet, or desktop computer.
- Quality Automation: Over 800 built-in quality measures or Key Performance Indicators (KPIs) are available on the executive dashboard, enabling our clients to evaluate the health of their quality system at a glance.
Pricing
- Available upon request
6. Zontec
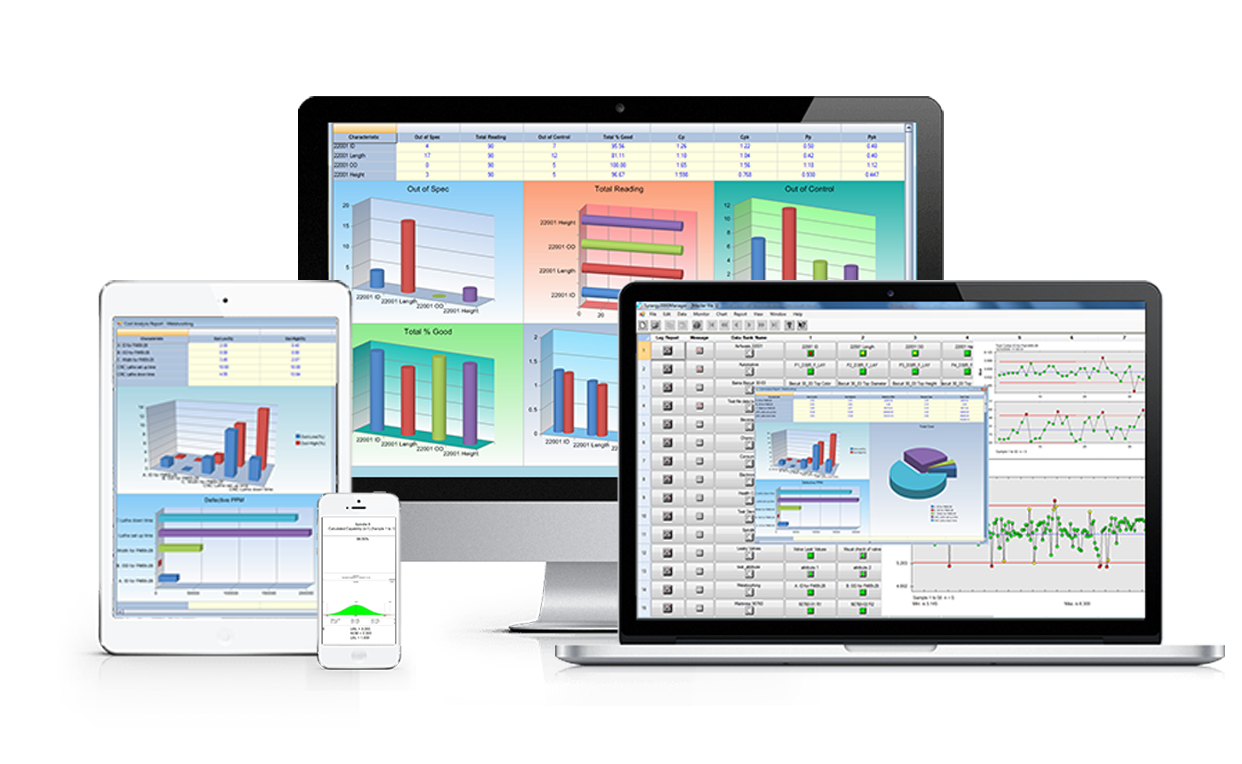
Streamline quality control inspections with this cloud-based software that comes with enhanced SPC. It will allow you to attain operational excellence.
To help you improve efficiency in manufacturing, Zontec gives you easy insights into the stability and capabilities of your processes. This allows you to make course corrections at the precise moment and position on the line.
In order to ensure that the manufacturing procedures you use are consistently fulfilling design requirements and delivering consistent outcomes, Zontec's SPC solutions can be readily accessed and used by all members of your team, from engineers to C-suite executives, and in real time as well.
Key Features
- Automatic Data Collection: The system automatically retrieves data from diverse sources such as sensors, databases, or connected devices, eliminating manual data entry and ensuring a continuous flow of accurate information.
- Quick Charting: Users can swiftly generate visual representations of data through intuitive tools, enabling rapid creation of charts and graphs without the need for specialized expertise.
- Real-time Monitoring and Analysis: The software provides live monitoring capabilities, allowing users to track data in real-time and promptly identify any deviations or anomalies.
Pricing
- Contact the vendor for pricing.
7. SAP ERP
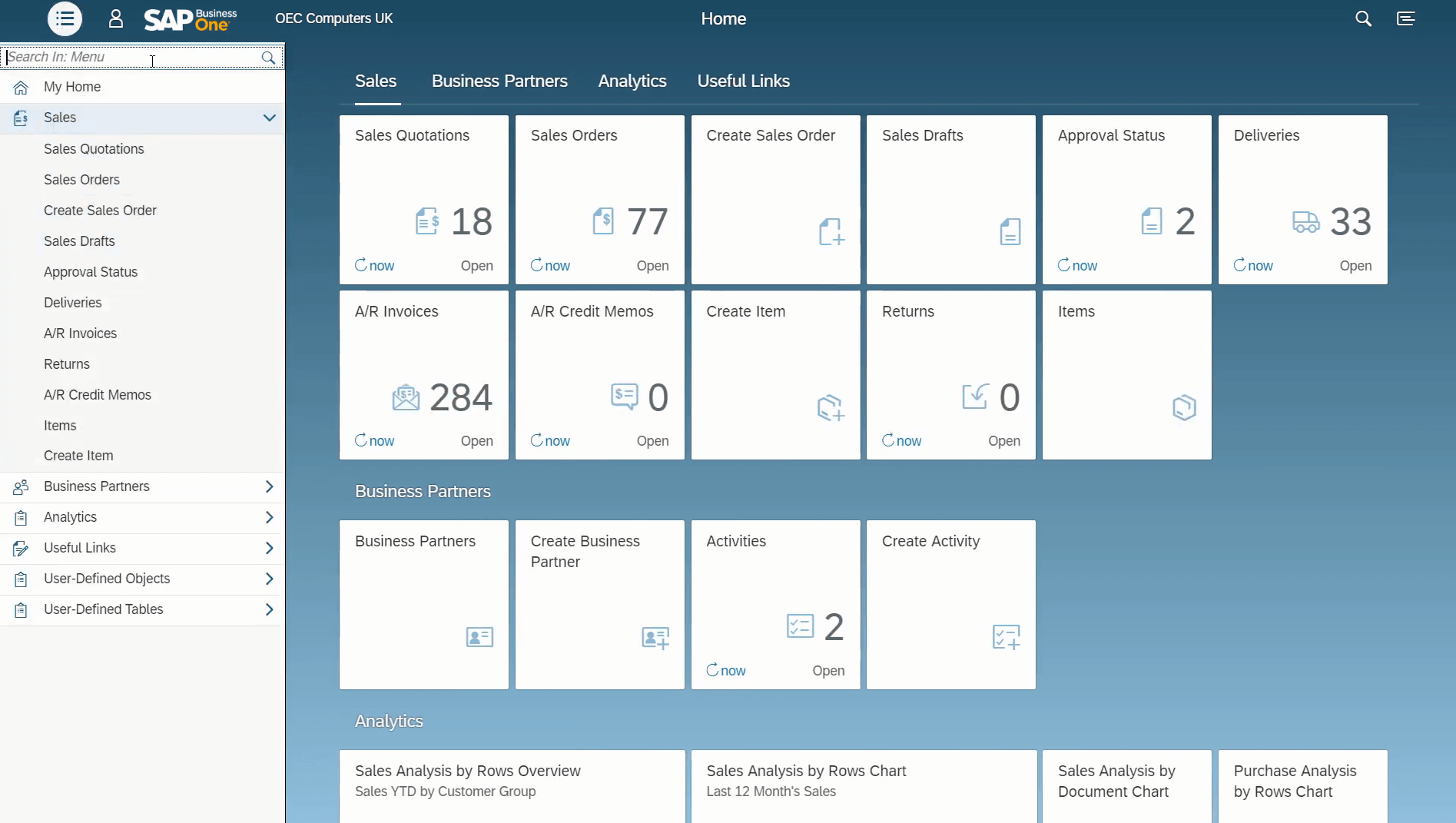
With SAP ERP's QM module, businesses in a variety of sectors can improve their quality control procedures by integrating them with the ERP system's extensive suite of modules for HRM, procurement, finance, supply chain management etc.
Businesses seeking fine-grained control over operational operations and robust security measures will find the SAP platform to be an excellent fit due to its complexity and high degree of customization. Its quality management capabilities allow you to design and carry out quality inspection plans, manage values and procedures for quality control, keep track of information about testing equipment, and generate quality certifications to prove that items are up to par.
Key Features
- Intuitive Tools: Use search help and workflow-based alerts to speed up the process of getting insights, as well as drag-and-relate and drill-down data.
- Real-time analytics: SAP Business One offers real-time analytics capabilities, allowing users to access and analyze data instantly as it is generated, providing up-to-the-minute insights into business operations.
- Quality Management: Module encompasses key capabilities such as Quality Control, Quality Assurance, Nonconformance Tracking, Audit Management, and Document Control..
Pricing
- Contact the vendor for pricing.
8. Axonator
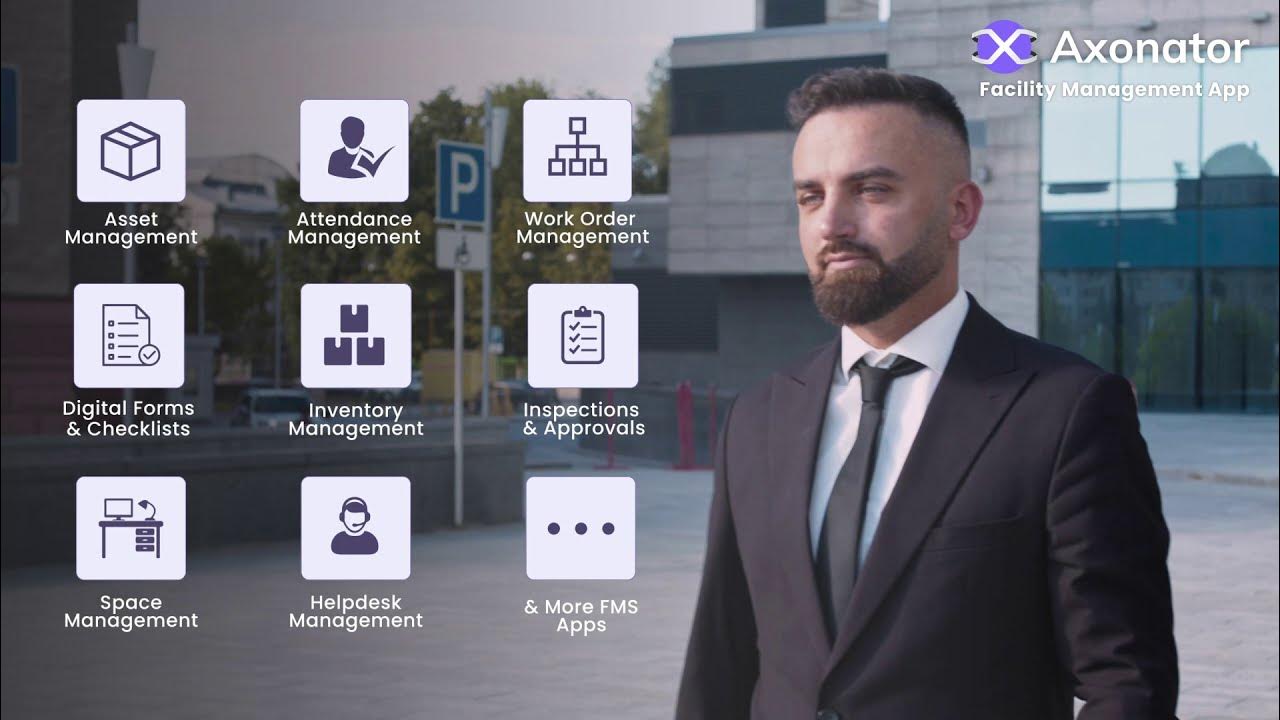
With Axonator, businesses can perform exceptional quality control at any time, anywhere. Its cloud-based platform increases efficiency and guarantees constant greatness by standardizing inspections, decreasing effort, and maintaining the highest standards.
Use quality inspection software designed for mobile devices to efficiently perform inspections right on the assembly line. Simplify the process of gathering inspection data, documenting problems, and reporting findings to quality supervisors.
Make sure all values are inside the anticipated ranges by implementing data validation. For speedier action, send warnings or notifications instantly if the value deviates.
Key Features
- Checklists and Forms: Carry out tasks such as gathering information about product weight and measurements with ease.
- Schedule Quality Inspections: Plan ahead for quality inspections so you can keep tabs on any lapses in standards and ensure timely compliance.
- Automated Quality Inspection Reports: When data is uploaded into the inspection forms, an automated system generates reports daily.
Pricing
- Basic: Free
- Pro Plan: $40/month
- Enterprise Plan: $70/month
9. Qualtrax

Gain a better understanding of your quality control in real-time.
By integrating state-of-the-art statistical process control tools with thorough inspection capabilities, this cloud-based platform enables data-driven decision-making to ensure constant excellence.
Put manufacturers in a position to make data-driven choices and boost production efficiency by providing them with actionable insights and real-time fault detection.
In order to facilitate quicker and better decision-making, empower operators, increase efficiency, cut costs, and assist both on-site and off-site staff, Enact can help you consolidate and standardize operational data.
Key Features
- Collect and Analyze Data Automatically: Automated data collection processes retrieve information from various sources without manual intervention, ensuring accuracy and consistency.
- Analyze Root Cause: The system offers tools for thorough root cause analysis, enabling users to identify underlying factors contributing to issues or trends.
- Simplify Audits: You can keep production going and fulfill compliance and auditing expectations with InfinityQS quality and process optimization solutions. These solutions automate, customize, and gather, analyze, and report enterprise-wide quality and process data.
Pricing
- Contact the vendor for pricing.
10. TrackWise
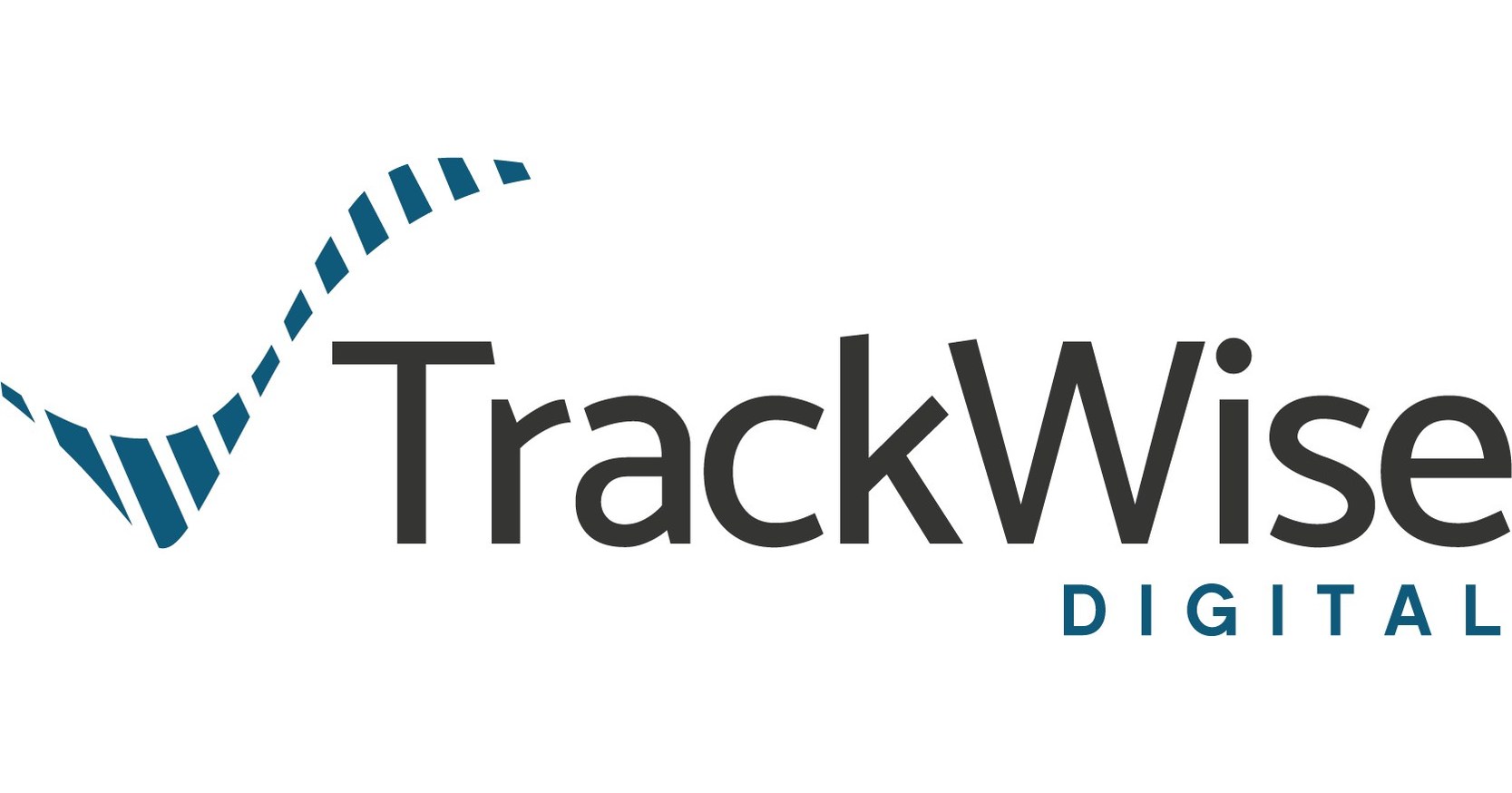
TrackWise provides a number of tools for quality control inspections as part of its quality management software. Its real-time monitoring capabilities and automated processes make it easy for manufacturers to keep quality standards high.
Through centralization of simultaneous quality procedures, the tool provides a bird's-eye view of your operational efficacy and compliance. In addition to offering several best-practice processes, TrackWise can be customized to match your current process and workflow.
Improved productivity, quality, compliance, and risk mitigation are some of the goals of businesses using TrackWise. These goals cut across a variety of sectors.
Key Features
- Automated Quality Control Workflows: The system streamlines quality control processes by automating workflows, ensuring consistency and efficiency in inspections, evaluations, and approvals.
- Document Control and Management: Users can centrally manage and control documents related to quality control, ensuring version control, access restrictions, and compliance with regulatory standards.
- Quality Data and Actionable Insights: The software provides comprehensive quality data analysis, offering insights into performance metrics, trends, and areas for improvement. These insights empower users to make informed decisions and take proactive actions to enhance quality and efficiency.
Pricing
- Contact the vendor for pricing.
Key Takeaway
Quality control is more vital than ever in today's fast-paced and highly competitive corporate climate.
The aforementioned manufacturing quality inspection software of 2024 have been known to revolutionize business processes and quality control for organizations in a variety of sectors.
With their extensive features and capabilities, these manufacturing quality inspection software can help organizations stay ahead of the competition by ensuring that their products and services satisfy high-quality requirements on a constant basis.
.webp)
%201%20(1).webp)